Butterfly valves are essential components in industrial fluid control systems, offering efficient flow regulation, tight shut-off capabilities, and compact design. They are widely used in industries such as oil & gas, water treatment, chemical processing, and food & beverage. Selecting the right butterfly valve for your industrial application is crucial to ensure operational efficiency, safety, and cost-effectiveness. The wrong choice can lead to leakage, pressure loss, increased maintenance costs, and even system failures.
This guide will help you navigate the key factors involved in choosing the right butterfly valve, including types, materials, actuation methods, pressure ratings, and industry standards. By the end of this article, you’ll have a clear understanding of what to consider for optimal valve performance in your specific application.
Understanding Butterfly Valves and Their Applications
What is a Butterfly Valve?
A butterfly valve is a quarter-turn rotational valve used to regulate the flow of liquids, gases, or slurries in a pipeline. It consists of a circular disc mounted on a rotating shaft, which, when turned, either allows or restricts the flow of the medium.
Key Components and Working Mechanism
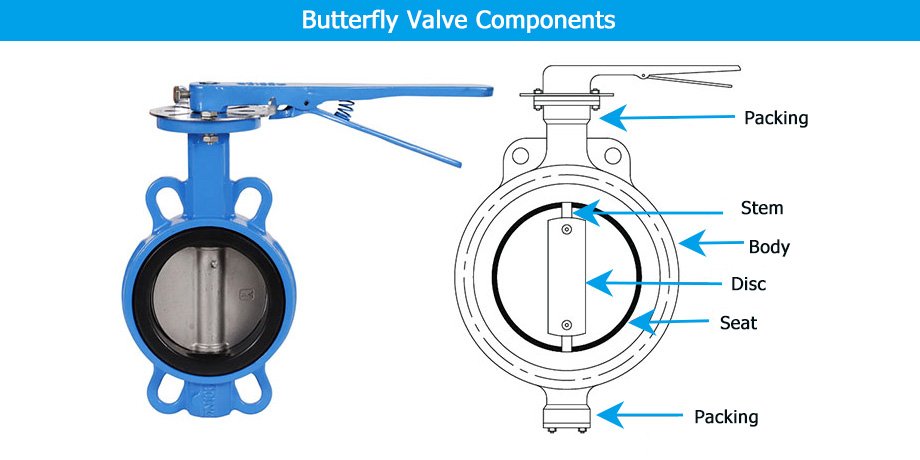
- Valve Body: Houses the internal components and connects to the pipeline.
- Disc: The rotating element that controls flow.
- Stem: Connects the actuator or handle to the disc.
- Seat: Ensures a tight seal when the valve is closed.
- Actuator or Handle: Provides the mechanism to open or close the valve.
Common Industrial Applications
Butterfly valves are widely used in various industries due to their lightweight design, quick operation, and cost-effectiveness. Some key applications include:
- Oil & Gas: Flow regulation in pipelines and refineries.
- Water Treatment: Used in filtration, wastewater treatment, and distribution systems.
- Chemical Processing: Handles aggressive fluids and corrosive substances.
- Food & Beverage: Controls flow in hygienic applications with FDA-approved materials.
- HVAC Systems: Regulates airflow in heating and cooling systems.
Understanding these fundamental aspects of butterfly valves will help in choosing the right one for your specific industrial needs.
Types of Butterfly Valves and Their Differences
Butterfly valves come in different designs to suit various industrial applications. The main types include concentric, double-offset, and triple-offset butterfly valves, each with distinct features and benefits.
Concentric Butterfly Valves
Also known as resilient-seated butterfly valves, these valves have a disc that is centered within the valve body and a flexible rubber seat.
- Features: Simple design, lightweight, and cost-effective.
- Benefits: Suitable for low-pressure applications and non-corrosive media.
- Best Applications: Water distribution, HVAC systems, and low-pressure industrial processes.
Double-Offset Butterfly Valves
These valves have a slightly offset disc and stem design, reducing seat wear and providing better sealing capabilities.
- Features: Improved sealing with reduced friction.
- Benefits: Longer lifespan and better performance under moderate pressure conditions.
- Best Applications: Water treatment plants, power generation, and chemical processing.
Triple-Offset Butterfly Valves
Designed for high-performance applications, these valves feature an angled seat and a metal-to-metal sealing system, eliminating leakage.
- Features: Zero-leakage performance with high durability.
- Benefits: Withstands high pressure and temperature conditions.
- Best Applications: Oil & gas, steam applications, and critical industrial processes.
Understanding the differences between these butterfly valve types is crucial in selecting the most suitable option for your specific application.
