When you’re working on a project that requires fittings, whether it’s for plumbing, a marine application, or industrial machinery, the choice of material can make a huge difference. Two popular options are brass and bronze fittings. At first glance, these metals might seem similar—they both have that classic, warm metallic tone—but they each have their own unique properties that make them better suited for different tasks. In this article, we’ll explore the key differences between brass vs. bronze fittings, helping you determine which is the right choice for your specific needs.
Choosing fittings might seem straightforward, but when you consider the importance of durability, corrosion resistance, and cost-effectiveness, the decision becomes more complex. Brass and bronze are both copper alloys that have been used for centuries in a variety of applications. However, they are not interchangeable, and the decision between the two can significantly impact the performance and longevity of your project.
Brass, with its bright, gold-like appearance, offers excellent workability and versatility. In contrast, bronze, which has a darker and more reddish hue, offers strength and corrosion resistance, especially in harsh environments like the open sea. By understanding the specific properties and best uses for each material, you can ensure that your fittings will stand the test of time and meet the demands of your project.
What Are Brass and Bronze Made Of?
To truly understand why brass and bronze perform differently, it’s important to start with their composition. These alloys are both primarily made from copper, but their secondary components make all the difference.
Brass Composition:
Brass is an alloy composed mainly of copper and zinc. The ratio of these two metals can vary, resulting in different types of brass with distinct properties. Typically, brass contains between 55% and 95% copper, with the remainder being zinc. The higher the zinc content, the stronger and more ductile the brass becomes. Additionally, adding small amounts of elements like lead, aluminum, or tin can enhance specific characteristics, such as corrosion resistance or machinability. For example, leaded brass is easier to machine, making it a popular choice in manufacturing.
Bronze Composition:
Bronze is also a copper alloy, but its primary additive is tin, typically comprising 12% to 15% of the alloy, with copper making up the balance. The presence of tin makes bronze harder and more resistant to wear compared to brass. Like brass, bronze can also include other elements such as aluminum, manganese, nickel, or phosphorus, depending on the intended application. For example, aluminum bronze offers exceptional strength and corrosion resistance, making it a popular choice for marine environments.
Understanding the basic composition of these alloys gives insight into their respective strengths and weaknesses, guiding you in selecting the best material for your specific needs.
How Do They Look and Feel?
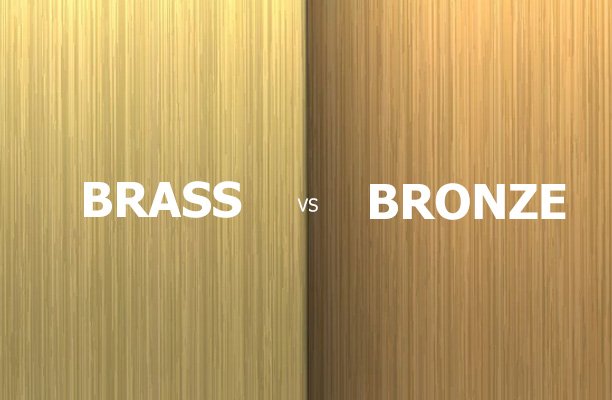
Now, let’s talk about how these metals look and feel—because that can also affect your choice.
Brass Characteristics:
Brass has a bright, yellowish-golden hue, which makes it particularly attractive for decorative purposes. It often finds use in visible settings, such as homes, musical instruments, and architectural accents. The metal’s relative softness and malleability allow it to be easily shaped into various designs. This softness also contributes to brass’s machinability, allowing manufacturers to create precise fittings with tight tolerances.
The tactile feel of brass is smooth and somewhat lighter compared to bronze. This makes brass fittings easier to handle and install, particularly in plumbing and HVAC systems where precision is key.
Bronze Characteristics:
Bronze, on the other hand, has a deeper, reddish-brown color, often with a slightly matte finish that can develop a greenish patina over time due to oxidation. This patina is often seen as desirable, especially in outdoor settings, as it adds an antique or rustic charm to the metal. The hardness of bronze is immediately apparent when handling it—bronze fittings are heavier and more robust, with a denser feel that speaks to their durability.
