Hydraulic systems are powerful, reliable, and crucial for many industries, but installing hydraulic fittings correctly is essential for them to function smoothly. Even a minor mistake can lead to leaks, system failures, or costly downtime. Unfortunately, many people make avoidable errors during installation that can undermine system performance and safety.
In this post, we’ll explore 5 common mistakes to avoid when installing hydraulic fittings, along with tips on how to prevent them. Whether you’re new to hydraulics or a seasoned pro, these insights can help ensure that your hydraulic systems stay efficient and leak-free for longer.
1. Using the Wrong Hydraulic Fitting for the Job
One of the most frequent errors in hydraulic system installation is using the wrong type or size of fitting. Hydraulic fittings come in various styles and materials, each designed for specific applications. Using the wrong one can cause leaks, poor system performance, or even damage to the equipment.
How to Avoid It:
- Match Fitting Size and Type: Always ensure that the fitting size matches the hose and pipe size. This includes both the diameter and the thread type.
- Consider the Material: Depending on the fluid being used and the operating conditions, you’ll need to choose the right material for the fitting. Stainless steel, for example, is corrosion-resistant and suitable for harsh environments, while brass fittings are great for lower-pressure systems.
- Check Pressure Ratings: Ensure that the hydraulic fitting you choose can handle the system’s pressure requirements. If you’re unsure, it’s always a good idea to consult the manufacturer’s specifications.
2. Incorrectly Installing the Fitting Threads
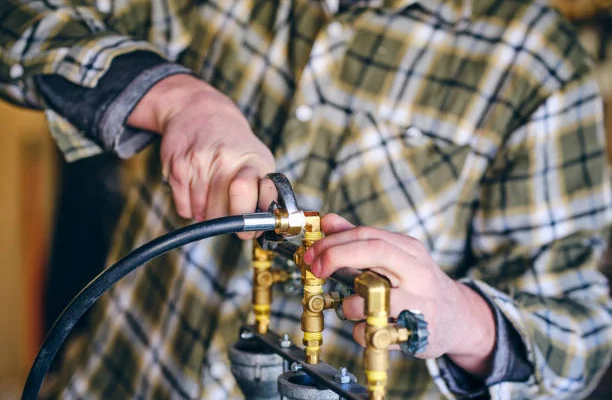
Threaded hydraulic fittings are common, but they come with their own set of challenges. Cross-threading, over-tightening, or under-tightening are all serious mistakes that can prevent the fitting from sealing properly, leading to leaks.
How to Avoid It:
- Hand-Tighten First: Begin by hand-tightening the fitting to ensure the threads align properly. Use a wrench to tighten it further, but avoid over-tightening.
- Use the Right Thread Sealant: For some applications, you’ll need to apply a thread sealant to prevent leaks. Make sure to use the correct type of sealant recommended for your system, as different systems require different sealants.
- Avoid Over-Tightening: Over-tightening can cause the threads to strip or deform, weakening the seal. Tighten the fitting until it’s snug and then give it a final, gentle turn. If you use a torque wrench, follow the recommended torque values.
3. Neglecting to Clean Fittings and Hoses
Hydraulic fittings and hoses must be clean and free of debris to ensure proper function. Any dirt, dust, or contaminants left inside the fittings or hoses can interfere with the hydraulic fluid’s flow, causing blockages or damage to seals.
How to Avoid It:
- Clean Before Installation: Always clean the fittings and hoses before installation. Use a lint-free cloth to wipe down surfaces, and ensure there’s no debris or moisture left inside.
- Inspect New Parts: Even new hydraulic fittings can have residue or manufacturing oils on them. Clean them before installing to avoid contamination of the hydraulic fluid.
- Keep Everything Sealed: Once cleaned, keep all fittings and hoses sealed with caps or plugs until installation to prevent contaminants from entering.
4. Failing to Check for Proper Alignment
When installing hydraulic fittings, it’s easy to overlook the alignment. Misaligned fittings can cause stress on the hoses or the fitting itself, which could lead to premature wear or catastrophic failure under pressure.
How to Avoid It:
- Ensure Proper Hose Routing: Check that hoses are properly routed and don’t have sharp bends or twists that could lead to misalignment or stress on the fittings.
- Avoid Twists: When installing the fittings, make sure the hoses are not twisted. If the hoses are twisted, the fittings will misalign, potentially causing leaks or damage.
- Use Support Clamps: For longer runs of hose, use clamps to keep the hoses aligned and prevent them from putting pressure on the fittings.
5. Ignoring System Pressure After Installation
After installing hydraulic fittings, it’s crucial to test the system under pressure to ensure everything is sealed correctly. Many installers skip this step, thinking that everything is fine as long as the system is not leaking during the installation process. However, pressure tests can reveal issues that are not visible at first glance.
How to Avoid It:
- Pressure Test the System: Once the installation is complete, perform a pressure test to ensure all fittings are sealed properly and that the system can handle the required pressure without leaks.
- Look for Leaks: During the pressure test, carefully inspect each fitting for signs of leaks. Even a small leak can turn into a bigger problem later on.
- Check for Vibration: If the system will experience high vibrations, ensure that fittings are properly secured and check them regularly for tightness. Vibration can cause fittings to loosen over time, leading to leaks or failures.
Conclusion
Installing hydraulic fittings may seem straightforward, but as we’ve discussed, small mistakes can lead to big problems. By choosing the correct fittings, aligning hoses properly, using thread sealants, and pressure-testing the system, you can significantly reduce the likelihood of costly errors.
Taking the time to follow these guidelines will ensure that your hydraulic systems function smoothly, perform efficiently, and have a longer lifespan. Whether you’re a DIY enthusiast or an experienced technician, the right approach to installation makes all the difference in system reliability and safety.
FAQs:
- What happens if I use the wrong hydraulic fitting?
- Using the wrong hydraulic fitting can lead to leaks, reduced system performance, or even catastrophic failure, causing damage to your equipment and possibly resulting in costly repairs.
- How tight should hydraulic fittings be?
- Hydraulic fittings should be snug but not over-tightened. Over-tightening can damage threads or cause distortion, while under-tightening may result in leaks. Use a torque wrench to follow manufacturer recommendations.
- Can I reuse hydraulic fittings?
- It’s best not to reuse hydraulic fittings, especially after they have been subjected to pressure. Reused fittings may not seal properly, which could lead to leaks or system failures.
- What is the best way to clean hydraulic fittings?
- Use a lint-free cloth and a mild solvent to clean hydraulic fittings before installation. Be sure to wipe off any residue, oils, or contaminants to prevent them from entering the system.