Hydraulic systems are everywhere—from excavators at construction sites to forklifts lifting heavy pallets in warehouses. These powerful and reliable systems keep operations running smoothly, but they aren’t invincible. Over time, wear and tear, poor maintenance, or normal usage can reveal key hydraulic system repair signs that compromise performance.
Recognizing the signs of hydraulic system failure early can save you time, money, and frustration. Whether it’s a simple repair or a complete replacement, knowing what to look for is key to preventing downtime. Let’s dive deeper into the most detailed signs your hydraulic system might need attention.
1. Unusual Noises: A Warning You Shouldn’t Ignore
Hydraulic systems are designed to run smoothly and efficiently. So, if your machine starts making odd noises like grinding, hissing, knocking, or whining, it’s a sure sign that something’s wrong. These noises don’t just happen out of nowhere—they’re your system’s way of saying, “Help!”
Common Causes of Unusual Noises:
- Aeration (Air in the System):
Air bubbles trapped in the hydraulic fluid cause a foaming effect. When the fluid passes through pumps or valves, it creates a loud whining or hissing noise. Aeration also reduces the fluid’s ability to transfer pressure effectively. - Cavitation:
Cavitation occurs when the hydraulic pump doesn’t get enough fluid, causing vapor bubbles to form. These bubbles collapse violently, producing loud banging or knocking sounds. Over time, cavitation can severely damage pump components. - Worn Bearings or Gears:
Mechanical parts, such as bearings, can wear down over time, leading to grinding or screeching noises.
What You Can Do:
- Inspect the fluid levels immediately. Low levels can cause both aeration and cavitation.
- Check for leaks or blockages in the suction line.
- Replace worn-out parts like bearings, gears, or seals.
- If you’re unsure, consult a professional to perform a detailed inspection of your system.
Ignoring unusual noises will only exacerbate the problem, potentially leading to more expensive repairs or replacements.
2. Fluid Leaks: Spotting the Silent Saboteur
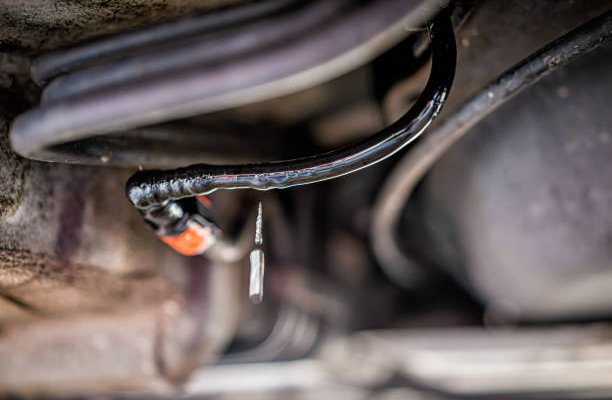
Leaks are perhaps the most noticeable sign of trouble in a hydraulic system. If you notice puddles of fluid under your equipment or see a consistent drop in fluid levels, it’s time to act.
Causes of Hydraulic Fluid Leaks:
- Worn Seals and O-Rings:
Over time, seals and O-rings degrade due to heat, pressure, or friction, leading to leaks. - Cracked Hoses or Tubing:
Hydraulic hoses, especially older ones, can crack under repeated bending, vibration, or high pressure. - Excessive System Pressure:
When pressure exceeds the system’s capacity, it can force fluid through weak points like seals or hose connections. - Loose Fittings:
Vibration and normal wear can cause fittings to loosen, leading to small leaks that grow over time.
Consequences of Ignoring Leaks:
- Performance Issues: Leaks reduce system pressure, leading to inefficient operation.
- Contamination Risks: External dirt and moisture can enter the system through the leak, contaminating the hydraulic fluid.
- Environmental Hazards: Spilled hydraulic fluid can harm the environment and create workplace hazards.
How to Fix Leaks:
- Replace damaged seals, O-rings, or hoses promptly.
- Tighten loose fittings.
- Use high-quality replacement components designed for your system.
- Perform regular inspections to catch leaks before they grow.
3. Sluggish Performance: When Your System Feels Tired
A healthy hydraulic system should operate smoothly and quickly. But if you notice your machinery taking longer to perform basic tasks or struggling under normal loads, it’s a sign of internal issues.
What Causes Sluggish Performance?
- Contaminated Fluid:
Hydraulic fluid contaminated with dirt, water, or metal particles can clog filters, reduce lubrication, and damage components. - Worn-Out Pumps or Motors:
Aging pumps and motors lose efficiency, resulting in a lack of power. - Restricted Flow:
Blocked filters or lines can choke the flow of fluid, causing slow and uneven performance. - Low Fluid Levels:
Insufficient hydraulic fluid reduces pressure, limiting the system’s ability to perform effectively.
Signs to Look Out For:
- Delayed or jerky movement in equipment
- Reduced lifting or pushing capacity
- Overheating during normal operation
Fixes and Preventive Measures:
- Regularly inspect and replace filters.
- Drain and replace contaminated hydraulic fluid.
- Check fluid levels and refill as needed.
- Have pumps and motors tested by a professional to determine if they need repair or replacement.
