Hydraulic valves play a pivotal role in any hydraulic system, ensuring smooth operation by controlling the flow, pressure, and direction of hydraulic fluid. These valves can be found in a wide range of machinery and equipment, from heavy construction machines to agricultural tools and industrial applications. However, without regular maintenance, even the best hydraulic valves can fail prematurely, leading to costly repairs and system downtimes.
Maintaining hydraulic valves is critical to keeping your equipment operating at peak efficiency. Whether you are overseeing machinery in a manufacturing plant or managing a fleet of construction vehicles, knowing how to properly maintain your hydraulic valves can extend the life of your equipment and save you time and money.
In this comprehensive guide, we will cover everything you need to know about hydraulic valve maintenance, from basic inspections to more advanced troubleshooting methods. By following these best practices, you can ensure your hydraulic valves perform optimally for years to come.
Why Hydraulic Valve Maintenance is Important
Hydraulic valves are the control points in a hydraulic system that determine how fluid flows within the system. These valves are responsible for ensuring that the right amount of fluid is directed to the correct component at the right time, helping control pressure, flow rate, and direction. Without a properly functioning valve, the system won’t perform as expected. Here’s why it’s so important to keep your hydraulic valves well-maintained:
- Maximizing Efficiency: Hydraulic systems rely on precise fluid control to function efficiently. A valve that’s not functioning properly can result in poor performance, like sluggish movements, erratic speeds, or inconsistent pressure, affecting overall system efficiency.
- Preventing Excessive Wear and Tear: If a valve fails to regulate the pressure correctly, it can cause excessive wear on other parts of the system, such as pumps, motors, or cylinders. This accelerated wear leads to an increased risk of breakdowns and expensive repairs.
- Improving Safety: A malfunctioning hydraulic valve could lead to over-pressurization, resulting in system failures or even catastrophic accidents. Regular valve maintenance ensures the pressure levels stay within safe limits, helping to avoid accidents and unsafe working conditions.
- Cost-Effective Long-Term Solution: Regular maintenance is far cheaper than replacing a hydraulic valve or an entire hydraulic system. By keeping your valves in optimal condition, you minimize the risk of untimely breakdowns and reduce repair costs.
Step-by-Step Guide to Maintaining Hydraulic Valves
Proper hydraulic valve maintenance consists of several key tasks, each of which helps improve the valve’s longevity and functionality. Let’s break down these steps in detail:
1. Regularly Inspect Hydraulic Valves
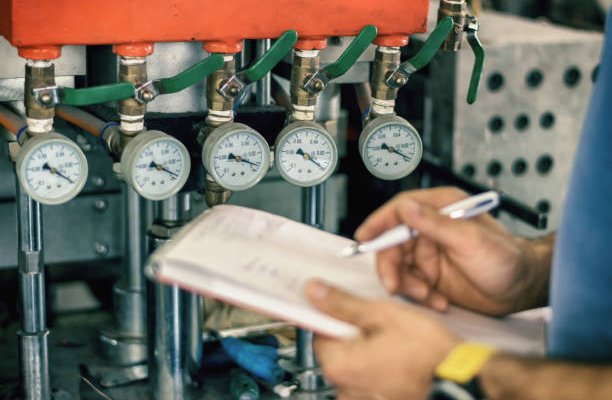
Routine inspections form the foundation of effective valve maintenance. By keeping a close eye on your hydraulic valves, you can catch problems early before they develop into major issues. Here’s a deeper dive into what to inspect:
- Visual Inspection for Leaks: One of the first things to check for is any visible hydraulic fluid leakage around the valve body, seals, or connections. Leaks, even if small, can cause fluid loss, leading to system inefficiency and potentially damaging other system components. When inspecting, use a flashlight to examine areas that may be difficult to see. If you notice any significant leaks, replace the seals or gaskets promptly.
- Examine Valve Condition: Hydraulic valves are subject to harsh conditions, including high pressure, temperature variations, and exposure to fluid contaminants. Regularly inspect for physical damage such as cracks, dents, or corrosion on the valve body. Such damage may compromise the valve’s operation and could lead to system failure. Pay attention to the mounting bolts or fasteners as well to ensure they’re not loose.
- Check the Seals and O-rings: Seals and O-rings play a crucial role in preventing leaks and maintaining proper pressure control. Inspect them carefully for wear, cracks, or deformation. Over time, seals can dry out or become brittle due to heat exposure, causing leaks. Replacing these parts regularly can prevent issues before they cause major problems.
2. Keep the System Clean
Contaminants like dirt, dust, water, and metal particles are a major enemy of hydraulic systems. These contaminants can find their way into hydraulic valves, causing clogging, wear, and reduced performance. Here’s how to prevent contamination:
- Ensure Clean Hydraulic Fluid: Always use clean, high-quality hydraulic fluid that meets the specifications of your hydraulic system. Dirty or old fluid is the primary cause of valve clogging and other issues. If your system uses a filter, make sure it’s working properly and replace it according to the manufacturer’s recommendations. Also, perform regular fluid analysis to detect any contaminants that could be affecting the performance of the valves.
- Seal Off Valve Ports: When valves are being serviced or when not in use, keep the ports sealed to prevent contaminants from entering. Dust, debris, and moisture can enter through open ports, especially in harsh environments. If your system has a port cover or cap, use it whenever possible.
