Sealing systems play a crucial role in ensuring the safe and efficient operation of countless mechanical systems. Whether it’s in high-tech aerospace equipment or household plumbing, one component consistently proves indispensable: the O-Ring. This small, versatile piece of engineering is a linchpin in modern technology, bridging the gap between simplicity and innovation.
With its simple donut shape, the O-Ring may not appear impressive at first glance. Yet, its ability to create effective seals under diverse conditions makes it invaluable. From extreme temperatures to high-pressure systems, O-Rings have become a universal solution across industries. This article delves deep into everything you need to know about O-Rings, from their origins and applications to maintenance and emerging trends.
What is an O-Ring?
An O-Ring is a circular elastomeric loop designed to prevent the leakage of liquids or gases. It functions as a seal by compressing and deforming slightly within its groove, filling the gap between two surfaces.
The unique simplicity of its design is key to its effectiveness. Unlike complex sealing mechanisms, an O-Ring relies on basic material properties—elasticity, resilience, and durability. Available in countless sizes and materials, O-Rings are incredibly versatile, capable of adapting to the needs of virtually any application.
When properly installed, an O-Ring forms a tight, leak-proof barrier that prevents the ingress or egress of substances. This makes it an indispensable component in applications as varied as car engines, hydraulic systems, and medical devices.
How O-Rings Work
The magic of an O-Ring lies in its material properties and shape. When placed in a groove and compressed between two surfaces, the O-Ring deforms slightly to fill the gap. This deformation creates a seal that prevents the escape or entry of substances, even under high pressure.
O-Rings are equally effective in static applications (where components remain stationary) and dynamic applications (where components move relative to one another). For example:
- Static Seals: Used in pipe connections, flanges, and stationary cylinders.
- Dynamic Seals: Found in hydraulic pistons, pumps, and rotating shafts.
In both cases, the O-Ring’s ability to return to its original shape after compression—its elasticity—is crucial. This ensures that the seal remains tight over time, even with repeated use or minor fluctuations in pressure and temperature.
Materials
The versatility of O-Rings stems largely from the wide range of materials available. Choosing the right material is essential for ensuring compatibility with the operating environment. Here are some common materials and their properties:
- Nitrile Rubber (NBR): Resistant to oil and fuel, making it ideal for automotive and industrial applications. However, it’s not suited for high-temperature environments.
- Silicone: With excellent temperature resistance (-55°C to 200°C), silicone is perfect for applications requiring flexibility and thermal stability. It’s commonly used in medical and food-grade seals.
- Fluorocarbon (Viton): Known for its chemical resistance and ability to handle extreme temperatures, Viton is a top choice for aerospace and chemical processing.
- EPDM (Ethylene Propylene Diene Monomer): Highly resistant to water, steam, and certain chemicals, EPDM is often used in plumbing and HVAC systems.
Other specialized materials, such as polyurethane, PTFE (Teflon), and neoprene, cater to niche applications requiring unique properties like abrasion resistance or low friction.
Types of O-Rings
- Standard O-Rings: The most widely used, these are suitable for general-purpose sealing applications.
- Metric O-Rings: Designed according to international standards, metric O-Rings ensure compatibility in systems manufactured outside the U.S.
- Custom O-Rings: When standard sizes or materials won’t suffice, custom one can be manufactured to precise specifications.
- FDA-Approved O-Rings: Made from food-grade materials, these are used in the food and beverage industry to meet safety standards.
Each type serves a unique purpose, making it important to select the right one based on the specific requirements of your application.
What is an O-Ring Used For?
The versatility of O-Rings is one of their defining characteristics. These small, circular seals are used across a wide range of industries and applications, making them indispensable in modern engineering and manufacturing. Their primary purpose is to create a tight, leak-proof seal between two or more surfaces, preventing the ingress or egress of fluids or gases. This seemingly simple function has vast implications in numerous fields.
