Hydraulic hose fitting diagnostics are essential for ensuring the safe and efficient operation of fluid power systems. These fittings connect hoses to machinery, maintaining the necessary pressure and flow conditions crucial for system performance. Regular diagnostics can prevent costly downtime, extend system life, and optimize performance. In this article, we’ll explore the importance of hydraulic hose fitting diagnostics, common types of fittings, causes of failures, and best practices for maintenance.
Common Types of Hydraulic Hose Fittings
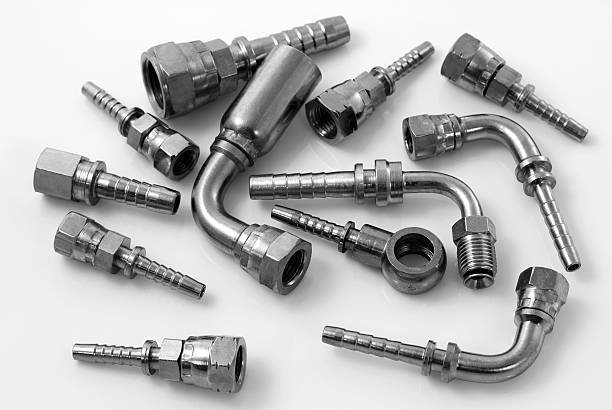
Hydraulic hose fittings come in various types, each designed for specific applications and operational requirements. Understanding these fittings is key to selecting the right components for your hydraulic system. Here are some of the most common types:
- JIC (Joint Industry Council) Fittings: These fittings are widely used in high-pressure applications and are designed to provide reliable connections. JIC fittings feature a 37-degree flare that allows for a tight seal, making them ideal for dynamic applications where vibration is a concern.
- ORFS (O-Ring Face Seal) Fittings: Known for providing leak-free connections, ORFS fittings utilize an O-ring to create a seal. This design helps prevent leaks in hydraulic circuits and is particularly useful in applications where high pressures and temperatures are common.
- Pipe Thread Fittings: Used in a variety of applications, pipe thread fittings offer a simple and effective sealing solution. These fittings can be found in many hydraulic systems, providing a reliable connection between hoses and components.
- NPT (National Pipe Thread) Fittings: Similar to pipe thread fittings, NPT fittings are tapered, which helps create a tighter seal as they are tightened. These fittings are widely used in hydraulic systems where leak prevention is critical.
- Flare Fittings: These fittings are designed for high-pressure applications and feature a conical shape that allows for a secure connection. Flare fittings are often used in fuel and hydraulic lines due to their resistance to leaks.
Understanding the various types of hydraulic hose fittings helps in making informed decisions for your hydraulic system, ultimately enhancing performance and safety.
Understanding Hydraulic Hose Failures
Common Causes of Hose Failures
Hydraulic hose failures can be caused by various factors; however, many of these are preventable with proper maintenance and diagnostics. Moreover, understanding these causes allows operators and technicians to take proactive steps to minimize downtime and ensure system reliability. Consequently, here are some of the most common causes:
Each hydraulic hose has a maximum rated pressure, which, if exceeded, can cause the hose to burst or degrade prematurely. Regular pressure testing is essential to ensure that hoses are rated correctly for their application. Understanding the pressure requirements of your system and selecting hoses accordingly is crucial.
Excessive Pressure:
Environmental Factors:
Hoses are often exposed to harsh environmental conditions, including extreme temperatures, UV light, chemicals, and moisture. Prolonged exposure to these elements can cause materials to break down, leading to cracks, swelling, and leaks. Selecting hoses designed to resist specific environmental conditions can significantly extend their service life. Regular monitoring of environmental exposure is recommended to prevent degradation.
Incorrect Hose Length and Routing:
Improper routing or using hoses that are too short can lead to excessive bending, twisting, or stretching, which places strain on the hose and fittings. This can result in early failure due to cracking or detachment from the fitting. Ensuring proper installation and using the correct hose lengths is vital in avoiding these issues. Consideration of the layout and potential movement of equipment can guide proper hose selection.
