Hydraulic systems play a vital role in a wide range of industries, from construction to manufacturing and beyond. These systems rely on hydraulic fittings to ensure a secure connection between components, allowing high-pressure fluid to flow efficiently. However, improper tightening of these fittings can lead to serious issues, including leaks, reduced system performance, and even safety hazards.
Achieving a leak-free connection requires more than just brute force; it involves understanding the type of fittings, adhering to manufacturer specifications, and following best practices. In this guide, we’ll explore the nuances of tightening hydraulic fittings, discuss common challenges, and provide step-by-step instructions to ensure optimal results. Whether you’re a seasoned technician or a beginner, this resource will help you maintain the integrity of your hydraulic systems.
Understanding Hydraulic Fittings
What Are Hydraulic Fittings?
Hydraulic fittings are critical components in hydraulic systems, serving as connectors between hoses, tubes, and other components. These fittings facilitate the transfer of hydraulic fluid under high pressure, ensuring a reliable flow and preventing leaks. Their design allows them to withstand extreme pressures and environments, making them essential for system efficiency and safety.
Types of Hydraulic Fittings
Hydraulic fittings come in various types, each suited to specific applications. Understanding these types can help you select the right fitting for your needs:
- Threaded Fittings: These include JIC (Joint Industry Council), NPT (National Pipe Thread), and BSP (British Standard Pipe) fittings. They rely on threads to create a seal, often supplemented with thread tape or sealant.
- O-Ring Fittings: Equipped with an O-ring to provide a secure, leak-proof seal. Common examples include ORFS (O-Ring Face Seal) and SAE (Society of Automotive Engineers) fittings.
- Flare and Compression Fittings: These fittings create a seal by deforming a tube or using a compression ring, offering high reliability in various pressure conditions.
Materials and Coatings
Hydraulic fittings are made from materials like stainless steel, brass, and carbon steel. The choice of material depends on factors such as operating pressure, fluid compatibility, and environmental conditions. Many fittings also feature protective coatings to resist corrosion, extending their lifespan in harsh environments.
The Consequences of Improper Tightening
Leaks and Pressure Loss
Improperly tightened hydraulic fittings are one of the leading causes of leaks in hydraulic systems. A loose fitting may allow hydraulic fluid to escape, resulting in a drop in system pressure. This not only compromises performance but can also lead to downtime and increased operational costs as the issue is diagnosed and repaired.
Equipment Damage
Overtightening hydraulic fittings can be just as problematic as under-tightening. Excessive force can damage the threads or deform the fitting, making it prone to failure. Stripped threads or crushed seals often require component replacement, adding to maintenance costs and delays.
Safety Hazards
Leaks from improperly tightened fittings can pose significant safety risks. Escaping hydraulic fluid under high pressure can cause injuries, and spilled fluid may create slip hazards or damage the surrounding environment. In extreme cases, catastrophic system failure can occur, endangering personnel and equipment.
Preparing for Fitting Tightening
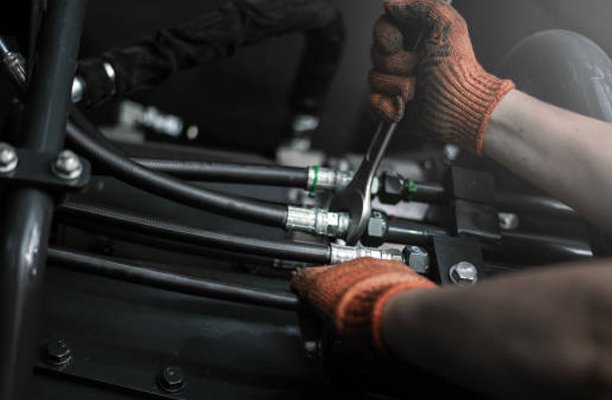
Tools and Equipment Needed
To ensure proper tightening of hydraulic fittings, having the right tools is essential. Some of the most commonly used tools include:
- Torque Wrenches: Provide precise control over the amount of force applied, helping to avoid overtightening or undertightening.
- Thread Sealants: Used to ensure a leak-proof seal. Options include thread tape (PTFE tape) and liquid sealants.
- Lubricants: Reduce friction and ensure smoother tightening, particularly for metal-to-metal connections.
Inspection of Components
Before tightening, it’s crucial to inspect all components for any signs of damage or wear. Look for stripped threads, cracked seals, or deformations in the fitting. Using compromised components can lead to poor performance and increased risk of failure.
