Introduction to Check Valves
Check valves are critical components in fluid systems designed to allow fluid flow in one direction while preventing reverse flow. This function is essential for maintaining system integrity, preventing damage to pumps, pipelines, and other equipment. Check valves are used across various industries, including oil and gas, chemical processing, HVAC systems, and water treatment facilities.
By ensuring that the fluid flows correctly, check valves protect equipment from potential failures due to backflow, contamination, and pressure surges. In this guide, we will explore the different types of check valves, their mechanisms, advantages, limitations, and the ideal applications for each type.
How Does Check Valves Work
Check valves are automatic devices that operate without external control, allowing fluid to flow in only one direction. The basic principle involves a mechanism that opens to let fluid pass when the flow is in the desired direction and closes to block the reverse flow.
When fluid flows forward, the pressure pushes a disc or similar mechanism away from the valve seat, allowing the fluid to move through. If the flow reverses, the disc returns to its seat, closing the valve and preventing backflow. This simple but effective operation makes check valves indispensable in protecting sensitive equipment like pumps and compressors.
Key Components of Check Valves
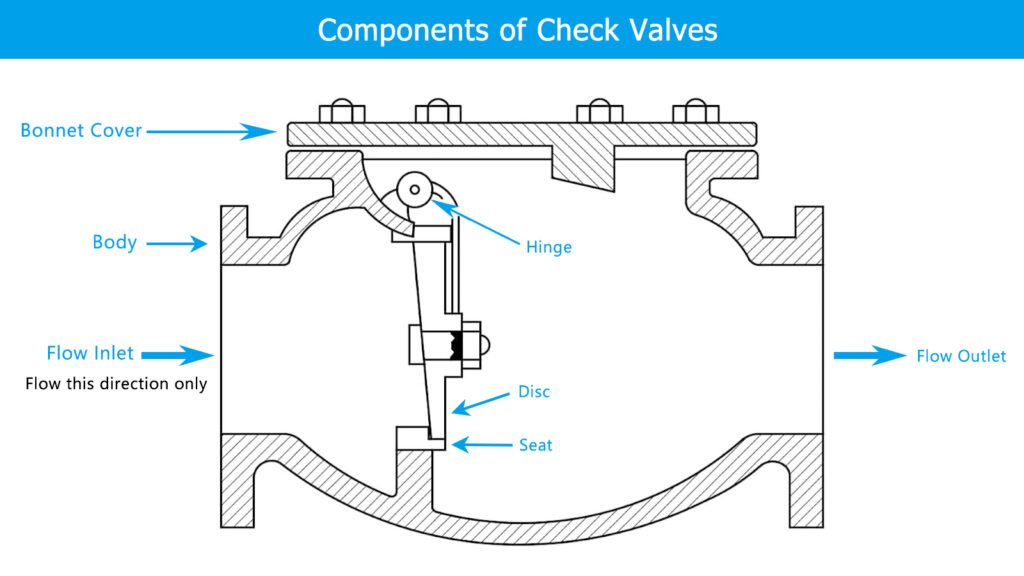
Check valves are made up of several critical components that work together to regulate fluid flow:
- Body: The outer casing of the valve, usually made from materials like stainless steel, brass, or plastic, depending on the application and fluid type.
- Disc: The movable part that controls the flow. It can be a ball, diaphragm, or plate, depending on the valve type.
- Seat: The surface against which the disc rests when the valve is closed. It ensures a tight seal to prevent backflow.
- Hinge or Spring Mechanism: Used to control the disc’s movement. Swing check valves use a hinge, while spring-loaded check valves rely on a spring to close the valve quickly.
- Inlet and Outlet Ports: These ports connect the valve to the pipeline, allowing fluid to enter and exit the valve in a controlled manner.