Improper Fitting Assembly:
Faulty fitting connections due to under-torqued or over-torqued fittings, mismatched fittings, or failure to follow assembly guidelines can create leaks, fitting slippage, and hose bursts. Ensuring that fittings are installed according to manufacturer specifications minimizes the risk of these issues. Training personnel on proper assembly techniques is also recommended to enhance reliability.
Abrasion and Mechanical Damage:
Contact with sharp objects, excessive friction, or repeated impacts with surrounding components can wear down the hose’s outer layer. Over time, abrasions can lead to leaks and compromise hose integrity. Installing protective sleeves and following recommended routing practices can mitigate abrasion-related damage. Regular inspections can help identify early signs of wear.
Fluid Compatibility Issues:
Some hydraulic fluids can be incompatible with certain hose materials; consequently, this can lead to internal deterioration. Additionally, using the wrong fluid can cause the inner tube of the hose to degrade, resulting in swelling, softening, and, ultimately, failure. Therefore, always check the compatibility of hose materials with the hydraulic fluid in use to prevent unexpected issues.
Old or Expired Hoses:
Hydraulic hoses have a finite lifespan, and over time, materials naturally degrade even when not in use. Utilizing old or expired hoses can result in unexpected failures due to age-related weakening. Following manufacturer recommendations for hose replacement intervals is essential in preventing these issues. Maintaining a record of hose installation dates can aid in timely replacements.
Excessive Bending or Kinking:
If a hose is bent or kinked beyond its minimum bend radius, it can cause internal stress and weaken the structure, leading to early wear. Correct routing that minimizes sharp bends and using strain relievers can prevent bending-related damage. Educating personnel on proper hose handling can further prevent kinks.
Contamination and Blockage:
Dirt, debris, or metal particles inside the hose can lead to abrasion, clogging, and decreased flow. These contaminants can erode the inner tube, leading to leaks and reduced efficiency. Regular cleaning and using filtration systems help keep hoses free from contaminants, promoting optimal performance.
Signs of Wear and Tear in Hose Fittings
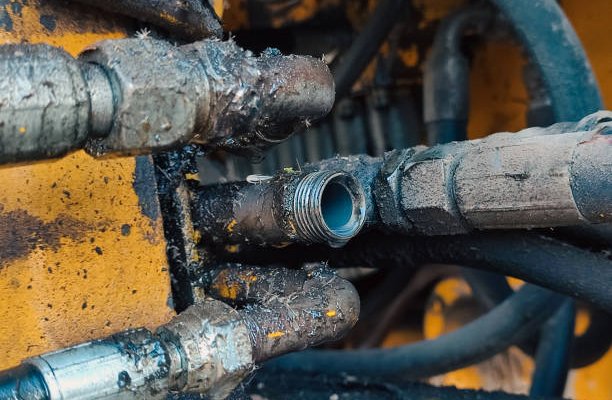
Identifying wear and tear early can prevent catastrophic failures. Key signs to watch for include:
- Visual Damage: Cracks, abrasions, or swelling on the hose or fittings are primary indicators of potential issues. Regular visual inspections should be part of your maintenance routine.
- Leaking Fluids: Any signs of hydraulic fluid escaping indicate a potential failure. Even small leaks can lead to larger issues over time, making early detection crucial.
- Unusual Noise: Hissing or whining sounds may suggest internal issues within the system. This could indicate air trapped in the system or other problems that need immediate attention.
- Reduced Performance: A noticeable drop in system performance or responsiveness may signal underlying issues with hose fittings or connections. Regular monitoring of system performance can help catch these issues early.