While not as easily machinable as brass, bronze’s hardness means it can withstand higher levels of stress and friction. This makes it an ideal material for fittings that need to endure tough conditions, such as in industrial machinery or marine environments.
How Do They Stand Up to Corrosion?
One of the most important factors to consider is how well these metals resist corrosion, especially if you’re working in an environment that’s harsh or exposed to the elements.
Brass Corrosion Resistance:
Brass generally resists corrosion, especially in freshwater environments, which is why it’s commonly used in plumbing applications. However, brass is susceptible to a process known as dezincification. This occurs when the zinc in brass leaches out, leaving behind a porous and weakened copper structure. Dezincification often occurs in environments where brass is exposed to chlorides, such as saltwater or areas with high chlorine levels. To address this, manufacturers developed dezincification-resistant (DZR) brass for use in harsher environments.
Despite this potential downside, brass fittings perform well in a wide range of settings, especially when properly selected and maintained. For indoor plumbing and HVAC systems, where the environment remains controlled and mild, brass fittings deliver a reliable and long-lasting solution.
Bronze Corrosion Resistance:
Bronze, by contrast, is highly resistant to corrosion, particularly in saltwater environments. For indoor plumbing and HVAC systems, where the environment remains controlled and not overly harsh, brass fittings provide a reliable and long-lasting solution. The tin in bronze plays a significant role in enhancing its corrosion resistance, making it much less likely to degrade over time compared to other metals.
Additionally, bronze’s ability to develop a protective patina helps further shield it from the elements. This patina forms a barrier that slows down the rate of corrosion, effectively extending the life of the fitting. As a result, bronze fittings frequently find use in outdoor applications, industrial settings, and situations where long-term durability is crucial.
Durability and Strength
When it comes to durability and strength, both metals have their strengths—but in different ways.
Brass Durability and Strength:
Brass is known for being strong yet ductile, meaning it can withstand significant stress without breaking. However, because it is softer than bronze, it may not be the best choice for applications that involve heavy wear or high pressure. Brass’s strength lies in its balance of durability and ease of use. It’s tough enough for most standard applications, like plumbing and HVAC, while still being easy to machine and install.
One of the advantages of brass is its ability to form tight seals, which is why it’s so popular in plumbing. Brass fittings solder or braze easily, forming secure, leak-proof connections that handle the pressures in most residential and commercial systems. However, in situations with high mechanical stress or abrasive conditions, brass may wear down faster than bronze.
Bronze Durability and Strength:
Bronze, on the other hand, is significantly harder than brass. The hardness of bronze increases its resistance to wear, making it a common choice for applications with constant friction or heavy loads. For example, marine environments favor bronze fittings for propellers, pumps, and other equipment that must withstand the harsh conditions of seawater and mechanical stress.
In industrial settings, where machinery is subjected to constant use, bronze fittings hold up better over time. Their high resistance to wear and tear means that they are less likely to deform or break under pressure, reducing the need for frequent replacements. This durability can lead to long-term cost savings, despite the higher initial cost of bronze fittings compared to brass.
Applications: Where Do Brass and Bronze Fittings Fit Best?
Understanding the typical applications of brass and bronze helps you determine which material best suits your needs. Both metals are versatile and applicable in various settings, but each excels in specific use cases.
Common Applications for Brass Fittings:
- Plumbing: Brass fittings are a staple in the plumbing industry. Both residential and commercial plumbing systems widely use them for connecting pipes, controlling water flow, and ensuring leak-free connections. Brass’s resistance to water corrosion, combined with its ease of machining, makes it ideal for creating the intricate shapes needed in plumbing fittings.
- HVAC Systems: In HVAC systems, brass fittings commonly connect pipes and components, regulate the flow of refrigerants, and ensure tight seals that prevent leaks. The ability of brass to withstand moderate pressures and temperatures makes it a reliable choice in these systems.
