Valves are the unsung heroes of fluid control systems, ensuring that liquids, gases, or vapors flow smoothly and efficiently. But when it comes to choosing between control valves and shut-off valves, things can get a bit tricky. Each type has distinct functions and is suited to different scenarios.
This blog delves into every aspect of these two valve types, from how they work to when and why you’d use one over the other. By the end, you’ll have a clear understanding of which valve will best meet your operational needs.
Understanding Control Valves: The Brain of Fluid Systems
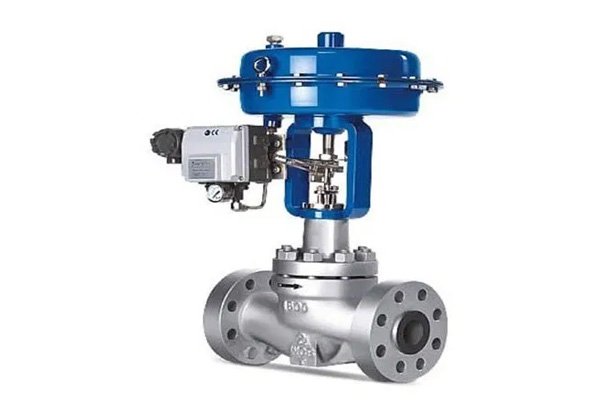
What Are Control Valves?
A control valve is a versatile device that modulates the flow, pressure, or temperature of a fluid within a system. Unlike simple on/off mechanisms, control valves offer a wide range of control positions, allowing precise adjustments based on system requirements.
Key Features of Control Valves:
- Adjustable Flow: Control valves can modulate flow based on real-time system demands.
- Automated Operation: Often connected to a control system or PLC (Programmable Logic Controller) for precise adjustments.
- Variable Positions: Unlike on/off valves, control valves can be partially open or closed.
- Applications: Commonly found in chemical plants, oil refineries, and HVAC systems.
Types of Control Valves:
- Globe Valves: Designed for precise throttling.
- Butterfly Valves: Lightweight, efficient, and great for large flow volumes.
- Ball Valves: Not ideal for precision but can be adapted for control purposes in some systems.
How Control Valves Work
Control valves operate using an actuator and a valve body:
- Actuator: Converts energy (usually electrical, pneumatic, or hydraulic) into mechanical motion to move the valve.
- Valve Body: Contains the fluid passage and the regulating component (e.g., plug, disk, or ball).
They’re typically integrated into automated systems where they respond to feedback signals from sensors, keeping conditions like pressure or temperature within desired limits.
Key Components of Control Valves
- Positioner: Ensures the valve opens/closes to the correct degree based on control signals.
- Valve Actuator: Moves the valve stem to regulate flow.
- Body and Trim: Designed to handle the specific fluid, pressure, and temperature requirements.
Advantages of Control Valves
- Precision Control: Enables fine-tuned adjustments for optimal performance.
- Automated Operation: Reduces human error and enhances efficiency.
- Flexibility: Suitable for dynamic systems with fluctuating conditions.
Applications of Control Valves
Control valves are widely used in industries that demand precision and automation, such as:
- Chemical Processing: Regulating chemical reactions by controlling flow and pressure.
- Oil and Gas: Managing flow rates in pipelines and refining processes.
- HVAC Systems: Controlling temperature and air pressure for efficient climate management.
- Power Plants: Ensuring precise control of steam flow and pressure.
Understanding Shut-Off Valves: The Muscle of Fluid Systems
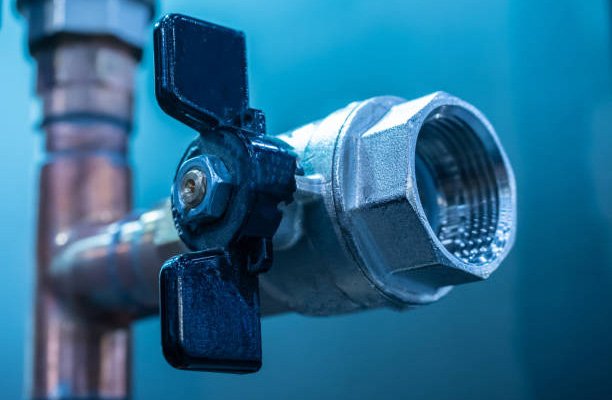
What Are Shut-Off Valves?
Unlike control valves, shut-off valves are simpler devices designed for one primary purpose: to start or stop the flow of fluid. They operate in a binary fashion—either fully open or fully closed—making them ideal for isolating parts of a system.
Key Features of Shut-Off Valves:
- On/Off Functionality: Shut-off valves don’t regulate flow; they simply start or stop it.
- Manual or Automatic: Can be manually operated or actuated for remote control.
- Robust Design: Built to withstand high pressure and harsh conditions.
- Applications: Common in emergency situations to quickly stop fluid flow, such as in pipelines or household plumbing systems.
Types of Shut-Off Valves:
- Gate Valves: Ideal for full-on or full-off flow with minimal pressure drop.
- Ball Valves: Known for their quick operation and tight seal.
- Plug Valves: Compact and reliable for simple on/off needs.
