If you’re wondering what a hydraulic cylinder is or looking for information on its components and functionality, you’re in the right place. Whether you’re planning a repair or a rebuild, understanding how hydraulic cylinders work is essential. This guide will answer common questions about hydraulic cylinders and explain the basics in detail.
What is a Hydraulic Cylinder?
A hydraulic cylinder, also known as a hydraulic actuator or hydraulic ram, is a mechanical device that creates linear motion by using hydraulic fluid. These devices are widely used across industries such as manufacturing, construction, aviation, and even agriculture. They provide the power needed for tasks that involve pushing, pulling, lifting, or pressing heavy loads. For example, the hydraulic cylinder in a forklift allows it to lift and lower loads with precision.
Hydraulic cylinders are a core component of hydraulic systems, where pressurized fluid is used to generate force. These systems are crucial in many industrial applications, including earthmoving machinery, industrial presses, and even aircraft landing gear.
How Does a Hydraulic Cylinder Work?
Hydraulic cylinders operate on the principle of fluid mechanics, specifically Pascal’s Principle, which states that pressure applied to a confined fluid is transmitted equally in all directions. When force is applied to the hydraulic fluid inside the cylinder, it creates pressure that moves the piston. This movement translates into linear mechanical force that can lift or move heavy objects.
To break it down further: When fluid enters the cylinder under pressure, it pushes the piston, causing it to extend or retract. The pressure applied to the hydraulic cylinder piston is crucial in determining the amount of force that will be generated. By using a piston with a larger surface area, greater force can be exerted without increasing the pressure of the fluid.
Components of a Hydraulic Cylinder
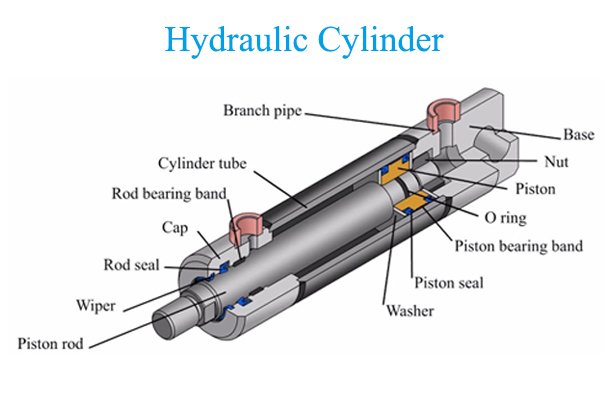
Hydraulic cylinders come in many shapes and sizes, but their core components remain largely the same. Here’s an overview of the main parts of a hydraulic cylinder:
- Piston: The piston moves inside the cylinder barrel, pushed by the hydraulic fluid. The movement of the piston is what creates the linear motion of the cylinder. Seals around the piston ensure that hydraulic fluid doesn’t leak from one side of the piston to the other, maintaining the pressure inside the cylinder.
- Cylinder barrel: This is the seamless steel tube that houses the piston. The barrel contains the hydraulic fluid and provides the structure for the cylinder’s operation. It must withstand high internal pressures without leaking.
- Cylinder head: Located at the end of the cylinder where the piston extends and retracts, the cylinder head keeps the piston aligned and ensures a proper seal. It also supports the rod as it moves in and out of the barrel.
- Cylinder base: This component seals the other end of the cylinder and often serves as the mounting point for the equipment that the cylinder is connected to.
- Seals and gaskets: These components are vital for maintaining pressure inside the cylinder and preventing leaks. Depending on the application, these seals can be made from materials like polyurethane, nitrile rubber, or Teflon to withstand extreme pressures and temperatures.
Types of Hydraulic Cylinders
Several types of hydraulic cylinders are used in various applications, each suited for specific tasks. Here are the most common types of hydraulic cylinders:
- Single-acting cylinders: These cylinders use hydraulic pressure to move the piston in one direction, while a spring or motor usually resets the piston after the hydraulic fluid is released. They are commonly used in applications where the load provides the return force, such as in hydraulic jacks.
- Double-acting cylinders: These cylinders have two chambers for fluid—one for extension and one for retraction. This allows the cylinder to move in both directions without external resetting mechanisms. Double-acting cylinders are ideal for applications where precise control is needed, such as in construction equipment like excavators.
- Telescopic cylinders: These cylinders consist of multiple stages, or sections, that allow for a longer stroke in a more compact design. Telescopic cylinders are commonly used in heavy equipment such as cranes and dump trucks, where large movements are required but space is limited.