Hydraulic Hose Fitting Diagnostics Tools and Techniques
Visual Inspection Techniques
Visual inspections are one of the most accessible yet vital diagnostic techniques for identifying potential issues in hydraulic hoses and fittings. Conducting regular visual inspections helps detect early signs of wear and damage, preventing more serious failures and costly downtime. Below is a step-by-step guide to performing an effective visual inspection on hydraulic hose fittings:
Prepare the Inspection Area:
Ensure that the area around the hydraulic system is well-lit to allow for a clear view of the hose and fittings. If necessary, use a flashlight to see hard-to-reach areas, and make sure the system is safely shut off to avoid unexpected movements during inspection.
Inspect the Hose Surface for Physical Damage:
Examine the entire length of the hose for visible signs of damage, including cracks, cuts, abrasions, and bulges. Check both the outer cover and any accessible internal layers. Damage to the outer layer can indicate exposure to excessive friction or external hazards, which may compromise integrity.
Check for Leaks Around Fittings:
Inspect the fittings and connection points for any signs of leaking fluid. Leaks often appear as wet spots, discoloration, or pooling fluid near the connection. Even small leaks can indicate a failing seal, loose fitting, or material degradation.
Examine for Signs of Wear on Fittings and Connections:
Look for signs of corrosion, rust, or unusual wear on the fittings. Corrosion weakens the fitting material, making it more prone to breakage under pressure. Ensure that the fittings are secure, and use a wrench to check for any looseness in the connections.
Inspect Bend Radii and Hose Routing:
Check that the hose is routed correctly and that there are no kinks, twists, or bends sharper than the recommended bend radius. Bends that exceed the minimum bend radius can cause undue stress, potentially leading to cracks or leaks. Hoses should be routed with enough slack to avoid over-stretching.
Look for Signs of Abrasion or Chafing:
Check if the hose has been rubbing against nearby components or surfaces. Abrasion can thin the hose wall, especially if it comes into regular contact with sharp edges or rough surfaces. Installing protective sleeves can help prevent this type of damage in the future.
Inspect for Bulges or Soft Spots:
Run your hand along the hose to feel for any bulges or soft spots. These signs indicate internal damage, possibly due to excessive pressure or chemical breakdown, and can lead to imminent failure if not addressed. Soft spots often indicate weakened areas likely to burst under pressure.
Check Labels and Hose Condition for Age:
Identify the manufacture date or any wear indicators on the hose to determine if it has exceeded its service life. Many hoses have expiration dates that help indicate when the material is likely to degrade. Replacing hoses periodically helps prevent age-related failures.
Document Findings and Take Photos if Necessary:
Document any issues you find, including detailed descriptions and photos of visible damage. Keeping a record of inspections allows for monitoring any progressive damage over time and aids in future maintenance planning.
By following these visual inspection steps, operators and technicians can identify and address issues early, extending the lifespan of hydraulic hoses and improving system reliability. Scheduling regular visual inspections, even on a monthly or weekly basis, can help prevent minor wear from developing into major failures.
Using Pressure Testing Equipment
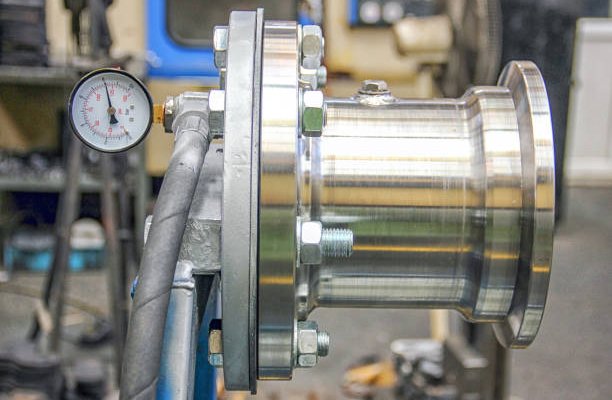
Pressure testing is a critical diagnostic tool for determining whether a hydraulic hose can withstand operational pressures. This method helps identify potential weaknesses that could lead to hose failure during normal operation. Pressure testing should be performed periodically, especially in high-demand systems. Here’s a basic overview of how to conduct pressure testing safely:
Gather the Necessary Equipment:
Obtain a pressure testing kit suitable for your hydraulic system. Ensure the testing equipment is rated for the maximum pressure the hose is designed to handle.
