Hydraulic systems are a fundamental component in various industries, playing a crucial role in powering machinery and equipment. These systems utilize fluid power to perform a range of tasks, from lifting heavy loads to precision cutting. Understanding how hydraulic system work can provide valuable insights into their efficiency, versatility, and importance in modern industrial applications.
Components of a Hydraulic System
1. Hydraulic Fluid
Hydraulic fluid is the lifeblood of a hydraulic system, transferring energy throughout the system. There are various types of hydraulic fluids, including:
- Mineral Oils: Commonly used due to their cost-effectiveness and good lubrication properties.
- Water-Based Fluids: Used in applications requiring fire resistance.
- Synthetic Fluids: Offer better temperature stability and environmental friendliness.
The primary roles of hydraulic fluid include:
- Transmitting power
- Lubricating components
- Dissipating heat
Regular monitoring and maintenance of hydraulic fluid are crucial for optimal system performance.
2. Reservoir
The reservoir stores hydraulic fluid and performs several key functions:
- Cooling the fluid
- Separating air and contaminants
- Maintaining fluid levels
Typically made from materials like steel or aluminum, reservoirs are designed to ensure a steady supply of clean fluid, maintaining pressure stability and prolonging the life of hydraulic components.
3. Hydraulic Pump
Pumps convert mechanical energy into hydraulic energy by creating a flow of hydraulic fluid. Common types include:
- Gear Pumps: Simple, cost-effective, and suitable for many applications.
- Vane Pumps: Offer higher efficiency and quieter operation.
- Piston Pumps: Known for high pressure capabilities and used in demanding applications.
Selecting the right pump depends on specific system requirements, such as pressure, flow rate, and efficiency.
4. Hydraulic Valves
Valves control the flow and direction of hydraulic fluid within the system. They are crucial for ensuring the hydraulic system operates safely and efficiently. There are several types of valves used in hydraulic systems, each with specific functions and applications:
- Pressure Relief Valves: Protect the system from excessive pressure by diverting excess fluid back to the reservoir. They ensure the system operates within safe pressure limits, preventing damage to components.
- Directional Control Valves: Manage the path of the fluid, allowing it to flow to different actuators. These valves control the movement of actuators, determining the direction of fluid flow. Common types include spool valves, poppet valves, and rotary valves.
- Flow Control Valves: Regulate the fluid flow rate, ensuring the system operates smoothly and efficiently. These valves adjust the flow rate to control the speed of actuators. Examples include needle valves, orifice valves, and pressure-compensated flow control valves.
- Check Valves: Allow fluid to flow in one direction only, preventing backflow. They are essential for maintaining unidirectional flow and ensuring system integrity.
- Proportional Valves: Provide variable control of flow and pressure, allowing for precise adjustments. These valves are often used in applications requiring fine control and accurate positioning.
Proper valve selection and maintenance are essential for the reliability and performance of a hydraulic system. Regular inspections and timely replacement of worn or damaged valves are crucial to avoid system failures and ensure optimal performance.
5. Actuators
Actuators convert hydraulic energy into mechanical motion. They include:
- Hydraulic Cylinders: Provide linear motion.
- Hydraulic Motors: Offer rotational motion.
Actuators perform tasks such as lifting, pushing, pulling, and rotating components in machinery. The choice of actuator depends on the type of motion required and the load to be moved.
6. Filters
Filters maintain the cleanliness of hydraulic fluid, preventing contamination from damaging system components. Common types include:
- Return Line Filters
- Pressure Line Filters
- Suction Filters
Regular filter maintenance is crucial to avoid system failures and ensure optimal performance.
How Do Hydraulic Systems Operate?
