What Are Ferrules in Hydraulic Systems?
Hydraulic systems are the lifeblood of countless industries—construction, automotive, aviation, and manufacturing, to name a few. One small yet incredibly vital component in these systems is the ferrule. This tiny but mighty part ensures secure, leak-free connections in high-pressure environments. But what exactly are ferrules, and why are they so critical? Let’s dive in and explore!
Understanding Ferrules: The Unsung Heroes of Hydraulic Systems
Before we break it all down, let’s start with the basics: What are ferrules?
Ferrules are cylindrical metal or plastic components, often used to create secure connections between hoses, tubes, or pipes in hydraulic systems. Think of them as the “reinforcements” that prevent leaks, enhance stability, and withstand extreme pressures.
In hydraulic systems, ferrules are usually made of stainless steel, brass, or aluminum, offering strength, corrosion resistance, and reliability. They’re crucial in ensuring that hydraulic fluid stays within the system and doesn’t escape—a problem that could lead to efficiency loss, equipment failure, or even hazardous situations.
Types of Ferrules in Hydraulic Systems
Ferrules come in different shapes, sizes, and materials, each designed for specific hydraulic applications. Choosing the right type can make or break the performance of your hydraulic system. Let’s break down the most common ferrule types in greater detail:
1. Single Ferrules
- Key Features:
- Made for low to medium-pressure systems.
- Compact design, easy to install.
- Applications:
- Perfect for systems where hydraulic fluid pressure doesn’t exceed 3,000 PSI.
- Used in agriculture (tractors and irrigation systems) and light industrial machines.
- Advantages:
- Cost-effective for less demanding applications.
- Ideal for simpler systems where quick repairs or replacements are needed.
- Drawbacks:
- Not suitable for high-pressure or high-vibration environments, as they lack the reinforcement of double ferrules.
2. Double Ferrules
- Key Features:
- Includes two components: a front ferrule for sealing and a back ferrule for gripping.
- Highly reliable for high-pressure, high-vibration systems.
- Applications:
- Commonly used in oil and gas, aerospace, and heavy machinery where pressures often exceed 5,000 PSI.
- Advantages:
- Provides superior leak prevention, even under extreme stress.
- Resistant to vibration-related loosening.
- Drawbacks:
- Slightly more expensive than single ferrules.
3. Tapered Ferrules
- Key Features:
- Designed to create a smooth connection for flexible hoses.
- Tapered design ensures minimal turbulence in the fluid flow.
- Applications:
- Frequently used in mobile hydraulic systems, such as forklifts, cranes, and earthmovers, where flexible hoses are required for maneuverability.
- Advantages:
- Reduces wear and tear on hoses by absorbing minor movements.
- Drawbacks:
- Limited to applications where hose flexibility is required, and may not offer the same level of sealing strength as double ferrules.
4. Flare Ferrules
- Key Features:
- Designed for tubing or pipes that have flared ends.
- Creates a tight, reliable connection by “sandwiching” the flare between the ferrule and fitting.
- Applications:
- Widely used in automotive brake systems, HVAC systems, and aviation fuel lines.
- Advantages:
- Suitable for systems where quick disassembly is required for maintenance or repair.
- Drawbacks:
- Requires specialized flaring tools for installation, adding an extra step to the process.
How to Choose the Right Ferrules for Your Hydraulic System
Selecting the right ferrules is crucial for ensuring optimal performance and safety. Here’s a more detailed guide to help you make the best choice:
A. Pressure Requirements
- Low-Pressure Systems (Below 3,000 PSI): Single ferrules are usually sufficient for applications like irrigation, light industrial machines, and basic machinery.
- High-Pressure Systems (3,000–10,000 PSI): Double ferrules are a must for industries like oil and gas, heavy machinery, and aerospace.
- Pro Tip: Always refer to the manufacturer’s specifications for your hydraulic system to determine the maximum pressure it can handle.
B. Material Selection
- Stainless Steel:
- Best for high-pressure systems and harsh environments (e.g., marine, oil rigs).
- Corrosion-resistant and extremely durable, but more expensive.
- Brass:
- Ideal for lower-pressure systems where cost is a concern.
- Common in agricultural and HVAC applications.
- Aluminum:
- Lightweight and cost-effective, suitable for low-pressure, low-stress systems.
- Not ideal for corrosive or high-stress environments.
- Pro Tip: Consider the operating temperature of your hydraulic system—stainless steel performs better in extreme heat or cold compared to brass or aluminum.
C. Accurate Sizing
- Measure the outer diameter (OD) of the hose or tube where the ferrule will be installed.
- Use tools like calipers for precise measurements.
- Select ferrules with a snug fit to prevent leaks but avoid forcing a ferrule that’s too small, as it could damage the hose.
- Pro Tip: Double-check manufacturer compatibility charts if you’re replacing old ferrules.
D. Environmental Considerations
For systems with minimal environmental exposure, brass or aluminum ferrules can save costs without sacrificing performance.