- Tandem cylinders: These designs connect two or more hydraulic cylinders in sequence to deliver more force without increasing the size of each cylinder. They are used when space is limited, but extra power is needed, like in some industrial presses.
Hydraulic Cylinder vs. Pneumatic Cylinder
Hydraulic and pneumatic cylinders both serve similar functions but operate on different principles. A hydraulic cylinder uses incompressible fluid, typically oil, to generate high force, while a pneumatic cylinder relies on compressed air.
Advantages of hydraulic cylinders:
- Higher force generation: Hydraulic cylinders can generate up to 4,000 psi, making them ideal for heavy-duty applications.
- Consistent force: Since hydraulic fluid is incompressible, it maintains a consistent level of force throughout the system.
Disadvantages of hydraulic cylinders:
- Complexity: Hydraulic systems require additional components such as pumps, motors, and reservoirs.
- Fluid leaks: Hydraulic cylinders can leak fluid, potentially leading to contamination of surrounding components.
Advantages of pneumatic cylinders:
- Simplicity: Pneumatic cylinders are easier to maintain and operate.
- Safety: Since they rely on compressed air, they pose less of a fire hazard than hydraulic systems.
Disadvantages of pneumatic cylinders:
- Lower force output: Lower force output: Pneumatic cylinders, limited to around 250 psi, are less powerful than hydraulic systems.
- Efficiency: Pneumatic systems often require a continuously running compressor, even when the cylinder isn’t in use.
How to Choose the Right Hydraulic Cylinder
Choosing the right hydraulic cylinder for your application involves several factors:
- Mass calculation: The weight of the load to be moved or lifted determines the size and durability of the required cylinder.
- Bore size: The diameter of the cylinder’s bore influences the amount of force it can generate. Larger bores are necessary for applications requiring more power.
- Rod size: The length of the cylinder’s stroke and the load-bearing requirements help determine the proper rod size. A longer stroke requires a sturdier rod to prevent buckling.
- Cushioning: If your application involves high-speed movements, consider using cushioning options to absorb impact at the ends of the stroke.
Common Applications of Hydraulic Cylinders
Hydraulic cylinders are critical components in various industries. Here are some common uses:
- Construction equipment: Hydraulic cylinders are essential in excavators, bulldozers, and backhoes, providing the force needed to move large amounts of earth and materials.
- Manufacturing: In manufacturing plants, hydraulic actuators power machinery like injection molders, presses, and compactors.
- Aviation: Aircraft landing gear relies on hydraulic cylinders for precise control during takeoff and landing, ensuring the smooth operation of heavy loads.
- Agriculture: Tractors and other agricultural equipment use hydraulic cylinders to operate lifting mechanisms, plows, and other attachments.
Maintenance and Troubleshooting
Proper maintenance is crucial for ensuring the longevity and efficiency of a hydraulic cylinder. Without regular care, even high-quality cylinders can suffer from performance degradation.
- Regular Maintenance: Routinely check the cylinder for leaks, worn-out seals, and fluid contamination. Lubricate moving parts to reduce wear and keep the cylinder operating smoothly.
- Common Issues: Hydraulic cylinders may experience issues like fluid leaks, piston misalignment, or loss of pressure. These problems often result from worn seals, damaged rods, or improper fluid levels.
- Troubleshooting Tips: Begin by inspecting seals and gaskets for leaks or wear. Make sure the hydraulic fluid is at the correct level and that there is no contamination. If there is still a problem, it may be necessary to disassemble and inspect internal parts for wear.
Hydraulic Cylinder Sizing and Selection Guide
Choosing the correct hydraulic cylinder requires careful consideration of your application’s demands.
- Understanding Force Requirements: Calculate the force required by multiplying the hydraulic pressure by the piston area (Force = Pressure x Area).
- Choosing the Right Type: Decide between single-acting and double-acting cylinders based on whether you need movement in one or both directions.
- Extreme Conditions: For applications in harsh environments or extreme temperatures, choose cylinders made with materials that can withstand such conditions, like stainless steel or specialty coatings.
Materials Used
The materials used in constructing a hydraulic cylinder significantly affect its durability and performance.
- Cylinder Barrel Materials: Common barrel materials include high-grade steel and aluminum. Steel handles heavy-duty applications, while aluminum is chosen for lightweight machinery.
- Seal Materials: Manufacturers often choose rubber, polyurethane, or Teflon to make seals because of their resistance to wear, heat, and chemical exposure.
Safety Tips for Operating Hydraulic Cylinders
When operating hydraulic systems, safety should always be a top priority.
