Hydraulic flange fittings are vital components in industrial applications, allowing fluid to move seamlessly through systems under high pressure. Their role in maintaining fluid power transfer makes them integral to many hydraulic systems across industries like manufacturing, construction, and energy. However, disassembling these fittings can be challenging and potentially hazardous if not performed with care. This guide details essential precautions to take when disassembling hydraulic flange fittings to ensure safety and prevent damage.
Understanding Hydraulic Flange Fittings
Hydraulic flange fittings are used to connect pipes, hoses, and other equipment in hydraulic systems. They are specially designed to withstand high pressures and ensure a tight seal that prevents fluid leaks, even in demanding environments. These fittings often feature bolts, O-rings, and other components that require specific tools and techniques for safe disassembly. Knowing the type of flange fitting you’re working with is crucial, as different fittings may require unique handling and safety measures.
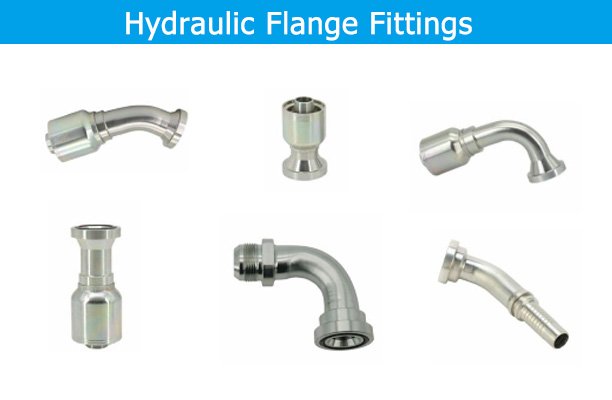
Reasons for Disassembling Hydraulic Flange Fittings
Disassembling hydraulic flange fittings may be necessary for several reasons:
- Routine Maintenance: Regular inspections and maintenance require periodic disassembly to check for wear, corrosion, and other issues.
- Component Repair or Replacement: Damaged or faulty components need to be replaced to maintain the hydraulic system’s efficiency and safety.
- Emergency Troubleshooting: In cases of unexpected leaks or malfunctions, disassembly may be required to diagnose and resolve issues quickly.
Understanding why a disassembly is needed can help prepare for the specific steps and tools required to safely dismantle the flange fitting.
Safety Risks in Disassembling Hydraulic Flange Fittings
Working with hydraulic systems involves inherent risks, particularly when dealing with high-pressure connections. Key safety risks include:
- Hydraulic Fluid Leaks and Pressure Release: Disassembling without relieving pressure can lead to sudden fluid release, causing injuries from high-velocity fluid or hot oil.
- Risk of Equipment Damage: Using incorrect tools or mishandling parts can damage flange fittings or surrounding equipment, leading to costly repairs or system failures.
- Environmental Hazards: Hydraulic fluid leaks can have environmental consequences if not contained and cleaned properly.
Required Tools and Equipment for Safe Disassembly
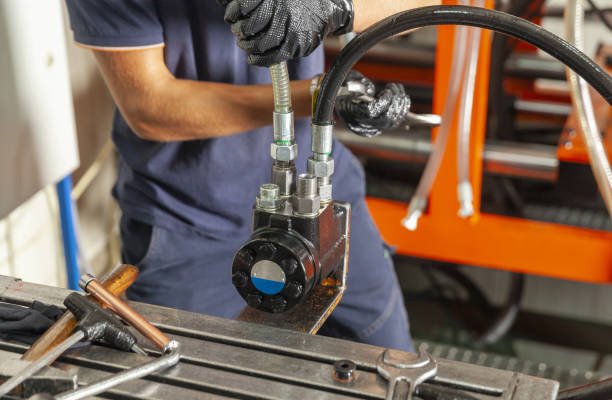
To ensure safe and effective disassembly of hydraulic flange fittings, specific tools and equipment are necessary:
- Hand Tools: Wrenches, socket sets, and screwdrivers are often essential. Always use tools suited to the fitting’s size and type to avoid damage.
