Introduction to Hydraulic Pressure Testing
Hydraulic pressure testing is a critical process used to verify the strength, durability, and leak-resistance of hydraulic systems and components. This method involves the controlled application of pressurized fluids—typically water or oil—into a system to evaluate its ability to withstand operational stress without failing. It is a standard procedure across industries such as aerospace, automotive, oil and gas, and manufacturing.
The importance of hydraulic pressure testing cannot be overstated. It not only helps in identifying flaws and weak points in hydraulic circuits but also prevents catastrophic failures that can result in property damage, downtime, or even personal injury. By ensuring that systems meet or exceed their pressure ratings, this process supports operational reliability, safety compliance, and cost-effectiveness.
Hydraulic Testing Methods
Engineers began practicing pressure testing during the early industrial revolution, developing rudimentary techniques to verify the integrity of steam boilers and pressure vessels. They initially used manual pumping and observational methods, which lacked precision and reliability.
Over the decades, hydraulic testing evolved with technological advancements. The mid-20th century saw the introduction of calibrated pressure gauges, relief valves, and more sophisticated testing rigs. These improvements allowed engineers to apply and measure pressures with much greater accuracy and repeatability. In modern times, digital pressure sensors, automated test benches, and computer-assisted diagnostics have transformed hydraulic testing into a highly accurate and data-driven discipline.
This evolution has not only enhanced testing accuracy but also made it possible to test complex systems under real-world simulated conditions, improving predictive maintenance and design validation processes.
How Hydraulic Pressure Testing Works
At its core, hydraulic pressure testing works by filling a system or component with an incompressible fluid—usually water or hydraulic oil—and applying pressure above its normal operating level. The objective is to check for structural integrity, leakage points, and pressure tolerance without causing permanent deformation or damage.
The basic mechanics involve connecting a high-pressure pump to the system, gradually increasing the pressure while monitoring it with precision gauges or digital sensors. During this process, all joints, welds, seals, and materials are scrutinized for any sign of leakage or failure. Depending on the goal of the test, the pressure may be held for a specific duration to confirm system stability.
Fluid dynamics play a vital role in this process. Because fluids are nearly incompressible, they can effectively transmit force through the system, making it easier to detect even minute weaknesses. Moreover, this incompressibility minimizes the risk of explosion or sudden failure, enhancing safety during testing.
Types of Hydraulic Pressure Tests
There are several types of hydraulic pressure tests, each tailored to specific objectives and system requirements. Understanding the differences between them is essential for choosing the appropriate method:
Proof Pressure Testing
This test subjects the component or system to a pressure higher than its normal operating level but below the threshold that could cause permanent damage. The goal is to confirm that the item can operate safely under maximum expected conditions.
Burst Pressure Testing
Burst testing involves pressurizing the system until it fails or ruptures. This test determines the maximum pressure a component can endure before catastrophic failure. It’s commonly used during product development or for validating design specifications.
Leak Testing
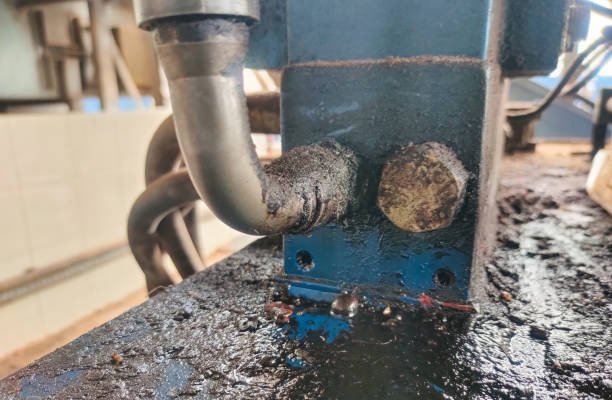
This method focuses on detecting and quantifying fluid leakage under pressure. It is crucial for systems that require tight seals, such as hydraulic cylinders, valves, and pipelines. Visual inspection, pressure decay, and sensor-based monitoring are often used in leak testing.
Cyclic Testing
Also known as fatigue testing, cyclic pressure tests involve repeatedly applying and releasing pressure to simulate long-term operational conditions. It helps in identifying potential weaknesses that may not be visible during single-application tests.
Key Equipment Used in Hydraulic Testing
To conduct hydraulic pressure testing safely and effectively, several specialized tools and instruments are employed:
High-Pressure Pumps
These pumps are used to generate the required pressure levels in the system. They can be manual, electric, or air-driven depending on the pressure range and application requirements.
Pressure Gauges and Sensors
Accurate measurement is vital in pressure testing. Analog gauges are still used for simplicity, but digital pressure transducers provide high precision and allow for real-time data logging.
Test Benches
Hydraulic test benches are complete systems designed for testing multiple components in a controlled environment. They often include integrated pumps, safety features, and computerized control systems.
Hoses, Valves, and Fittings
These components must be rated for high pressures and chemically compatible with the testing fluid. Quick-connect fittings are often used for efficiency and safety during test setup and teardown.
