Hydraulic fittings are essential in fluid power systems. They ensure that components connect and function properly. Understanding their importance, types, and uses is crucial for anyone working with hydraulic systems. These fittings help maintain system integrity and efficiency.
What Are Hydraulic Fittings?
Hydraulic fittings connect hoses, tubes, and pipes to hydraulic system components. They can withstand high pressures and provide a leak-proof seal. This helps maintain system integrity and efficiency. These fittings come in various types and configurations. Each type is designed for specific applications and pressure ranges. This variety ensures they meet the needs of different hydraulic systems.
Materials Used in Hydraulic Fittings
Hydraulic fittings are made from materials chosen for their specific application requirements. Therefore, Knowing these materials can help you pick the right fitting for your needs.
- Steel: Steel fittings are known for their strength and durability. They are suitable for high-pressure industrial applications. Their robustness makes them ideal for heavy machinery and demanding environments.
- Stainless Steel: Stainless steel fittings resist corrosion. Consequently, They are perfect for harsh environments. They are also great for medicine and food processing. In these areas, hygiene is crucial.
- Brass: Brass fittings resist corrosion well. They work best in low to medium-pressure systems like pipes and heating. They are popular in many residential and commercial applications.
- Aluminum: Aluminum fittings are lightweight and resist corrosion. They are perfect for weight-sensitive applications in aerospace and automotive industries. Their lightness does not compromise their strength. This makes them ideal for high-performance uses.
- Plastic: Plastic fittings are best used in low-pressure applications. They resist chemicals effectively and are commonly found in lab and medical equipment. Their corrosion resistance makes them suitable for specialized environments.
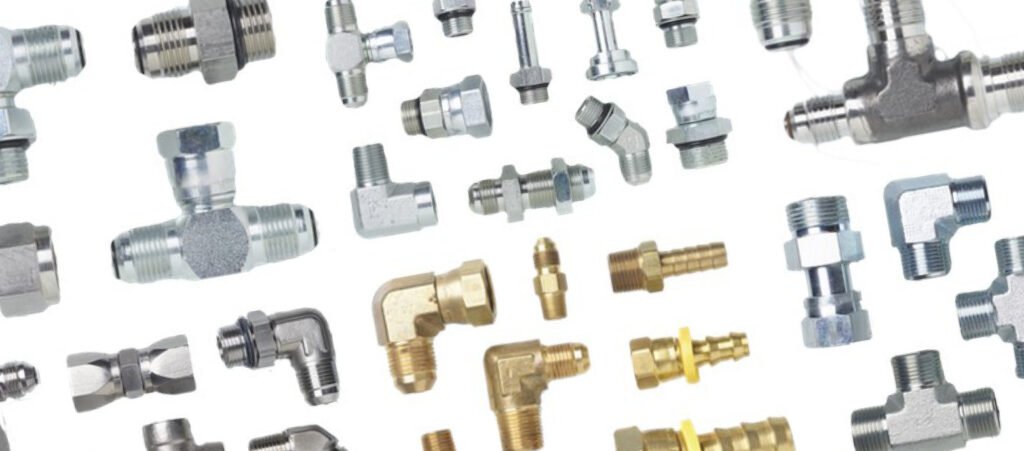
Types of Hydraulic Fittings
There are several types of hydraulic fittings, each serving specific purposes. Understanding these types can help you choose the right fitting for your system:
- Compression Fittings: These fittings join pipes or tubes using compressive force. They are simple and reliable, suitable for both low and high-pressure applications. They consist of a nut, a compression ring (ferrule), and a seat.
- Crimp Fittings: Used with hydraulic hoses, crimp fittings need a crimping tool to secure them onto the hose. They create a tight, permanent connection and are ideal for high-pressure applications.
- Flare Fittings: These fittings flare the end of a tube to form a tight seal. People use them in high-pressure applications, common in the aerospace and automotive industries.
- Bite-Type Fittings: These fittings have a sharp ferrule that “bites” into the hose or tube when the nut is tightened. They create a strong, leak-proof seal, making them perfect for heavy machinery and industrial uses.
- O-Ring Face Seal (ORFS) Fittings: These fittings use an O-ring to create a face seal, offering excellent leak resistance. The food and beverage industry widely uses them for their cleanliness and reliability.
- Push-to-Connect Fittings: Also known as push fittings, these are easy to use and don’t need special tools for installation. They are perfect for quick assembly and disassembly, common in laboratory and pneumatic systems.
Comparison: Permanent vs. Reusable Fittings
Choosing between permanent and field reusable fittings depends on the specific needs of your application:
- Permanent Fittings: Designed to be installed once, these fittings are not meant to be removed or reused. They provide a secure, leak-proof connection suitable for high-pressure applications, ensuring long-term reliability.