Prepare the System:
Safely shut down the hydraulic system and relieve any existing pressure. Isolate the section of the hydraulic circuit you will test, and ensure that all personnel are informed to avoid accidents.
Connect the Pressure Testing Equipment:
Attach the pressure gauge and testing equipment to the hose fitting according to the manufacturer’s instructions. Ensure all connections are secure and leak-free.
Increase Pressure Gradually:
Slowly increase the pressure to the specified test level, monitoring for any signs of leaks or failures in the hose and fittings. Allow the system to stabilize at the test pressure for a predetermined period, typically 15 to 30 minutes.
Monitor for Leaks or Deformation:
During the test, watch for any leaks, bulging, or deformation of the hose. Take note of any irregularities and document them for further analysis.
Release the Pressure Safely:
After the testing period, carefully release the pressure in the system according to safety protocols. Ensure all personnel are clear of the testing area during this process.
Evaluate Results:
Analyze the test results to determine if the hose meets operational standards. If any issues were noted, further inspection or replacement of the hose may be necessary.
Pressure testing is a vital part of a comprehensive maintenance program for hydraulic hoses, as it helps identify potential issues before they lead to failures.
Ultrasonic Testing for Early Detection
Ultrasonic testing is an advanced diagnostic technique that uses sound waves to detect internal flaws in hydraulic hoses and fittings that may not be visible through visual inspections. This non-destructive testing method is highly effective for identifying early signs of wear, cracks, or degradation within hoses. Here’s how ultrasonic testing works and its benefits:
- Understanding Ultrasonic Testing: Ultrasonic testing employs high-frequency sound waves, which are transmitted through the material. When sound waves encounter a defect, they are reflected back, allowing the technician to analyze the data for signs of damage.
- Equipment Used: The ultrasonic testing equipment typically includes a handheld ultrasonic transducer that emits sound waves and receives the echoes. The device is connected to a display that interprets the data and shows any anomalies detected within the hose.
- Conducting the Test: To perform ultrasonic testing, the technician places the transducer against the surface of the hose and activates the device. The system scans the material for internal flaws, providing real-time data that highlights any issues.
- Analyzing Results: The data gathered during the ultrasonic test is analyzed to determine the integrity of the hose. Any irregularities or variations in the sound wave patterns can indicate potential problems such as internal tears, material degradation, or weak spots.
- Benefits of Ultrasonic Testing: One of the main advantages of ultrasonic testing is its non-destructive nature, meaning that it does not compromise the integrity of the hose during the inspection process. Additionally, ultrasonic testing can detect flaws that are not visible through visual inspections, allowing for earlier intervention and reducing the risk of catastrophic failures.
Incorporating ultrasonic testing into your maintenance program enhances the reliability of hydraulic systems by identifying issues before they lead to significant problems.
Troubleshooting Hydraulic Hose Fittings
Step-by-Step Diagnostic Procedures
When a hydraulic system is underperforming, following a structured diagnostic procedure can help identify the root cause. Here’s a step-by-step guide to troubleshooting hydraulic hose fittings:
- Identify Symptoms: Start by assessing the system for visible issues and performance drops. Document symptoms such as unusual noises, leaks, or fluctuations in pressure.
- Perform Visual Inspections: Conduct thorough visual inspections of the hoses, fittings, and connections to identify any signs of wear, damage, or leaks.
- Utilize Testing Methods: If visual inspections do not reveal the problem, employ pressure testing and ultrasonic testing to further investigate. These methods can identify internal issues that may not be immediately apparent.
- Review System Specifications: Cross-reference the system’s operational parameters with the specifications of the hoses and fittings in use. Ensure that all components are rated for the necessary pressure and environmental conditions.
- Consult Manufacturer Guidelines: Refer to the manufacturer’s documentation for troubleshooting guidance specific to the components in your hydraulic system. This can provide valuable insights into common issues and their resolutions.