- Protective Gear: Personal protective equipment (PPE) is crucial when handling hydraulic systems. This includes safety gloves, goggles, and, in some cases, face shields to protect against sudden fluid discharge.
- Certified Tools: Using tools specifically designed for hydraulic work is important. Non-certified tools may slip or damage components, increasing the risk of leaks or equipment failure.
Preparing for Disassembly
- Shut Down the System: Power down the hydraulic system and release internal pressure. This step is essential to prevent fluid ejection, which can cause injury.
- Clean the Work Area: Keep the workspace clean to prevent dust or debris from entering the system during disassembly. Contaminants can impact performance and lead to costly repairs.
- Use Appropriate Tools: Selecting correct tools (e.g., torque wrenches) ensures proper handling and prevents damage to parts. Incorrect tools can lead to scratches, thread damage, or over-tightening issues.
- Label and Document: Mark and record the position of each connection before disassembly. Proper labeling minimizes reassembly errors and saves time, especially with complex systems.
- Stabilize and Support: Use supports to keep fittings stable, preventing accidental falls or damage to delicate parts.
Key Safety Precautions During Disassembly
- Check Seals: Inspect seals, O-rings, and gaskets during disassembly. Replace any worn or damaged seals to ensure leak-free operation upon reassembly.
- Handle Threads Carefully: Avoid scratching or damaging threads, as they are critical for maintaining strong, secure connections during reassembly.
- Avoid Excessive Force: Apply gentle force when loosening parts. Excessive force or impact methods can damage components and compromise their performance.
Steps for Proper Disassembly of Hydraulic Flange Fittings
- Power Down: Ensure the system is completely off and depressurized.
- Label Parts: Mark connections for easy reassembly.
- Use Correct Tools: Remove bolts and parts using the recommended tools.
- Inspect Components: Check for any damage or wear.
- Store Parts Safely: Place small components in secure storage for reassembly.
Importance of Cleanliness and Contamination Prevention
Hydraulic systems are highly sensitive to contaminants like dust, dirt, and debris. Keeping the system clean during disassembly is essential:
- Preventing Contamination: Immediately cover open lines and ports with clean, lint-free caps or plugs. This prevents dust or other contaminants from entering the system.
- Using Clean Tools and Surfaces: Ensure that tools, workspaces, and hands are clean to avoid introducing particles that can damage sensitive components.
- Maintaining Cleanliness in the Disassembled Parts: Place removed components on a clean, dry surface and cover them with a clean cloth to prevent contamination.
Contamination can lead to component wear, decreased performance, and costly repairs, so attention to cleanliness is critical.
Inspecting Parts for Damage and Wear
After disassembling the hydraulic flange fitting, it’s essential to inspect all parts for signs of damage or wear:
- Checking Seals and Gaskets: Examine seals, O-rings, and gaskets for cracks, warping, or degradation. Damaged seals should be replaced immediately, as they are critical for maintaining a leak-free system.
- Inspecting Flanges for Corrosion or Misalignment: Hydraulic flanges may experience corrosion over time, especially if they operate in harsh environments. Look for rust, pitting, or any alignment issues that may affect the system’s performance.
- Assessing Bolts and Fittings: Ensure that bolts and fittings are in good condition. Replace any bolts that show signs of wear or corrosion to prevent future failures.
Careful inspection helps identify potential issues early, ensuring that the hydraulic system operates efficiently after reassembly.
Safe Disposal of Hydraulic Fluid and Components
Proper disposal of hydraulic fluid and components is essential for both safety and environmental protection:
- Dispose of Hydraulic Fluid According to Regulations: Follow local regulations to dispose of used hydraulic fluid properly. Many fluids contain additives that can be harmful if not handled properly, so take them to a designated waste disposal facility.
- Handle Damaged Components Safely: Dispose of or recycle damaged parts, such as worn seals or corroded bolts, following environmental safety guidelines. Avoid discarding them in regular trash, as they may contain contaminants.