Types of Check Valves and Their Applications
1. Swing Check Valve
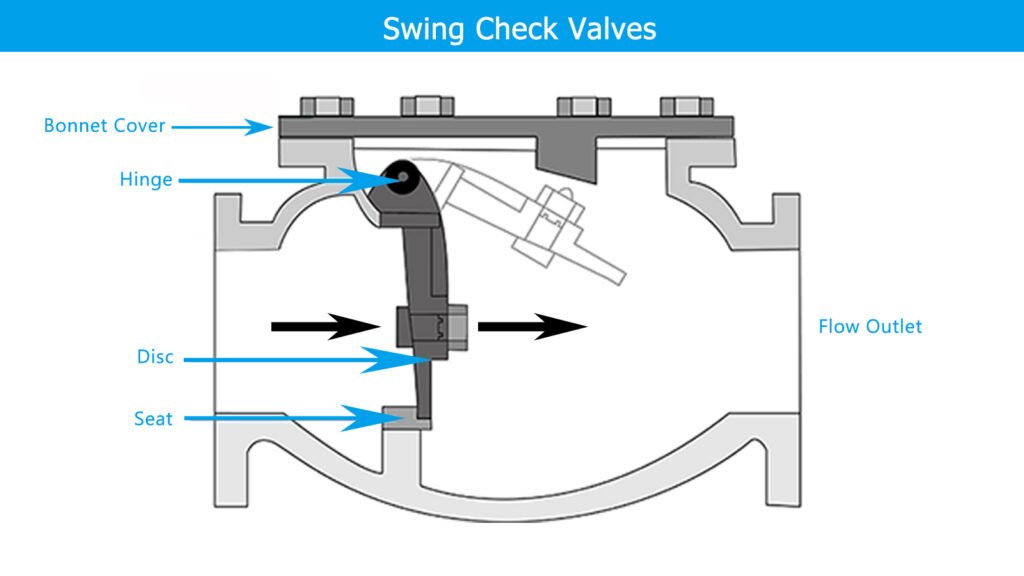
A swing check valve features a hinged disc (or flapper) that swings open when fluid flows forward and closes when the flow reverses, stopping backflow. This type of valve offers minimal resistance, making it ideal for horizontal installations where low-pressure loss is critical.
Advantages
- Low-pressure drop: The design allows for minimal resistance, preserving system efficiency.
- Best for low-velocity flows: Ideal for systems where consistent flow rates are essential.
Limitations
- Not suited for pulsating flows: Rapid flow changes can wear the valve and lead to improper sealing.
- Water hammer risk: In high-velocity systems, the rapid closure of the valve can cause a water hammer effect, leading to pressure surges.
Applications
- Water and wastewater systems
- HVAC systems
- Oil and gas pipelines
2. Ball Check Valve
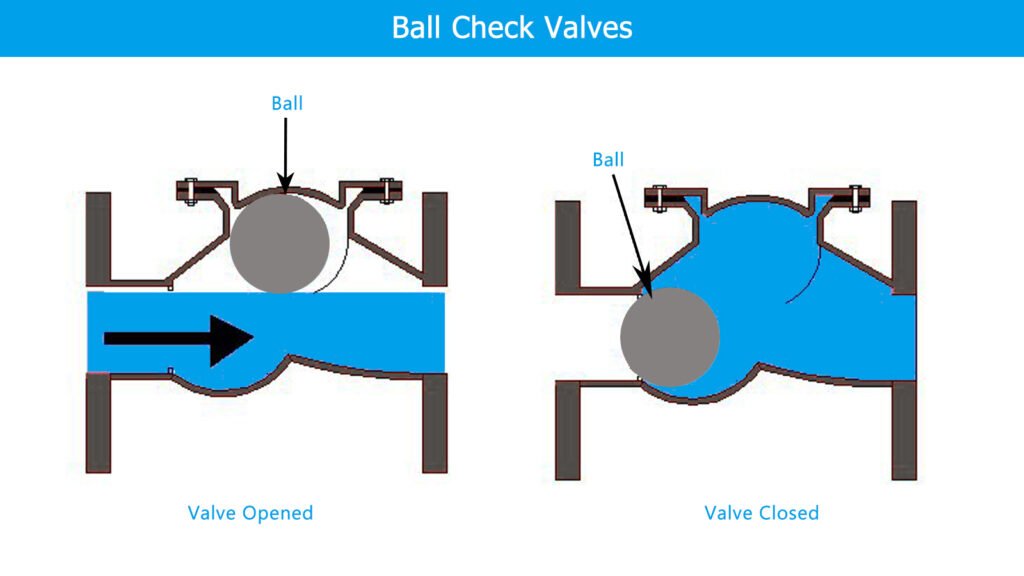
Ball check valves use a spherical ball inside the valve body to control the flow. When fluid flows in the intended direction, the ball is lifted off its seat by the pressure, allowing fluid to pass. When the flow reverses, the ball is pushed back into place, sealing the valve.
