In the world of metal forming and cable termination, two methods often take center stage: swaging and crimping. These techniques, while serving distinct purposes, are fundamental across various industries, offering unique advantages depending on the specific application. Whether you’re working in aerospace, construction, or electronics, understanding the differences between swaging and crimping is crucial for ensuring the reliability and durability of your work. This comprehensive guide will explore the nuances of swaging vs crimping tools, their applications, tools, and future trends.
Understanding Swaging
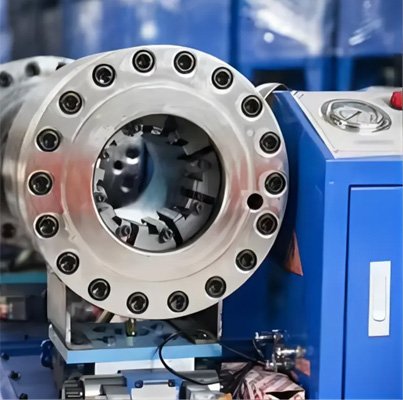
What is a Swaging Tool?
A swaging tool is a device used to reshape metal through the application of compressive forces. Unlike other metalworking techniques that involve cutting or removing material, swaging reshapes the metal by pushing it into a die, creating a new form. This process can be performed either cold or hot, depending on the material and desired outcome.
Swaging is often used to reduce the diameter of tubes, wires, or rods, which is ideal for creating smooth, tapered ends or joining two metal pieces. You can perform the process using manual, hydraulic, or rotary swaging tools, each suited to different levels of precision and industrial needs.
Activated vs Normal Swage
The swaging process can be further categorized into normal swage and activated swage:
- Normal Swage: This refers to the standard swaging process, where you compress material with consistent force to achieve the desired shape. It’s commonly used in simple applications where intricate details aren’t necessary.
- Activated Swage: Activated swaging involves the incorporation of additional mechanisms or processes, such as the application of heat or specialized dies, to enhance precision or achieve specific material properties. This method is often used in applications demanding higher accuracy or when working with more complex materials.
Understanding Crimping
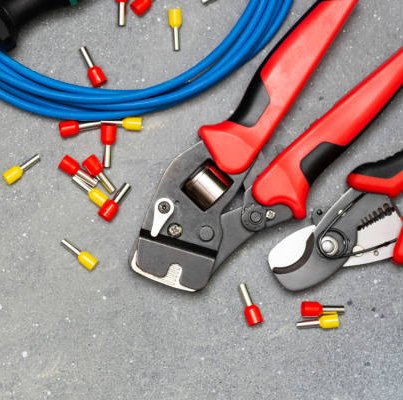
What is a Crimping Tool?
A crimping tool is a specialized device designed to join two pieces of metal or other ductile materials by deforming one or both to hold the other securely. In cable applications, crimping ensures a firm and reliable connection between the cable and its connector. The process involves placing the cable and connector into the crimping tool and applying force, which deforms the connector around the cable, creating a solid mechanical and electrical bond.
Crimping tools come in various designs, ranging from simple handheld tools to advanced electric or hydraulic models. The choice of crimping tool depends on the complexity of the application, the volume of work, and the level of precision required.
Cable Crimp: Importance and Applications
Cable crimping is critical for establishing secure electrical connections, particularly in environments where soldering isn’t feasible or practical. Proper crimping ensures:
- Electrical Conductivity: A well-executed crimp offers optimal electrical flow between the cable and connector.
- Mechanical Strength: Crimped connections are designed to withstand physical stresses, vibrations, and environmental factors.
- Durability: High-quality crimping prolongs the lifespan of electrical systems by preventing failures.
Cable crimping is common in industries like automotive, aerospace, telecommunications, and consumer electronics, where reliability and precision are crucial.
Types of Swaging Tools
Swaging tools are essential for various metalworking tasks, each type serving specific purposes and industries.
Manual Swagers
People typically use manual swagers for smaller projects or when working with softer metals. These tools offer precision and control, making them ideal for detailed work, like in artisan workshops or small-scale applications where custom work is needed.
Hydraulic Swagers
Hydraulic swagers are designed for larger, more industrial applications. These tools utilize hydraulic pressure to apply the necessary force, making them capable of reshaping harder metals and larger workpieces with ease. Hydraulic swaging is often used in industries such as aerospace, automotive manufacturing, and construction, where strength and precision are critical.
Rotary and Pneumatic Swagers
Rotary swagers involve rotating dies that compress the workpiece as it is fed through the machine, creating a seamless and uniform finish. This type of swaging is particularly useful in applications requiring continuous production of swaged components, such as in the manufacturing of wire ropes.
