Valves are the unsung heroes of countless industrial and domestic systems, and understanding the valve selection guide is crucial for making the right choice. Whether it’s controlling water flow in plumbing systems or managing high-pressure steam in power plants, valves are essential for ensuring smooth and safe operations. However, not all valves are created equal, and selecting the right one for your specific application can be challenging.
In this guide, we’ll cover the types of valves, their unique characteristics, and how to evaluate key factors such as pressure, temperature, and flow control requirements. By the end, you’ll have a clear understanding of how to choose the perfect valve for your system.
What Are Valves and Why Are They Important?
At their core, valves are mechanical devices designed to regulate the flow of liquids, gases, or slurries. They can be used to start or stop flow, throttle it, or even prevent backflow in a system. Depending on the type, valves can handle everything from low-pressure water lines to extreme temperatures and highly corrosive chemicals.
Their importance lies in their ability to:
- Protect equipment by regulating pressure and flow.
- Prevent leaks or hazardous situations caused by backflow.
- Ensure system efficiency and longevity.
Without the right valve, systems can experience unnecessary wear and tear, reduced performance, and even catastrophic failures.
Common Types of Valves and Their Applications
The right valve depends largely on your system’s needs. Below is a detailed breakdown of common valve types, their features, advantages, and ideal applications:
1. Gate Valves
Gate valves are among the oldest and most commonly used valves in industrial and residential applications. Their design allows for an unobstructed flow when fully open and a tight seal when closed.
Industrial steam systems where tight shutoff is needed.
Working Principle:
The valve operates by raising or lowering a gate (usually wedge-shaped) into the path of the flow. When the gate is fully lifted, the valve is open; when fully lowered, the valve is closed.
Advantages:
Excellent for isolating sections of a system (on/off control).
Minimal pressure drop when fully open.
Cost-effective for large-diameter pipes.
Limitations:
Not designed for throttling (partial opening can cause vibration and erosion).
Operates slowly compared to other valve types due to the gate movement.
Applications:
Water distribution systems for pipeline isolation.
Oil and gas transmission pipelines.
2. Ball Valves
Ball valves are known for their durability, tight sealing, and ease of operation. They are popular in applications requiring quick shutoff and are often used in systems where leakage prevention is critical.
- Working Principle:
A ball with a hole in its center rotates within the valve body. Aligning the hole with the flow allows fluid to pass through, while rotating the ball blocks the flow. - Advantages:
- Quick operation (a 90-degree turn opens or closes the valve).
- Minimal leakage due to tight seals.
- Suitable for high-pressure and high-temperature applications.
- Limitations:
- Not ideal for throttling, as it can damage the ball and seats.
- Limited size range compared to gate or butterfly valves.
- Applications:
- Natural gas and oil pipelines for quick shutoff.
- Chemical processing plants for handling corrosive fluids.
- Plumbing systems for residential and commercial water shutoff.
3. Globe Valves
Globe valves are the go-to solution for throttling and precise flow control. Their unique design allows for better control over flow rates compared to gate or ball valves.
- Working Principle:
A movable plug or disc moves perpendicular to a stationary seat, allowing the operator to finely control the flow. - Advantages:
- Superior throttling capabilities.
- Effective in high-pressure applications.
- Provides a tight shutoff when closed.
- Limitations:
- Higher pressure drop due to the tortuous flow path.
- More expensive and bulkier than simpler valve designs like gate or ball valves.
- Applications:
- Steam systems in power plants for precise pressure and temperature control.
- HVAC systems for regulating water or air flow.
- Chemical processing for throttling and controlling chemical reactions.
4. Check Valves
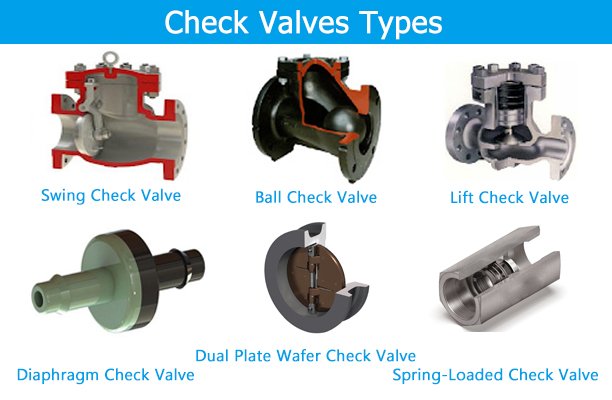
Check valves are vital for protecting equipment from backflow, which can damage pumps or contaminate clean systems. They are simple, cost-effective, and require minimal maintenance.
- Working Principle:
The valve allows fluid to flow in one direction by automatically closing when the flow reverses. The closure mechanism can be a spring-loaded disc, a swing arm, or a ball. - Advantages:
- Prevents backflow without manual intervention.
- Simple and durable design.
- Low maintenance requirements.
- Limitations:
- May not function properly in low-pressure systems.
- Swing and lift check valves can be prone to clogging if solids are present in the fluid.
- Applications:
- Pumping systems to protect against reverse flow.
- Wastewater treatment plants for managing sewage flow.
- HVAC systems to prevent backflow of gases or liquids.
5. Butterfly Valves
Butterfly valves are lightweight, compact, and cost-effective solutions for large-diameter pipelines. Their design makes them ideal for applications requiring quick operation and moderate flow control.
- Working Principle:
A flat, circular disc (the “butterfly”) is mounted on a rotating shaft. Turning the shaft rotates the disc, allowing the operator to control the flow. - Advantages:
- Lightweight and easy to install.
- Requires minimal space in comparison to gate or ball valves.
- Available in large sizes, making them ideal for high-capacity systems.