- Environmental Safety Precautions: Spills can have negative environmental impacts. Use spill containment solutions if any fluid accidentally leaks, and clean up immediately using appropriate absorbent materials.
Reassembly Precautions After Disassembly
Once inspection and maintenance are complete, reassembling the hydraulic flange fitting requires careful attention to detail:
- Ensure Cleanliness of All Components: Cleanliness is critical during reassembly. Wipe down all parts with a lint-free cloth to remove any contaminants that may have gathered during the process.
- Check Alignment and Torque Specifications: Proper alignment of the flange fittings is crucial for maintaining a strong seal. Use torque specifications provided by the manufacturer to tighten bolts evenly, avoiding over-torque that could damage components.
- Conduct Pressure Testing Post-Reassembly: After reassembly, conduct a pressure test to confirm that all seals and connections are secure. This test helps prevent leaks and ensures the system is operating safely before resuming full use.
These reassembly steps are essential for maintaining hydraulic system integrity and avoiding performance issues after disassembly.
Common Mistakes to Avoid When Disassembling Hydraulic Flanges
Avoiding common mistakes during disassembly can help prevent accidents and damage:
- Skipping Pressure Release Steps: Failing to relieve system pressure before starting disassembly is a frequent and dangerous mistake. This can lead to sudden fluid release, posing a serious risk to safety.
- Using Incorrect Tools: Using the wrong tools or makeshift solutions (like pliers in place of a wrench) can damage fittings and lead to leaks. Always use the right tools designed for hydraulic components.
- Ignoring Manufacturer Guidelines: Manufacturer guidelines offer specific instructions for handling hydraulic flange fittings. Disregarding these guidelines can compromise system safety and lead to damage.
By understanding these common errors and how to avoid them, you can improve safety and reduce the risk of costly repairs.
Maintenance Tips to Extend the Life of Hydraulic Flange Fittings
Proper maintenance can significantly extend the life of hydraulic flange fittings, reducing the need for frequent repairs:
- Regular Inspections: Perform routine checks on flange fittings, looking for signs of wear, corrosion, or leaks. Address any issues immediately to prevent further damage.
- Maintain Tightness and Seal Integrity: Ensure bolts are correctly torqued, and check seals regularly to prevent fluid leaks. Loose connections or worn seals can lead to reduced efficiency and safety risks.
- Keep Components Clean: Dirt and debris can accelerate wear on hydraulic components. Cleaning both the fittings and surrounding areas helps maintain performance and prevent contamination.
By integrating these practices into your maintenance routine, you can improve system reliability and reduce downtime.
Conclusion
Disassembling hydraulic flange fittings requires careful planning, the right tools, and strict adherence to safety protocols. By understanding the risks, using the correct techniques, and maintaining cleanliness, you can safely disassemble, inspect, and reassemble hydraulic flange fittings without compromising system performance. Regular maintenance and attention to detail will help keep hydraulic systems running smoothly and reduce the likelihood of unexpected issues.
FAQs
- Why is it important to depressurize a hydraulic system before disassembly?
Depressurizing prevents high-pressure fluid ejection, which can cause serious injuries or damage components. - What tools are essential for disassembling hydraulic flange fittings?
Key tools include torque wrenches, seal removal tools, and PPE to ensure safe and proper handling. - How often should hydraulic flange fittings be disassembled for maintenance?
Frequency varies but should be based on maintenance schedules or if leaks and performance issues are detected. - What are best practices for cleaning hydraulic flange fittings?
Clean with lint-free cloths, and maintain a debris-free workspace to prevent contaminants from entering sensitive areas. - Can damaged seals be reused in hydraulic flange fittings?
No, damaged seals should be replaced to maintain a leak-free connection and system performance. - How should hydraulic fluid be disposed of after disassembly?
Follow local environmental regulations for hazardous waste disposal to ensure safe and responsible handling.