Hydraulic systems are the backbone of modern machinery, enabling seamless energy transfer for various industrial and automotive applications. Among the essential components in these systems, 77 Series Crimp Hydraulic Fittings stand out as a trusted solution for robust, efficient, and durable connections. This article explores the design, applications, and advantages of these fittings while providing a comprehensive understanding of their role in hydraulic systems.
What Are 77 Series Crimp Hydraulic Fittings?
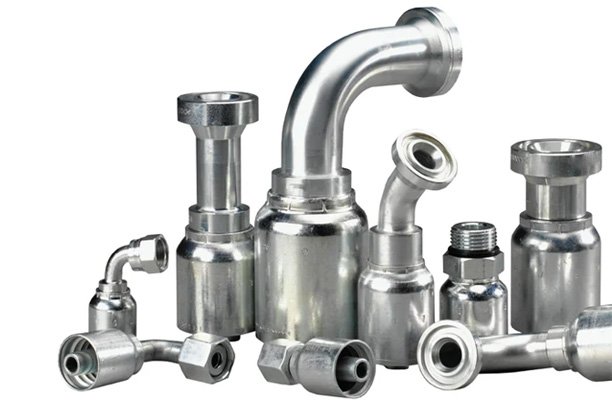
77 SeriesThe 77 Series Crimp Hydraulic Fittings are specialized connectors designed for high-pressure hydraulic applications. Specifically, these fittings connect hoses to hydraulic components, ensuring a secure and leak-proof connection. Additionally, the “crimp” mechanism involves using a crimping machine to compress the fitting onto the hose, thereby creating a durable bond that can withstand intense pressure and vibration.
Key Features of 77 Series Crimp Hydraulic Fittings
- High-Pressure Performance:
These fittings are designed to handle extremely high pressures, making them suitable for demanding hydraulic applications. - Corrosion Resistance:
Manufactured from premium materials like stainless steel or plated steel, they resist rust and corrosion, ensuring a long service life. - Wide Range of Sizes:
77 Series fittings come in various sizes to fit different hose diameters, providing versatility in application. - Leak-Proof Design:
The crimping process creates a seal that prevents fluid leakage, ensuring system efficiency. - Ease of Installation:
With the right tools, these fittings are easy to install, reducing downtime and labor costs.
Types of 77 Series Crimp Hydraulic Fittings
Discuss the various types of fittings available in the 77 Series, such as:
- Straight Fittings: Commonly used for direct connections.
- Elbow Fittings: Designed for applications requiring angular connections (e.g., 45° or 90°).
- Tee Fittings: Used to split fluid flow in different directions.
- Swivel Fittings: Allow rotational movement, reducing stress on the system.
Applications of 77 Series Crimp Hydraulic Fittings
1. Industrial Machinery:
Industries like manufacturing, mining, and construction rely on hydraulic systems for equipment such as excavators, loaders, and cranes. The robust design of 77 Series fittings ensures reliable performance in these heavy-duty machines.
2. Automotive Systems:
Hydraulic systems in vehicles, including braking and steering mechanisms, benefit significantly from the high-pressure tolerance and reliability of these fittings. Consequently, they ensure enhanced performance and safety in critical vehicle operations.
3. Agricultural Equipment:
Tractors, harvesters, and irrigation systems extensively utilize hydraulic power. Moreover, 77 Series fittings play a crucial role in maintaining efficiency and durability in such equipment, ensuring reliable operation under various agricultural conditions.
4. Aerospace Applications:
Precision and reliability are paramount in aerospace hydraulics, and 77 Series fittings meet these rigorous demands.
5. Oil and Gas Industry:
In environments where hydraulic systems face extreme conditions, such as offshore drilling rigs, the corrosion resistance of 77 Series fittings is crucial.
Benefits of Using 77 Series Crimp Hydraulic Fittings
1. Enhanced Durability:
77 Series fittings are built to last, even in challenging environments. Their robust design minimizes wear and tear, reducing the frequency of replacements.
2. Improved System Efficiency:
The secure connection provided by crimp fittings prevents fluid leakage, thus ensuring optimal hydraulic performance. This reliability is essential for maintaining system efficiency and preventing downtime.
3. Cost-Effectiveness:
By reducing the need for maintenance and replacements, these fittings help save costs over the long term.
4. Versatility:
The wide range of sizes and configurations available makes 77 Series fittings suitable for diverse applications across industries, thereby offering versatility and adaptability in various hydraulic system setups.
5. Safety:
Secure connections reduce the risk of hydraulic failure, which can lead to accidents or equipment damage, thereby enhancing safety and reliability in system operations.