4. Overheating: A Critical Red Flag
Hydraulic systems are designed to handle heat, but when temperatures soar beyond normal limits, it’s a clear sign of trouble. Persistent overheating can lead to catastrophic failures if left unchecked.
What Causes Overheating?
- Low Fluid Levels:
Insufficient fluid reduces the system’s ability to dissipate heat. - Poor Fluid Quality:
Old or degraded hydraulic fluid can’t cool or lubricate components effectively. - Blocked Heat Exchangers or Radiators:
Clogged cooling systems can trap heat, causing the system to overheat. - Excessive Load:
Operating machinery beyond its capacity increases strain and heat generation.
Why Overheating Is Dangerous:
- Degraded seals and hoses due to excessive heat exposure
- Reduced fluid viscosity, leading to poor lubrication and efficiency
- Thermal decomposition of hydraulic fluid, creating sludge and deposits
What to Do:
- Inspect and clean heat exchangers and radiators.
- Replace old or contaminated hydraulic fluid.
- Monitor fluid levels regularly.
- Reduce system load or cycle time to prevent overheating.
5. Erratic Movements: The Sign of Something Misaligned
Hydraulic machinery is designed for smooth and precise movements. When it starts jerking, stalling, or moving unpredictably, there’s usually a deeper issue at play.
What Causes Erratic Movements?
- Air in the System:
Trapped air creates inconsistent fluid flow, leading to jerky movements. - Sticky or Malfunctioning Valves:
Dirt, debris, or worn-out parts can cause control valves to stick or operate inconsistently. - Worn Components:
Pistons, seals, or other internal components that have worn out can’t maintain proper performance.
Solutions:
- Bleed the system to remove trapped air.
- Clean and lubricate valves to ensure smooth operation.
- Replace worn or damaged components.
6. Contaminated Hydraulic Fluid: The Silent Killer
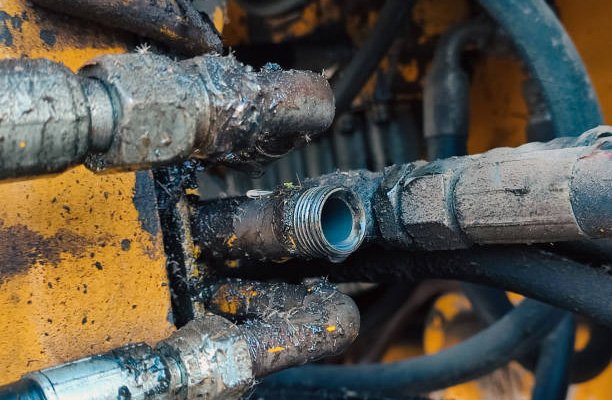
Hydraulic fluid contamination is a leading cause of system failure. While it’s not always visible, its effects are significant and often devastating.
Types of Contamination:
- Water:
Water in the fluid causes rust, reduces lubrication, and leads to poor system performance. - Particles:
Dirt, metal shavings, or other debris can cause abrasive wear on components. - Degraded Fluid:
Overheated or old fluid can break down chemically, forming sludge and reducing efficiency.
How to Prevent Contamination:
- Use sealed storage containers for hydraulic fluid.
- Install high-quality filters and replace them regularly.
- Inspect and replace seals to prevent contaminants from entering the system.
7. Pressure Drops: A System Losing Its Power
Hydraulic systems rely on consistent pressure to function effectively. A drop in pressure is often a sign of leaks, blockages, or failing components.
How to Diagnose a Pressure Drop:
- Check for visible leaks in hoses, seals, or fittings.
- Test the pump for signs of wear or inefficiency.
- Inspect filters and valves for blockages.
8. Frequent Repairs: When It’s Time to Say Goodbye
If your hydraulic system requires constant repairs, it may no longer be cost-effective to keep it running. Consider replacing the system if repair costs outweigh replacement costs or if the system’s performance is severely impacting productivity.
Conclusion
Catching issues early is the key to maintaining a reliable and efficient hydraulic system. Don’t ignore the warning signs—whether it’s unusual noises, fluid leaks, or sluggish performance. Addressing these problems early will save you time, money, and downtime.
FAQs
1. How often should I service my hydraulic system?
It’s recommended to perform basic inspections weekly and schedule professional maintenance every 3-6 months, depending on the intensity of use.
2. What are the most common causes of hydraulic system failure?
The top causes include fluid contamination, worn seals or components, low fluid levels, overheating, and leaks. Regular maintenance can help prevent these issues.
3. Can I use any hydraulic fluid for my system?
No, always use the hydraulic fluid recommended by the manufacturer. Using the wrong type can cause damage and reduce system efficiency.
4. How do I know if my hydraulic fluid is contaminated?
Look for signs like cloudy or milky fluid (indicating water contamination), dark or sludgy fluid, and strange odors. Contaminated fluid often leads to performance issues.
5. What should I do if my hydraulic system is overheating?
Check for low fluid levels, blocked cooling systems, or excessive system loads. Replace old fluid and ensure the cooling components are working properly.
6. When should I replace my hydraulic system instead of repairing it?
Consider replacing the system if repairs are frequent, costs exceed 50% of the replacement value, or the system is outdated and incompatible with modern equipment.