The efficient operation of hydraulic systems relies heavily on maintaining consistent fluid pressure throughout the system. However, a critical aspect that often leads to inefficiencies is the pressure drop across hose fittings. This phenomenon can negatively impact performance, leading to equipment malfunctions, increased energy consumption, and, ultimately, reduced productivity. In this article, we will delve into the various factors affecting hose fittings pressure drop, why it occurs, and how to manage it for optimal system performance.
What is Hose Fittings Pressure Drop?
Pressure drop refers to the reduction in pressure from one end of the hose to the other, especially when fluid flows through fittings, connectors, or adapters. In hydraulic systems, this pressure loss is inevitable but must be controlled to ensure proper system function. Hose fittings, in particular, are one of the key contributors to pressure drop due to the changes they cause in flow direction and fluid velocity.
When fluid moves through a hose fitting, turbulence and friction can arise. These disturbances restrict the flow, causing the system’s pressure to decrease. If pressure drop is excessive, it can affect the operation of hydraulic components like actuators and valves, compromising the efficiency and safety of the entire system.
Why Does Pressure Drop Occur in Hose Fittings?
Pressure drop in hose fittings occurs primarily due to frictional forces and changes in flow dynamics. As hydraulic fluid passes through a hose and encounters a fitting, the fitting can alter the speed and direction of the flow, generating turbulence and resistance. Several factors contribute to pressure drop in hose fittings, which we will explore in greater detail:
Frictional Losses in Hose Fittings
Every hose fitting introduces friction between the fluid and the internal surface of the fitting. This friction generates resistance, slowing the fluid and causing a reduction in pressure. The larger the surface area in contact with the fluid or the rougher the fitting’s internal texture, the greater the frictional losses.
Flow Restrictions
Many hose fittings have narrower passages than the hose itself. As fluid flows through these restricted areas, its velocity increases, leading to pressure loss. Elbows, tees, reducers, and other specialty fittings tend to create significant restrictions, exacerbating pressure drop.
Turbulence
When hydraulic fluid encounters sharp turns or transitions within fittings, it often leads to turbulence. Turbulence is a chaotic flow pattern that further increases energy loss in the system, contributing to a higher pressure drop. Elbow fittings are notorious for causing turbulence due to the abrupt changes in flow direction.
Viscosity of Fluid
The viscosity, or thickness, of the hydraulic fluid plays a pivotal role in pressure drop. Higher-viscosity fluids are more resistant to flow, resulting in greater pressure loss through fittings. The viscosity can vary depending on fluid temperature, with colder fluids becoming thicker and more difficult to pump.
Fitting Design and Material
The design and material of hose fittings also influence pressure drop. Poorly designed fittings with sharp edges or narrow passages create more resistance, while fittings made from materials with rough internal surfaces exacerbate frictional losses. Conversely, high-quality fittings with smooth internal surfaces and optimal designs can help minimize pressure drop.
How to Minimize Pressure Drop in Hose Fittings
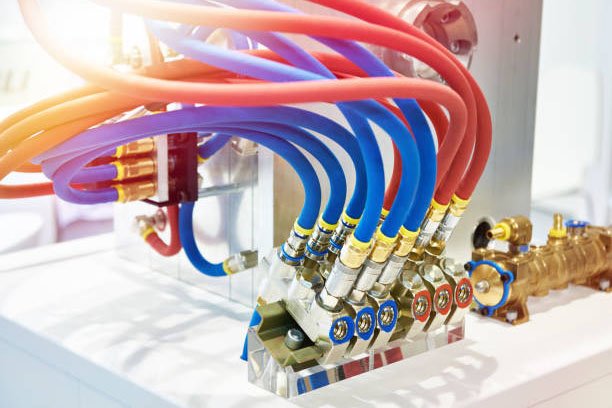
Understanding the factors that cause pressure drop is the first step toward minimizing it. Here are several strategies you can employ to reduce pressure loss in hose fittings:
Select Properly Sized Hose and Fittings
One of the simplest ways to reduce pressure drop is to choose fittings and hoses that are properly sized for the application. Ensure that the hose diameter matches the fitting size, avoiding any unnecessary restrictions. Oversizing the hose slightly can help reduce the velocity of the fluid, minimizing friction and pressure loss.
Use High-Quality Fittings
Investing in high-quality hose fittings designed for optimal flow can make a significant difference in pressure drop. Look for fittings with smooth, rounded internal surfaces to minimize friction and turbulence. Stainless steel and brass fittings tend to offer better flow characteristics than some cheaper alternatives.
Minimize the Number of Fittings and Elbows
Each additional fitting or elbow introduces a new point of resistance, contributing to pressure drop. Where possible, reduce the number of fittings in your hydraulic system. For example, instead of using multiple 90-degree elbows, try to reroute the hose to avoid sharp turns.
Maintain Appropriate Fluid Viscosity
Ensure that the hydraulic fluid being used is appropriate for the system’s operating temperature. Viscosity changes can lead to excessive pressure drop, especially if the fluid thickens due to low temperatures. In colder environments, consider using a lower-viscosity fluid or heating the system to maintain the correct temperature.
Use Long Radius Elbows
When elbows are necessary, choose long radius elbows over short radius ones. Long radius elbows cause less disruption to the fluid flow, resulting in less turbulence and pressure loss. While these fittings may require more space, the reduction in pressure drop often justifies the trade-off.