Choosing the Right Valve Based on Media and Temperature
One of the most important factors in selecting a butterfly valve is understanding the type of media it will handle and the operating temperature conditions. Different valves are designed to perform optimally under specific conditions, so choosing the right one ensures efficiency, longevity, and safety.
Handling Liquids vs. Gases
- Liquids: For water, oils, or chemical solutions, ensure the valve material is resistant to corrosion and compatible with the fluid’s properties.
- Gases: When dealing with air, steam, or industrial gases, consider pressure ratings and sealing capabilities to prevent leaks.
Temperature and Pressure Considerations
- Low-Temperature Applications: Rubber-seated butterfly valves are suitable for applications below 80°C (176°F).
- High-Temperature Applications: Metal-seated or triple-offset butterfly valves are ideal for temperatures exceeding 200°C (392°F).
- Pressure Ratings: Choose a valve rated for the system’s operating pressure to prevent failure under extreme conditions.
Corrosive and Abrasive Media Compatibility
- Corrosive Fluids: Use stainless steel or lined butterfly valves (PTFE, EPDM) for chemicals that may degrade metal surfaces.
- Abrasive Media: Select a valve with reinforced materials, such as hardened metal discs, to withstand particle erosion.
By carefully evaluating these factors, you can ensure that your butterfly valve operates efficiently while minimizing wear and potential failure in your system.
Selecting the Right Valve Material
Choosing the correct material for your butterfly valve is essential to ensure durability, efficiency, and compatibility with the media it will handle. The materials used for the valve body, disc, and seat must be suitable for the application’s temperature, pressure, and chemical composition.
Common Body Materials
- Cast Iron: Cost-effective and widely used for water applications but not ideal for highly corrosive environments.
- Carbon Steel: Strong and durable, suitable for high-pressure and temperature applications.
- Stainless Steel: Resistant to corrosion and chemical damage, making it ideal for food processing, pharmaceuticals, and aggressive fluids.
- PVC (Polyvinyl Chloride): Lightweight and corrosion-resistant, used in low-pressure applications and chemical handling.
Disc and Seat Materials
- Stainless Steel Discs: Provides excellent corrosion resistance for chemical and food processing industries.
- Bronze Discs: Suitable for marine applications due to high resistance to seawater.
- PTFE (Teflon) Seats: Ideal for handling corrosive chemicals due to its non-reactive properties.
- EPDM (Ethylene Propylene Diene Monomer) Seats: Commonly used for water and non-oil-based applications due to its flexibility and durability.
- Viton Seats: Best suited for high-temperature and chemical applications, including fuel and oil handling.
By selecting the right material for the valve body, disc, and seat, you can ensure a longer lifespan and optimal performance while reducing the risk of failure or damage.
Understanding Valve Actuation Options
Actuation is a key factor in butterfly valve selection, as it determines how the valve opens and closes. Depending on your application, you can choose from manual, electric, pneumatic, or hydraulic actuation.
Manual Actuation
Manual butterfly valves are operated using a hand lever or a gear mechanism, making them ideal for low-pressure and infrequent operation applications.
- Hand Lever: Best suited for small-diameter valves where quick operation is needed.
- Gear Operator: Provides increased torque and is recommended for larger valves that require more force to operate.
- Best Applications: Water distribution, HVAC systems, and low-pressure fluid control.
Electric Actuation
Electric actuators use motors to open and close the valve, providing automation and remote operation capabilities.
- Features: Precise control, low maintenance, and ideal for integration with automated systems.
- Benefits: Reduces the need for manual intervention, improves efficiency, and allows remote operation.
- Best Applications: Industrial automation, chemical processing, and energy systems.
Pneumatic and Hydraulic Actuation
Pneumatic and hydraulic actuators use air or fluid pressure to operate the valve, making them ideal for high-speed and high-force applications.
- Pneumatic Actuation: Uses compressed air for fast and reliable operation. Suitable for explosion-proof environments.
- Hydraulic Actuation: Uses pressurized liquid to generate high torque, making it ideal for large-diameter valves.
- Best Applications: Oil & gas, power plants, and industries requiring fast or heavy-duty valve operation.
Choosing the right actuation method depends on your system requirements, including automation needs, operating frequency, and environmental factors.
Pressure Ratings and Flow Control Considerations
Understanding pressure ratings and flow control is crucial when selecting a butterfly valve for your industrial application. Choosing the wrong valve can lead to performance issues, system failures, or even safety hazards.
How to Read Pressure Ratings
Pressure ratings indicate the maximum pressure a valve can handle without failure. These ratings are usually measured in PSI (pounds per square inch) or bar.