Understanding Manufacturer Specifications
Each fitting is designed to operate within specific parameters, including torque values and pressure ratings. Always refer to the manufacturer’s guidelines to determine the correct tightening procedures. Ignoring these specifications can result in leaks or damaged components.
Step-by-Step Guide to Tightening Hydraulic Fittings
Step 1: Clean the Components
Before assembling and tightening hydraulic fittings, ensure all components are clean and free from debris. Old thread sealant, dirt, or metal shavings can prevent a proper seal and compromise the integrity of the connection. Use a clean, lint-free cloth and, if necessary, a solvent to clean the threads and sealing surfaces.
Step 2: Apply Sealants or Lubricants
For threaded fittings, apply thread tape or liquid sealant to ensure a leak-free connection. When using thread tape, wrap it around the male threads in the direction of tightening, starting a few threads back from the end to avoid contamination of the hydraulic fluid. For O-ring fittings, lubricate the O-ring with a compatible lubricant to prevent pinching or damage during tightening.
Step 3: Align the Fittings
Proper alignment of the fittings is crucial to prevent stress on the connection. Misaligned fittings can cause leaks, increase wear, and reduce system efficiency. Before tightening, ensure that the fittings are properly oriented and aligned with the connected components.
Step 4: Tighten the Fitting
Begin by hand-tightening the fitting to ensure the threads engage properly. Then, use a torque wrench to apply the manufacturer-recommended torque value. Avoid overtightening, as this can damage the threads or deform the sealing surfaces. If no torque specifications are available, tighten the fitting until it is snug and then apply a quarter-turn for optimal sealing.
Common Mistakes to Avoid
Overtightening
One of the most common mistakes when tightening hydraulic fittings is applying too much force. Overtightening can damage threads, crush seals, or deform the fitting, compromising the integrity of the connection. It’s crucial to use a torque wrench and adhere to the manufacturer’s recommended torque values to avoid this issue.
Using Incorrect Tools
Hydraulic fittings require specific tools for proper installation. Using inappropriate tools, such as pliers or adjustable wrenches, can damage the fitting surfaces or fail to provide the necessary precision. Always use tools like torque wrenches, spanner wrenches, or fitting-specific tools for best results.
Ignoring Manufacturer Guidelines
Every hydraulic fitting has specific requirements for installation, including torque values, sealant use, and alignment procedures. Ignoring these guidelines can lead to leaks, pressure loss, and premature failure. Always consult the manufacturer’s instructions before tightening fittings.
Maintenance and Inspection Tips
Regular Checks for Leaks
Inspect hydraulic fittings regularly for signs of leaks. Look for visible fluid, wetness around the fittings, or pressure drops in the system. Early detection of leaks can prevent minor issues from becoming major problems, reducing downtime and maintenance costs.
Monitoring Torque Settings
Over time, vibration and pressure fluctuations can loosen hydraulic fittings. Periodically check the torque on fittings to ensure they remain within the manufacturer’s recommended range. Avoid tightening beyond the original torque specification to prevent damage.
Replacing Worn Components
Fittings, O-rings, and seals are subject to wear and tear over time. Regularly inspect these components for cracks, deformation, or other signs of deterioration. Replace any damaged parts immediately to maintain the system’s performance and prevent leaks.
Advanced Techniques for Professional Installations
Using Hydraulic Fitting Gauges
Hydraulic fitting gauges are specialized tools designed to measure the alignment and tightness of fittings accurately. These gauges help ensure that fittings are installed within the correct parameters, reducing the risk of leaks and improving overall system reliability.
Applying Torque Indicators
Torque indicators are an advanced tool that ensures precise tightening by providing visual or digital feedback when the correct torque value is reached. These indicators are particularly useful for high-precision applications or in systems where over- or under-tightening can have significant consequences.
Training for Technicians
Proper training for technicians is essential for ensuring professional hydraulic fitting installations. Training programs should cover topics such as understanding torque specifications, using advanced tools, and following industry best practices. Well-trained technicians can significantly reduce the risk of system failure and improve system longevity.
Industry Standards and Compliance
ISO Standards for Hydraulic Fittings
Hydraulic fittings are often manufactured to meet ISO (International Organization for Standardization) standards, which ensure global compatibility and quality. Adhering to these standards helps maintain the reliability and safety of hydraulic systems across industries. Examples include ISO 8434 for metallic tube connections and ISO 3601 for O-ring specifications.