Step-by-Step Hydraulic Pressure Testing Procedure
Performing hydraulic pressure testing involves a systematic approach to ensure safety and accuracy. Below is a typical procedure:
1. System Inspection and Preparation
Before beginning the test, inspect the system for visible damage or loose components. Make sure all fittings are secure, and verify that the system is clean and free from debris.
2. Filling and Bleeding the System
Fill the system with the chosen test fluid, usually water or hydraulic oil. Bleed any trapped air from the system to avoid inaccurate readings and potential safety hazards.
3. Applying Pressure
Using a calibrated pump, gradually increase the pressure to the designated test level. Monitor the rise using pressure gauges or digital instruments, ensuring it follows the specified rate.
4. Holding and Monitoring
Maintain the test pressure for a predetermined period. Observe the system for signs of leakage, deformation, or pressure drop. Document all observations meticulously.
5. Depressurizing and Inspection
Once the test duration is complete, slowly depressurize the system to avoid hydraulic shock. Conduct a final inspection to verify structural integrity and ensure no residual damage has occurred.
Safety Protocols and Precautions
Hydraulic pressure testing involves high pressures that can pose serious safety risks if not properly managed. Strict adherence to safety protocols is essential to protect personnel, equipment, and the environment.
Personal Protective Equipment (PPE)
Operators must wear appropriate PPE, including safety goggles, gloves, steel-toed boots, and protective clothing. In high-pressure applications, face shields and body armor may also be recommended to guard against unexpected fluid ejections or component failure.
Emergency Shut-Off Systems
Modern testing setups often include emergency shut-off valves or buttons that immediately relieve system pressure. These features are crucial for stopping the test quickly in case of irregular behavior or danger signs.
System Isolation and Signage
Isolate the test area with barriers or signage to prevent unauthorized personnel from entering. Ensure all valves are properly locked and tagged, and that the system is completely vented before maintenance or adjustments.
Standards and Certifications in Hydraulic Testing
Various international and industry-specific standards govern hydraulic pressure testing to ensure consistency, reliability, and safety. Certification and operational approval often require compliance with these standards.
ISO Standards
ISO 4413 outlines the general rules for designing and constructing hydraulic systems, while ISO 10100 focuses on safety guidelines for testing hydraulic cylinders. These standards help ensure test procedures are universally accepted and reduce liability.
ASME and ASTM Standards
The American Society of Mechanical Engineers (ASME) and American Society for Testing and Materials (ASTM) offer detailed codes and specifications for testing materials and components under pressure. For example, ASME Boiler and Pressure Vessel Code (BPVC) is widely used in high-stakes industries like power generation and petrochemicals.
Certification Bodies
Third-party certification ensures that the testing process complies with required standards. Common certifying organizations include TÜV, DNV-GL, and SGS, which provide auditing and documentation services to validate test results.
Common Challenges and Troubleshooting
Despite best practices, issues can arise during hydraulic pressure testing. Knowing how to identify and resolve these problems is key to maintaining test integrity and minimizing delays.
Pressure Drop Issues
If the system cannot maintain the target pressure, it may indicate a leak, seal failure, or incorrect gauge reading. Double-check all connections and re-test after tightening or replacing components.
Equipment Malfunctions
Pumps or gauges may malfunction due to wear or improper use. Always calibrate instruments before testing and have backup tools ready to avoid downtime.
Micro-Leaks Detection
Some leaks are so small they do not show up immediately. Use ultrasonic leak detectors or dye-based fluids for more sensitive testing. Repeated or extended pressure holds can also reveal slow leaks.
Industries That Rely on Hydraulic Pressure Testing
Hydraulic pressure testing is a cornerstone of quality assurance across a variety of high-stakes industries. Each sector has its own unique requirements and operational standards, but all depend on reliable pressure testing to maintain system safety and performance.
Aerospace and Defense
In aerospace, even the smallest failure can have catastrophic consequences. Hydraulic systems in aircraft landing gear, flight controls, and missile launch mechanisms undergo rigorous testing to meet strict aviation safety standards such as those from the FAA and EASA.
Oil & Gas Industry
Hydraulic testing ensures the reliability of pipelines, blowout preventers (BOPs), drilling equipment, and offshore rigs. Testing under extreme pressures replicates real-world operating conditions to prevent leaks and explosions in high-risk environments.
Automotive and Manufacturing
Manufacturers must pressure test hydraulic systems used in machinery, braking systems, and robotic arms to ensure smooth and safe operations. Technicians routinely test automotive components such as fuel injectors and hydraulic clutches for durability and leak resistance.
Marine and Shipbuilding
Ships use extensive hydraulic systems for steering, cargo handling, and stabilization. Pressure testing helps verify the performance of hydraulic circuits exposed to varying water pressures and corrosive environments.
Environmental Considerations
Hydraulic pressure testing can have an environmental impact if not carefully managed. As sustainability becomes a greater priority in engineering practices, organizations are adopting greener testing methods.
