Introduction
Hydraulic systems are essential in various industries, including automotive, aerospace, construction, and heavy machinery. These systems rely on pressurized fluid to generate force and movement, making them integral to modern engineering. However, maintaining the integrity of a hydraulic system requires strong and reliable fastening solutions.
Bolts play a critical role in securing hydraulic components, ensuring leak-proof connections and maintaining system efficiency. Without proper bolting techniques, hydraulic leaks, pressure failures, and even catastrophic system breakdowns can occur. In this article, we’ll explore how bolts are used in hydraulic systems, the types of bolts best suited for these applications, and best practices for their installation and maintenance.
Understanding Hydraulic Systems
A hydraulic system operates based on Pascal’s Law, which states that when pressure is applied to a confined fluid, it transmits force equally in all directions. This principle allows hydraulic systems to generate immense power using relatively small components.
Key Components of a Hydraulic System
- Hydraulic Pump – Generates pressure to move the fluid.
- Valves – Control the direction and pressure of the hydraulic fluid.
- Cylinders – Convert hydraulic energy into mechanical force.
- Hoses and Fittings – Transport the pressurized fluid.
- Bolts and Fasteners – Secure hydraulic components and prevent fluid leaks.
Since hydraulic systems operate under extreme pressure, every connection point must be robust and leak-proof. This is where high-strength bolts come into play, ensuring that joints, flanges, and other hydraulic elements remain tightly secured.
The Role of Bolts in Hydraulic Systems
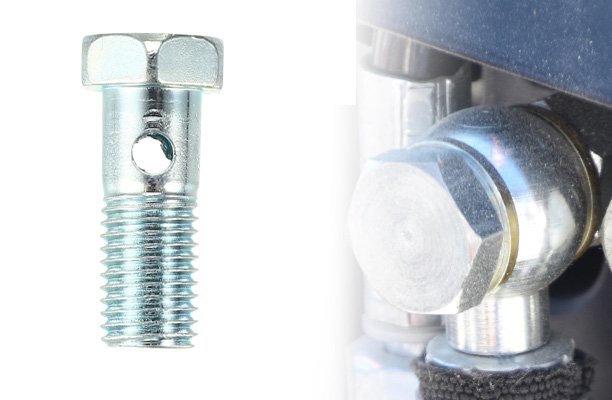
Bolts serve multiple essential functions in hydraulic systems, including:
- Ensuring Secure Connections – Hydraulic fittings, valves, and flanges need tightly fastened bolts to prevent leaks.
- Maintaining System Efficiency – Loose bolts can cause pressure drops, reducing system performance.
- Enhancing Safety – Properly torqued bolts minimize the risk of sudden failures in high-pressure environments.
- Preventing Vibrational Loosening – Hydraulic machinery often operates in high-vibration settings, requiring special bolting techniques to maintain stability.
Because hydraulic systems often deal with thousands of PSI (pounds per square inch) of pressure, using the right bolts with the correct torque settings is crucial to avoid breakdowns and costly repairs.
Types of Bolts Used in Hydraulic Systems
Selecting the right type of bolt for hydraulic applications is crucial for ensuring the system’s durability and efficiency. Different bolt types serve various purposes, depending on factors like pressure, vibration, and material compatibility.
Common Bolt Types for Hydraulic Systems
- High-Strength Structural Bolts
- Used in critical load-bearing hydraulic applications.
- Designed to withstand extreme pressure and stress.
- Typically made from alloy steel for superior strength.
- Flange Bolts
- Ideal for securing hydraulic fittings and pressure-tight connections.
- Feature a built-in washer-like flange to distribute load evenly.
- Help prevent leaks by maintaining a tight seal under pressure.
- Hex Bolts vs. Socket Head Bolts
- Hex Bolts: Commonly used for general hydraulic connections; easily tightened with wrenches.
- Socket Head Bolts: Preferred in compact hydraulic assemblies where space is limited.
- Anti-Corrosion and Coated Bolts
- Used in outdoor or marine hydraulic systems to resist rust and wear.
- Coatings like zinc, cadmium, and galvanization enhance durability.
Using the appropriate bolt type helps maintain system integrity, reduces maintenance needs, and prolongs the lifespan of hydraulic equipment.
Bolt Materials and Coatings for Hydraulic Systems
The material and coating of bolts used in hydraulic systems significantly impact their performance, longevity, and resistance to environmental factors.
Common Bolt Materials
- Stainless Steel – Offers corrosion resistance but may not have the highest strength.
- Alloy Steel – Strong and durable, ideal for high-pressure applications.