- Musical Instruments: Brass is also used in the manufacture of musical instruments like trumpets, trombones, and saxophones. The metal’s acoustic properties, along with its ease of forming into complex shapes, make it ideal for creating instruments that produce a clear, bright sound.
- Decorative Hardware: Beyond its functional uses, brass is often chosen for decorative hardware, such as doorknobs, handles, and light fixtures. Its bright, golden color adds a touch of elegance to homes and buildings, making it a popular choice for interior design.
Common Applications for Bronze Fittings:
- Marine Industry: The marine industry heavily relies on bronze fittings due to their exceptional corrosion resistance in saltwater environments. Bronze is used in a wide range of marine applications, including ship propellers, through-hull fittings, and pumps. Its durability ensures that these components can withstand the harsh conditions of the sea, providing long-lasting performance with minimal maintenance.
- Industrial Machinery: In industrial machinery, bronze fittings are used in applications where high wear resistance is required. This includes bearings, bushings, and gears, where the metal’s ability to withstand constant friction and pressure is critical. The hardness and strength of bronze make it the preferred choice for machinery that operates under heavy loads or in abrasive conditions.
- Electrical Contacts: Bronze is also commonly used in electrical connectors and contacts. Its excellent conductivity, combined with its durability, makes it suitable for electrical components that need to endure long-term use without degrading.
- Sculpture and Art: Due to its ability to be cast into detailed shapes and its aesthetically pleasing finish, bronze has been a favored material for sculptures and art pieces for centuries. The patina that develops over time adds character to the metal, making bronze statues and ornaments highly valued.
Cost Considerations: How Much Will It Set You Back?
Cost is another big factor when choosing between brass and bronze. Here’s how they stack up.
Cost of Brass Fittings:
Brass is generally more affordable than bronze. The cost of brass fittings can vary depending on the specific alloy used and the current market prices for copper and zinc. Brass’s lower cost makes it an attractive option for a wide range of applications, especially in large-scale projects where budget constraints are a concern.
However, while brass is less expensive upfront, it’s important to consider the long-term costs. In environments where corrosion or wear is a concern, the potential for dezincification or mechanical failure could lead to higher maintenance costs and the need for more frequent replacements.
Cost of Bronze Fittings:
Bronze fittings are typically more expensive due to the higher cost of tin and the additional benefits they provide. The superior durability and corrosion resistance of bronze can justify the higher price, particularly in applications where long-term performance is critical.
In industrial settings, the durability of bronze can also translate into lower downtime and repair costs, making it a cost-effective choice despite the higher upfront cost.
Manufacturing Process: How Are Brass and Bronze Fittings Made?
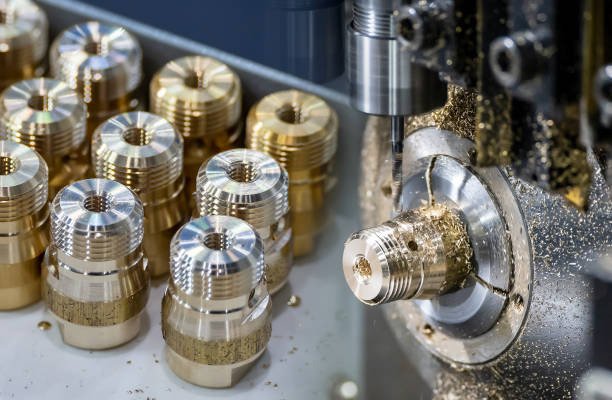
The manufacturing process of brass and bronze fittings plays a crucial role in determining their final properties and performance. Both metals are typically processed using casting, but there are differences in how each material is handled.
Manufacturing Brass Fittings:
Brass fittings are often produced through casting, forging, or extrusion. Casting involves pouring molten brass into molds to create the desired shape. Because brass is relatively easy to work with, it can be cast into complex and intricate shapes with high precision. This is particularly important for fittings that require tight tolerances and exact specifications.
