Hydraulic systems are the powerhouse behind countless industrial and commercial applications—from powering heavy construction equipment to driving precision machinery in factories. However, if you don’t properly maintain a hydraulic system, its performance can degrade quickly, leading to inefficiency, costly downtime, or even complete failure. To keep things running smoothly, it’s crucial to develop a consistent maintenance routine and follow best practices. This comprehensive guide will help you learn how to maintain a hydraulic system for maximum efficiency, longevity, and reliable performance.
Why Hydraulic System Maintenance Is Non-Negotiable
Hydraulic systems rely on a fine balance of precision, pressure, and fluid movement. Neglecting maintenance disrupts this balance and can lead to the following problems:
1. Reduced System Performance
Contaminants, leaks, or worn components can cause your system to lose power or respond sluggishly, reducing productivity.
2. Frequent Downtime
Unexpected failures mean unscheduled repairs, halting operations and leading to significant financial losses.
3. Costly Repairs
Neglected systems are more prone to severe damage, such as pump or cylinder failure, requiring expensive parts and labor to fix.
4. Safety Hazards
Malfunctioning hydraulic systems can result in hazardous situations, particularly in high-pressure applications.
Hydraulic Fluid: The Lifeblood of Your System
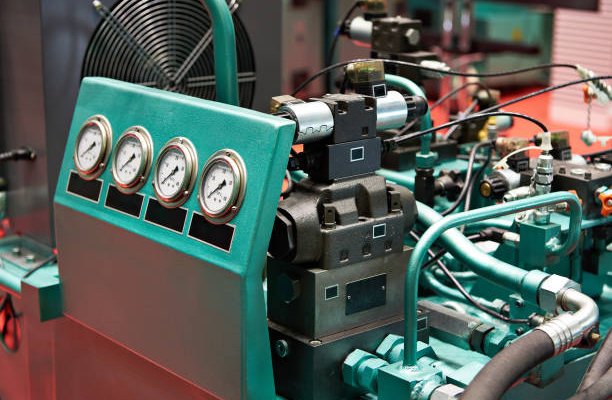
The hydraulic fluid is the single most critical component of any hydraulic system. Think of it as the bloodstream that keeps everything running. Neglecting fluid care is one of the fastest ways to destroy system efficiency.
a) Monitor Fluid Levels
Regularly check the fluid reservoir to ensure it’s filled to the recommended level. Low fluid levels lead to cavitation—a condition where air pockets form in the fluid, causing erratic behavior and potential damage.
- Tip: Implement a daily or weekly check for fluid levels depending on your system’s usage intensity.
b) Change the Fluid Regularly
Hydraulic fluid wears down due to heat, oxidation, and contamination. Follow the fluid change schedule recommended by your system’s manufacturer.
- Signs You Need a Fluid Change:
- Dark, discolored fluid
- Strong burnt smell
- Decreased system performance
c) Test the Fluid for Contaminants
Use a fluid analysis kit to measure particle contamination, water content, and fluid health. Contaminated fluid can erode components and drastically reduce system efficiency.
- Pro Tip: Aim for cleanliness levels specified by the ISO 4406 standard for hydraulic systems.
d) Choose the Right Fluid
Every hydraulic system is designed to use specific fluid types (e.g., mineral oil-based, synthetic, or water-glycol fluids). Using the wrong fluid can compromise performance, corrode components, and void warranties.
Filters: Your System’s Protective Shield
Filters prevent contaminants from entering critical components of the hydraulic system, like pumps and valves. A clogged or ineffective filter can cause significant damage.
a) Regular Filter Checks
Inspect filters at regular intervals. Modern hydraulic systems often have a clogging indicator that lets you know when the filter is becoming saturated.
- Common Filter Locations:
- Return-line filters
- Pressure-line filters
- Suction filters
b) Replace Filters When Needed
Even the best filters have a finite lifespan. Replace them as per the manufacturer’s schedule or sooner if contamination levels are high.
- DIY Tip: Keep spare filters on hand to avoid downtime during replacements.
c) Upgrade Filters if Necessary
Consider upgrading to higher-efficiency filters if your system operates in a harsh or dirty environment. High-performance filters can capture smaller particles, keeping your system cleaner for longer.
Conduct Routine Inspections
Routine inspections are the backbone of hydraulic system maintenance. They help catch problems early, saving you time and money.
a) Look for Leaks
Hydraulic leaks often occur at hose connections, fittings, or seals. A small leak may not seem like a big deal, but it can reduce pressure and lead to fluid loss over time.
- Quick Tip: Place absorbent pads under your system to spot small leaks that might not be visible otherwise.
b) Inspect Hoses and Fittings
Hoses are prone to wear from high pressure, temperature fluctuations, and bending. Look for:
- Cracks
- Abrasions
- Bulges
Replace worn hoses immediately to avoid sudden failures.
c) Examine Cylinders and Pumps
Check for signs of excessive heat, vibration, or noise during operation. These are often early warning signs of internal damage.
- Pro Tip: Use thermal imaging cameras to detect hotspots in cylinders or pumps that indicate potential failures.
