Hose ferrules are small but indispensable components in a wide range of industrial and mechanical systems — from hydraulic assemblies to pneumatic tools and fuel lines. These cylindrical metal sleeves are responsible for clamping the hose to the fitting, creating a secure, leak-free seal that can withstand high pressure, temperature changes, and vibrations. Timely hose ferrule replacement is essential to prevent leaks, system failures, and costly downtime in demanding environments.
Failure to replace a worn-out or damaged ferrule in time can result in devastating consequences such as leaks, machine malfunction, production downtime, or even serious safety hazards. That’s why early detection is essential.
In this in-depth guide, we’ll walk through the top 5 signs that your hose ferrule needs replacement, explaining how to identify them, why they occur, and what to do about them. Whether you’re a maintenance engineer, a technician, or an industrial operator, understanding these signs can save you time, money, and a potential disaster.
1. Visible Cracks or Corrosion
Why Physical Damage is a Red Flag
Hose ferrules operate under harsh environmental conditions. Over time, the material — typically steel, stainless steel, brass, or aluminum — can suffer from fatigue, oxidation, and mechanical wear. This makes visible surface damage the most immediate and easiest-to-spot warning sign that a ferrule needs to be replaced.
What to Inspect
- Cracks: Fine or wide surface fractures, especially at the edges or along the crimped area.
- Pitting corrosion: Localized corrosion that creates small cavities, especially in marine or chemical environments.
- Rust: Discoloration, orange-brown flakes, or powdery residues, which indicate oxidation of iron-based ferrules.
- Deformation: Flattened or misshapen ferrules, often caused by excess crimping force or mechanical impact.
Consequences of Ignoring It
A cracked or corroded ferrule weakens the overall clamping force and introduces points of failure where leaks can start. In hydraulic systems, this can result in fluid spray — a serious safety risk, especially under high pressure. Additionally, corrosion can spread to nearby components and accelerate systemic degradation.
2. Leaking Fluids at the Fitting
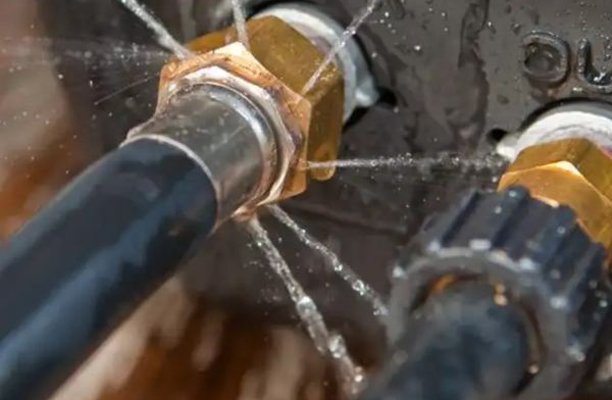
One of the Earliest and Most Common Warning Signs
If you notice oil, coolant, hydraulic fluid, or any other medium leaking at the hose-ferrule junction, it’s a clear indication that the seal has been compromised. This may stem from a damaged ferrule, improper crimping, wear from pressure cycling, or internal corrosion that weakens the clamping bond.
Root Causes of Leakage
- Internal wear: Prolonged use can cause microscopic wear inside the ferrule, loosening the seal.
- Thermal expansion: Frequent heating and cooling cycles cause materials to expand and contract, stressing the joint.
- Improper crimp angle or pressure: Poorly installed ferrules may appear intact but fail to create a uniform seal.
How to Confirm a Leak is Ferrule-Related
To verify that the leak is due to the ferrule and not the hose or fitting:
- Use a UV dye or leak detection fluid around the suspected area.
- Check for wetness at the transition between the hose cover and the metal ferrule.
- Monitor system pressure drops and fluid level inconsistencies.
Pro Tip:
Always depressurize the system before inspecting or replacing the ferrule. In high-pressure environments, a tiny leak can evolve into a dangerous jet of fluid capable of piercing skin or damaging equipment.
3. Hose Slippage or Loose Fitting
Understanding Ferrule-Grip Failure
The ferrule’s primary function is to mechanically compress the hose onto the fitting, creating a firm grip that maintains the integrity of the connection under pressure. If the hose begins to slip, rotate, or pull out of the ferrule, it’s a clear signal that the ferrule is no longer performing effectively.
Causes of Slippage
- Improper Crimping: Incorrect crimp diameter, uneven crimp force, or off-center alignment during installation can result in an insufficient grip.
- Hose Material Degradation: Exposure to chemicals, heat, or UV radiation can soften the hose material, reducing friction and allowing movement.
- Ferrule Fatigue: With repeated use and pressure cycling, the ferrule may expand or deform slightly, loosening its grip.
What to Look For
- Hose appears pulled out or misaligned with the fitting.