- Field Reusable Fittings: Also called reusable fittings, you can install and remove them multiple times. They are perfect for situations where you frequently replace or repair hoses, providing flexibility and easy maintenance.
How to Identify Hydraulic Hose Fittings
Identifying hydraulic hose fittings involves several steps to ensure compatibility and proper function:
- Check the Thread Type: Determine if the thread is NPT, BSP, JIC, or another standard. This ensures that the fitting will connect properly with the system components.
- Measure the Diameter: Use calipers to measure the outside diameter of the thread. Accurate measurement is crucial for selecting the correct fitting size.
- Determine the Thread Pitch: Use a thread pitch gauge to accurately measure the distance between threads. This measurement is crucial for identifying the correct thread type, which, in turn, ensures a secure and reliable fit.
- Identify the Seat Angle: Use a seat angle gauge to measure the angle of the flare or seat. Proper identification of the seat angle ensures a leak-proof connection.
Understanding JIC Fittings
JIC stands for Joint Industry Council. JIC fittings have a 37-degree flare seating surface, making them reliable and versatile for use in hydraulic systems. Consequently, they can withstand high pressures and provide leak-proof connections, making them suitable for many industrial applications.
Choosing the Right End Fittings
Selecting the right end fittings involves considering several factors to ensure optimal performance:
- Pressure Rating: Ensure the fitting can withstand the system’s maximum operating pressure. Using a fitting with a lower pressure rating than required can lead to failures and safety hazards.
- Material Suitability: Select a fitting material that suits the hydraulic fluid and system environment. This prevents corrosion and ensures the fitting lasts longer.
- Size and Configuration: Match the fitting’s size and configuration to the hose or tube. Mismatched sizes can lead to leaks and problems.
- Application Requirements: Consider the need for quick assembly and disassembly, as well as specific sealing characteristics. Doing so ensures that the fitting meets the performance demands effectively.
- Standards and Certifications: Ensure the fitting meets relevant industry standards and certifications. This guarantees its suitability for the intended application and ensures compliance with safety regulations.
Installing Hydraulic Hose Fittings
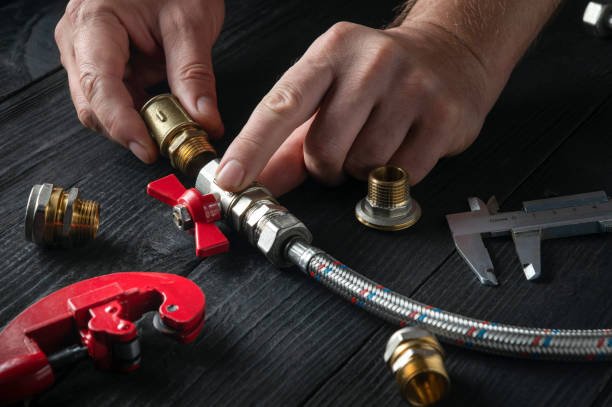
Proper installation of hydraulic hose fittings is crucial for ensuring a secure and leak-proof connection. Follow these steps:
- Cut the Hose: Cut the hose to the required length using a hose cutter. Ensure the cut is clean and straight to prevent leaks.
- Clean the Hose End: Remove any debris or contaminants from the hose end. Clean surfaces ensure a proper seal.
- Install the Fitting: Insert the fitting into the hose end. Seat it fully and align it correctly.
- Crimp the Fitting: Use a crimping tool to secure the fitting onto the hose. Apply even pressure to avoid damaging the fitting or hose.
- Inspect the Connection: Check for leaks and ensure you seat the fitting properly.A thorough inspection prevents future issues.
Sealing Hydraulic Fittings
Sealing hydraulic fittings involves using appropriate methods to ensure leak-free connections:
- O-Rings: Use O-rings to create a seal between the fitting and the connection point. Ensure the O-ring is compatible with the hydraulic fluid.
- Thread Sealants: Apply thread sealant to the threads before tightening the fitting. This helps prevent leaks through the threads.
- Teflon Tape: Use Teflon tape on tapered threads to prevent leaks. Avoid using it on fittings with O-rings or straight threads as it can interfere with the sealing mechanism.
Applications of Hydraulic Fittings
Hydraulic fittings are integral to many industries and applications, ensuring the efficient operation of various systems:
- Industrial Machinery: Hydraulic systems are the backbone of many industrial machines, from manufacturing equipment to conveyor systems. Therefore, hydraulic fittings are essential to ensure these systems operate smoothly and efficiently.
- Construction Equipment: Construction machinery, such as excavators, loaders, and cranes, rely heavily on hydraulic systems. Robust and reliable fittings are crucial for the safety and performance of this equipment.