Keep Your System Spotlessly Clean
Cleanliness cannot be overstated when it comes to hydraulic systems. Contaminants like dirt, water, or even small metal particles can damage components and disrupt operations.
a) Clean Reservoirs and Components
Before opening the system (e.g., to check fluid or replace parts), clean the surrounding area to prevent contaminants from entering.
b) Use Quality Breathers
Install high-quality breather caps on reservoirs. These caps allow air exchange while preventing dirt or moisture from entering.
c) Flush the System Periodically
Flushing removes built-up contaminants from the entire hydraulic circuit. This process is especially crucial after major repairs or when changing the type of hydraulic fluid.
Recognize Warning Signs Early
Hydraulic systems often exhibit warning signs before a failure occurs. Pay attention to these red flags to maintain hydraulic system:
- Sluggish Performance: Indicates fluid contamination or a worn-out pump.
- Noisy Operation: A whining or banging sound could mean air is trapped in the system.
- Overheating: Excessive heat might signal clogged filters, inadequate fluid, or faulty components.
By addressing these symptoms promptly, you can prevent small issues from escalating into major problems.
Train Operators and Technicians
Even the best maintenance practices will fall short if your team isn’t properly trained. An educated workforce is critical to system longevity.
a) Teach Operators How to Spot Issues
Operators are often the first to notice performance changes. Train them to recognize early signs of trouble, like odd noises or reduced power.
b) Develop Standard Procedures
Create a standardized maintenance checklist. This ensures every team member follows the same steps when inspecting or servicing the hydraulic system.
c) Invest in Advanced Training
For complex systems, send your technicians to specialized training programs offered by equipment manufacturers or industry experts.
Use Proper Tools and Equipment
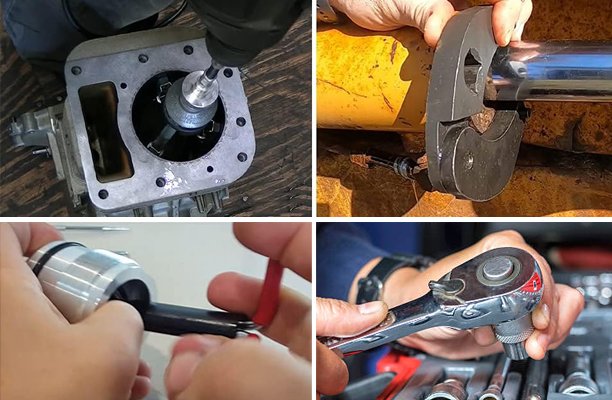
Having the right tools ensures accurate diagnostics and safe maintenance. Here’s what you’ll need:
- Pressure Gauges: To monitor system pressure and identify irregularities.
- Thermal Cameras: Detect overheating components in real-time.
- Fluid Testing Kits: Test for contamination, water content, and fluid degradation.
- Torque Wrenches: Secure connections to the correct specifications without over-tightening.
Follow Manufacturer’s Recommendations
Your system’s manual is your best friend when it comes to maintenance. It provides detailed guidelines specific to your equipment.
a) Adhere to Maintenance Schedules
The manual outlines the ideal schedule for fluid changes, filter replacements, and inspections. Stick to it for optimal results.
b) Use OEM Parts
Avoid aftermarket parts unless specifically approved by the manufacturer. OEM (Original Equipment Manufacturer) parts ensure compatibility and maintain warranty coverage.
c) Leverage Troubleshooting Guides
When issues arise, refer to the manual’s troubleshooting section to diagnose problems quickly and accurately.
Conclusion
A well-maintained hydraulic system doesn’t just save you money—it ensures reliability, safety, and peak performance for years to come. By focusing on hydraulic fluid care, routine inspections, and training your team, you can avoid costly downtime and maximize system efficiency.
Take proactive measures today, and your hydraulic system will reward you with long-lasting performance and fewer headaches down the road!
FAQs
Q1: What happens if I don’t maintain my hydraulic system?
Neglecting maintenance leads to performance issues, frequent breakdowns, safety risks, and higher long-term costs.
Q2: How do I prevent hydraulic fluid contamination?
Use quality filters, breather caps, and follow clean maintenance practices like wiping components before opening the system.
Q3: Can I overfill the fluid reservoir?
Yes, overfilling can cause overflow and create pressure imbalances. Always follow the recommended levels in your system’s manual.
Q4: How often should I inspect my hydraulic system?
Routine checks should be performed daily, weekly, or monthly, depending on usage. Conduct in-depth inspections quarterly or annually.
Q5: Can I use a generic filter for my hydraulic system?
It’s best to use manufacturer-recommended filters. Generic filters may not provide adequate protection, potentially harming your system.
Q6: How can I reduce wear and tear on hydraulic components?
To reduce wear and tear on hydraulic components, ensure you use clean, high-quality hydraulic fluid, replace filters regularly, and avoid overloading the system. Monitoring system pressure, maintaining proper fluid levels, and addressing leaks or minor issues immediately can also help minimize unnecessary strain on parts.