Key Applications
- Automotive Industry:
O-Rings are essential in vehicles, where they seal engine components, fuel injectors, and air conditioning systems. They help maintain fluid pressure and prevent oil, coolant, and fuel leaks, ensuring efficient and safe vehicle operation. - Aerospace and Aviation:
In aerospace systems, they are used to maintain pressure and prevent leaks in hydraulic and fuel systems. Their ability to perform under extreme temperatures and pressures is crucial for aircraft safety. - Medical and Pharmaceutical Equipment:
O-Rings are frequently employed in medical devices like syringes, infusion pumps, and diagnostic equipment. They provide sterile seals that prevent contamination and ensure the safe delivery of medicines and fluids. - Hydraulics and Pneumatics:
In hydraulic and pneumatic systems, it serves as seals in cylinders, valves, and pumps. They help maintain pressure, ensure smooth operation, and prevent leaks in these high-pressure environments. - Plumbing Systems:
From faucets to pipe joints, they are widely used in plumbing to prevent water leaks. Their durability and ability to withstand exposure to water and steam make them a reliable choice for household and industrial plumbing. - Food and Beverage Industry:
FDA-compliant O-Rings are used in food processing equipment to create seals that are both sanitary and effective. These are made from food-grade materials that can withstand high temperatures and cleaning chemicals. - Electronics and Semiconductor Manufacturing:
In electronics, it protects sensitive components from moisture and dust. In semiconductor manufacturing, they are used in vacuum seals and equipment exposed to harsh chemicals.
Advantages
- Versatility: They function effectively in both static and dynamic systems, making them suitable for an extensive range of applications.
- Cost-Effectiveness: Their affordability and ease of replacement contribute to their widespread use.
- Reliability: Properly installed and maintained o-rings offer consistent performance over long periods, even in demanding conditions.
Whether it’s in a home faucet or a spacecraft, the role is undeniable. Their adaptability and reliability ensure they remain one of the most valuable components in engineering design.
Choosing the Right O-Ring
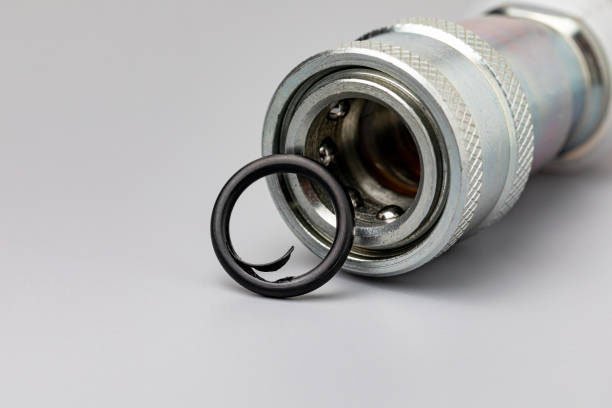
Selecting the correct O-Ring for your specific application is critical for ensuring optimal performance, durability, and reliability. O-Rings are versatile, but their effectiveness hinges on choosing the right combination of size, material, and compatibility with operating conditions. A misstep in this selection process can lead to seal failure, system inefficiencies, or costly repairs. Here’s an extended guide to help you navigate this decision-making process.
Factors to Consider When Choosing
Material Compatibility
The choice of material is fundamental. Different materials respond uniquely to environmental factors such as temperature, pressure, and chemical exposure. For instance:
- Nitrile Rubber (NBR): Best for petroleum-based oils and fuels but not ideal for high-temperature applications.
- Silicone: Great for extreme temperature ranges but less resistant to abrasion.
- Fluorocarbon (Viton): Offers excellent chemical and heat resistance, making it ideal for demanding applications.
- EPDM: Resistant to water, steam, and some chemicals but not suitable for petroleum-based fluids.
Size and Dimensions
The size of an O-Ring is another crucial factor. It must fit perfectly within its groove to create an effective seal. They are measured by their inner diameter (ID), outer diameter (OD), and cross-sectional thickness (CS).