- PN (Pressure Nominal): A common rating system used internationally to indicate pressure resistance.
- Class Ratings: ANSI Class 150, 300, and 600 define the pressure-handling capability of the valve.
- Working Pressure (WP): The maximum continuous pressure the valve can handle in operation.
- Test Pressure: The pressure the valve can withstand during safety testing, typically higher than the WP.
Valve Sizing for Optimal Flow Control
Proper valve sizing ensures efficient flow control and minimizes pressure loss in the system. Key considerations include:
- Valve Diameter: Must match the pipeline size for optimal performance.
- Flow Coefficient (Cv): A measure of how much fluid flows through the valve at a given pressure.
- Pressure Drop: A significant pressure drop indicates improper sizing, which can reduce system efficiency.
Ensuring Compliance with Industry Standards
Different industries have specific regulations governing pressure and flow control. Ensuring compliance is essential for safety and operational efficiency.
- API (American Petroleum Institute): Standards for oil & gas applications.
- ANSI (American National Standards Institute): Defines pressure classes and dimensions.
- ISO (International Organization for Standardization): Sets global industrial valve standards.
By selecting a butterfly valve with the appropriate pressure rating and flow control capabilities, you can ensure efficiency, safety, and regulatory compliance in your application.
End Connection Types and Installation Factors
Butterfly valves come with different end connection types, each designed for specific installation and operational needs. Choosing the right connection type ensures proper sealing, ease of installation, and long-term reliability.
Types of End Connections
1. Wafer Connection
The wafer-style butterfly valve is designed to fit between two flanges with bolts passing through the valve body.
- Features: Lightweight and compact design.
- Benefits: Cost-effective and easy to install.
- Best Applications: Low-pressure systems, HVAC, and water distribution.
2. Lug Connection
Lug-style butterfly valves have threaded inserts that allow them to be bolted directly to the pipeline flanges.
- Features: Provides independent pipeline isolation.
- Benefits: Suitable for end-of-line service, allowing one side to be disconnected without affecting the other.
- Best Applications: Industrial water systems, chemical processing, and food industries.
3. Flanged Connection
Flanged butterfly valves have built-in flanges that bolt directly to the pipeline flanges, ensuring a strong and secure connection.
- Features: High durability and leak-proof performance.
- Benefits: Best suited for high-pressure applications.
- Best Applications: Oil & gas, power plants, and high-pressure industrial pipelines.
Installation Considerations
- Pipeline Compatibility: Ensure the valve size and connection type match the existing pipeline system.
- Space Constraints: Wafer-style valves are ideal for tight spaces, while flanged valves require more room.
- Accessibility for Maintenance: Consider ease of access for future repairs or replacements.
By selecting the correct end connection type and considering installation factors, you can improve system efficiency, reduce maintenance downtime, and enhance operational safety.
Maintenance and Lifespan Considerations
Proper maintenance is crucial to extending the lifespan of a butterfly valve and ensuring its reliable operation. Routine inspections, cleaning, and timely replacements of worn components can prevent costly failures and system downtime.
Routine Maintenance Tips
- Regular Inspection: Check for leaks, corrosion, or signs of wear on the disc, seat, and seals.
- Lubrication: Keep moving parts properly lubricated to ensure smooth operation, especially for manual and gear-operated valves.
- Cleaning: Remove any debris or buildup that may obstruct the valve’s movement or cause sealing issues.
- Actuator Maintenance: For automated valves, periodically test the actuator to ensure proper functionality.
Expected Lifespan Based on Materials and Application
The lifespan of a butterfly valve depends on the material, operating conditions, and maintenance schedule:
- Rubber-Seated Valves: Typically last 5–10 years in moderate conditions but may degrade faster in chemical or high-temperature environments.
- Metal-Seated Valves: Designed for high-temperature and abrasive applications, with a lifespan of 15+ years.
- Stainless Steel and PTFE-Lined Valves: Provide extended durability in corrosive applications, lasting 10–20 years with proper care.
Common Issues and Troubleshooting
- Leakage Around the Seat: May indicate wear or improper sealing; replace the seat or adjust alignment.
- Hard-to-Turn Handle: Could be due to buildup inside the valve or insufficient lubrication.
- Actuator Failure: Check power supply, air pressure (for pneumatic actuators), and mechanical connections.
Implementing a proactive maintenance strategy will maximize the efficiency and service life of your butterfly valve, reducing the need for unexpected replacements.
Industry Standards and Certifications
Ensuring that your butterfly valve meets industry standards and certifications is essential for safety, efficiency, and regulatory compliance. These standards define performance requirements, material specifications, and pressure ratings to ensure reliable operation in various industrial applications.