- Install High-Quality Filters: Hydraulic filters capture particles and contaminants before they can damage the system. Installing high-quality filters at key points in the system will prevent contaminants from reaching the valves. Be sure to clean or replace filters regularly to keep them effective.
3. Check Fluid Levels and Quality
Hydraulic fluid is the lifeblood of the entire hydraulic system, including the valves. Fluid that is too low, contaminated, or degraded can cause poor valve performance and even damage the system. Here’s what to focus on:
- Monitor Fluid Levels: Check the hydraulic fluid levels regularly. Low fluid levels can lead to air entering the system, causing erratic valve movement or complete failure. If the fluid is low, top it off with the correct fluid type, ensuring you don’t overfill. Keep in mind that fluid levels can drop over time, so a regular check is essential.
- Test Fluid Quality: Over time, hydraulic fluid can degrade and become contaminated. Perform periodic fluid tests to detect the presence of contaminants like water, particles, and metal shavings. Contaminated fluid can cause valves to wear prematurely, resulting in system failure. If the fluid is dirty or contaminated, it’s time to replace it.
- Change Fluid According to Manufacturer’s Guidelines: The life of hydraulic fluid depends on the type of system and the conditions under which it operates. Some systems may need fluid changes more frequently, especially in high-demand environments. Always follow the manufacturer’s recommendations for fluid change intervals.
4. Lubricate Moving Parts
Many hydraulic valves have moving parts that require lubrication to reduce friction and wear. Adequate lubrication ensures smooth operation and helps prevent issues like sticking or sluggish valve action. Here’s how to properly lubricate the components:
- Use the Right Lubricant: Always use the manufacturer’s recommended lubricant for your hydraulic valves. The wrong lubricant can cause the valve to malfunction or degrade the seals. Make sure the lubricant is compatible with your hydraulic fluid.
- Grease Valve Fittings: Many hydraulic valves have grease fittings that should be lubricated regularly to prevent corrosion and ensure smooth operation. Follow the manufacturer’s schedule for lubrication and avoid over-greasing, as excessive grease can attract dust and dirt.
- Lubricate Moving Parts During Valve Disassembly: When performing valve maintenance or disassembly, take the opportunity to lubricate all moving parts, including valve spools, springs, and seals. Lubrication during reassembly will prevent unnecessary friction and wear during operation.
5. Monitor System Pressure and Flow Rates
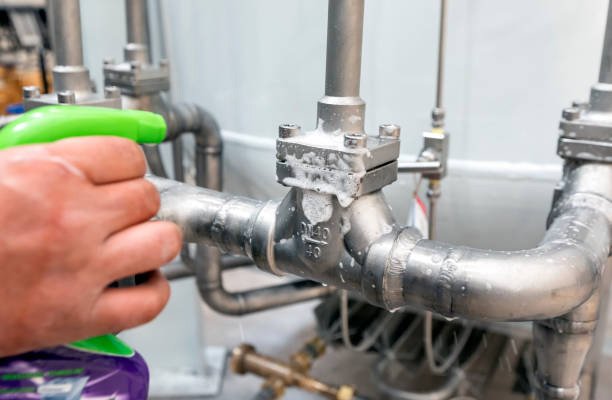
Hydraulic valves are designed to operate within specific pressure and flow parameters. Consistently monitoring system pressure and flow rates is essential to ensure that the valves perform optimally.
- Monitor Pressure Relief Valves: Pressure relief valves prevent the system from becoming over-pressurized, which could damage the valve or other parts of the system. Ensure that pressure relief valves are functioning properly and are set to the correct pressure levels. Test them regularly and replace any faulty valves.
- Ensure Proper Flow Rates: Hydraulic valves depend on specific flow rates for proper operation. If the flow rate is too high, the valve could experience cavitation, leading to internal damage. If the flow rate is too low, the valve may not function as intended. Measure the flow rate regularly and adjust it as necessary.
Conclusion
Maintaining hydraulic valves is an ongoing process that requires attention to detail and routine checks. With regular inspections, fluid quality control, lubrication, and pressure monitoring, you can ensure that your valves operate efficiently, avoid unnecessary repairs, and extend the lifespan of your entire hydraulic system. Proper maintenance not only keeps your equipment running smoothly but also saves you time and money in the long run.
By following these steps and taking the time to address small issues early, you’ll maximize the performance and reliability of your hydraulic valves, allowing your systems to continue operating at their best. If you’re unsure about any of the maintenance procedures, always consult the manufacturer’s guidelines or seek advice from a hydraulic specialist.
FAQs
1. How often should I inspect my hydraulic valves?
Inspect valves every 3–6 months, or more often in high-demand systems or harsh conditions.
2. What signs indicate my hydraulic valve needs maintenance?
Look for leaks, unusual noises, slow or erratic movement, or inconsistent pressure—all signs the valve may need attention.
3. How can I tell if my hydraulic fluid is contaminated?
Perform fluid analysis or check for cloudiness, discoloration, or visible debris in the fluid.
4. Can I repair a hydraulic valve myself?
Minor issues, like seal leaks, can often be fixed yourself, but complex issues should be handled by a professional.
5. What type of lubricant should I use for hydraulic valves?
Always use the manufacturer-recommended lubricant to prevent damage and ensure smooth operation.
6. How can I prevent contamination in my hydraulic system?
Use clean fluid, replace filters regularly, seal connections when not in use, and maintain a clean environment.