Introduction to Pressure Drop in Hose Fittings
Pressure drop is a critical factor in fluid systems that refers to the reduction in pressure as a fluid flows through a hose and its associated fittings. This phenomenon can have a significant impact on system performance, efficiency, and operational costs. In practical terms, a higher-than-expected pressure drop can cause pumps and compressors to work harder, potentially leading to increased wear, energy consumption, and even system failure.
Understanding how and why pressure drop occurs in hose fittings is essential for engineers, maintenance professionals, and system designers. Whether in hydraulic applications, industrial processing, or residential plumbing, the management of pressure loss ensures consistent flow, reduced operational risks, and longer equipment lifespan.
The Science Behind Pressure Drop
To grasp how pressure drop affects a hose system, it helps to look at the physics behind it—specifically, Bernoulli’s Principle. This principle states that an increase in the speed of a fluid occurs simultaneously with a decrease in pressure. As fluid moves through a constriction (like a fitting), its velocity increases and its pressure drops. The narrower the path or the rougher the internal surface, the more resistance the fluid encounters, resulting in a higher pressure loss.
Moreover, pressure drop is influenced by several physical variables, including hose diameter, fluid velocity, fluid viscosity, and turbulence within the system. The formula commonly used to estimate pressure drop is derived from the Darcy-Weisbach equation or the Hazen-Williams equation, depending on the fluid type and flow regime.
Common Causes of Pressure Drop in Hose Fittings
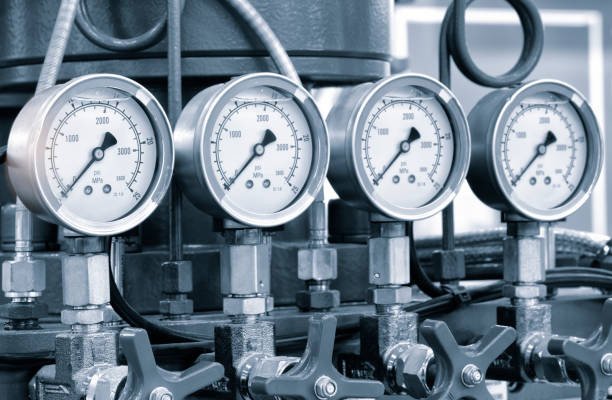
Several design and operational factors contribute to pressure drop in hose fittings. Understanding these helps in identifying and resolving inefficiencies in a fluid system:
- Hose Length and Diameter: Longer hoses increase frictional resistance, while smaller diameters intensify velocity, both of which lead to greater pressure drops.
- Type and Number of Fittings: Each fitting—especially elbows, tees, and reducers—adds resistance. The more transitions and connections, the higher the cumulative pressure drop.
- Flow Rate and Fluid Viscosity: High flow rates and viscous fluids create more resistance inside hoses and fittings, increasing the pressure loss exponentially in some cases.
Other culprits include obstructions in the hose (like buildup or debris), poor fitting alignment, and sudden directional changes that disrupt smooth flow. Minimizing these variables is crucial for efficient system design.
Types of Hose Fittings and Their Impact on Pressure Drop
Different hose fittings come with distinct internal geometries and connection methods, all of which influence the magnitude of pressure drop in a fluid system. Selecting the correct type of fitting for your application can significantly reduce unnecessary losses.
Barbed Fittings
Barbed fittings use a series of ridges (barbs) to grip the inner wall of the hose. While they’re easy to install and cost-effective, the internal obstruction from the barbs and the use of hose clamps can create moderate pressure losses, especially at higher flow rates.
Compression Fittings
Compression fittings seal by tightening a nut around a ferrule, which compresses against the hose or tube. They generally offer smoother internal flow paths than barbed fittings, leading to relatively lower pressure drops. However, if not properly aligned or tightened, they may still contribute to inefficiencies.
Quick-Connect Fittings
These fittings are designed for fast, tool-free hose connection and disconnection. However, they often contain internal check valves or mechanisms that reduce the effective internal diameter, which can cause higher pressure drops than other fitting types.
Swivel Fittings
Swivel fittings allow for rotational movement, preventing hose kinks and twists. Though beneficial for dynamic systems, their internal complexity and seals can cause mild to moderate pressure losses depending on the design.
Measuring Pressure Drop in Hose Assemblies
Accurate measurement of pressure drop is key to diagnosing system performance and making informed design adjustments. Professionals typically use manometers, differential pressure gauges, or electronic pressure sensors to assess pressure loss across a hose and fitting assembly.
Tools Used for Measurement
- Differential pressure gauges
- Manometers
- Digital pressure sensors with data logging
- Flow meters (to correlate flow and pressure)
Step-by-Step Procedure
- Install pressure gauges at both the inlet and outlet of the hose assembly.
- Ensure the system is sealed and fully operational before testing.
- Record pressure readings while fluid is flowing under typical operating conditions.
- Calculate the pressure drop by subtracting the outlet pressure from the inlet pressure.
It’s important to perform multiple readings at various flow rates to identify any non-linear behavior in pressure loss.