Key Industry Standards
- API (American Petroleum Institute): API 609 specifies design, testing, and pressure ratings for industrial butterfly valves used in oil, gas, and petrochemical industries.
- ANSI (American National Standards Institute): Defines valve pressure classes (e.g., Class 150, 300) and flange dimensions for compatibility in industrial systems.
- ISO (International Organization for Standardization): Establishes global standards for manufacturing, quality control, and safety compliance.
- AWWA (American Water Works Association): AWWA C504 and C516 outline design and performance criteria for butterfly valves in water distribution systems.
- EN (European Norm): EN 593 governs butterfly valves used in European industrial and water treatment applications.
Certifications to Look For
- CE (Conformité Européenne): Required for valves sold in Europe, indicating compliance with European safety and environmental regulations.
- UL (Underwriters Laboratories): Certification for fire-safe butterfly valves used in HVAC and fire protection systems.
- NSF (National Sanitation Foundation): NSF 61 certifies butterfly valves for drinking water applications, ensuring they are free from harmful contaminants.
- FM (Factory Mutual): Certification for valves used in fire protection and safety systems.
- ATEX (Atmosphères Explosibles): Required for valves operating in explosive or hazardous environments.
By selecting butterfly valves that meet relevant industry standards and certifications, you ensure compliance with safety regulations, improve system reliability, and enhance overall performance.
Cost vs. Performance Trade-Offs
When selecting a butterfly valve for an industrial application, it’s important to balance cost and performance. While budget-friendly options may seem attractive, investing in a high-performance valve can lead to long-term savings by reducing maintenance costs and improving efficiency.
Budget-Friendly vs. High-Performance Valves
- Standard Rubber-Seated Butterfly Valves: Lower initial cost, suitable for low-pressure and non-corrosive applications.
- Metal-Seated Butterfly Valves: Higher cost but designed for extreme temperatures, pressure, and aggressive fluids.
- Triple-Offset Butterfly Valves: The most expensive option but offers zero-leakage performance and long-term durability.
Long-Term Cost-Effectiveness Considerations
- Maintenance Costs: Higher-quality materials and coatings reduce the need for frequent repairs and replacements.
- Energy Efficiency: A well-sealed butterfly valve minimizes energy losses due to leakage or pressure drops.
- Downtime Reduction: Reliable valves minimize unplanned shutdowns, which can be costly in industrial processes.
- Total Cost of Ownership (TCO): Consider not just the purchase price, but also installation, maintenance, and operational costs.
When to Invest in a Premium Valve
- High-Pressure or High-Temperature Applications: Requires durable, high-quality materials.
- Critical Process Control: Industries like oil & gas, pharmaceuticals, and chemical processing benefit from premium performance.
- Corrosive or Abrasive Media Handling: Requires specialized materials like stainless steel or PTFE lining for longevity.
By carefully evaluating the cost versus performance trade-offs, you can make an informed decision that balances affordability with long-term operational efficiency.
Common Mistakes to Avoid When Selecting a Butterfly Valve
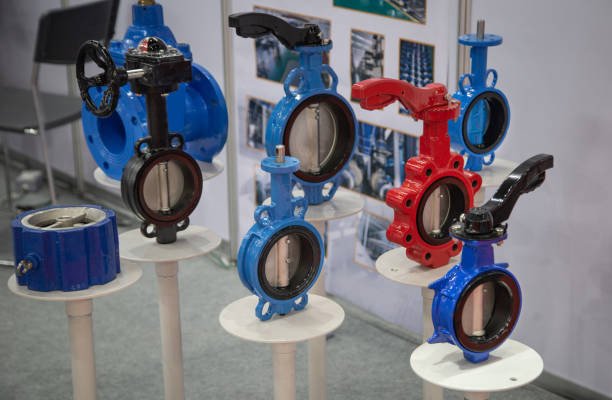
Selecting the wrong butterfly valve can lead to inefficiencies, leaks, or even system failure. Avoiding common mistakes will help ensure you choose the best valve for your application.
1. Choosing the Wrong Size
- Problem: An oversized valve can cause instability, while an undersized valve may restrict flow and create excessive pressure drop.
- Solution: Use proper flow calculations and consult sizing charts to match the valve to your system.
2. Ignoring Material Compatibility
- Problem: Selecting the wrong material can lead to corrosion, contamination, or premature wear.
- Solution: Consider the type of media (water, chemicals, gas) and choose a material resistant to its properties.
3. Overlooking Actuation Needs
- Problem: Manual valves may not be practical for high-frequency operation, and automated valves may require additional infrastructure.
