Imperial threaded fittings are essential in piping systems, providing robust connections across diverse applications. Despite their utility, these fittings can fail due to various factors, many of which are preventable. This article dives deep into the causes, prevention methods, and best practices for ensuring the longevity of imperial threaded fittings.
What Are Imperial Threaded Fittings?
Imperial threaded fittings are connectors used in piping systems, characterized by precise threading that provides a secure seal. These fittings come in various types—elbows, tees, couplings—each serving a specific purpose, whether to join pipes, change flow direction, or connect to other equipment. Threaded fittings are widely used in systems that require durability, such as in industrial, plumbing, and HVAC applications. The use of imperial measurements in their design allows for compatibility with a broad range of systems in the UK, the US, and other regions.
Understanding the structure and applications of imperial threaded fittings is essential for choosing the right type for specific needs, as well as for implementing measures that prevent failure.
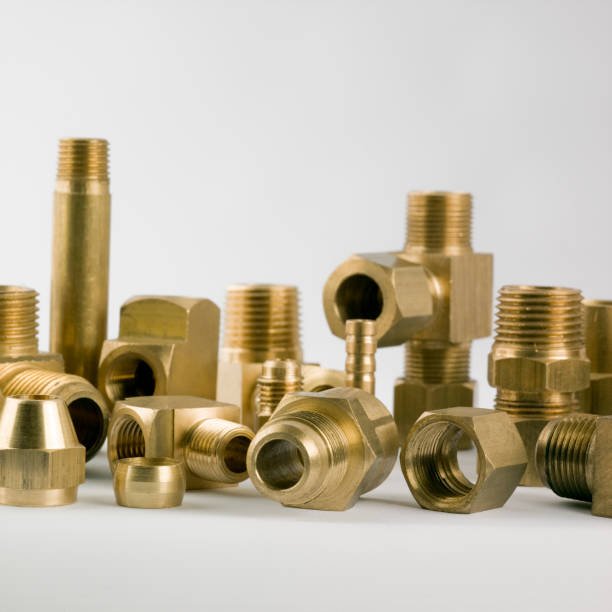
Common Causes of Imperial Threaded Fitting Failures
Material Issues
The material quality of imperial threaded fittings has a direct impact on their durability and performance. Low-quality or incompatible materials may not withstand the high pressures and temperatures common in piping systems. For instance, substandard steel can corrode easily or develop grain boundary corrosion, making it prone to leaks or deformation. Additionally, fittings with contaminants from poor processing or secondary pollution are at risk of structural integrity issues. Using high-grade materials and adhering to strict quality standards can significantly reduce the chances of premature failure.
Manufacturing Defects
The production process itself is a common source of fitting failure. Improper heat treatment, for example, can lead to weak spots within the fitting, reducing its resistance to pressure. Similarly, welding defects or poor machining can cause uneven threading, leading to loose connections. Manufacturing defects like these can be minimized through rigorous process controls and thorough testing. Reputable suppliers typically invest in optimized production lines and conduct regular quality assurance checks to catch any weaknesses before products reach the market.
Improper Installation
Installation practices significantly influence fitting performance. Over-tightening or unevenly tightened threads can distort the fitting, causing stress that may eventually lead to leaks. Inadequate alignment during installation may also compromise the fitting’s ability to handle pressure evenly, leading to failures in specific areas of the connection. Adhering to best practices, including the use of calibrated tools and following installation guides, helps prevent such issues and ensures fittings are stable, secure, and long-lasting.
Design Flaws
Poorly designed fittings can exacerbate failure risks, particularly in high-stress environments. Common design flaws include insufficient consideration of stress factors, inadequate structural rigidity, or misjudged size specifications. These flaws make fittings more susceptible to wear and tear, leading to early failure. Designing fittings to meet specific operational requirements and conducting performance simulations can help avoid these pitfalls, especially in heavy-duty or critical applications.
The Role of Threading Quality in Fitting Durability
Threading quality plays a critical role in ensuring a secure, leak-free connection. High-quality threading creates a tight seal that minimizes the risk of leaks and reduces stress concentration points. In high-pressure applications, precise threading is crucial, as any imperfections can quickly lead to deterioration or damage under extreme conditions. Investing in fittings with well-crafted threads not only extends their lifespan but also enhances overall system efficiency, reducing the need for frequent replacements or repairs.
High-quality threads also make installation easier and allow for more even force distribution, which prevents distortions and misalignments that could lead to failure. Regularly checking for thread integrity, especially in older systems, can also prevent unexpected issues.
Signs of Imminent Threaded Fitting Failure
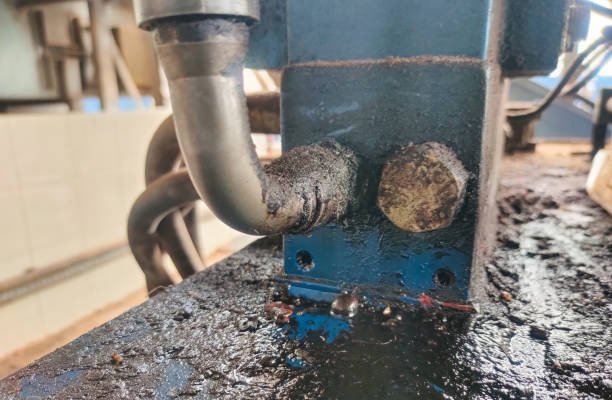
Recognizing early signs of failure can prevent costly downtime and potential safety hazards. Common indicators include:
- Visible Rust or Corrosion: Corrosion often appears as rust or discoloration on the fitting surface, indicating that the material is reacting with environmental factors. This can weaken the fitting over time, making it prone to leaks or breakage.