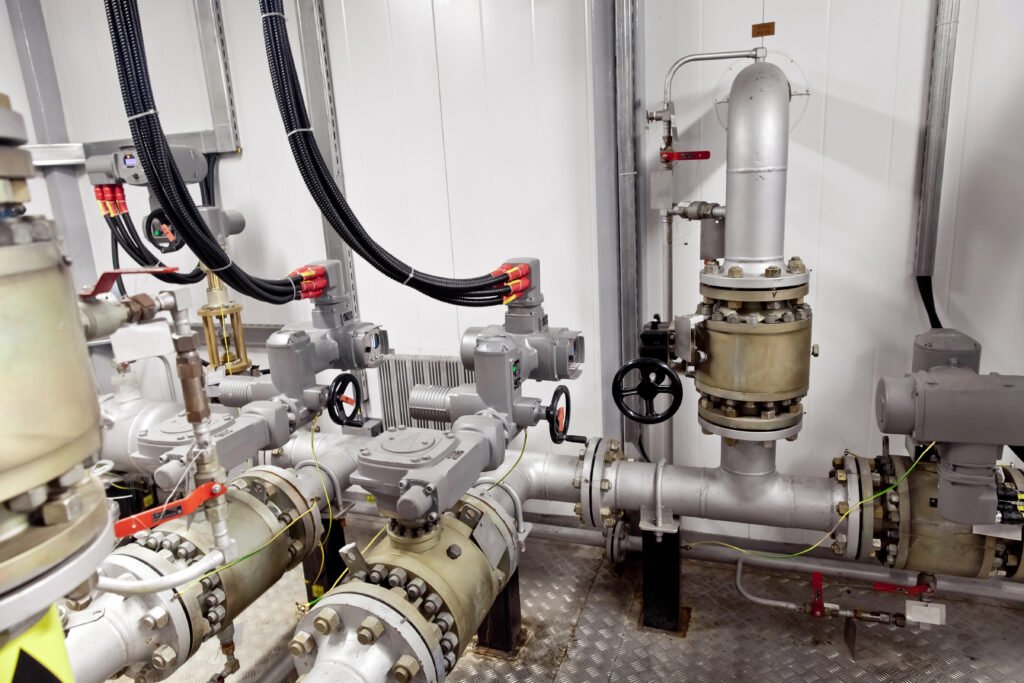
The operation of a hydraulic system can be summarized in a series of steps:
- Fluid Reservoir: The hydraulic fluid starts in the reservoir.
- Pump: The pump draws fluid from the reservoir, creating flow and pressure.
- Valves: The pressurized fluid is directed by control valves to the actuators.
- Actuators: Hydraulic cylinders or motors convert the fluid power into mechanical action.
- Return: The fluid returns to the reservoir, completing the cycle.
What Are the Types of Hydraulic Systems?
Open Loop Systems
Open loop systems circulate fluid from the reservoir to the pump and then to the actuator before returning to the reservoir. They are simpler and more cost-effective but may have lower efficiency due to fluid loss and contamination risks.
Closed Loop Systems:
Closed loop systems recirculate fluid directly between the pump and the actuator with minimal interaction with the reservoir. These systems offer higher efficiency and better control but are more complex and costly to maintain.
What Are the Common Applications of Hydraulic Systems?

Hydraulic systems are used in many industries and have numerous applications. The most common applications include:
1. Hydraulic Press
Hydraulic presses are used for forming and shaping materials by applying a controlled force. They are widely used in manufacturing such as metal forming, forging, and molding.
2. Hydraulic Work-holding System
These systems secure work-pieces in place during machining operations. Hydraulic work-holding systems provide consistent clamping force, improving machining accuracy and efficiency.
3. Hydraulic Excavator
Hydraulic excavators are essential in construction for digging, lifting, and moving materials. They use hydraulic cylinders and motors to control the movement of the boom, arm, and bucket.
4. Dishwashers
Hydraulic systems are used in industrial dishwashers to control water pressure and spray arms, ensuring effective cleaning of large quantities of dishes.
5. Gas Pumps
Gas pumps utilize hydraulic systems to control the flow of fuel, providing a reliable and efficient means of dispensing gasoline.
6. Airplanes
Hydraulic systems in airplanes control various functions, including landing gear, flaps, and brakes. They provide the necessary force and precision required for safe and reliable operation.
7. Office Chairs
Hydraulic systems in office chairs allow for smooth height adjustment, providing comfort and ergonomic support to users.
8. Industrial Applications
In manufacturing, hydraulic systems power machinery used in production lines, presses, and robotic arms. Their precision and reliability make them ideal for repetitive tasks in automated systems.
9. Mobile Applications
Hydraulic systems are integral to construction machinery such as excavators, loaders, and bulldozers. They provide the necessary power for lifting heavy loads, digging, and moving materials efficiently.
10. Specialized Applications
In aerospace, hydraulic systems control flight surfaces and landing gear. Marine applications include steering mechanisms and deck machinery. The versatility of hydraulic systems allows them to be adapted to various specialized tasks.
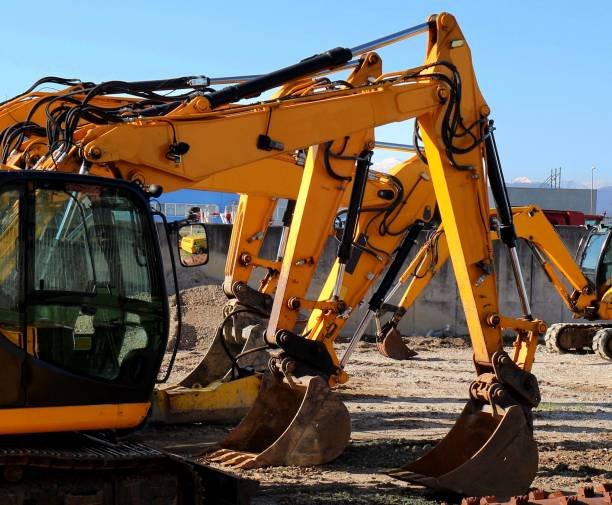
How to Maintain and Troubleshoot Hydraulic Systems?