Pneumatic swagers use compressed air to operate, offering a balance between manual and hydraulic swaging. They are often used in medium-scale industrial applications where speed and consistency are important, but the full power of hydraulic systems isn’t necessary.
Types of Crimping Tools
Crimping tools are equally diverse, designed to meet various requirements from simple home wiring to complex industrial installations.
Manual Crimping Tools
Manual crimping tools are the most basic type, ideal for smaller, less complex jobs. People commonly use them in home wiring projects, small-scale electronics assembly, and hobbyist work. These tools usually have adjustable settings to fit different connector sizes and are popular for their simplicity and portability.
Ratchet and Insulated Crimping Tools
Ratchet crimping tools provide better control by ensuring the crimp is complete before the tool releases, which helps maintain consistency and reliability. Insulated crimping tools are specifically designed for insulated connectors, ensuring the insulation stays intact and the crimp is secure.
Electric and Battery-Operated Crimping Tools
Electric crimping tools: Manufacturers design electric crimping tools for high-volume applications where speed and consistency are crucial. These tools, powered by electricity or batteries, allow for quick and efficient crimping with minimal manual effort. Industries such as automotive manufacturing, telecommunications, and large-scale electrical installations widely use electric and battery-operated crimpers.
Swaging vs Crimping: Key Differences
While both swaging and crimping involve deforming materials to create a secure connection or desired shape, they differ significantly in their processes, tools, and applications.
Process and Technique
- Swaging: Primarily focuses on reshaping or resizing metal components. The material is compressed into a die, reducing its diameter or altering its shape without cutting or removing material.
- Crimping: Involves deforming a connector around a cable to establish a mechanical and electrical bond. It’s more about joining two components rather than reshaping one.
Tools and Equipment
- Swaging Tool: Includes manual swagers, hydraulic swaging machines, and rotary swagers. These tools cater to various scales, from small workshops to large industrial setups.
- Crimping Tool: Ranges from simple handheld crimpers suitable for DIY tasks to advanced electric crimping machines used in mass production.
Applications Across Industries
- Swaging: Commonly used in manufacturing wire ropes, creating precise metal fittings, and producing components in aerospace, construction, and medical devices.
- Crimping: Essential in electrical wiring, creating connections in automotive systems, assembling electronic devices, and setting up telecommunications infrastructure.
Advanced Techniques in Swaging vs Crimping
As technology evolves, so do the techniques used in swaging and crimping, with advanced methods improving precision, efficiency, and applicability across various fields.
Custom Swaging Techniques
Mandrel swaging and radial swaging are advanced techniques used in industries where precision and consistency are crucial. Mandrel swaging involves placing a mandrel inside the tube during the swaging process to ensure a smooth interior surface, which is essential in applications such as fuel lines or medical devices. Radial swaging uses radial movement to apply force, allowing for more uniform pressure and a smoother finish.
Advanced Crimping Techniques
In complex electrical systems, techniques such as double crimping or multi-wire crimping are employed. Double crimping provides additional mechanical strength by securing two separate parts of the connector, while multi-wire crimping allows for the simultaneous crimping of multiple wires, which is particularly useful in dense wiring harnesses found in automotive and aerospace industries.
Impact of Material Science: Swaging vs Crimping
The choice of materials plays a significant role in the effectiveness and durability of swaging and crimping processes.
New Materials and Their Effects
Advances in material science have introduced new metals and composites that require specialized swaging and crimping techniques. For example, high-strength alloys used in aerospace applications may require activated swaging processes to achieve the desired precision and strength. Similarly, new insulation materials for cables can affect the crimping process, necessitating the use of insulated crimping tools to ensure a secure connection without damaging the insulation.
Material Compatibility
Understanding material compatibility is crucial when choosing between swaging and crimping. Metals such as copper, aluminum, and titanium behave differently under compressive forces, and each requires specific tools and techniques to achieve optimal results. For example, copper’s malleability makes it ideal for crimping in electrical applications, while aluminum’s lightweight nature makes it a preferred choice for swaging in aerospace components.
Cost-Benefit Analysis
When deciding between swaging and crimping, it’s essential to consider the long-term costs and benefits. Swaging tools, particularly hydraulic models, tend to be more expensive initially but offer long-term durability and strength, which can justify the investment in industries where safety and reliability are paramount. Crimping tools, on the other hand, are generally more affordable and require less specialized training, making them a cost-effective solution for high-volume electrical work.