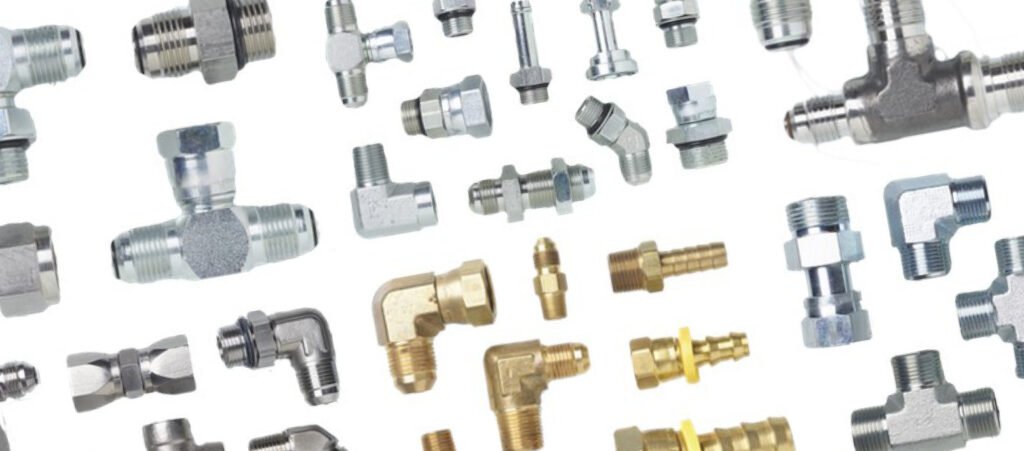
Materials Used in 77 Series Crimp Hydraulic Fittings
- Stainless Steel:
Known for its strength and corrosion resistance, stainless steel is a popular choice for harsh environments. - Carbon Steel:
This material provides a balance between strength and cost, making it ideal for general-purpose applications. - Brass:
While less common, brass fittings are used in applications where lower pressure and superior corrosion resistance are required. - Composite Materials:
Lightweight and resistant to specific chemicals, composite fittings are suitable for niche applications.
Installation Process of 77 Series Crimp Hydraulic Fittings
Step 1: Prepare the Hose and Fitting
First, cut the hydraulic hose to the required length using a hose-cutting tool to ensure a clean and straight edge. Then, select a fitting that is compatible with the hose diameter and pressure rating.
Step 2: Insert the Hose
Push the hose end into the fitting until it reaches the designated stop position. Ensure no part of the hose is twisted or misaligned.
Step 3: Crimp the Fitting
Using a hydraulic crimping machine, compress the fitting onto the hose. Follow the manufacturer’s guidelines for the correct crimping diameter and pressure settings.
Step 4: Inspect the Connection
Verify that the crimp is uniform and that there are no visible defects. Test the assembly under pressure to ensure there are no leaks.
Common Issues and How to Avoid Them
1. Improper Crimping:
- Problem: A poorly executed crimp can result in leaks or fitting failure.
- Solution: Always use the recommended crimping tools and follow the manufacturer’s specifications.
2. Incorrect Hose Selection:
- Problem: Using a hose incompatible with the fitting can compromise the system.
- Solution: Ensure the hose matches the fitting’s size and pressure rating.
3. Over-Tightening:
- Problem: Excessive crimping can damage the fitting or hose.
- Solution: Use precise crimping settings to avoid over-compression.
4. Material Incompatibility:
- Problem: Certain hydraulic fluids may react with the fitting material.
- Solution: Select fittings compatible with the specific fluid used in the system.
Maintaining 77 Series Crimp Hydraulic Fittings
- Regular Inspections:
Periodically check for signs of wear, corrosion, or leaks. - Proper Cleaning:
Keep fittings clean and free of debris to maintain their integrity. - Timely Replacement:
Replace fittings at the first sign of damage to avoid system failures. - Store Appropriately:
Store unused fittings in a dry, clean environment to prevent corrosion or contamination.
Comparison: 77 Series vs. Other Hydraulic Fittings
Feature | 77 Series Crimp Fittings | Reusable Fittings | Push-On Fittings |
---|---|---|---|
Installation | Requires crimping tools | No special tools needed | Simple push-on mechanism |
Pressure Tolerance | High | Moderate | Low to moderate |
Durability | Excellent | Good | Average |
Cost | Moderate | High | Low |
Applications | Heavy-duty, industrial | Temporary or emergency use | Low-pressure systems |
How to Choose the Right 77 Series Fitting for Your Application
Selecting Selecting the correct 77 Series Crimp Hydraulic Fitting is critical for the efficiency, safety, and longevity of your hydraulic system. Consequently, the wrong choice can lead to leaks, pressure drops, or even system failure. Therefore, here’s a detailed guide to help you make the right decision.
1. Understand Your System’s Requirements
Begin by analyzing your hydraulic system’s specifications and operational conditions. Key factors to consider include:
- Pressure Rating: Ensure the fitting matches or exceeds the system’s maximum operating pressure.
- Temperature Range: Verify the fitting can withstand the system’s temperature fluctuations.
- Fluid Type: Some hydraulic fluids may react with certain materials. Confirm compatibility.
