Metric ports play a significant role in industrial and mechanical applications, particularly in hydraulic systems. These ports connect various components, ensuring smooth fluid flow and efficient machinery operation. Despite their wide use, many individuals often struggle to fully grasp the intricate details involved in metric port selection and compatibility. Anyone involved in engineering, manufacturing, or maintenance must understand metric ports. This guide dives deep into the complexities of metric ports, breaking down their types, standards, and practical usage in hydraulic systems.
Understanding Metric Ports
Metric ports connect components, particularly in hydraulic systems, through specialized openings. These ports follow international measurement standards based on the metric system, unlike other standards such as the imperial system. Used extensively across Europe, Asia, and various global industries, metric ports ensure high performance and precision in hydraulic applications.
The main feature of metric ports is their threading. This threading allows for secure connections between fittings, tubes, and hoses. With thread standards being vital, it’s important to know the difference between the types of threads and their applications. Hydraulic systems, which often operate under high pressure, depend on the reliability of these threaded connections to prevent leakage and ensure efficiency.
Why Metric Ports Are Important
Understanding the importance of metric ports begins with recognizing how they impact the overall function of hydraulic systems. Since hydraulic machinery serves diverse industries — including construction, aviation, automotive, and manufacturing — choosing the correct fittings and ports is crucial.
Metric ports offer advantages over other systems due to their global acceptance. They provide seamless integration with machinery and components manufactured worldwide. Moreover, metric systems promote accuracy in measurement, ensuring that parts are easily interchangeable. The ability to use standard measurements across various machines reduces the potential for errors in fitting and maintenance.
Metric Thread Standards for Ports
One of the critical aspects of understanding metric ports lies in their thread standards. Several thread types are prevalent in metric systems, with each having distinct uses and advantages. Here are the most commonly used metric thread standards:
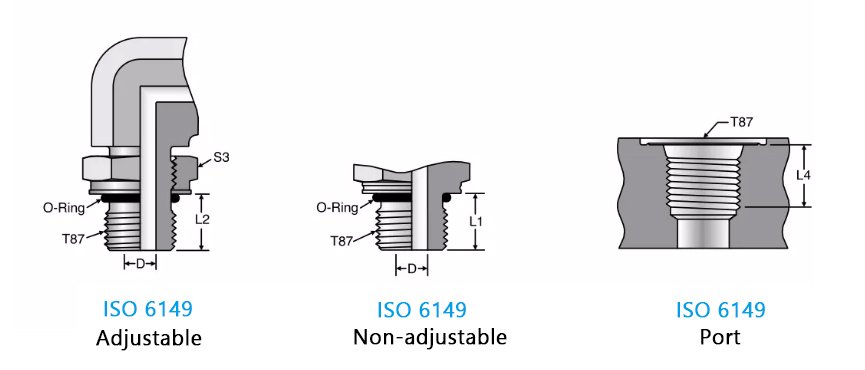
ISO 6149
ISO 6149, a metric thread standard, specifically targets hydraulic ports. Many industries widely adopt this standard because it handles high pressure effectively, particularly in hydraulic systems. Ports following this standard use a metric thread with an O-ring for sealing, ensuring leak-free operation in hydraulic applications.
Metric BSPP (British Standard Pipe Parallel)
Although BSPP threads follow a British standard, many metric applications, especially in Europe, use them. The BSPP system features parallel threads, so the threads do not taper. Instead, an O-ring or bonded washer at the mating surface usually provides the seal. Low-pressure hydraulic systems often feature this type of thread.
DIN 3852
The DIN 3852 standard covers both straight and tapered metric threads. The focus of this standard is precision, which ensures that the ports provide an exceptionally tight seal, making them ideal for high-pressure applications. Additionally, it offers flexibility in using both elastomeric seals and metal-to-metal contact seals, depending on the nature of the application.
JIS (Japanese Industrial Standard)
The JIS standard is commonly found in Asian markets and focuses on hydraulic ports with metric threads. Similar to ISO 6149, JIS threads provide strong sealing properties, often with the help of a gasket or O-ring. This makes them ideal for industrial hydraulic systems where reliability and durability are critical.
How Metric Ports are Used in Hydraulic Systems
Hydraulic systems rely heavily on the correct use of fittings and ports, and metric ports are central to this setup. In such systems, fluid power drives work, and the fluid requires a secure pathway to travel. Metric ports play a crucial role by providing the necessary connections between hoses, pumps, cylinders, and valves.
For example, mobile hydraulic equipment like cranes and excavators uses metric ports to connect hoses to hydraulic pumps and actuators. These connections must withstand extreme pressure, and any leakage could lead to system failure. The use of O-ring sealed metric threads, like those in ISO 6149, helps ensure these connections remain tight and leak-free even under high-pressure conditions.
Common Applications of Metric Ports
Metric ports are employed in a variety of industrial sectors. Here are some examples where metric ports play a vital role:
Automotive Industry
In automotive applications, hydraulic systems power everything from braking systems to power steering. Metric ports ensure that these hydraulic systems function efficiently, with components designed to provide tight seals, reducing the risk of leaks and ensuring optimal performance. These ports allow for easy interchangeability between parts and systems produced across the globe, facilitating repairs and maintenance.