- Use a precise measuring tool, such as a caliper, to determine these dimensions.
- Refer to standard O-Ring sizing charts or ISO 3601 specifications for accuracy.
Application Environment
Temperature: Ensure the material can withstand the maximum and minimum temperatures it will encounter. For example, silicone O-Rings work well in extreme cold, while Viton handles high heat.
Pressure: Determine whether it will face static or dynamic pressure. High-pressure environments may require backup rings or harder elastomers to prevent extrusion.
Motion: In dynamic applications, such as pistons or rotating shafts, select materials with good abrasion and wear resistance.
Hardness (Durometer)
O-Ring hardness, rated on the Shore A scale, influences sealing performance. Softer options (low durometer) easily conform to surfaces, ensuring effective seals but may extrude under high pressure. Harder variants (high durometer) resist extrusion but need greater compression force for sealing. Select a hardness that balances flexibility and durability to suit your application requirements.
Regulatory and Industry Standards
For applications in regulated industries like medical, food, or aerospace, ensure the O-Ring complies with relevant standards. For example:
- FDA-compliant O-Rings for food and beverage applications.
- ISO 9001-certified O-Rings for quality assurance in industrial applications.
Lubrication and Surface Finish
Proper lubrication reduces friction and aids in the installation, especially in dynamic applications. However, the lubricant must be compatible with both the material and the system environment. Additionally, ensure that the surfaces the interacts with are smooth and free from burrs or sharp edges to prevent premature wear.
Tips for Choosing the Right O-Ring
- Use Sizing Charts: Refer to manufacturer guides for size and material compatibility.
- Test Prototypes: Validate performance in controlled conditions before finalizing.
- Add Backup Rings: Prevent extrusion in high-pressure systems.
- Consult Experts: Seek advice from specialists or manufacturers for tailored solutions.
Common Mistakes to Avoid
- Overstretching the O-Ring: Stretching an O-Ring too far during installation can cause it to lose its elastic properties or break.
- Using the Wrong Material: Even a high-quality O-Ring will fail if the material isn’t compatible with the operating environment.
- Ignoring Long-Term Conditions: Consider factors like aging, UV exposure, and thermal cycling, which can degrade the O-Ring over time.
Choosing the right one might seem straightforward, but a well-informed selection process ensures not just system performance but also long-term reliability and cost savings. Taking the time to analyze your application’s needs thoroughly will pay dividends in the form of reduced maintenance and fewer system failures.
Conclusion
O-Rings are a testament to the power of simplicity in engineering. Their versatility, affordability, and reliability have cemented their place as a cornerstone of countless industries. By understanding their materials, applications, and limitations, you can maximize the performance and lifespan of O-Rings in your systems. As technology continues to evolve, O-Rings will undoubtedly remain a vital tool in sealing solutions.
FAQs
What are O-Rings used for?
O-Rings are used to create seals that prevent the leakage of fluids or gases in various applications. They are commonly found in engines, hydraulic systems, medical devices, and plumbing systems.
How do I know if an O-Ring needs replacing?
Signs of wear, such as cracks, flattening, or hardening, indicate that an O-Ring should be replaced. Leaks or reduced performance in the system may also signal O-Ring failure.
What material is best for high-temperature environments?
Silicone and fluorocarbon (Viton) are excellent materials for high-temperature applications, withstanding temperatures up to 200°C and beyond in some cases.
How do I ensure proper installation of an O-Ring?
To ensure proper installation, clean the groove, use the correct size O-Ring, apply a compatible lubricant, and avoid over-stretching or twisting the O-Ring during placement.
Can O-Rings handle chemical exposure?
Yes, but the material must be selected carefully to match the chemical environment. For example, fluorocarbon (Viton) resists most chemicals, while EPDM works well with water-based substances.
What causes O-Ring failure?
O-Ring failure can result from improper material selection, incorrect sizing, chemical degradation, extreme temperatures, or excessive wear. Ensuring compatibility and proper maintenance can prevent most issues.