- Loosened or Misaligned Fittings: If a fitting appears loose or out of alignment, it may be under stress or improperly installed, increasing the likelihood of failure.
- Unusual Noise or Vibration: Strange sounds or vibrations around the fitting are warning signs that internal pressures are affecting its stability.
- Small Leaks or Drops in System Pressure: A decrease in pressure or the presence of minor leaks can signal that the fitting is no longer maintaining a tight seal and needs attention.
Detecting and addressing these signs early can prevent full-scale failures and extend the fitting’s operational life.
Inspection Techniques for Threaded Fittings
Regular inspections are essential to ensure fitting integrity and safety. Effective inspection methods include:
- Visual Inspection: Conduct routine visual checks for surface cracks, corrosion, or other apparent defects. Even minor irregularities can lead to major issues if left unaddressed.
- Pressure Testing: Test fittings under operating pressures to evaluate their performance in real-world conditions. Any minor leaks or deformations during testing suggest potential weak points.
- Ultrasonic Testing: This non-destructive technique detects internal flaws, particularly useful in high-pressure systems where even minor internal defects can lead to catastrophic failures.
Consistent inspections allow early intervention, improving overall system reliability and preventing sudden failures.
Preventive Maintenance for Imperial Threaded Fittings
Preventive maintenance extends the life of threaded fittings and enhances system performance. Essential maintenance practices include:
- Regular Lubrication: Proper lubrication prevents rust and reduces friction on threads, maintaining a secure seal.
- Cleaning: Periodically clean fittings to remove debris and residue, which can compromise sealing surfaces and contribute to deterioration.
- Thread Re-Tightening: Re-tightening fittings ensures they stay securely in place, especially in systems subject to vibrations or pressure fluctuations. This reduces stress and wear on the fittings.
Implementing these preventive steps minimizes wear and tear and helps fittings maintain their structural integrity over time.
Solutions for Preventing and Fixing Threaded Fitting Failures
Addressing fitting issues promptly can prevent minor problems from escalating. Key solutions include:
- Replace Damaged Parts: Replace worn or corroded fittings immediately to avoid leaks or breakages.
- Re-Tap Threads: For minor thread damage, re-tapping can restore the fitting’s ability to form a tight seal, improving its performance.
- Use Quality Sealants: High-quality sealants enhance thread sealing, preventing minor leaks and reinforcing fitting durability in high-pressure systems.
Proactive maintenance and timely repairs can greatly reduce downtime and improve fitting lifespan.
Choosing the Right Supplier for Quality Threaded Fittings
Working with a reliable supplier is essential to securing high-quality fittings. Look for suppliers who:
- Provide certified materials and document quality standards
- Utilize advanced production processes with thorough testing protocols
- Have a track record of product quality and reliable performance
Choosing the right supplier not only ensures better fittings but also improves system reliability and reduces long-term maintenance costs.
Cost-Benefit Analysis: Quality Threaded Fittings vs. Replacement Costs
While quality fittings may involve a higher upfront investment, they offer significant long-term savings. High-quality fittings reduce the need for frequent replacements, minimize system downtime, and require less maintenance. This investment also lowers the overall risk of failures, contributing to operational efficiency and safety. By choosing reliable, durable fittings from the start, businesses can reduce repair costs, prolong system lifespan, and optimize resources.
Conclusion
By understanding the causes of threaded fitting failures and implementing proactive measures, you can extend the life of imperial threaded fittings and ensure consistent performance. From choosing quality materials and following best installation practices to conducting regular inspections, each step is crucial in maintaining the integrity and longevity of imperial threaded fittings.
FAQs
What are the main causes of failure in imperial threaded fittings?
The primary causes include low-quality materials, manufacturing defects, improper installation, and design flaws. Each of these factors can weaken fittings, leading to issues like leaks or structural damage.
How can I prevent failures in imperial threaded fittings?
Preventive measures include choosing high-quality materials, following correct installation procedures, conducting regular inspections, and performing routine maintenance such as cleaning and re-tightening.
What is the importance of threading quality in imperial fittings?
High-quality threading ensures a tight seal, reducing the risk of leaks and stress-related failures. Precision threading is especially important in high-pressure applications.
What signs indicate that a threaded fitting may fail soon?
Warning signs include visible rust, loose or misaligned fittings, unusual noise or vibration, and minor leaks. Early detection helps prevent larger issues.
What maintenance practices help extend the life of imperial threaded fittings?
Essential maintenance includes lubrication to prevent rust, regular cleaning, and periodic re-tightening to maintain a secure seal and alignment.
How do I choose the right supplier for quality imperial threaded fittings?
Look for suppliers offering certified materials, thorough quality testing, and a history of reliable performance to ensure durable and high-performing fittings.