Construction and Heavy Machinery
Large construction machinery, such as bulldozers, excavators, and cranes, relies on hydraulic systems for most of their movements and functions. These machines operate under harsh conditions and high pressures, making the reliability of metric ports and fittings paramount. Metric threads are standard across much of the European and Asian machinery, contributing to the global compatibility of these components.
Industrial Equipment
Factories and production plants that utilize hydraulic presses, conveyor belts, and other heavy machinery depend on secure connections between hydraulic components. Here, metric ports ensure minimal downtime for equipment maintenance and provide consistency in part sizing and threading, enabling quick repairs.
Sealing Methods in Metric Ports
Sealing is critical in hydraulic systems to prevent fluid leaks and maintain system pressure. There are various sealing technologies used in metric ports, depending on the type of thread standard and the application.
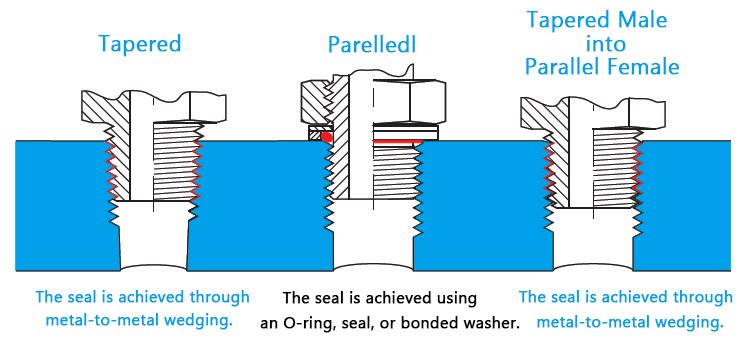
O-Ring Seals
O-rings are one of the most common sealing methods in metric ports. These elastomeric seals provide an efficient, low-cost solution to prevent leakage. When the port and fitting are tightened, the O-ring is compressed, creating a reliable seal. O-rings are highly effective in high-pressure environments, making them a staple in hydraulic systems.
Metal-to-Metal Seals
Metal-to-metal seals are used in extreme pressure situations, where elastomeric seals like O-rings may fail. These seals work by creating a precise fit between two metal surfaces, ensuring no leakage occurs even in high-pressure environments. While they are less common than O-ring seals, they are necessary in certain hydraulic applications, especially those involving heavy-duty machinery.
Bonded Seals
Bonded seals, often referred to as “Dowty seals,” combine the advantages of both O-ring and metal-to-metal seals. They consist of a metal washer with an elastomeric seal bonded to the inside. This type of seal is typically used with BSPP threads and provides an extra level of reliability in medium-pressure systems.
Benefits of Metric Ports in Hydraulic Systems
Using metric ports in hydraulic systems offers several advantages, particularly when compared to other standards like NPT (National Pipe Thread) or SAE (Society of Automotive Engineers) standards.
Global Standardization
One of the most significant benefits of metric ports is their widespread use and global standardization. This makes sourcing parts, repairing systems, and maintaining equipment much more straightforward. With the majority of industrialized nations using metric systems, it reduces the likelihood of compatibility issues when working with machinery from different regions.
Leak Prevention
Metric ports, especially those with O-ring or bonded seals, are designed to minimize leaks. This is critical in hydraulic systems where even a small fluid leak can result in loss of pressure, reduced efficiency, or even catastrophic failure in certain systems.
Ease of Installation and Maintenance
Metric ports are often easier to work with than their imperial counterparts. The standardization of threads and the precision in manufacturing mean that installing and maintaining hydraulic systems is more streamlined. When combined with the common availability of parts, metric ports allow for fast, efficient repairs, reducing machinery downtime.
Conclusion
Understanding metric ports is essential for anyone working with hydraulic systems or industrial machinery. These ports offer reliability, global standardization, and ease of maintenance, making them indispensable in industries that rely on fluid power systems. By familiarizing yourself with the various thread standards, sealing technologies, and practical applications of metric ports, you can ensure the smooth operation and longevity of your hydraulic equipment.
FAQs
What are metric ports used for?
Hydraulic systems primarily use metric ports to connect components like hoses, pumps, and cylinders. They ensure secure, leak-free connections and find widespread use in industries such as automotive, construction, and industrial machinery.
How do metric ports differ from imperial ports?
Metric ports use the metric system for measurements and threading, while imperial ports rely on the inch-based imperial system. Metric ports are more common globally, especially in Europe and Asia, whereas imperial ports are more prevalent in North America.
What is the ISO 6149 thread standard?
ISO 6149 is a thread standard specifically designed for hydraulic ports. It uses metric threads with an O-ring seal, providing a reliable and leak-proof connection in high-pressure applications.
Can metric ports be used with imperial fittings?
No, metric and imperial systems have different thread sizes and standards, meaning they are not interchangeable. Using an incompatible fitting can lead to leaks, system failure, or equipment damage.
What are the advantages of using O-ring seals in metric ports?
O-ring seals offer excellent leak prevention, especially in high-pressure hydraulic systems. They provide a reliable, low-cost solution for sealing connections and are easy to replace during maintenance.
Which industries commonly use metric ports?
Metric ports are widely used in industries such as automotive, construction, and manufacturing. They are essential in hydraulic systems for machinery like excavators, cranes, and factory equipment.