- Limitations:
- Not suitable for high-pressure applications.
- Throttling capabilities are less precise than globe valves.
- Applications:
- Water treatment plants for isolating flow in large-diameter pipes.
- Food and beverage industries for hygienic applications.
- Cooling water systems in power plants.
6. Diaphragm Valves
Diaphragm valves are designed for hygienic or corrosive environments, making them indispensable in industries like pharmaceuticals and food processing.
- Working Principle:
A flexible diaphragm is pressed against a seat to control flow. This design ensures there are no crevices where contaminants can accumulate. - Advantages:
- Exceptional chemical resistance (depending on diaphragm material).
- Hygienic design suitable for sterile processes.
- Simple construction and easy maintenance.
- Limitations:
- Limited pressure and temperature capabilities compared to metal-seated valves.
- Diaphragms can wear out over time and require replacement.
- Applications:
- Pharmaceutical manufacturing for sterile processes.
- Food and beverage production, such as breweries or dairy plants.
- Chemical plants handling corrosive acids or alkalis.
Summary Table: Valve Types at a Glance
Valve Type | Best For | Advantages | Limitations | Key Applications |
---|---|---|---|---|
Gate Valve | On/off control | Tight seal, minimal pressure drop | Not for throttling | Water, oil, steam distribution |
Ball Valve | Quick shutoff | Durable, minimal leakage | Poor throttling capabilities | Gas lines, chemical processes |
Globe Valve | Precise flow control | Accurate throttling | High pressure drop | Steam, HVAC, chemical industries |
Check Valve | Preventing backflow | Low maintenance, automatic | May clog in dirty fluids | Pumps, wastewater, HVAC |
Butterfly Valve | Large pipelines, moderate control | Lightweight, cost-effective | Limited to low-pressure systems | Water, cooling systems, food industry |
Diaphragm Valve | Hygienic/corrosive environments | Hygienic, chemical resistant | Limited temperature/pressure | Pharmaceuticals, food, chemical plants |
Key Factors to Consider When Selecting a Valve
Choosing the right valve isn’t just about its type. Here are some critical factors to consider:
1. Material Compatibility
The valve material must be compatible with the medium flowing through it. Common materials include:
- Stainless Steel: Resistant to corrosion and suitable for high temperatures.
- Brass: Durable and cost-effective, ideal for water systems.
- Plastic (PVC or CPVC): Lightweight and corrosion-resistant, suitable for low-pressure applications.
2. Flow Control Needs
Some systems only require an on/off function, while others demand precise throttling. Here’s how different valves compare:
- On/Off Applications: Use gate valves or ball valves.
- Throttling Applications: Opt for globe or butterfly valves.
3. Pressure and Temperature Ratings
Ensure the valve can handle your system’s maximum pressure and temperature. For example:
- High Pressure: Forged steel valves or gate valves.
- High Temperature: Metal-seated globe valves or butterfly valves.
4. End Connections
Valve connections should match your system’s configuration. Common options include:
- Threaded: For smaller systems and low-pressure applications.
- Flanged: For high-pressure systems or where frequent maintenance is needed.
- Welded: For permanent, leak-proof installations.
5. Automation vs. Manual Control
Modern systems often use automated valves (e.g., motorized or pneumatic) for convenience and efficiency. Manual valves, on the other hand, are cost-effective and simpler to operate.
Tips for Selecting and Maintaining Valves
Selecting the Right Valve
- Understand System Requirements: Evaluate fluid properties, pressure, and temperature.
- Prioritize Quality: Cheap valves can lead to higher costs in the long run due to maintenance or replacement.
- Test Before Installation: Test the valve’s performance under actual operating conditions.
Maintaining Valves
- Perform Regular Inspections: Check for wear, leaks, and corrosion.
- Lubricate Moving Parts: This reduces wear and ensures smooth operation.
- Follow Manufacturer Guidelines: Adhering to maintenance schedules prolongs valve life.
Conclusion
Selecting the right valve for your system is a crucial decision that impacts efficiency, safety, and cost. By understanding the types of valves and evaluating your system’s requirements, you can make an informed choice that ensures smooth operations and long-term reliability.
Still unsure? Consult with a valve specialist to avoid costly mistakes and ensure your system is equipped with the best solution!
FAQs
1. What is the best valve for high-pressure applications?
Gate valves and globe valves are excellent options for high-pressure systems. Gate valves are ideal for on/off control, while globe valves work well for precise flow regulation under high-pressure conditions.
2. How do I select the right material for my valve?
The material selection depends on the type of fluid or gas in your system. For corrosive fluids, stainless steel or PTFE-lined valves are ideal. For less aggressive environments, brass or PVC valves may be sufficient. Always consider fluid temperature and pressure as well.
3. What type of valve is best for throttling applications?
Globe valves are the go-to choice for throttling, as they are designed to provide precise control over fluid flow. Butterfly valves can also be used for throttling, but they are less accurate than globe valves.
4. Can one valve type handle both liquid and gas flow?
Yes, some valve types, such as ball valves, are versatile and can handle both liquid and gas applications effectively. However, always check the manufacturer’s specifications to ensure compatibility with your specific system.
5. How can I tell if a valve is failing?
Signs of valve failure include leaks, unusual noises, increased pressure drops, difficulty in operation (e.g., stuck valves), and irregular flow rates. Regular inspections and maintenance can help detect these issues early.
6. Is automation worth it for valve control?
Automated valves (e.g., motorized or pneumatic) are worth considering for large-scale systems or applications where frequent adjustments are needed. They improve efficiency and reduce manual labor. However, for small systems or occasional use, manual valves may be more cost-effective.