Advantages
- Simple design: Fewer moving parts make ball check valves easy to maintain.
- Handles contaminated media: The design works well in systems containing particulates or viscous fluids.
Limitations
- Higher pressure drop: The ball can create more resistance to flow, leading to a higher pressure drop.
- Not ideal for low-pressure systems: In low-pressure applications, the ball may not seat properly, causing leakage.
Applications
- Pump discharge applications
- Slurry and viscous fluid systems
- Food processing industries
3. Lift Check Valve
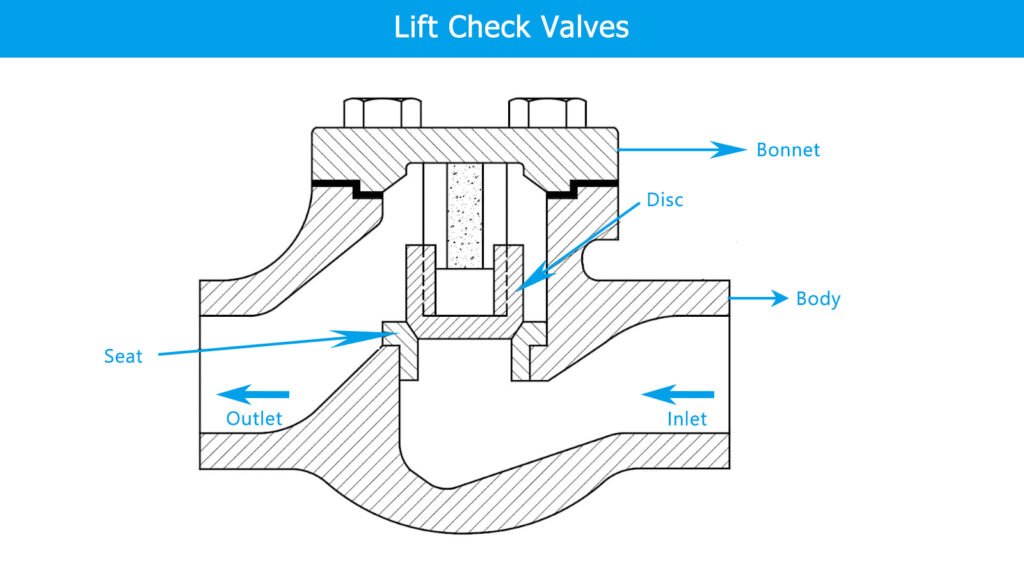
Lift check valves feature a disc or piston that moves vertically within the valve body. Forward pressure lifts the disc off its seat, allowing fluid to flow. When the flow reverses, the disc falls back into place, closing the valve and preventing reverse flow. These valves are suitable for both horizontal and vertical installations, provided the pressure is sufficient.
Advantages
- Ideal for high-pressure systems: Lift check valves are robust enough to handle high-pressure conditions.
- Can be installed horizontally or vertically: Flexibility in system design due to installation options.
Limitations
- Not suitable for dirty fluids: Particles in the fluid can block the valve or cause damage.
- Requires proper alignment: Incorrect installation can lead to valve malfunction.
