Hydraulic systems are like the lifeblood of modern machinery, and hydraulic hoses play a crucial role in keeping everything running smoothly. The braid layer of a hydraulic hose is especially important—it provides the reinforcement needed to handle immense pressures and maintain system safety.
Choosing the right hydraulic hose braid layer isn’t a one-size-fits-all process. You need to think about pressure ratings, flexibility, environmental challenges, and application-specific requirements. In this detailed guide, we’ll walk you through everything you need to know to make an informed decision.
What is a Hydraulic Hose Braid Layer?
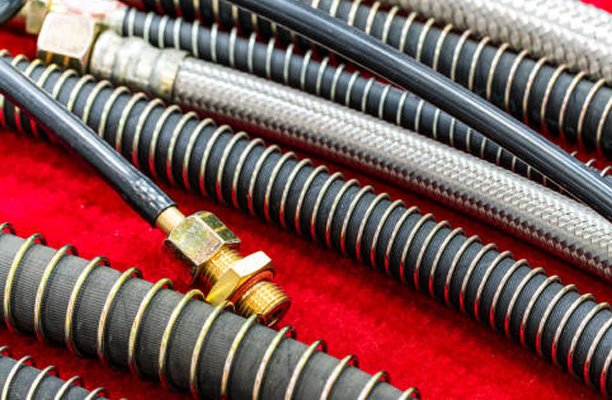
A hydraulic hose has three main components:
- Inner Tube: This layer carries hydraulic fluids and must resist chemical reactions with those fluids.
- Reinforcement Layer: The braided layer sits here, providing strength and pressure tolerance.
- Outer Cover: Protects the hose from abrasion, heat, and external damage.
The braid layer is made by weaving steel wire, synthetic fibers, or textiles in a crisscross pattern around the inner tube. This reinforcement gives the hose its ability to withstand high-pressure conditions while maintaining flexibility.
Here’s why the braid layer is crucial:
- Pressure Resistance: It strengthens the hose to handle varying pressure levels.
- Flexibility: Ensures the hose can bend and fit into tight spaces without kinking.
- Durability: Reinforcement protects the inner tube from external damage or sudden pressure spikes.
Now, let’s break down the types of braid layers to better understand what makes them suitable for different systems.
Types of Hydraulic Hose Braid Layers
Hydraulic hoses are available with single, double, or multiple braid layers. Understanding each type helps you choose the best option for your specific needs.
1. Single Wire-Braided Hydraulic Hoses
Single-braided hoses feature one layer of wire reinforcement. They’re designed for low to medium-pressure applications and are often more lightweight and flexible than other options.
- Construction: One layer of woven steel wire or synthetic braid surrounding the inner tube.
- Pressure Capacity: Typically supports pressures up to 3,000 PSI, but the exact rating depends on the hose’s size and material.
- Applications: Ideal for general-purpose tasks like construction equipment, agricultural machinery, and light industrial applications.
Advantages:
- Lightweight, making installation easier.
- More flexible than double or multi-layer braided hoses.
- Cost-effective for systems operating under moderate pressures.
Limitations:
- Can’t handle the extreme pressures required by heavy-duty machinery.
- May wear out faster in high-stress environments or with frequent pulsations.
Best Use Cases:
- Hydraulic steering systems.
- Return lines for hydraulic fluid.
- Low-pressure systems in light machinery.
2. Double Wire-Braided Hydraulic Hoses
Double-braided hoses take things up a notch by adding an extra layer of wire reinforcement. This makes them suitable for medium to high-pressure applications.
- Construction: Two layers of wire reinforcement, woven in opposite directions, providing additional strength and durability.
- Pressure Capacity: Generally handles pressures of up to 6,000 PSI, depending on hose specifications.
- Applications: Used in industrial machinery, construction equipment, and heavy-duty vehicles that operate under higher pressures.
Advantages:
- Stronger and more durable than single-braided hoses.
- Able to withstand higher pressure levels without rupturing.
- Suitable for dynamic environments where hoses face frequent movement.
Limitations:
- Slightly less flexible than single-braided hoses, which can make installation trickier in tight spaces.
- More expensive than single-braided options.
Best Use Cases:
- Excavators, loaders, and other construction equipment.
- Hydraulic power lines in industrial systems.
- Hydraulic systems with frequent pulsations or pressure spikes.
3. Multi-Layer Braided Hydraulic Hoses
Multi-layer braided hoses (with three or more braid layers) are built to handle ultra-high pressures and harsh environmental conditions. They’re the workhorses of hydraulic systems used in mining, offshore drilling, and heavy-duty industrial applications.
- Construction: Three or more wire or synthetic braid layers stacked for maximum reinforcement.
- Pressure Capacity: Exceeds 6,000 PSI, making them suitable for extreme environments and high-pressure systems.
- Applications: Ultra-high-pressure systems in industries like oil and gas, mining, and defense.
Advantages:
- Provides unmatched pressure tolerance and reliability.
- Designed for extreme environments, including high temperatures and harsh chemicals.
- High safety factor due to its robust design.
Limitations:
- Very rigid and heavy, making them difficult to install in flexible or compact spaces.
- Expensive compared to single- and double-braided hoses.
Best Use Cases:
- Hydraulic fracturing (fracking) operations.
- Equipment used in mining and offshore drilling.