For systems exposed to corrosive environments (e.g., saltwater or chemicals), stainless steel ferrules are the best choice.
Why Are Ferrules Important in Hydraulic Systems?
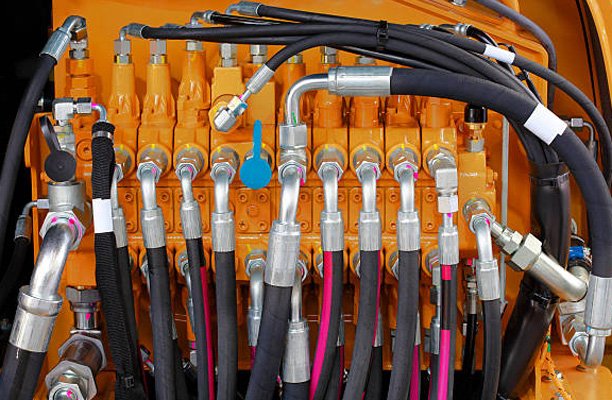
To truly appreciate the importance of ferrules, let’s look at how they contribute to overall system performance and safety.
Preventing System Failures
- Imagine a hydraulic system powering a construction crane. A worn or damaged ferrule could result in a leak, causing the crane to lose hydraulic pressure and drop its load—potentially leading to injuries or equipment damage.
- Ferrules act as the first line of defense, ensuring connections remain secure even under high pressure and vibration.
Enhancing System Efficiency
- Leaks aren’t just dangerous—they waste hydraulic fluid, reducing system efficiency and increasing operational costs. By maintaining a tight seal, ferrules help keep systems running at peak performance.
Signs Your Ferrules Need Maintenance or Replacement
Ferrules are durable, but they’re not immune to wear and tear. Here are some signs it’s time for maintenance or replacement:
- Visible Cracks or Corrosion: If the ferrule shows wear, it could fail under pressure.
- Leaking Hydraulic Fluid: A sign that the ferrule is no longer providing a tight seal.
- Loose Connections: Vibration or pressure changes can cause ferrules to loosen over time.
Maintenance Tips for Hydraulic Ferrules
Ferrules might seem low-maintenance, but neglecting them can lead to costly failures. Here’s a more detailed look at how to maintain them effectively:
A. Inspection Checklist
- Look for cracks, deformation, or corrosion on the ferrules.
- Check for fluid leaks around ferrule connections. Even a small drip could indicate a compromised seal.
- Inspect the hose or tube for damage near the ferrule. If the hose looks worn, the ferrule may not provide a secure connection.
B. Cleaning Guidelines
- Use compressed air to remove dirt and debris from ferrule connections before installation.
- For heavily soiled ferrules, use a non-corrosive cleaning solvent like isopropyl alcohol or a mild degreaser.
- Avoid abrasive cleaners that might scratch the ferrule’s surface or compromise its seal.
C. Replacement Rules
- Replace ferrules if you notice:
- Significant corrosion.
- Visible damage, such as cracks or deformation.
- Persistent leaks after tightening.
- Pro Tip: Always replace ferrules during hose or tube replacement. Even if the ferrules look fine, old ferrules may not perform well with new components.
D. Preventive Maintenance
- Store spare ferrules in a dry, clean environment to prevent corrosion.
- Use protective caps or covers on unused hoses and ferrules to keep contaminants out.
- Train staff on proper installation techniques to avoid damaging ferrules during setup.
Conclusion
Ferrules might not get the spotlight, but they’re a cornerstone of hydraulic systems. Without them, achieving secure and efficient connections would be nearly impossible. Whether you’re working in construction, automotive, or manufacturing, using the right ferrules can ensure your system runs smoothly, safely, and effectively.
FAQs
1. What are ferrules in hydraulic systems?
Ferrules are small, cylindrical components—usually made of metal like stainless steel or brass—that secure hoses or tubes to fittings in hydraulic systems. They ensure leak-free, high-pressure connections.
2. Why are ferrules important in hydraulic systems?
Ferrules prevent leaks, maintain strong connections, and handle the extreme pressure and vibration common in hydraulic systems. They’re essential for the system’s safety, efficiency, and longevity.
3. How do I choose the right ferrule for my hydraulic system?
Select ferrules based on your system’s pressure rating, material compatibility (e.g., stainless steel for harsh environments), and the correct size to fit your hose or tube snugly.
4. Can ferrules be reused?
No, ferrules are typically designed for single-use only. Reusing them can compromise the seal, leading to leaks or system failure.
5. How often should ferrules be replaced?
Inspect ferrules regularly and replace them if they show signs of wear, corrosion, or damage. It’s also a good idea to replace ferrules whenever you replace hoses or tubes.
6. Are there different types of ferrules?
Yes, common types include single ferrules (low to medium pressure), double ferrules (high pressure), tapered ferrules (for flexible hoses), and flare ferrules (for tubing with flared ends).