Forging brass involves shaping the metal with compressive forces, which enhances its strength and grain structure. In contrast, extrusion pushes brass through a die to form long shapes like rods or pipes, which can later be cut and shaped into fittings.
Brass’s malleability makes it ideal for manufacturing, enabling the creation of fittings that are both functional and visually appealing.
Manufacturing Bronze Fittings:
Casting typically manufactures bronze fittings, as the higher melting point and fluidity of bronze make it well-suited to this process. The bronze casting process involves pouring molten bronze into a mold, where it cools and hardens into the desired shape. Since bronze is harder and denser than brass, it creates fittings that are strong and able to handle high pressures and stresses.
Bronze’s ability to fill molds completely and create dense, durable castings makes it the preferred method for producing heavy-duty fittings that need to endure demanding conditions. The resulting fittings are less likely to have internal voids or weaknesses, ensuring a long service life.
Environmental Impact: How Green Are Brass and Bronze?
In today’s world, the environmental impact of the materials we use is becoming increasingly important.
Brass:
Brass is highly recyclable, which is a big plus from an environmental perspective. In fact, a lot of the brass in use today comes from recycled materials, reducing the need for new mining and refining.
Bronze:
Like brass, bronze is also highly recyclable. Its durability means that bronze fittings tend to last longer, which can reduce waste and environmental impact over time.
Choosing the Right Fitting: Brass or Bronze?
When deciding between brass and bronze fittings, consider the following factors:
Consider the Environmental Conditions:
If harsh environmental conditions, such as saltwater or chemicals, will expose your fittings, bronze is usually the better choice due to its superior corrosion resistance. For marine applications, outdoor use, or industrial settings where the environment is challenging, bronze’s ability to withstand these conditions without degrading makes it the ideal material.
Think About Mechanical Stress:
For applications where the fittings will experience high levels of mechanical stress, friction, or pressure, bronze’s higher hardness and wear resistance make it the preferred option. Bronze fittings are less likely to deform or wear out under stress, providing a longer service life and reducing the need for replacements.
Weigh the Costs:
If cost is a major factor in your decision, and the environment in which the fittings will be used is relatively benign, brass may be the more cost-effective choice. Brass provides a good balance of durability, machinability, and corrosion resistance at a lower cost, making it suitable for a wide range of applications where extreme conditions are not a concern.
Consider Aesthetic Preferences:
If the appearance of the fittings is important—such as in decorative applications or where the fittings will be visible—brass’s bright, golden color may be more appealing. However, if you prefer a more antique or rustic look, or if the fittings will develop a patina over time, bronze may be the better choice.
Conclusion
Choosing between brass and bronze fittings is more than just a matter of preference; it’s about selecting the right material for the job. By considering factors such as composition, durability, corrosion resistance, cost, and the specific needs of your project, you can ensure that your fittings will deliver the performance and longevity you require. Whether you’re working on a residential plumbing system, an industrial machine, or a marine vessel, understanding the key differences between brass and bronze will help you make the best choice for your project’s success.
FAQs
What’s the difference between brass and bronze fittings?
Brass is an alloy of copper and zinc, while bronze is primarily made from copper and tin. Brass is softer and more malleable, whereas bronze is harder and more durable.
Which metal resists corrosion better—brass or bronze?
Bronze generally offers better corrosion resistance, especially in marine environments where it’s exposed to saltwater.
Can brass and bronze fittings be used interchangeably?
While they can be used in some similar applications, they are not always interchangeable. The choice depends on factors like the environment and mechanical stress.
Is brass cheaper than bronze?
Yes, brass is typically more affordable than bronze, making it a good option for cost-sensitive projects.
What are the best uses for brass fittings?
Brass fittings are commonly used in plumbing, HVAC systems, and musical instruments due to their corrosion resistance and ease of machining.
How can you tell brass from bronze?
Brass usually has a brighter, yellowish color, while bronze is darker and more reddish-brown. Bronze is also harder and heavier than brass.