- Titanium – Lightweight and corrosion-resistant, often used in aerospace hydraulics.
Protective Coatings for Hydraulic Bolts
- Zinc Coating – Prevents corrosion but may wear off over time.
- Cadmium Plating – Provides excellent corrosion resistance, especially in marine environments.
- Galvanization – A thick protective layer that enhances durability in harsh conditions.
The right combination of material and coating ensures bolts can withstand hydraulic pressures, environmental exposure, and long-term wear.
Bolt Tightening Techniques in Hydraulic Systems
Proper bolt tightening is essential to prevent leaks, maintain pressure stability, and ensure the overall safety of the hydraulic system.
Best Practices for Bolt Tightening
- Follow Manufacturer Torque Specifications
- Over-tightening can damage threads and crush hydraulic seals.
- Under-tightening can lead to leaks and pressure loss.
- Use the Right Tightening Tools
- Hydraulic Torque Wrenches – Ideal for high-precision applications.
- Manual Torque Wrenches – Suitable for small to mid-sized hydraulic systems.
- Pneumatic Wrenches – Useful for large-scale industrial hydraulic setups.
- Prevent Bolt Loosening in High-Vibration Environments
- Use lock washers or thread-locking compounds to secure bolts.
- Implement double-nut techniques to add extra stability in mobile hydraulic machinery.
By applying the correct tightening methods, hydraulic systems can avoid common issues such as pressure leaks, bolt fatigue, and system inefficiencies.
Common Challenges in Using Bolts for Hydraulic Applications
While bolts are essential for securing hydraulic components, improper selection or installation can lead to serious issues. Below are some common challenges and how to address them.
1. Bolt Fatigue and Failure
- Hydraulic systems operate under extreme pressure and vibration, causing bolts to weaken over time.
- Solution: Use high-strength bolts designed for hydraulic applications and conduct regular inspections.
2. Preventing Leaks Due to Improper Bolt Tightening
- Loose bolts can cause hydraulic fluid leaks, leading to performance issues and safety risks.
- Solution: Always use the correct torque settings and tightening sequence recommended by manufacturers.
3. Over-Tightening and Its Impact on Hydraulic Seals
- Excessive force can deform seals, leading to leaks and pressure loss.
- Solution: Use a torque wrench to apply the precise amount of force.
By understanding these challenges, engineers and maintenance teams can implement preventive measures to enhance system reliability.
Best Practices for Bolt Selection and Installation in Hydraulics
Selecting the right bolts and installing them properly can significantly impact the efficiency and safety of hydraulic systems.
1. Choosing the Right Bolt Type and Material
- Consider factors like pressure, vibration, and environmental exposure.
- Use stainless steel or alloy steel bolts for high-pressure applications.
2. Applying Correct Torque Specifications
- Follow manufacturer guidelines to prevent leaks and system failures.
- Use calibrated torque wrenches for accuracy.
3. Ensuring Proper Bolt Alignment
- Misaligned bolts can lead to uneven stress distribution.
- Check for proper alignment before tightening.
4. Conducting Regular Bolt Inspections
- Inspect bolts for signs of wear, corrosion, or loosening.
- Replace damaged bolts immediately to maintain system integrity.
Implementing these best practices can extend the lifespan of hydraulic components and prevent costly downtime.
Bolt Safety Considerations in Hydraulic Systems
Safety is a top priority when working with hydraulic systems, as improper bolting can lead to catastrophic failures.
1. Ensuring Secure Connections in High-Pressure Systems
- Hydraulic systems operate at thousands of PSI, making secure bolting essential.
- Always double-check bolt tightness before pressurizing the system.
2. Preventing Catastrophic Failures
- A single loose or damaged bolt can lead to leaks, pressure loss, or even system rupture.
- Use locking mechanisms like lock washers and thread-locking compounds for added security.
3. Compliance with Industry Standards
- Ensure bolts meet ISO, ASME, and SAE standards for hydraulic applications.
- Using certified bolts helps maintain quality and safety compliance.
By following these safety considerations, hydraulic systems can operate efficiently while minimizing risks.
Industry Applications of Bolts in Hydraulic Systems
Bolts play a critical role in securing hydraulic components across multiple industries. Their proper selection and use ensure system stability, safety, and efficiency.
1. Automotive and Heavy Machinery
- Hydraulic bolts secure braking systems, steering components, and suspension systems in vehicles.
- Heavy machinery like excavators and bulldozers rely on durable bolts to handle extreme pressure and vibration.