- Automotive Industry: In automotive applications, hydraulic fittings are utilized in braking systems, power steering, and hydraulic suspensions. Consequently, they enhance the reliability and safety of these critical systems.
- Aerospace Industry: In the aerospace sector, hydraulic systems control landing gear, flight control surfaces, and braking systems. Consequently, the fittings used in these applications must meet stringent standards for reliability and performance.
- Agriculture: Hydraulic systems power a wide range of agricultural machinery, including tractors and harvesters. Therefore, reliable fittings are essential for maintaining the efficiency and functionality of these machines.
- Marine Industry: Marine applications use hydraulic fittings in steering systems, deck machinery, and stabilizers. Consequently, these fittings must withstand harsh marine environments and provide leak-free connections.
Selecting the Right Hydraulic Fitting
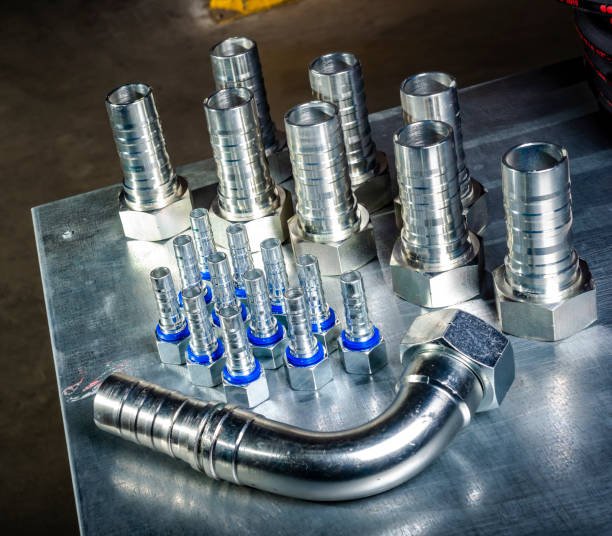
Choosing the right hydraulic fitting involves considering several factors to ensure optimal performance and safety:
- Pressure Rating: Ensure the fitting can withstand the system’s maximum operating pressure. Using a fitting with a lower pressure rating than required can lead to failures and safety hazards.
- Material Compatibility: Select a fitting material that is compatible with the hydraulic fluid and the system’s environment. This prevents corrosion and ensures the longevity of the fitting.
- Size and Configuration: Ensure the fitting’s size and configuration match the hose or tube it will connect to. Otherwise, mismatched sizes can lead to leaks and inefficiencies.
- Application Requirements: Consider the specific requirements of the application, such as the need for quick assembly, disassembly, or specific sealing characteristics. This ensures the fitting meets the operational demands.
- Standards and Certifications: Check if the fitting meets relevant industry standards and certifications. By doing so, you guarantee its suitability for the intended application and ensure compliance with safety regulations.
Maintaining and Inspecting Hydraulic Fittings
Regular maintenance and inspection of hydraulic fittings are essential for the longevity and efficiency of hydraulic systems:
- Visual Inspection: Regularly inspect fittings for signs of wear, corrosion, or damage. Address any issues immediately to prevent system failures.
- Tightening and Adjustments: Properly tighten and adjust the fittings. Loose fittings can cause leaks, while over-tightening can damage threads and seals.
- Replacement of Worn Components: Replace worn or damaged fittings promptly. Using compromised fittings can lead to system inefficiencies and potential safety hazards.
- Lubrication and Sealing: Apply appropriate lubrication and sealing compounds to fittings during maintenance. This helps maintain leak-free connections and extends the life of the fittings.
Hydraulic Fitting Standards and Certifications
Hydraulic fittings must adhere to various standards and certifications to ensure safety, reliability, and compatibility across different systems. Notably, some of the most recognized standards include:
- ISO (International Organization for Standardization): ISO standards ensure that products and services are safe, reliable, and of good quality.
- SAE (Society of Automotive Engineers): The automotive and aerospace industries widely use SAE standards.
- DIN (Deutsches Institut für Normung): DIN standards are common in Europe and apply to many industrial and commercial products.
- ASTM (American Society for Testing and Materials): ASTM standards ensure the quality and safety of materials and products.
- JIC (Joint Industry Council): JIC standards are specifically for hydraulic fittings. They ensure the fittings can withstand high pressures and provide reliable connections.
Common Problems and Solutions
Hydraulic fittings can face several common issues. Here’s how to identify and solve them:
- Leaks: Leaks are the most common problem with hydraulic fittings. They can be caused by improper installation, worn seals, or damaged fittings.Solution: Ensure fittings are properly installed and tightened. Replace worn seals and damaged fittings. Use the appropriate sealing methods, such as O-rings or thread sealants.
- Corrosion: Corrosion can weaken fittings, causing leaks or failures, especially in harsh environments.