Applications
- Steam and gas systems
- High-pressure water applications
- Chemical and petrochemical industries
4. Diaphragm Check Valve
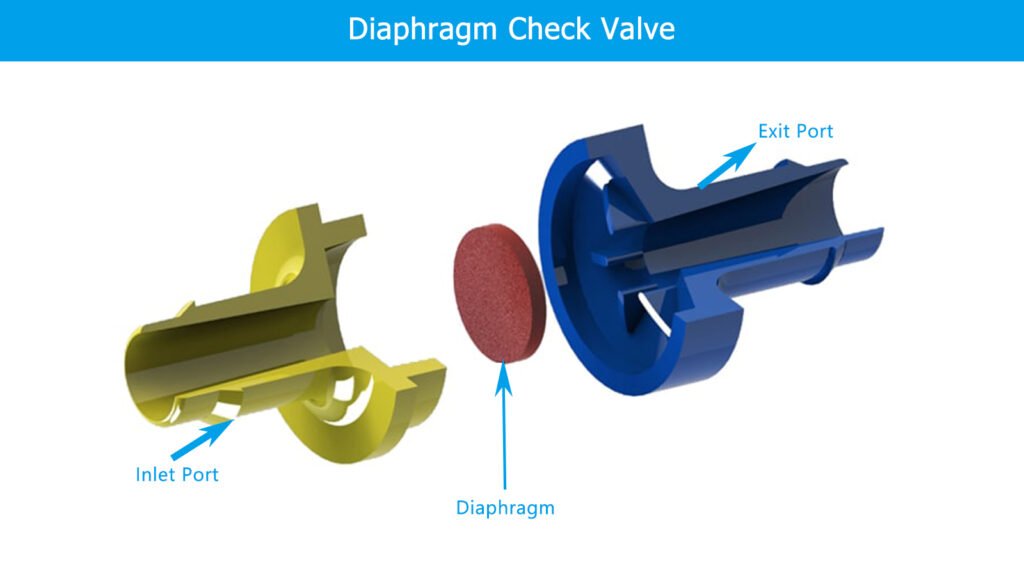
Diaphragm check valves use a flexible diaphragm made of rubber or elastomer, which flexes to allow forward flow and returns to its original position to seal the valve when flow reverses. This design is particularly effective in sanitary or sensitive applications where contamination is a concern.
Advantages
- Excellent for sanitary applications: The diaphragm design ensures a clean, contamination-free system, making it suitable for food and pharmaceutical industries.
- Effective for sensitive media: Diaphragm check valves provide a tight seal to prevent contamination in systems carrying sensitive fluids.
Limitations
- Limited in high-pressure applications: The diaphragm can fail in high-pressure environments.
- Prone to wear from abrasive fluids: Abrasive media can damage the diaphragm, reducing efficiency over time.
Applications
- Pharmaceutical and food processing
- Medical equipment
- Chemical dosing systems
5. Dual Plate Wafer Check Valve
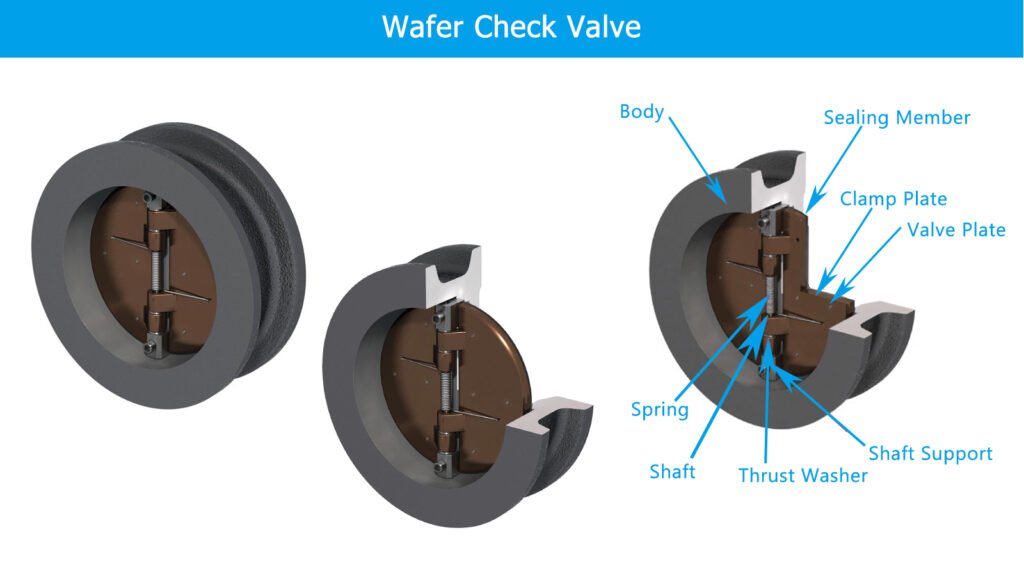
The dual plate wafer check valve, also known as a dual-door check valve, features two spring-loaded plates that pivot open to allow forward flow and snap shut when the flow reverses. This design is compact and lightweight, making it an excellent choice for space-constrained installations. The wafer-style valve is typically installed between two flanges in a pipeline, reducing the need for bulky valve bodies.