How Shut-Off Valves Work
Shut-off valves rely on straightforward mechanisms:
- Manual Operation: Many shut-off valves, like gate valves or ball valves, are manually operated by turning a handle or wheel.
- Actuated Operation: In automated systems, shut-off valves can use actuators for remote control, making them useful for hazardous or hard-to-reach areas.
When in the closed position, shut-off valves provide a tight seal to completely isolate the system, ensuring no fluid leaks or flow.
Key Components of Shut-Off Valves
- Valve Disc or Gate: Blocks or allows the passage of fluid.
- Sealing Mechanism: Ensures a leak-proof closure.
- Handle/Actuator: Used to operate the valve.
Advantages of Shut-Off Valves
- Simplicity: Easy to use and maintain.
- Reliability: Offers complete isolation of a system when needed.
- Cost-Effectiveness: More affordable than control valves for basic flow management tasks.
Applications of Shut-Off Valves
Shut-off valves are a staple in systems requiring straightforward operation, such as:
- Emergency Systems: Stopping fluid flow in the event of a leak or system failure.
- Maintenance Isolation: Safely isolating sections of a pipeline for repair or inspection.
- Household Plumbing: Shutting off water supply in kitchens, bathrooms, and outdoor fixtures.
- Fuel and Gas Pipelines: Isolating lines to prevent accidents.
Key Differences Between Control Valves and Shut-Off Valves
Let’s take a deeper dive into their distinctions:
Feature | Control Valves | Shut-Off Valves |
---|---|---|
Primary Function | Regulates flow, pressure, or temperature | Starts or stops the flow completely |
Control Mechanism | Variable positioning for fine adjustments | Binary operation: open or closed |
Complexity | High, requires integration with control systems | Low, simple and straightforward |
Automation | Highly automated, often with feedback controls | Can be manual or automated |
Applications | Precision systems (e.g., chemical plants) | Emergency isolation and basic flow systems |
Cost | Expensive due to advanced technology | Cost-effective for simple applications |
Durability | Can handle high-stress conditions but requires maintenance | Built for long-term reliability with minimal upkeep |
When to Use a Control Valve
Control valves are your go-to choice when you need:
- Precise adjustments: For processes where minor flow changes matter, like in chemical mixing.
- Automated systems: Ideal for large-scale operations that rely on PLCs or SCADA systems.
- Dynamic environments: If flow rates and pressure conditions fluctuate frequently, control valves excel.
When to Use a Shut-Off Valve
Shut-off valves are perfect for:
- Emergency isolation: Quick and complete stop of fluid flow during maintenance or safety hazards.
- Simple operations: Great for pipelines, household plumbing, and straightforward on/off needs.
- Cost-conscious applications: When budget constraints are tight, shut-off valves are a practical choice.
Can You Use Both in a Single System?
Yes! Many systems use both valve types for optimal performance:
- Control Valves: Ensure smooth and precise flow regulation during regular operations.
- Shut-Off Valves: Act as safety or isolation devices, cutting off flow during emergencies or maintenance.
For example, in a chemical processing plant, control valves regulate the chemical flow, while shut-off valves isolate the system during a leak or for maintenance purposes.
Factors to Consider When Choosing Between Control and Shut-Off Valves
When selecting the right valve for your system, keep these factors in mind:
- Purpose:
- If you need precision and automated control, go with a control valve.
- For safety isolation or straightforward on/off flow, choose a shut-off valve.
- System Requirements:
- Evaluate flow rates, pressure, and fluid type. Control valves handle fluctuating conditions better.
- Budget:
- Control valves are typically more expensive but offer greater flexibility. Shut-off valves are budget-friendly for simpler needs.
- Maintenance Needs:
- Shut-off valves are simpler to maintain, while control valves may require specialized servicing.
- Application Environment:
- In harsh or hazardous environments, shut-off valves with actuators may be preferred for safety.
Conclusion
Control valves and shut-off valves serve distinct roles, and understanding these differences is key to choosing the right one for your system. Whether you’re after precise control or reliable isolation, knowing their strengths and weaknesses can save you time, money, and headaches down the road.
When designing or maintaining a fluid control system, remember: control valves excel in precision and automation, while shut-off valves shine in simplicity and reliability. Why not use both for the best of both worlds?
FAQs
1. Are control valves more expensive than shut-off valves?
Yes, control valves are typically pricier due to their complexity and automation capabilities. Shut-off valves, being simpler, are more cost-effective.
2. Can a shut-off valve regulate flow like a control valve?
No. Shut-off valves are designed for binary operations (open/close) and lack the precision needed for flow regulation.
3. Which valve type is better for emergency situations?
Shut-off valves are the clear winner for emergencies due to their ability to completely stop flow quickly.
4. Are control valves suitable for high-pressure systems?
Yes, many control valves are designed to handle high-pressure environments, but always check specifications before installation.
5. Can shut-off valves replace control valves?
No, shut-off valves lack the precision and automation necessary for regulating flow and pressure. They’re designed solely for isolation.
6. Are control valves more prone to wear and tear?
Yes, because they operate continuously to modulate flow, control valves may require more frequent maintenance compared to shut-off valves.