Pressure Drop Chart for Hose Fittings
Pressure drop charts offer pre-calculated data that helps engineers quickly estimate the loss expected for a specific hose diameter, length, and type of fitting. These charts are often available from manufacturers and are based on laboratory testing under controlled conditions.
Sample Charts for Different Sizes and Materials
For example, a 1/2\” rubber hose with a straight-through barbed fitting might show a pressure drop of 5 PSI at a flow rate of 10 GPM, whereas a 3/4\” hose under similar conditions could have only 2 PSI of pressure loss. Fitting material also plays a role: brass may offer smoother flow compared to plastic or stainless steel with coarser finishes.
Interpreting the Data
When using a pressure drop chart, always ensure that the test conditions (fluid type, temperature, flow rate) match or closely resemble your own system’s parameters. Deviations can lead to inaccurate estimations. For more precise applications, charts should be used as a starting point, followed by in-situ testing for confirmation.
How to Calculate Pressure Drop in Hose Fittings
Calculating pressure drop accurately is essential for designing efficient fluid systems and preventing energy losses. The calculations can be done using empirical data, manufacturer charts, or fluid dynamics formulas depending on the complexity and precision required.
Key Formulas and Equations
One widely used formula is the Darcy-Weisbach Equation:
ΔP = f * (L/D) * (ρ * v² / 2)
- ΔP = Pressure drop (Pa)
- f = Friction factor (dimensionless)
- L = Hose length (m)
- D = Hose diameter (m)
- ρ = Fluid density (kg/m³)
- v = Fluid velocity (m/s)
For water systems, the Hazen-Williams equation is often used as a simpler alternative for estimating pressure loss due to friction, especially in low-viscosity fluids.
Example Calculation
Suppose you have a 10-meter long hose with an inner diameter of 0.02 meters (20 mm), water flowing at 1.5 m/s, and a friction factor of 0.03:
ΔP = 0.03 * (10 / 0.02) * (1000 * 1.5² / 2) ΔP = 0.03 * 500 * (1125) ΔP = 16,875 Pascals ≈ 2.45 PSI
This indicates a pressure drop of approximately 2.45 PSI along the hose due to friction alone, excluding any fitting-induced losses.
Factors That Exacerbate Pressure Drop
Several secondary factors can significantly amplify pressure drop beyond basic calculations, and failing to account for these can lead to performance bottlenecks.
- Temperature Changes: Elevated temperatures can reduce fluid viscosity, leading to higher flow velocities and potential turbulence, increasing pressure losses.
- Abrupt Bends or Kinks: Any sharp turns, kinks, or tightly radiused bends disrupt laminar flow, causing turbulence and significant pressure reduction.
- Incompatible Fitting Materials: Using fittings made from incompatible or reactive materials can lead to corrosion or scale buildup, narrowing internal passages over time.
- Incorrect Installation: Misaligned hoses and poorly sealed fittings introduce micro-obstructions and leaks, both of which contribute to pressure inefficiency.
By identifying these secondary contributors early in the design or maintenance phase, you can proactively mitigate pressure drop and preserve flow consistency.
Minimizing Pressure Drop: Best Practices
To enhance system efficiency and extend component lifespan, minimizing pressure drop should be a priority in both design and operational stages. Below are some industry-proven best practices:
- Select the Right Hose Diameter: Oversizing slightly can reduce fluid velocity and friction, lowering pressure losses across the system.
- Limit the Number of Fittings: Each fitting adds resistance; minimizing transitions and directional changes can help maintain consistent flow.
- Use Smooth, High-Quality Fittings: Precision-machined fittings with smooth internal bores reduce turbulence and pressure loss.
- Install with Proper Bend Radius: Maintain recommended bend radii for the hose type to prevent internal collapse and flow restriction.
- Regularly Inspect for Wear and Buildup: Scheduled maintenance to remove debris or replace worn-out components helps sustain optimal pressure levels.
Implementing these measures will not only reduce pressure drop but also increase energy efficiency, reduce equipment strain, and enhance overall system reliability.
Pressure Drop vs. Flow Efficiency
While pressure drop and flow efficiency are closely related, they are not the same. Pressure drop refers to the loss in fluid pressure as it moves through a hose system, whereas flow efficiency describes how effectively the system delivers fluid to its intended destination.
How They Relate
A higher pressure drop usually signals increased resistance within the system, which in turn decreases the flow rate. This relationship can significantly impact applications where maintaining a specific flow velocity or pressure is crucial, such as in hydraulic systems or chemical processing lines. The more pressure lost overcoming friction and turbulence, the less energy is available to move the fluid efficiently through the system.
Importance of System Design Balance
Optimizing both parameters requires thoughtful design—selecting appropriate hose diameters, limiting fitting transitions, and using smooth-bore hoses. A balanced system minimizes pressure drop while maintaining desired flow rates, ensuring that pumps and compressors operate within optimal efficiency ranges.
Industrial Applications Affected by Hose Fitting Pressure Drop
Pressure drop in hose fittings is not just a theoretical concern—it directly impacts real-world applications across various industries. Understanding where and how it matters can help organizations make smarter engineering and purchasing decisions.