- Solution: Determine whether manual, electric, pneumatic, or hydraulic actuation best suits your process needs.
4. Not Considering Pressure and Temperature Ratings
- Problem: Using a valve that cannot withstand the system’s pressure or temperature may lead to leaks or failure.
- Solution: Always check the valve’s pressure class and temperature limits against your system’s requirements.
5. Neglecting End Connection Types
- Problem: Mismatched valve connections can lead to installation challenges and leaks.
- Solution: Select the right end connection type (wafer, lug, flanged) based on your pipeline configuration.
6. Forgetting Industry Standards and Certifications
- Problem: Non-compliant valves can lead to regulatory issues and compromised safety.
- Solution: Ensure the valve meets necessary standards such as API, ANSI, ISO, or NSF.
By avoiding these common mistakes, you can ensure a more efficient, cost-effective, and reliable butterfly valve selection for your industrial application.
Expert Recommendations and Final Selection Tips
Choosing the right butterfly valve requires a careful evaluation of multiple factors, from valve type and material to actuation method and industry standards. Here are some expert recommendations to guide your selection process.
Checklist for Selecting the Best Butterfly Valve
- Define Your Application Needs: Identify the type of media (liquid, gas, corrosive, abrasive) and operating conditions.
- Select the Right Valve Type: Choose between concentric, double-offset, or triple-offset valves based on pressure and sealing requirements.
- Ensure Material Compatibility: Match the valve body, disc, and seat materials to the chemical properties of the media.
- Determine the Proper Actuation Method: Decide between manual, electric, pneumatic, or hydraulic actuation based on automation and control requirements.
- Verify Pressure and Temperature Ratings: Ensure the valve can handle the system’s operating conditions.
- Check Installation and Space Constraints: Consider the pipeline layout and choose the appropriate end connection (wafer, lug, flanged).
- Ensure Compliance with Industry Standards: Look for API, ANSI, ISO, NSF, or other relevant certifications.
- Plan for Maintenance and Longevity: Choose a valve that offers ease of maintenance and durability.
Seeking Expert Consultation
If you’re unsure about your selection, consulting with a valve specialist or supplier can help you make an informed decision. Experts can provide insights based on experience, system requirements, and regulatory compliance.
By following these recommendations, you can ensure that your butterfly valve performs efficiently, reduces downtime, and meets your industrial application’s specific needs.
Conclusion
Selecting the right butterfly valve for your industrial application is crucial for ensuring efficiency, safety, and cost-effectiveness. By understanding different valve types, materials, actuation methods, pressure ratings, and installation factors, you can make an informed choice that meets your system’s specific requirements.
Key takeaways from this guide include:
- Identify the type of media and operating conditions before selecting a valve.
- Choose the right valve type (concentric, double-offset, or triple-offset) for your pressure and sealing needs.
- Ensure compatibility of valve materials with the media being handled.
- Select the appropriate actuation method based on automation and control requirements.
- Verify pressure and temperature ratings to prevent failures.
- Check installation space and end connection types for proper fitting.
- Look for industry certifications and compliance with relevant standards.
By following these guidelines, you can enhance operational efficiency, minimize maintenance costs, and extend the lifespan of your butterfly valve. If you’re still unsure about the best choice for your application, consult an industry expert or supplier for professional guidance.
Investing in the right butterfly valve today will ensure long-term performance and reliability in your industrial processes.
FAQs
1. What factors should I consider when selecting a butterfly valve?
When selecting a butterfly valve, consider factors such as the type of media, pressure and temperature ratings, material compatibility, actuation method, end connection type, and compliance with industry standards.
2. What is the difference between a wafer and a lug-style butterfly valve?
A wafer-style butterfly valve is designed to be sandwiched between two pipe flanges using bolts, whereas a lug-style valve has threaded inserts that allow it to be bolted directly to the pipeline. Lug-style valves provide independent isolation of one side of the pipeline.
3. Can butterfly valves handle high-pressure applications?
Yes, but the selection depends on the type of butterfly valve. Triple-offset butterfly valves are best suited for high-pressure and high-temperature applications, while concentric valves are ideal for low-pressure systems.
4. How often should butterfly valves be maintained?
Maintenance frequency depends on operating conditions. In general, periodic inspections should be done every 6–12 months to check for leaks, wear, and corrosion. High-performance applications may require more frequent servicing.
5. Are butterfly valves suitable for corrosive chemicals?
Yes, but it is essential to choose the right materials. Stainless steel, PTFE-lined, and other corrosion-resistant materials are recommended for handling aggressive chemicals.