2. Choose the Right Material for 77 Series Crimp
The material of the fitting is crucial, as it impacts the fitting’s durability and resistance to environmental factors. Common options include, but are not limited to:
- Stainless Steel: Ideal for corrosive environments, such as marine or chemical industries.
- Carbon Steel: A cost-effective choice for general-purpose applications with moderate conditions.
- Brass: Excellent for systems with lower pressures and requiring superior corrosion resistance.
- Plated Steel: Combines affordability and corrosion resistance for diverse applications.
3. Determine the Fitting Type
Different types of fittings serve distinct purposes. Select one based on your system’s configuration:
- Straight Fittings: Best for linear connections without directional changes.
- Elbow Fittings (e.g., 45° or 90°): Suitable for systems requiring angular connections.
- Tee Fittings: Ideal for branching hydraulic flow into multiple directions.
- Swivel Fittings: Allow rotational movement to reduce stress on hoses and components.
4. Consider Hose Compatibility
The fitting must be compatible with the hydraulic hose in terms of:
- Size: Match the fitting to the hose’s inner and outer diameters.
- Construction: Ensure compatibility with the hose’s reinforcement layers, such as braided or spiral steel.
- Flexibility: Assess the hose’s bending radius and ensure the fitting doesn’t restrict movement.
5. Factor in Environmental Conditions
The operating environment significantly affects the choice of fittings:
- Corrosive Environments: Use stainless steel or brass fittings for long-lasting performance.
- High-Temperature Areas: Opt for materials with high thermal resistance.
- High-Vibration Zones: Swivel or elbow fittings can reduce stress on hoses caused by movement or vibrations.
6. Evaluate Cost vs. Performance
While it’s tempting to opt for lower-cost fittings, they may not offer the durability or performance required. Consider:
- Long-Term Costs: High-quality fittings reduce downtime, maintenance, and replacement expenses.
- Application Criticality: For critical systems, prioritize reliability over cost savings.
7. Review Industry Standards and Certifications
Ensure the fittings comply with industry regulations for your application, such as:
- SAE J516: For hydraulic hose fittings.
- ISO 8434-2: Pertaining to 37° flared fittings.
- DNV/ABS Approvals: Required for marine and offshore applications.
Meeting these standards guarantees the fitting’s quality, safety, and compatibility with industry practices.
8. Consult the Manufacturer’s Specifications
Every fitting comes with a datasheet outlining its specifications, such as:
- Pressure and temperature limits.
- Material compatibility.
- Crimping guidelines.
Follow the manufacturer’s recommendations to ensure optimal performance.
9. Use Application-Specific Tools and Resources
Many manufacturers and distributors provide online tools, such as:
- Hose and Fitting Selector Tools: Input your system details to receive a tailored recommendation.
- Pressure Drop Calculators: Determine the impact of fittings on system efficiency.
- Technical Support: Contact technical experts to clarify any doubts about fitting selection.
10. Plan for Future Needs
Anticipate potential system upgrades or changes:
- Choose fittings compatible with both current and future equipment.
- Select fittings that allow easy replacement or expansion of the system.
Future Trends in Hydraulic Fittings
As technology advances, the demand for innovative hydraulic fittings grows. Emerging trends in the industry include:
- Eco-Friendly Materials:
Increased focus on sustainable and recyclable materials for fittings. - Smart Monitoring Systems:
Integration of sensors into fittings to monitor pressure, temperature, and performance in real-time. - Enhanced Corrosion Resistance:
New coatings and materials are being developed to improve resistance to harsh chemicals and environments. - Miniaturization:
As equipment becomes more compact, fittings are being designed to deliver high performance in smaller sizes.
Conclusion
The 77 Series Crimp Hydraulic Fittings are a critical component for maintaining the efficiency and reliability of hydraulic systems across various industries. Consequently, their high-pressure tolerance, durability, and versatility make them an excellent choice for demanding applications. Furthermore, by understanding their features, installation process, and maintenance requirements, you can optimize your hydraulic systems for long-term performance and safety.
FAQs
Q1: What tools are required to install 77 Series crimp fittings?
A hydraulic crimping machine, hose-cutting tool, and calipers for measurement are essential.
Q2: Can 77 Series fittings be reused?
No, these fittings are designed for one-time use. Reusing them compromises the integrity of the connection.
Q3: How do I determine the correct fitting size?
Refer to the hose diameter and pressure rating specified in your hydraulic system’s manual.
Q4: Are these fittings compatible with all hydraulic fluids?
Most fittings are compatible with standard fluids, but always check the manufacturer’s specifications for compatibility with specialized fluids.
Q5: What is the maximum pressure rating for 77 Series crimp fittings?
The pressure rating varies by size and material but typically ranges from 5,000 to 6,000 psi.
Q6: How can I prevent leaks in my hydraulic system?
Ensure proper crimping, select compatible materials, and conduct regular system maintenance.