Hydraulic Systems
In hydraulic machinery, even a minor pressure drop can result in slower actuation, reduced lifting force, and overheating of components. Designers must ensure that hose assemblies maintain minimal pressure loss to preserve system performance and safety.
HVAC Systems
Heating, ventilation, and air conditioning (HVAC) setups rely on precise air and fluid flow. High pressure drops in flexible ducting or refrigerant lines can reduce thermal exchange efficiency, resulting in higher energy costs and reduced system life.
Chemical and Food Processing
These industries require sanitary, predictable, and efficient fluid transport. Pressure drops can disrupt flow rates in dosing and mixing operations, leading to inconsistent product quality or batch failures. Additionally, turbulent flows caused by poor fittings can trap residue, increasing contamination risks.
Troubleshooting Pressure Drop Issues
When systems exhibit performance issues, pressure drop should be one of the first factors investigated. Troubleshooting effectively requires both observation and data-driven diagnosis.
Signs of Excessive Pressure Drop
- Reduced flow rates or weak fluid output
- Overheating of pumps or compressors
- Increased energy consumption or system load
- Vibration or noise in fluid lines
Diagnostic Checklist
- Check for kinks, bends, or collapsed hose sections.
- Inspect fittings for signs of corrosion, blockages, or damage.
- Measure inlet and outlet pressure using calibrated gauges.
- Compare findings against manufacturer pressure drop charts.
- Verify that hose and fitting sizes match system specifications.
By following this checklist, technicians can isolate and correct the sources of pressure inefficiency, improving overall system function and lifespan.
Innovations in Hose Fitting Design
Technological advances are continuously improving hose fitting designs to reduce pressure drop and improve overall system performance. These innovations cater to industries demanding higher efficiency, reliability, and adaptability in fluid systems.
Low-Pressure-Drop Fittings
Modern manufacturers now offer fittings specifically engineered to minimize internal turbulence and flow resistance. These include smooth-bore designs, tapered transitions, and materials with lower surface roughness coefficients. Some feature streamlined internal geometries that prevent sharp flow disruptions, ideal for high-performance systems.
Smart Fittings with Sensors
The rise of Industry 4.0 has introduced smart hose fittings embedded with pressure and temperature sensors. These fittings allow real-time monitoring and predictive maintenance, enabling operators to detect anomalies in pressure drop before system failure occurs. This proactive approach significantly reduces downtime and repair costs.
Regulatory Standards and Compliance
Ensuring your hose fittings and assemblies meet industry standards is not only a best practice but also a requirement in many regulated sectors. Pressure drop performance is often an essential parameter in certification and operational compliance.
ISO and SAE Guidelines
Several international organizations have established benchmarks for hose performance, including pressure drop tolerances. The International Organization for Standardization (ISO) and the Society of Automotive Engineers (SAE) provide detailed standards such as:
- ISO 1436: Hydraulic hose and hose assemblies requirements
- SAE J517: Hydraulic hose standards for pressure, construction, and temperature ratings
Using certified components helps ensure your system adheres to these rigorous safety and performance benchmarks.
Importance of Meeting Safety Standards
Non-compliance can lead to fines, operational hazards, or equipment failures—especially in high-stakes industries like oil & gas, food processing, or aerospace. Regular inspections and documentation ensure that systems maintain conformity over time.
Conclusion
Pressure drop in hose fittings is an inevitable part of fluid dynamics, but with careful planning, it can be minimized to maintain system integrity and efficiency. By understanding the causes, measuring accurately, selecting appropriate fittings, and applying best practices, organizations can reduce operational costs, improve flow consistency, and extend equipment lifespan.
Stay informed about the latest fitting technologies and adhere to regulatory standards to future-proof your fluid systems. Routine assessments and data-driven maintenance will help ensure optimal performance, safety, and compliance in any industrial application.
FAQs
1. What is considered an acceptable pressure drop in hose fittings?
An acceptable pressure drop depends on the specific application, but generally, a drop of less than 10% of the system’s inlet pressure is considered manageable. In precision systems, even a 2–5% drop might warrant attention. Always refer to manufacturer guidelines for tolerance ranges specific to your system.
2. How can I tell if pressure drop is affecting my system’s performance?
Common indicators include slower fluid delivery, pump strain, increased system noise, overheating, and pressure alarms. Using differential pressure gauges at key system points can help quantify the drop and confirm if it’s impacting performance.
3. Do larger hose diameters always reduce pressure drop?
Generally, yes. Larger diameters reduce fluid velocity and internal friction, leading to lower pressure drops. However, oversizing can introduce other issues such as higher costs and installation constraints, so balance is key.
4. Are flexible hoses more prone to pressure drop than rigid piping?
Flexible hoses typically have higher pressure drops than rigid pipes due to their corrugated or less smooth interiors, bends, and more frequent fittings. However, flexibility may be necessary in dynamic systems, and using optimized fittings can mitigate losses.
5. Can temperature changes cause permanent damage related to pressure drop?
Yes. Extreme temperature variations can cause material fatigue, swelling, or contraction of hoses and fittings. These changes increase resistance and pressure drop, potentially leading to leaks or bursts. Selecting temperature-rated hoses and materials helps prevent such damage.