- Solution: Use fittings made from corrosion-resistant materials like stainless steel or brass. Apply protective coatings to fittings. Regularly inspect and replace corroded fittings.
- Cracks and Deformation: Fittings may crack or deform because of excessive pressure, poor-quality materials, or improper installation.
- Solution: Ensure the system operates within the specified pressure range. Use high-quality fittings designed for the specific application. Avoid over-tightening fittings during installation.
- Thread Damage: Damaged threads can lead to poor sealing and leaks.Solution: Use thread sealants or Teflon tape appropriately. Avoid cross-threading by carefully aligning fittings during installation. Replace fittings with damaged threads.
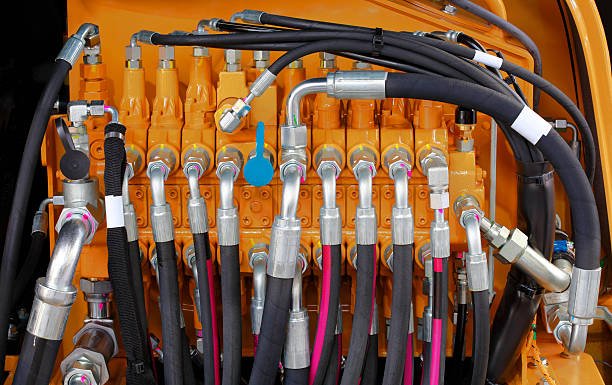
Hydraulic Fittings Safety Tips
Ensuring safety when working with hydraulic fittings is crucial to prevent accidents and injuries. Here are some safety tips to follow:
- Use Proper Tools and Equipment: Always use the right tools and equipment for installing and maintaining hydraulic fittings. This helps prevent damage to the fittings and ensures a secure connection.
- Wear Protective Gear: Wear protective gear like gloves and safety glasses. This protects you from high-pressure fluid leaks and flying debris.
- Follow Manufacturer Guidelines: Adhere to the manufacturer’s guidelines for installation, maintenance, and operation of hydraulic fittings. By doing so, you ensure that the fittings are used correctly and safely.
- Inspect Regularly: Regularly inspect hydraulic fittings for signs of wear, damage, or leaks. Consequently, early detection and replacement of faulty fittings can prevent system failures and accidents.
- Avoid Overloading Systems: Ensure the hydraulic system operates within its specified pressure range. Overloading the system can cause fittings to fail, leading to leaks or bursts.
Future Trends in Hydraulic Fittings
The hydraulic fittings industry continues to evolve with advancements in technology and materials. Here are some future trends to watch:
- Smart Fittings: Smart fittings with embedded sensors can monitor pressure, temperature, and other parameters in real-time. Consequently, this allows for predictive maintenance and improved system efficiency.
- Eco-Friendly Materials: There is a growing trend towards using eco-friendly materials and manufacturing processes. Specifically, this includes biodegradable hydraulic fluids and fittings made from sustainable materials.
- Advanced Coatings: Researchers are developing new coatings to improve the durability and corrosion resistance of hydraulic fittings. These coatings can extend the lifespan of fittings and reduce maintenance costs.
- Customization: Advancements in manufacturing technologies, such as 3D printing, are enabling the production of customized hydraulic fittings tailored to specific applications and requirements.
Conclusion
To ensure efficient and reliable hydraulic systems, it is important to understand the materials, types, installation, and maintenance of hydraulic fittings. By choosing the right fittings, following proper installation procedures, and adhering to safety guidelines, you can enhance both performance and longevity. Furthermore, staying updated on trends and advancements will help you continuously improve your hydraulic system’s efficiency and sustainability.
Frequently Asked Questions (FAQs)
Q1 : How do I choose the right hydraulic fitting? Choosing the right hydraulic fitting involves considering factors such as pressure rating, temperature range, compatibility with hydraulic fluid, and environmental conditions.
Q2 : What are the common materials used in hydraulic fittings? Common materials include steel, stainless steel, brass, and aluminum, each chosen based on the application’s specific requirements.
Q3 : How often should hydraulic fittings be inspected? Regular inspection is crucial, typically every few months, or more frequently in high-stress environments. Look for signs of wear, leaks, and corrosion.
Q4 :Can hydraulic fittings be reused? While some hydraulic fittings can be reused, it’s generally recommended to replace them to ensure the integrity of the connection and prevent potential leaks.
Q5 :What is the difference between threaded and crimp hydraulic fittings? Threaded fittings screw onto components, while crimp fittings use a crimping tool to secure a sleeve around the hose and fitting, providing a more permanent connection.
Q6 :Are there special considerations for hydraulic fittings in marine applications? Yes, marine applications require fittings with high corrosion resistance due to exposure to saltwater and harsh environmental conditions.