- Safety Hazards: High-pressure fluid leaks can cause serious injuries or damage machinery. Always wear protective gear and ensure the system is shut off before performing maintenance.
- Best Practices: Regularly inspect cylinders for leaks and misalignment. Properly install all components and avoid overloading the system.
- Emergency Shutdown Procedures: In case of a hydraulic system malfunction, immediately shut down the system, depressurize the cylinder, and contact a professional for repairs.
Hydraulic Cylinder Accessories
Many accessories can enhance the performance of hydraulic cylinders in specific applications.
- Mounting Options: There are different mounting styles, such as flange, clevis, or trunnion, depending on your application’s needs.
- Valves and Controls: Proper valves control the flow of hydraulic fluid, ensuring smooth operation and protection against overpressure.
- Hoses and Fittings: Selecting the right hydraulic hoses and fittings is crucial for maintaining pressure and preventing leaks.
Comparing Hydraulic Cylinders to Other Actuator Types
Hydraulic cylinders aren’t the only option for linear motion. Here’s how they compare to other actuators:
- Hydraulic vs. Electric Actuators: While electric actuators are more energy-efficient and easier to control, hydraulic actuators provide much higher force.
- Hydraulic vs. Mechanical Actuators: Hydraulic systems can generate more force and offer better durability in heavy-duty applications than mechanical gear systems.
Hydraulic Cylinder Rebuild vs. Replacement
When a hydraulic cylinder fails, the decision to rebuild or replace it depends on several factors.
- When to Rebuild: If the damage is minor and the cylinder is relatively new, rebuilding might be a more cost-effective solution.
- Rebuilding Process: Rebuilding involves disassembling the cylinder, replacing seals, cleaning parts, and reassembling.
- Costs and Benefits: Rebuilding can save money but may not be worthwhile if the cylinder has extensive damage or is nearing the end of its life.
Industry-Specific Applications
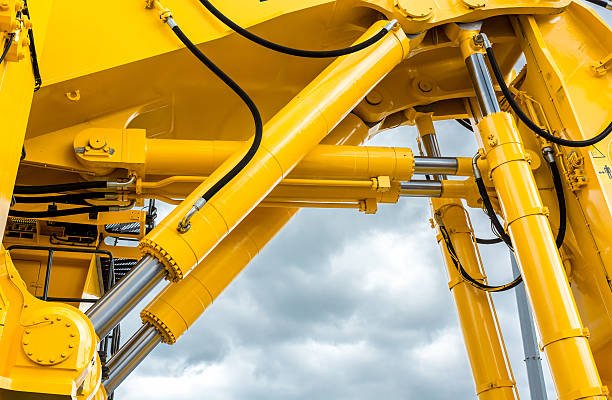
Hydraulic cylinders play key roles in various industries.
- Automotive: Besides forklifts, hydraulic cylinders are used in car lifts, brake systems, and convertible roofs.
- Marine Industry: Hydraulic cylinders control boat rudders and stabilizers, allowing for smooth navigation in rough waters.
- Mining: In mining, hydraulic cylinders operate heavy machinery, such as excavators, which endure extreme pressure and conditions.
- Energy Sector: Hydraulic systems in wind turbines and oil rigs rely on cylinders to manage heavy loads and ensure operational safety.
Conclusion
Hydraulic cylinders are indispensable components in various industries, delivering the power needed for tasks that require linear motion. By understanding the different types of hydraulic cylinders and their key components, such as the hydraulic cylinder piston and seals, you can make informed decisions when selecting the right cylinder for your specific application. Whether you’re working with a single-acting hydraulic ram or a double-acting telescopic cylinder, having a clear grasp of their functionality will help you optimize performance and ensure smooth operations in your machinery.
FAQs
What is the purpose of a hydraulic cylinder? Hydraulic cylinders convert fluid pressure into mechanical motion, powering heavy machinery for lifting, pushing, or pulling.
What are the main types of hydraulic cylinders? The three main types are single-acting, double-acting, and telescopic hydraulic cylinders.
Can you repair a hydraulic cylinder? Yes, hydraulic cylinders can be repaired by replacing worn parts like seals or rods. Some repairs may require professional services.
How do I determine the size of my hydraulic cylinder? Cylinder size is based on bore diameter, rod diameter, and stroke length. These measurements help in selecting the right cylinder.
What does a hydraulic cylinder cost? Prices range from $100 for smaller cylinders to several thousand dollars for larger, custom-built models.
Where can I find hydraulic cylinder manufacturers? Search for hydraulic equipment suppliers or repair services in your area through online directories.