- Industrial hydraulic presses and cranes.
Factors to Consider When Choosing a Hydraulic Hose Braid Layer
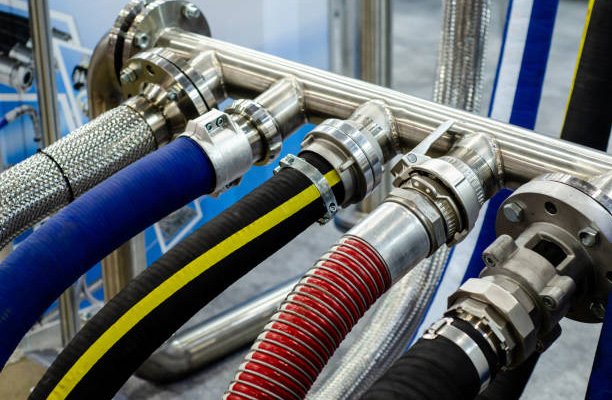
Choosing the right braid layer involves more than just knowing the pressure requirements. Let’s explore other critical factors:
1. System Pressure Requirements
Start by checking your hydraulic system’s maximum operating pressure.
- Low Pressure (<3,000 PSI): Single-braided hoses are sufficient.
- Medium to High Pressure (3,000–6,000 PSI): Double-braided hoses are your go-to.
- Ultra-High Pressure (>6,000 PSI): Multi-layer braided hoses or spiral hoses are needed.
Tip: Always choose a hose with a pressure rating at least 25% higher than your system’s maximum pressure to account for pressure spikes.
2. Flexibility Needs
Hoses need to navigate tight spaces in many systems. Single-braided hoses are the most flexible, while multi-layer hoses are stiffer. If flexibility is critical, opt for single or double-braided options.
3. Environmental Challenges
Consider what your hose will face in its environment:
- High Temperatures: Use heat-resistant outer covers and internal materials.
- Abrasion Risks: Go for hoses with abrasion-resistant outer coatings.
- Chemical Exposure: Ensure compatibility with the chemicals or hydraulic fluids your system uses.
4. Budget
The cost of the hose depends on the braid layer. While single-braided hoses are budget-friendly, multi-layer hoses are more expensive due to their robust construction.
Hydraulic Hose Braid vs. Spiral Hoses: Which One is Right for You?
When it comes to hydraulic hose reinforcements, braided and spiral designs dominate the market. Here’s how they differ:
- Braided Hoses:
- More flexible and lightweight.
- Suitable for low to medium pressures.
- Best for applications that need maneuverability.
- Spiral Hoses:
- Built with layers of spirally wrapped wire reinforcement.
- Designed for ultra-high pressure and heavy pulsations.
- Stiffer and less flexible but more durable under heavy-duty conditions.
Common Mistakes to Avoid
Avoid these pitfalls to ensure your hydraulic system runs smoothly:
- Underestimating Pressure Requirements: Always choose a hose with a pressure rating above your system’s maximum.
- Ignoring the Environment: Make sure the hose is built for the chemicals, temperatures, or abrasions it will face.
- Neglecting Flexibility: A stiff hose in a compact system will fail over time.
- Skipping Inspections: Regular maintenance prevents costly downtime and catastrophic failures.
Conclusion
Choosing the right hydraulic hose braid layer is critical for system safety, reliability, and performance. By understanding the differences between single, double, and multi-layer hoses and considering your system’s pressure, flexibility, and environmental needs, you’ll make a choice that saves time, money, and headaches in the long run.
FAQs
Q1: Can I use a single-braided hose for a high-pressure system?
A: No, single-braided hoses are designed for low to medium-pressure applications, typically below 3,000 PSI. For high-pressure systems, it’s recommended to use a double-braided or multi-layer braided hose for added strength and safety.
Q2: How do I determine the correct hose size for my hydraulic system?
A: The key measurement is the inner diameter (ID) of the hose, which must match your system’s flow requirements to avoid pressure drops or inefficiencies. Use the “Dash Size” system (e.g., -04 for 1/4″) or consult the manufacturer’s specifications.
Q3: How do braided hoses compare to spiral hoses?
A: Braided hoses are more flexible and lightweight, making them suitable for low to medium-pressure systems. Spiral hoses, on the other hand, are less flexible but can handle ultra-high pressures and heavy pulsations, making them ideal for heavy-duty applications.
Q4: How often should hydraulic hoses be replaced?
A: Hydraulic hoses typically last between 1-5 years, depending on usage and environmental conditions. Regular inspections are crucial, and hoses showing signs of wear—such as leaks, cracks, or blisters—should be replaced immediately to avoid system failure.
Q5: What factors should I consider when choosing a hose braid layer?
A: Key factors include:
- Pressure Requirements: Ensure the hose’s pressure rating exceeds your system’s operating pressure.
- Flexibility: Single-braided hoses are more flexible, while multi-layer hoses are more rigid.
- Environmental Conditions: Consider heat, abrasion, and chemical exposure in your application.
- Budget: Balance performance needs with cost to avoid under- or over-engineering your system.
Q6: Are there special hydraulic hoses for extreme environments?
A: Yes, multi-layer braided hoses or spiral hoses are designed for extreme environments, such as high temperatures, harsh chemicals, and abrasive conditions. These hoses often feature heat-resistant or chemical-resistant outer covers for added durability.