2. Aerospace and Aviation Hydraulics
- Aircraft rely on high-strength, lightweight bolts to secure hydraulic actuators for landing gear, flaps, and brakes.
- Aerospace bolts must meet strict industry standards (e.g., AS9100) to ensure safety and reliability.
3. Industrial and Construction Equipment
- Hydraulic systems power cranes, forklifts, and hydraulic presses.
- Bolts prevent leaks and pressure loss in high-load-bearing applications.
4. Marine and Offshore Hydraulic Systems
- Used in ship steering mechanisms, winches, and offshore drilling rigs.
- Corrosion-resistant bolts are crucial due to constant exposure to moisture and saltwater.
The reliability of bolts in these applications ensures optimal performance and minimizes downtime.
Innovations in Bolt Technology for Hydraulic Systems
As technology advances, bolt designs are evolving to improve efficiency, durability, and safety in hydraulic applications.
1. Smart Bolts with Tension-Monitoring Technology
- Embedded sensors measure real-time tension and torque levels, preventing failures.
- Alerts maintenance teams to replace or tighten bolts before failure occurs.
2. Advanced Coatings for Extended Lifespan
- Self-lubricating coatings reduce friction and prevent galling in high-pressure environments.
- Corrosion-resistant alloys improve performance in harsh conditions.
3. Lightweight Yet Strong Composite Bolts
- Carbon-fiber and titanium bolts offer high strength with reduced weight.
- Used in aerospace and automotive applications where weight reduction is crucial.
These innovations enhance hydraulic system safety and performance while reducing maintenance needs.
Case Studies: Real-World Use of Bolts in Hydraulic Systems
Examining real-world applications helps illustrate the importance of proper bolt selection and installation.
1. Hydraulic Failure Due to Improper Bolting
- A construction crane experienced hydraulic system failure due to improperly torqued bolts, leading to costly downtime.
- Lesson learned: Proper torque application and regular inspections are crucial for preventing failures.
2. Successful Application of Advanced Bolts in Hydraulic Presses
- A manufacturing company improved hydraulic press efficiency using high-strength, corrosion-resistant bolts.
- Result: Increased lifespan of equipment and reduced maintenance costs.
By analyzing these cases, industries can adopt best practices for maintaining secure hydraulic systems.
How to Maintain Bolts in Hydraulic Systems
Regular maintenance of bolts in hydraulic systems is essential to ensure system longevity, prevent failures, and maintain efficiency.
1. Periodic Inspection Schedules
- Inspect bolts weekly or monthly, depending on system usage and operating conditions.
- Look for signs of wear, corrosion, and loosening that could compromise performance.
2. Detecting and Replacing Worn-Out Bolts
- Replace bolts with signs of fatigue, rust, or deformation immediately.
- Use only manufacturer-approved replacement bolts to ensure compatibility.
3. Lubrication and Anti-Seize Applications
- Apply anti-seize compounds to prevent galling and thread wear.
- Use hydraulic-compatible lubricants to ensure smooth bolt tightening and removal.
Implementing these maintenance practices reduces downtime and enhances system reliability.
Conclusion
Bolts play a vital role in securing hydraulic components, preventing leaks, and ensuring safety in high-pressure environments. The right bolt selection, proper installation, and routine maintenance are crucial to hydraulic system efficiency.
By using high-strength, corrosion-resistant bolts, applying the correct torque, and following industry best practices, businesses can extend the lifespan of their hydraulic systems and reduce costly repairs.
As technology evolves, innovations in bolt materials, coatings, and smart monitoring systems will further enhance hydraulic system performance. Investing in the right bolting solutions today ensures long-term reliability and safety in any hydraulic application.
FAQs
1. What type of bolts are best for high-pressure hydraulic systems?
High-strength alloy steel or stainless steel bolts with corrosion-resistant coatings are ideal for high-pressure hydraulic applications.
2. How often should bolts in hydraulic systems be inspected?
Inspection frequency depends on system usage, but bolts should generally be checked weekly or monthly for signs of wear, corrosion, or loosening.
3. What happens if bolts are over-tightened in a hydraulic system?
Over-tightening can deform hydraulic seals, cause leaks, and lead to component failure. Always follow manufacturer-recommended torque specifications.
4. Are stainless steel bolts good for hydraulic applications?
Yes, stainless steel bolts offer corrosion resistance, making them suitable for marine and outdoor hydraulic systems. However, they may not have the highest tensile strength compared to alloy steel.
5. How do I prevent bolts from loosening in hydraulic machinery?
Use lock washers, thread-locking compounds, and double-nut techniques to prevent bolts from loosening in high-vibration environments.