Water vs. Oil Testing
While oil-based fluids offer superior lubrication and pressure characteristics, they pose a greater environmental risk in case of leaks. Water-based testing fluids are often used where contamination risks must be minimized, such as in food processing or environmentally sensitive areas.
Spill Management
Spill containment systems such as trays, drip pans, and absorbent mats should be employed to catch any leaks during testing. Proper disposal of contaminated fluids is essential to comply with environmental regulations and protect natural ecosystems.
Eco-Friendly Test Fluids
Biodegradable and non-toxic hydraulic fluids are increasingly used for testing, especially in industries with strict environmental compliance requirements. These fluids reduce risk in the event of accidental releases and make cleanup easier and safer.
Innovations and Future Trends
The field of hydraulic pressure testing is undergoing significant technological transformation, driven by the need for higher precision, automation, and predictive maintenance.
Digital Monitoring and Automation
Advanced test benches now feature digital control panels and sensors that collect real-time data on pressure, temperature, and flow. Automation minimizes human error and allows for repeatable, consistent testing conditions.
Remote Testing Systems
IoT-enabled testing setups allow engineers to control and monitor tests remotely, improving safety and efficiency, especially in hazardous or hard-to-reach locations. Cloud integration enables centralized data storage and analysis across multiple facilities.
AI-Driven Leak Detection
Machine learning algorithms are being trained to identify micro-leaks and unusual system behavior by analyzing pressure trends and sensor data. This not only enhances leak detection accuracy but also enables predictive maintenance by flagging components at risk of failure before they break down.
Cost and Time Efficiency in Pressure Testing
Implementing an efficient hydraulic pressure testing strategy can yield substantial cost savings and minimize downtime. However, achieving this balance requires careful planning, investment in quality equipment, and streamlined operational processes.
Budgeting for Equipment and Operations
Initial costs may include purchasing or renting pressure test pumps, gauges, benches, and safety gear. Factoring in labor, fluid disposal, and maintenance is also essential. While high-quality equipment can be more expensive upfront, it often proves more economical in the long run by reducing repeat tests and errors.
Time-Saving Strategies
Standardized procedures, pre-calibrated instruments, and quick-connect fittings can drastically reduce setup and test time. Integrating digital workflows with automated data capture also cuts down on manual entry and human error, accelerating the overall process.
Return on Investment (ROI)
A reliable pressure testing regimen helps prevent catastrophic system failures, saving costs related to repairs, insurance claims, and lost productivity. ROI is also realized through improved safety records, regulatory compliance, and enhanced customer trust.
Selecting the Right Testing Provider
Outsourcing hydraulic pressure testing to certified professionals can enhance reliability and ensure compliance with industry standards. Choosing the right provider requires a careful evaluation of capabilities, experience, and credentials.
Key Criteria to Evaluate
Look for providers with a proven track record in your specific industry. Verify that they use calibrated and certified equipment, follow recognized testing standards, and offer complete documentation of results.
Questions to Ask Vendors
- What standards and certifications do you comply with?
- Can you handle our system’s pressure range and specifications?
- Do you offer on-site and off-site testing services?
- How is test data recorded, stored, and shared?
Comparing Services and Pricing
Don’t base your decision solely on cost. Compare the comprehensiveness of their services, turnaround time, safety procedures, and customer support. A slightly higher upfront fee may be justified by better accuracy, faster results, and added services like consultation and failure analysis.
Conclusion
Hydraulic pressure testing is far more than a routine inspection—it’s a foundational practice that safeguards performance, prevents failures, and ensures compliance across industries. From aerospace to marine, its value is demonstrated through enhanced operational integrity, worker safety, and long-term cost savings.
As technologies advance and environmental standards tighten, hydraulic pressure testing continues to evolve. By adopting modern tools, staying compliant with global standards, and working with experienced providers, organizations can ensure that their hydraulic systems operate safely and efficiently under any condition.
FAQs
1. What is the purpose of hydraulic pressure testing?
Hydraulic pressure testing is used to ensure that components or systems can safely withstand operational pressures without leaking or failing. It validates the strength and integrity of parts such as valves, cylinders, and pipelines in industries like aerospace, oil & gas, and manufacturing.
2. How do you perform a hydraulic pressure test?
The process involves filling the system with a test fluid, gradually applying pressure using a pump, monitoring for leaks or deformations, and then documenting the results. Safety protocols and industry standards must be followed strictly during the procedure.
3. What is the difference between proof and burst pressure tests?
Proof pressure testing applies pressure slightly above the operating limit to confirm the component can handle expected stress, while burst pressure testing continues until failure to determine the maximum pressure capacity. Proof testing is non-destructive; burst testing is destructive.
4. What fluids are commonly used in hydraulic pressure testing?
Water and mineral-based hydraulic oils are most commonly used. In environmentally sensitive settings, biodegradable fluids or water-based solutions are preferred to minimize ecological impact in the event of a spill.
5. How often should hydraulic pressure testing be performed?
Testing frequency depends on the industry, equipment usage, and regulatory requirements. Critical systems may require testing annually or semi-annually, while others follow a schedule aligned with maintenance cycles or manufacturer recommendations.