1. Regular Maintenance Practices
Routine maintenance is crucial for the longevity of hydraulic systems. This includes checking fluid levels, inspecting hoses and connections, and replacing worn components. Regular maintenance helps prevent breakdowns and ensures optimal performance.
2. Troubleshooting Common Issues
Common issues include leaks, pressure drops, and contamination. Identifying and fixing these problems promptly is essential to maintaining system efficiency. Techniques such as visual inspections, pressure testing, and fluid analysis are used for troubleshooting.
Advantages of Hydraulic Systems
1. High Power Density
Hydraulic systems can generate significant force from relatively compact components, making them ideal for applications where space is limited but high power is required.
2. Precision and Control
Hydraulic systems offer precise control over speed, position, and force, which is essential for applications requiring high accuracy, such as in manufacturing and robotics.
3. Reliability and Durability
Hydraulic components are designed to withstand harsh environments and heavy use, ensuring long-lasting performance with minimal downtime.
4. Flexibility
Hydraulic systems can be easily adapted to various applications and modified to meet specific requirements, providing great versatility in industrial operations.
5. Smooth Operation
Hydraulic systems provide smooth and consistent power delivery, which is crucial for applications requiring steady and controlled movement.
Disadvantages of Hydraulic Systems
1. Maintenance Requirements
Hydraulic systems require regular maintenance to ensure proper operation. This includes monitoring fluid levels, checking for leaks, and replacing worn components. Neglecting maintenance can lead to system failures and costly repairs.
2. Environmental Concerns
Hydraulic fluid can pose environmental hazards if not properly managed. Spills and leaks can contaminate soil and water sources, requiring careful handling and disposal of used fluids.
3. Efficiency Losses
Hydraulic systems can experience efficiency losses due to fluid leakage, friction, and heat generation. Proper system design and maintenance can help mitigate these losses.
4. Potential for Leaks
Hydraulic systems are prone to leaks, which can lead to reduced performance and environmental contamination. Regular inspections and timely repairs are essential to minimize leakage.
What Are the Safety Considerations in Hydraulics?
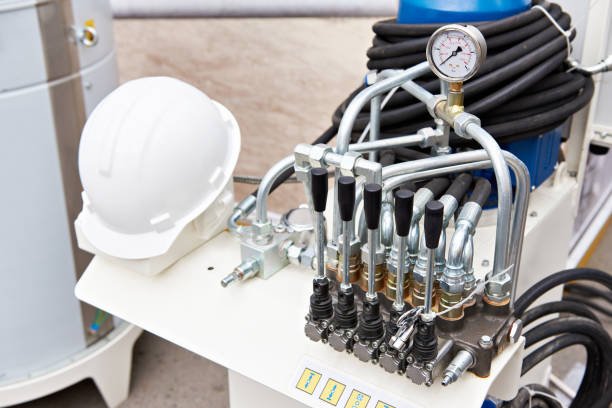
Safety is a critical aspect of hydraulic system operation. To ensure safe and efficient operation, consider the following:
- Pressure Management: Always monitor and regulate system pressure to prevent over-pressurization, which can lead to component failure and accidents.
- Proper Training: Ensure that all operators and maintenance personnel are properly trained in the safe operation and maintenance of hydraulic systems.
- Regular Inspections: Conduct regular inspections to identify and address wear, leaks, and other potential issues before they result in system failure.
- Use of Protective Equipment: Operators should use appropriate personal protective equipment (PPE) to protect against hydraulic fluid exposure and high-pressure injuries.
- System Cleanliness: Maintain system cleanliness to prevent contamination, which can lead to malfunctions and safety hazards.
- Emergency Procedures: Establish and practice emergency shutdown procedures to quickly and safely respond to hydraulic system failures or accidents.
Future Trends in Hydraulic Systems
1. Technological Advancements
The integration of smart hydraulics and IoT technology allows for real-time monitoring and predictive maintenance. This leads to improved efficiency and reduced downtime.
2. Industry Innovations
Advancements in materials and design have led to more compact, lightweight, and corrosion-resistant hydraulic components. These innovations enhance performance and expand the range of applications.
Conclusion
Hydraulic systems are indispensable in modern industry, offering unparalleled power and control in various applications. Understanding their components, working principles, and maintenance requirements helps in appreciating their role and maximizing their efficiency.
Explore our range of hydraulic solutions on our website. For more information, contact our experts and discover how we can help optimize your hydraulic systems.