At its core, a hydraulic pressure drop is a loss of pressure that occurs when hydraulic fluid flows through components of a system. This pressure loss reduces the energy available for powering machinery, leading to inefficiencies or even system failures.
The hydraulic pressure in any system is generated by a pump, and it’s maintained through the proper design and operation of components like pipes, hoses, valves, and actuators. When pressure drops happen, they signal resistance or obstacles within the fluid’s path.
Hydraulic pressure drops are inevitable to some degree, but excessive drops indicate something is wrong. This could stem from improper system design, aging components, or poor maintenance practices. Let’s break this concept down further.
The Science Behind Hydraulic Pressure Drop
Imagine you’re driving up a hill. To maintain speed, your car engine has to work harder due to the resistance from gravity and the incline. Similarly, hydraulic systems experience resistance as fluid flows through pipes, bends, and valves.
This resistance is caused by:
- Friction – Fluid rubbing against surfaces like the inside of pipes.
- Obstructions – Physical blockages or narrow points in the system that restrict flow.
- Fluid Properties – Fluids with higher viscosity (thicker fluids) require more energy to move through the system.
The result? Less pressure at the output end, leading to reduced system performance.
Factors That Cause Hydraulic Pressure Drops
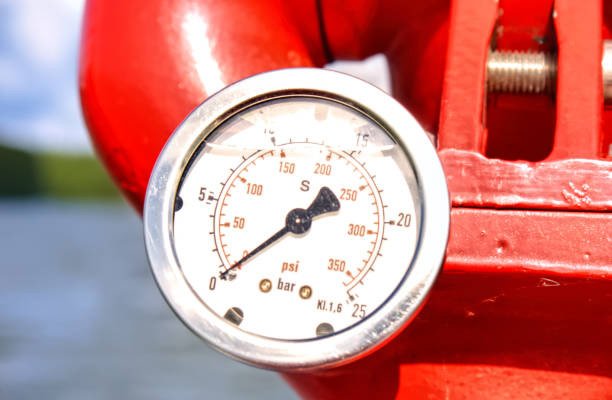
Let’s dive into the common culprits behind hydraulic pressure drops. Understanding these factors can help you identify and address the root cause in your system.
1. Frictional Losses in Pipes and Components
When hydraulic fluid flows, it interacts with the walls of pipes, hoses, and fittings. This interaction creates friction, which resists the movement of the fluid and results in pressure loss. The more contact the fluid has with the walls (e.g., in long or narrow pipes), the greater the friction—and the bigger the pressure drop.
Example: A 10-meter-long pipe with a small diameter will cause significantly more pressure loss than a 5-meter-long pipe with a larger diameter.
2. Length and Diameter of Pipes
Pipe dimensions play a crucial role in determining the extent of pressure drops. Longer pipes increase the distance the fluid has to travel, which means more friction along the way. Similarly, narrower pipes restrict fluid flow, causing higher resistance.
Pro Tip: Opt for shorter and wider pipes wherever possible to minimize friction.
3. Fluid Viscosity
Viscosity refers to how thick or thin a fluid is. High-viscosity fluids (thicker ones) require more energy to flow, leading to greater pressure losses.
Example: In cold weather, hydraulic fluids can thicken, increasing resistance and causing pressure drops. Using temperature-stable fluids can help maintain optimal flow properties.
4. Blockages or Debris in the System
Filters, valves, or pipes can become clogged with dirt, debris, or contamination over time. These blockages obstruct fluid flow and create sudden, sharp pressure drops.
Key Tip: Regularly inspect and clean filters to prevent buildup.
5. Complex System Design
Sharp bends, elbows, and restrictive fittings within the hydraulic system can create turbulence, further increasing resistance and pressure loss.
Example: A hydraulic system with multiple 90-degree bends will lose more pressure compared to a system with a straighter design.
Why Hydraulic Pressure Drop Matters
Hydraulic pressure drops might sound like a minor annoyance, but their impact can be far-reaching. Let’s explore why it’s crucial to keep pressure drops in check.
1. Reduced Efficiency
When energy is lost due to pressure drops, less power is available to operate the machinery. This means your system has to work harder to achieve the same results, leading to inefficiencies.
Impact: Slower equipment performance, reduced productivity, and increased wear on components.
2. Increased Energy Costs
Compensating for pressure drops often requires pumps to work harder or longer, which increases energy consumption.
Real-World Example: A hydraulic press that requires more power to compensate for pressure loss will lead to higher electricity bills over time.
3. Wear and Tear on Components
Excessive pressure drops can overburden pumps, valves, and hoses, causing them to degrade faster. This leads to higher maintenance costs and shorter component lifespan.
4. System Failures
In extreme cases, unaddressed pressure drops can cause the system to malfunction altogether. This can result in operational downtime, costly repairs, or even safety hazards.
How to Reduce Hydraulic Pressure Drops
Tackling hydraulic pressure drops requires a proactive approach. Here are some practical strategies:
1. Optimize Pipe Design
- Use pipes with larger diameters to reduce friction.
- Minimize pipe length where possible.
- Avoid sharp bends and use gradual curves instead.
2. Select the Right Hydraulic Fluid
- Choose a fluid with the appropriate viscosity for your operating temperature range.
- Consider synthetic fluids that offer better flow properties in extreme conditions.
3. Maintain Cleanliness
- Regularly clean and replace filters to prevent debris buildup.
- Flush the system periodically to remove contaminants.
4. Upgrade Components
- Invest in high-quality, low-resistance fittings, valves, and hoses.
- Replace aging or worn-out parts before they cause pressure losses.
5. Simplify the System Layout
- Reduce the number of connections, valves, and bends in your hydraulic system.
- Consider redesigning complex systems for better flow efficiency.
Common Scenarios and Troubleshooting
Let’s look at a practical example:
Scenario: A hydraulic lift in a warehouse is slowing down, and its efficiency has dropped noticeably.
Diagnosis: Upon inspection, technicians find:
- Clogged filters causing blockages.
- Overly narrow hoses creating high resistance.
Solution: Replacing the filters and upgrading to wider hoses restores the system to peak performance.
Conclusion
Hydraulic pressure drop is a critical factor in system performance. While some degree of pressure loss is unavoidable, understanding the causes and taking steps to minimize it can save you from inefficiency, higher costs, and potential downtime.
By optimizing your system design, maintaining cleanliness, and using the right components, you’ll ensure your hydraulic machinery runs like a well-oiled machine—literally!
FAQs
1. Can pressure drops be completely eliminated?
No, some pressure loss is normal in hydraulic systems. However, excessive drops can and should be minimized.
2. How do I measure hydraulic pressure drops?
Use pressure gauges at different points in the system to identify where significant losses occur.
3. What’s the role of temperature in pressure drops?
Temperature changes can affect fluid viscosity, making pressure drops worse in extreme heat or cold.
4. How can I detect a hydraulic pressure drop?
Use pressure gauges to measure pressure at different points in the system. A significant difference in readings indicates a pressure drop.
5. Can hydraulic pressure drops be prevented?
While they can’t be completely eliminated, you can reduce them by optimizing system design, maintaining cleanliness, and using properly sized components.
6. What are the signs of a hydraulic pressure drop?
Signs include slower system performance, overheating, unusual noises, and increased energy consumption.