Environmental Considerations
Hydraulic systems must comply with environmental regulations to minimize their ecological impact. This includes using fittings that prevent leaks, reducing hydraulic fluid waste, and ensuring proper disposal of used components. Selecting fittings with eco-friendly coatings or materials can further support sustainability goals.
Meeting Safety Regulations
Compliance with safety standards is critical in industries where hydraulic systems operate under high pressures and challenging conditions. Regulatory bodies, such as OSHA (Occupational Safety and Health Administration) in the United States, set guidelines to ensure worker safety and prevent accidents. Using fittings that meet these requirements can help organizations avoid penalties and maintain safe working environments.
Troubleshooting Common Issues
Persistent Leaks
Even after proper tightening, leaks can sometimes persist. This issue may be caused by damaged threads, worn seals, or improperly aligned components. To address the problem, inspect the affected area closely, replace faulty parts, and ensure proper alignment before retightening.
Damaged Threads
Threads on hydraulic fittings can become stripped or damaged due to overtightening, corrosion, or cross-threading. Damaged threads compromise the seal and can lead to leaks. The solution often involves replacing the fitting or, in some cases, rethreading the component using specialized tools.
Seal Failures
Seal failures are a common cause of hydraulic system issues. O-rings and other seals can degrade over time due to wear, temperature fluctuations, or exposure to incompatible fluids. Identifying the cause of the failure and replacing the seal with a compatible, high-quality alternative can resolve this problem.
The Role of Technology in Hydraulic Fittings
Smart Fittings and Monitoring Systems
Advancements in technology have introduced smart fittings equipped with sensors that monitor pressure, temperature, and vibration in real time. These systems provide valuable data that can help predict and prevent potential issues, improving system reliability and reducing downtime.
Digital Torque Tools
Digital torque tools are revolutionizing the tightening process by offering precise control and feedback. These tools ensure that fittings are tightened to the exact torque specifications, reducing the risk of overtightening or undertightening. Many models also log torque data for compliance and quality control purposes.
Automated Assembly Systems
In industrial settings, automated systems are increasingly used to assemble and tighten hydraulic fittings. These systems use robotic arms and advanced software to achieve consistent and accurate results, enhancing efficiency and reducing human error.
Conclusion
Properly tightening hydraulic fittings is a critical aspect of maintaining the efficiency, safety, and longevity of hydraulic systems. By understanding the different types of fittings, using the correct tools, and adhering to manufacturer guidelines, you can prevent leaks, minimize downtime, and avoid costly repairs.
From basic preparation steps to advanced technologies like digital torque tools and smart monitoring systems, there are numerous ways to ensure leak-free and reliable performance. Regular inspections and maintenance further enhance system integrity, reducing the likelihood of failure and extending the life of your equipment.
Whether you’re an experienced technician or new to hydraulic systems, following these best practices will help you achieve optimal results and maintain the highest standards of safety and performance in your operations.
FAQs
1. What is the best way to tighten hydraulic fittings without causing damage?
The best way to tighten hydraulic fittings is to start by hand-tightening and then using a torque wrench to apply the manufacturer-recommended torque value. This ensures a secure connection without over- or under-tightening.
2. How can I identify if a hydraulic fitting is overtightened?
Signs of overtightening include deformed threads, crushed seals, and difficulty in removing the fitting. Overtightened fittings may also show stress fractures or leak due to damaged sealing surfaces.
3. Are there universal torque values for all hydraulic fittings?
No, torque values vary based on the type, size, and material of the fitting. Always refer to the manufacturer’s specifications to determine the correct torque value for your specific application.
4. When should I replace hydraulic fittings instead of retightening them?
You should replace hydraulic fittings if they show signs of damage, such as stripped threads, cracks, or deformation. Fittings that consistently leak despite proper tightening should also be replaced.
5. What is the difference between thread sealant and thread tape?
Thread sealant (often a liquid or paste) creates a secure, leak-proof seal and is commonly used in permanent installations. Thread tape, typically made from PTFE, is wrapped around threads to create a temporary seal and is often used for connections requiring disassembly.
6. What should I do if a hydraulic fitting continues to leak after tightening?
If a hydraulic fitting continues to leak after proper tightening, inspect the threads, seals, and alignment for damage or wear. Replace any faulty components and ensure that the fitting is properly aligned before retightening. If the problem persists, consult the manufacturer or a hydraulic specialist for further guidance.