- Make Repairs or Replacements: Based on the findings from the inspections and testing, determine whether repairs can be made or if components need replacement. Document all actions taken for future reference.
Common Issues
Common problems encountered in hydraulic hose fittings include:
- Leakage: Often a result of worn seals, loose fittings, or improper assembly, leaks can lead to reduced system efficiency and increased risk of accidents.
- Hose Burst: Can occur from overpressure, excessive heat, or external damage. Understanding the operational limits and maintaining a robust maintenance schedule can help prevent these failures.
- Loose Fittings: Fittings may become loose over time due to vibrations or improper torque during installation. Regular inspections and tightening can help mitigate this issue.
Maintenance Best Practices
Regular Inspection Schedules
Implementing a regular inspection schedule is crucial for maintaining the integrity of hydraulic hoses and fittings. Depending on the usage and environmental conditions, inspections should be scheduled monthly or even weekly for high-demand systems. Consider the following points when developing an inspection schedule:
- Define Inspection Intervals: Establish clear intervals based on system usage, age of components, and environmental factors. High-use systems may require more frequent checks.
- Incorporate Inspection Checklists: Develop checklists for inspectors to follow during visual inspections. This ensures consistency and thoroughness in the inspection process.
- Track Inspection Records: Maintain detailed records of inspections, findings, and actions taken. This data can inform future maintenance decisions and identify trends in wear or damage.
Cleaning and Storage Guidelines
Proper cleaning and storage of hydraulic hoses and fittings can significantly extend their life. Here are some best practices:
- Regular Cleaning: Clean hoses regularly to remove contaminants, dirt, and debris. Use compatible cleaning solutions and avoid harsh chemicals that may degrade hose materials.
- Storage Conditions: Store hoses in a cool, dry place, coiled to prevent kinks and protect them from exposure to sunlight and harsh environmental conditions. Ensure that hoses are not stored under heavy objects or in locations where they could be damaged.
- Use Protective Sleeves: Consider using protective sleeves for hoses that are likely to encounter abrasion or damage. These sleeves provide an additional layer of protection against mechanical wear.
Upgrading Your Hydraulic Hose Fitting System
Choosing the Right Fittings
Selecting the right hydraulic hose fittings is critical for system performance and reliability. Here are some tips for choosing the right components:
- Assess Pressure Ratings: Ensure that the fittings are rated for the maximum pressure of the hydraulic system. Using components rated for lower pressures can lead to failures.
- Consider Temperature Compatibility: Take into account the operating temperatures of your system and select fittings that can withstand those conditions.
- Check Fluid Compatibility: Ensure that the materials used in the fittings are compatible with the hydraulic fluids in use. Incompatible materials can lead to premature wear and failures.
- Evaluate Installation Requirements: Consider the installation and assembly requirements of the fittings. Some fittings may require specialized tools or techniques for proper installation.
Conclusion
Regular diagnostics of hydraulic hose fittings are essential for maintaining performance and safety in fluid power systems. By implementing a structured diagnostic approach that includes visual inspections, pressure testing, and ultrasonic diagnostics, operators can identify issues early and extend the lifespan of their hydraulic systems. Incorporating best practices for maintenance and staying informed about advancements in technology will help ensure the continued efficiency and reliability of hydraulic hose fittings.
FAQs
What are the signs of a failing hydraulic hose fitting? Signs include visible cracks, leaks, unusual noises, and reduced performance. Regular inspections can catch these signs early.
How often should hydraulic hose fittings be inspected? Monthly inspections are recommended, or weekly in high-use systems.
What tools are essential for hydraulic hose fitting diagnostics? Key tools include visual inspection aids, pressure testing kits, and ultrasonic testing equipment.
Can hydraulic hose fittings be repaired? Minor issues can often be repaired, but significant damage usually requires replacement.
What materials are used in hydraulic hose fittings? Common materials include steel, brass, and stainless steel for durability and corrosion resistance.