Advantages
- Compact and lightweight: Ideal for applications where space is limited.
- Low-pressure drop: The two-plate design offers minimal resistance to flow, maintaining system efficiency.
- Prevents water hammer: The quick-closing action of the plates helps prevent water hammer, reducing potential damage to system components.
Limitations
- Not ideal for very thick fluids: Dual plate wafer check valves may struggle to close properly in systems with highly viscous fluids.
- Limited in very high-pressure applications: The design, while efficient, may not be suitable for extreme pressure environments.
Applications
- HVAC systems
- Power plants and energy generation systems
- Water distribution systems
- Industrial piping systems
6. Spring-Loaded Check Valve
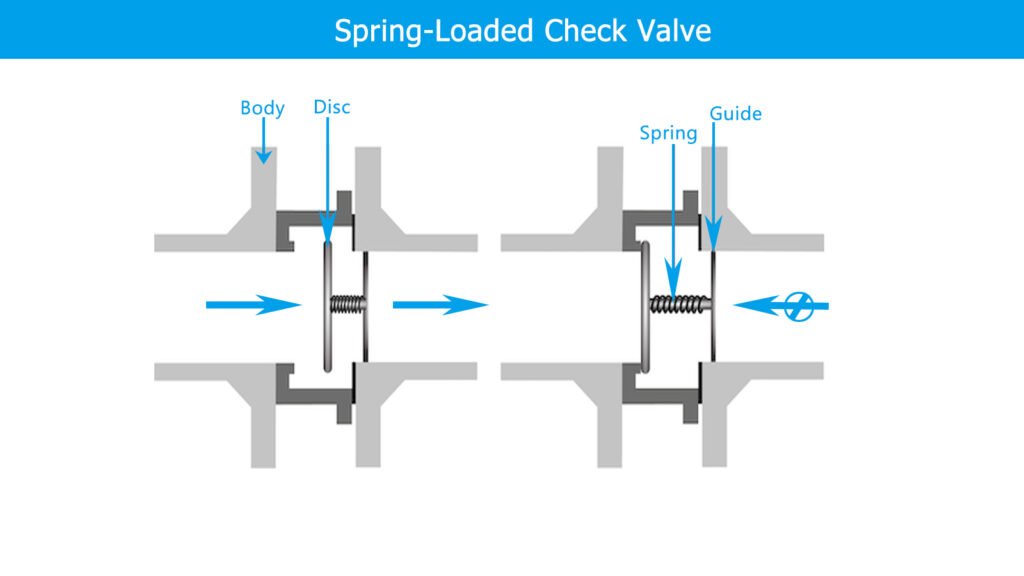
Spring-loaded check valves use a spring mechanism to assist in the closure of the valve. The valve disc or piston is connected to a spring that ensures the valve closes quickly when forward flow stops. This design is particularly effective in preventing water hammer and is suitable for both horizontal and vertical installations.
Advantages
- Prevents water hammer: The spring mechanism ensures controlled closure, avoiding pressure surges.
- Reliable in vertical installations: Spring-loaded check valves work well in both horizontal and vertical systems.
Limitations
- Higher pressure drop: The spring creates resistance, leading to a higher pressure drop in the system.
- Requires regular maintenance: Over time, the spring may weaken or corrode, requiring periodic checks.