Regular Maintenance and Inspection
Regularly inspecting hoses and fittings for wear, damage, or blockages is crucial in minimizing pressure drop. Any internal buildup or corrosion can restrict flow and increase resistance. Periodically flushing the system and replacing worn fittings can help maintain consistent pressure throughout the system.
Impact of Hose Fittings Pressure Drop on Hydraulic Systems
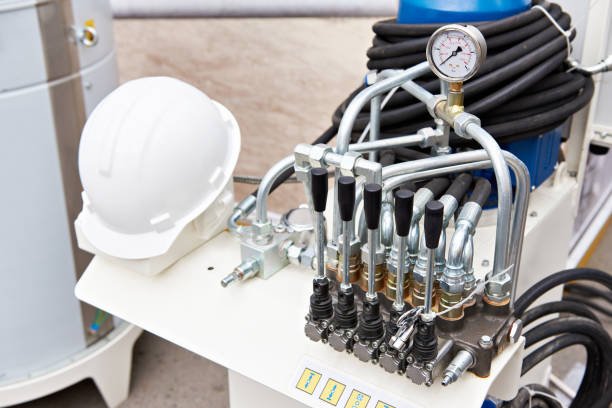
The consequences of excessive pressure drop in hose fittings extend beyond mere performance inefficiencies. Here’s how pressure drop can affect a hydraulic system:
Reduced System Efficiency
When the pressure drop across hose fittings is significant, more energy is required to maintain fluid flow. This leads to increased power consumption, driving up operational costs and reducing the overall efficiency of the system.
Component Wear and Tear
Excessive pressure drop can cause certain components to overcompensate, resulting in higher wear and tear. Pumps, for example, may need to work harder to maintain the required pressure levels, shortening their lifespan.
System Failure
In extreme cases, excessive pressure drop can lead to system failure. If critical components do not receive sufficient pressure to function properly, the entire hydraulic system may shut down or operate unpredictably, posing a safety risk.
Calculating Pressure Drop in Hose Fittings
To effectively manage pressure drop, it’s essential to calculate it accurately. The pressure drop across hose fittings can be calculated using the Darcy-Weisbach equation or by referring to manufacturer’s data charts for specific fittings. Here’s a simplified approach to understanding these calculations:
Darcy-Weisbach Equation
The Darcy-Weisbach equation is a widely used formula to calculate pressure loss in a piping system, including hose fittings. The equation is as follows:
ΔP = (f * L * V^2) / (2 * D)
Where:
ΔP = Pressure drop
f = Friction factor (depends on the fitting material and fluid properties)
L = Length of the hose
V = Fluid velocity
D = Diameter of the hose
For hose fittings, L would represent the equivalent length of the fitting, which manufacturers typically provide. The friction factor depends on factors like the fluid’s viscosity and the fitting’s material.
Using Manufacturer’s Data
Most fitting manufacturers provide pressure drop charts or software tools that simplify the process. These resources allow you to input variables such as flow rate, hose diameter, and fitting type to get an accurate estimate of pressure drop.
Common Misconceptions about Hose Fittings Pressure Drop
Several misconceptions surround pressure drop in hose fittings, leading to inefficiencies or suboptimal system designs. Let’s address a few common myths:
Larger Hoses Always Solve Pressure Drop Issues
While increasing hose size can reduce pressure drop in some cases, it is not always a universal solution. If the fittings are undersized or poorly designed, increasing the hose size alone will not prevent pressure loss. It is critical to match both hoses and fittings for optimal performance.
All Fittings Cause the Same Amount of Pressure Drop
Not all hose fittings are created equal when it comes to pressure drop. Elbows, reducers, and tees introduce varying amounts of resistance, with some designs (e.g., long-radius elbows) being far more efficient than others. Always consider the specific design of the fitting when assessing pressure drop.
Pressure Drop Is Only an Issue at High Flow Rates
While high flow rates exacerbate pressure drop, even systems operating at low flow rates can experience significant pressure loss if the fittings are undersized or poorly maintained. Pressure drop should be monitored regardless of flow conditions.
Conclusion
Managing hose fittings pressure drop is crucial for the efficient and safe operation of hydraulic systems. By understanding the causes of pressure drop—such as friction, turbulence, and fitting design—you can take proactive steps to minimize pressure loss. Properly sizing hoses and fittings, using high-quality components, and performing regular maintenance will ensure optimal system performance while reducing energy consumption and equipment wear. As hydraulic systems become more complex, focusing on pressure management will play a key role in maintaining reliability and extending the life of your equipment.
FAQs
How do I measure pressure drop in hose fittings?
Pressure drop can be measured using pressure gauges installed at various points along the hose. Compare the inlet and outlet pressures to determine the amount of drop across a fitting.
Can I reduce pressure drop by using flexible hoses?
Flexible hoses can help reduce pressure drop by allowing smoother flow paths, especially if they can replace rigid fittings with sharp turns. However, the material and design of the hose still play a significant role.
What role do couplings play in pressure drop?
Couplings can contribute to pressure drop, especially if they introduce flow restrictions or turbulence. Opt for couplings with smooth internal designs to minimize this effect.
Is pressure drop the same as pressure loss?
Yes, pressure drop and pressure loss are terms used interchangeably to describe the reduction in pressure as fluid flows through a system.
Can pressure drop affect system safety?
Excessive pressure drop can lead to system malfunctions or failure, posing safety risks, especially in high-pressure hydraulic systems.
Why do elbows cause more pressure drop than straight fittings?
Elbows change the direction of fluid flow, creating turbulence and increasing resistance, which leads to a greater pressure drop compared to straight fittings.