Automation and Smart Tools
The integration of automation in swaging and crimping processes is transforming these industries, improving both efficiency and consistency. Automated machines equipped with sensors can monitor each step of the process, ensuring precision and reducing human error. Additionally, the rise of smart tools—devices connected to the Internet of Things (IoT)—allows for real-time monitoring and quality control, further enhancing the reliability of swaged and crimped connections.
Sustainable Manufacturing Practices
Industries are increasingly adopting sustainable manufacturing practices to reduce their carbon footprint. In swaging, this might involve using renewable energy sources or optimizing the process to reduce waste. In crimping, the focus is on using recyclable materials and designing tools that consume less power. These practices not only contribute to environmental conservation but also appeal to consumers and businesses looking to meet stringent environmental regulations.
Swaging and Crimping in High-Pressure Environments
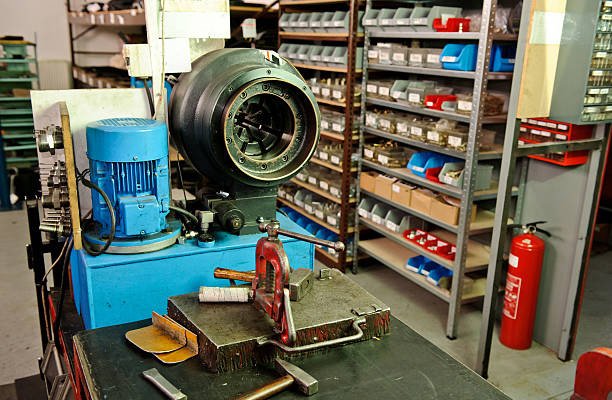
In certain industries, the ability to withstand high pressure is a critical factor in choosing between swaging and crimping.
Subsea and Offshore Applications
In subsea and offshore environments, the durability and strength of connections are vital due to the extreme pressures and corrosive conditions. In these applications, engineers often prefer swaging to create robust connections in pipelines and structural components. While less common, they use crimping in electrical systems where reliable connections are necessary despite harsh conditions.
Aerospace Applications Revisited
In aerospace, both swaging and crimping are widely used for different purposes. Engineers typically use swaging in structural parts and control systems where a strong connection is crucial. Crimping, on the other hand, is crucial for wiring harnesses and electrical systems, where the reliability of the connection under varying conditions is paramount.
Professional Training Programs
Numerous training programs offer courses on the correct use of swaging and crimping tools. These programs, which can range from short workshops to comprehensive certifications, provide hands-on experience and teach industry standards. For example, in the aerospace and construction industries, professionals often undergo extensive training to ensure they can perform these techniques safely and effectively.
Importance of Certification
Certification is particularly important in regulated industries like aerospace, construction, and telecommunications, where the integrity of the connections can impact safety and performance. Certified professionals demonstrate their expertise and often follow strict guidelines, ensuring that swaging and crimping processes meet the highest standards of quality and reliability.
Conclusion and Key Differences
Both swaging and crimping are integral techniques in metal forming and cable termination. Understanding the differences, applications, and tools involved—like the swaging tool and crimper for cable—ensures precise and efficient project execution. By staying informed and adhering to best practices, professionals can harness the full potential of these methods, delivering quality results across industries.
FAQs
Can I use a swaging tool as a crimping tool?
While both tools deform materials, they serve distinct purposes. Swaging is used for reshaping or resizing metal, while crimping is for creating secure electrical connections. It’s advisable to use each tool for its intended function to ensure optimal results.
What’s the difference between activated and normal swage?
Activated swage incorporates additional processes like heat to enhance precision, whereas normal swage relies on standard compressive forces to reshape the material.
How do I ensure a quality cable crimp?
Use the correct crimping tool for your connector and cable type, and follow the manufacturer’s guidelines to achieve a reliable connection. Ensure the cable is stripped properly and positioned correctly in the crimper.
Are there universal crimping tools suitable for all cables?
While some crimping tools are versatile, it’s best to use tools designed for specific connector types to ensure compatibility and effectiveness.
How can I maintain my swaging and crimping tools?
Regular maintenance is crucial. For swaging tools, keep dies clean and well-lubricated, and inspect them for wear. For crimping tools, ensure the jaws are clean and calibrated correctly. Regularly check for any signs of damage or wear.
What materials are best suited for swaging and crimping?
Swaging is ideal for metals like aluminum, steel, and brass, especially in applications requiring strong, durable joints. Copper and aluminum wires, commonly used in electrical applications, are best suited for crimping.