- The ferrule spins freely or shifts when touched.
- System pressure fluctuates unexpectedly or becomes difficult to maintain.
Why This Matters
Loose hose connections introduce a high risk of sudden hose ejection or fluid blowout, especially in hydraulic or high-pressure pneumatic systems. This not only risks costly equipment damage but also endangers nearby personnel.
4. Unusual Noises or Vibrations
Audible and Physical Warnings
Strange sounds or vibrations in your system may be symptomatic of a failing ferrule. These symptoms usually indicate that the internal components are no longer aligned correctly, allowing movement or gaps in the connection point that shouldn’t exist in a properly crimped system.
What to Watch (and Listen) For
- Hissing: Often points to a slow air or fluid leak under pressure — a sign of a compromised seal.
- Rattling or Clicking: May result from micro-movements of the hose inside a loose ferrule.
- Increased Vibration: Especially if localized around the fitting or hose end, indicates joint instability or misalignment.
Technical Insight
Vibration is not only a symptom but also a contributor to ferrule failure. Persistent vibration can accelerate wear at the joint, leading to fatigue cracks, premature loosening, or even structural failure. If left unchecked, the vibration cycle can spiral into a full mechanical breakdown.
Inspection Tip
Use a mechanic’s stethoscope or vibration sensor to isolate noise sources in complex systems. Compare vibration readings at the hose end with baseline levels to identify anomalies.
5. Age and Wear from Extended Use
When Time Takes Its Toll
Like any mechanical component, hose ferrules have a limited service life. Even if no visible damage is present, internal fatigue from pressure cycles, heat exposure, and environmental factors will eventually degrade their performance.
Key Factors Affecting Lifespan
- Operating Pressure: Higher pressures accelerate material fatigue, especially near the crimp zone.
- Temperature Extremes: Metal expansion and contraction stress the ferrule-hose interface.
- Chemical Exposure: Some fluids can cause internal corrosion or weaken the hose/ferrule bond.
- Number of Cycles: Systems with frequent start-stop operations or pressure changes degrade components faster.
Recommended Replacement Intervals
Always follow OEM (Original Equipment Manufacturer) guidelines for ferrule replacement intervals. As a general rule of thumb:
- Replace ferrules in critical applications every 12-18 months, regardless of visible damage.
- For low-risk environments, extend replacement to 24-36 months with regular inspections.
Preventive Maintenance Advice
Log system hours, pressure cycles, and temperature exposures in a maintenance record. Implementing a predictive maintenance schedule can drastically reduce the risk of catastrophic failure due to ferrule aging.
Conclusion
Hose ferrules might seem like minor components, but they are vital to the integrity and safety of fluid handling systems. Failing to recognize the early signs of ferrule deterioration can lead to significant equipment failure, safety risks, and unplanned downtime. This is particularly critical in industries that depend on high-pressure systems, such as hydraulics, fuel delivery, and manufacturing automation.
By understanding and monitoring these five warning signs — visible damage, fluid leakage, hose slippage, abnormal noise/vibration, and age-related wear — maintenance professionals can take proactive steps to avoid system failure. Whether you’re operating on a factory floor or in the field, regular inspection and timely replacement of worn-out ferrules should be a standard part of your maintenance strategy.
Additionally, always choose the right ferrule material and type for your specific hose and application. Use manufacturer guidelines and certified equipment to ensure proper crimping and installation. In many cases, the quality of your ferrule can make the difference between peak performance and operational downtime.
Remember: a $5 part failure can lead to $5,000 in damage — prevention is always more cost-effective than repair.
FAQs
1. What is a hose ferrule and why is it important?
A hose ferrule is a cylindrical metal sleeve that compresses over the hose and fitting, locking them together. It ensures leak-free, secure connections that can handle high pressures and prevent hose detachment.
2. Can I reuse an old ferrule when replacing the hose?
No. Ferrules are designed for single-use only. Reusing them compromises the integrity of the crimp and increases the risk of failure. Always install a new ferrule with a new hose assembly.
3. How often should ferrules be inspected in industrial systems?
Ferrules should be visually inspected during every scheduled maintenance cycle. In high-risk or high-pressure systems, weekly or even daily inspections may be necessary depending on use and exposure conditions.
4. What tools are required for replacing a hose ferrule?
You’ll need a hose crimping machine (manual, hydraulic, or electric), compatible ferrules, new hose fittings, calipers for measurement, and safety gear like gloves and eye protection. Follow the manufacturer’s crimp specs exactly.
5. What material ferrules are best for corrosive environments?
Stainless steel ferrules are typically best for harsh or corrosive environments due to their superior resistance to rust, chemicals, and temperature extremes. For lower-pressure or non-corrosive setups, brass or aluminum may suffice.