Applications
- Water pumping systems
- Compressed air systems
- Chemical processing plants
How to Choose the Right Check Valve
Selecting the appropriate check valve depends on various factors such as the type of media (liquids, gases, slurries), pressure and temperature conditions, flow rate, and system configuration. Using the wrong valve can lead to inefficiencies, equipment failure, and even safety hazards. Below are key considerations to help you choose the right check valve for your system:
1. Media Type
The type of fluid moving through the system is one of the most critical factors when selecting a check valve:
- Liquids: For clean water or other liquid systems, swing or lift check valves are generally preferred. For contaminated or viscous liquids, a ball check valve may be more suitable.
- Gases: Lift or spring-loaded check valves are ideal for gas systems, offering a reliable seal with minimal leakage.
- Slurries: For slurries containing suspended solids, ball or diaphragm check valves are typically used to handle particles without clogging.
2. Pressure and Temperature Ranges
The operating pressure and temperature of the system will also influence the type of check valve you choose:
- High-pressure systems: Lift and spring-loaded check valves are robust enough for high-pressure applications.
- Low-pressure systems: Swing check valves are sufficient for low-pressure systems due to their low resistance.
- High-temperature systems: For high-temperature environments, metal-bodied valves like stainless steel or brass are more suitable.
3. Flow Rates and System Design
The flow rate of the system is also crucial when choosing a check valve:
- Low-velocity flows: Swing check valves are ideal for low-flow systems where minimal resistance is needed.
- High-velocity flows: Spring-loaded or lift check valves are better suited for high-flow systems, providing quick closure to prevent reverse flow.
Installation and Orientation of Check Valves
The installation and orientation of check valves are essential for optimal performance. Whether installed horizontally or vertically, the orientation affects how the valve operates, and improper installation can lead to operational failures.
Horizontal Installation
In horizontal installations, swing check valves and ball check valves perform better as gravity helps keep the disc or ball in place when the valve closes. However, swing check valves may not work as efficiently in systems with fluctuating flows, where rapid closure can cause water hammer.
Vertical Installation
For vertical systems, especially with upward flow, lift check valves and spring-loaded check valves are more effective. These valves use gravity or spring tension to ensure proper closure, even when fluid is not flowing. Avoid using swing check valves in vertical installations unless specifically designed for this orientation.
Maintenance and Lifespan of Check Valves
Check valves are designed for durability, but regular maintenance is critical to ensure their long-term performance. The maintenance needs vary depending on the valve type and the operating environment.
Inspection Frequency
Regular inspections help identify potential issues like wear and tear, corrosion, or debris buildup. Each valve type has its unique maintenance considerations:
- Swing check valves: Inspect the hinge or disc for wear, especially in high-use or abrasive environments.
- Spring-loaded check valves: Check the spring mechanism regularly for corrosion or tension loss.
- Diaphragm check valves: Diaphragms can degrade over time, especially when exposed to abrasive or corrosive media, so frequent checks are recommended.
Cleaning and Debris Removal
In systems with particulates or slurries, debris can accumulate in the valve, causing improper sealing or valve failure. Regular cleaning, especially in ball check valves and systems handling viscous or contaminated fluids, will help prevent clogs and ensure efficient operation.
Valve Replacement
Over time, check valves will wear out and need to be replaced. Monitoring system performance for signs like increased pressure drops, leaks, or sluggish operation can help determine when a valve needs replacing.
Conclusion
Choosing the right check valve is essential for ensuring the efficiency and safety of your fluid systems. By matching the valve type to the media, pressure, temperature, and system design, you can ensure reliable performance and long-term durability. Regular maintenance and proper installation are also key factors in extending the lifespan of check valves and preventing costly failures.
FAQs
1. What is a check valve?
A check valve is a one-way valve designed to allow fluid to flow in one direction and prevent reverse flow.
2. How does a check valve work?
A check valve operates automatically, opening when fluid flows forward and closing when flow reverses to prevent backflow.
3. What are the main types of check valves?
Common types include swing check valves, ball check valves, lift check valves, diaphragm check valves, wafer check valves, and spring-loaded check valves.
4. Where are check valves used?
Check valves are used in industries such as oil and gas, water systems, HVAC, chemical processing, and pharmaceuticals.
5. Can check valves be installed vertically?
Yes, certain types of check valves, such as lift and spring-loaded check valves, can be installed vertically, but proper orientation is crucial for effective operation.