When it comes to fluid power systems, hydraulic hoses and fittings play a critical role in keeping machinery running smoothly. These components are essential in a range of industries, from agriculture and construction to manufacturing and aerospace. Hydraulic systems rely on pressurized fluid to transmit force, and the hoses and fittings are the highways that make that force transfer possible. But what exactly are hydraulic hoses and fittings? And why are they so important? How to troubleshooting hydraulic hose and fitting problems?
What Are Hydraulic Hoses?
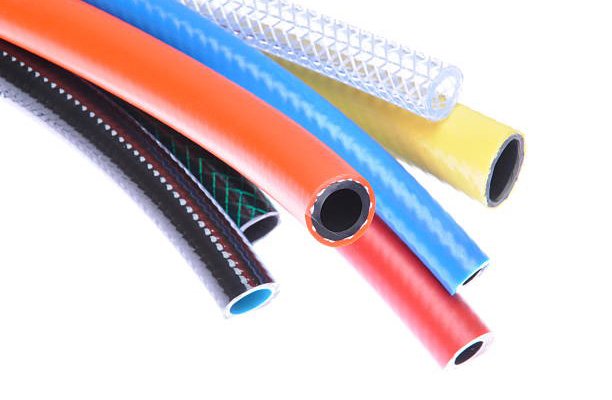
Hydraulic hoses carry pressurized fluid within a hydraulic system. They withstand high pressure and work with other components like pumps, cylinders, and valves to transmit power. Manufacturers typically make them from synthetic rubber or thermoplastic, reinforcing them with layers of steel, textile, or braided wire to increase strength and pressure resistance.
In short, hydraulic hoses are like the arteries of a hydraulic system—without them, the fluid would have nowhere to flow.
Key Features of Hydraulic Hoses:
- Durability: Built to last under extreme conditions.
- Flexibility: Can bend and twist to fit various system configurations.
- Pressure Resistance: Designed to handle high-pressure fluids.
- Temperature Range: Can withstand both hot and cold temperatures, depending on the material.
Types of Hydraulic Hoses
Hydraulic hoses come in several types, each suited for different applications. The primary difference among them lies in the material construction and pressure ratings. Let’s explore some of the most common types:
- Wire Braided Hydraulic Hoses
Reinforced with braided steel wire, these hoses are extremely durable and can handle high-pressure applications. They are commonly used in industries such as construction, mining, and agriculture. - Spiral Hydraulic Hoses
Spiral hoses are reinforced with multiple layers of steel wire arranged in a spiral configuration. These hoses are ideal for systems that require high flexibility and extreme pressure resistance, such as those found in heavy machinery. - Thermoplastic Hydraulic Hoses
Manufacturers make these hoses from thermoplastic materials, making them lighter and more flexible than traditional rubber hoses. They often use them in applications with limited space or where the hose must resist chemicals, abrasion, and high temperatures. - Rubber Hydraulic Hoses
Rubber hoses are the most common type and serve a wide range of applications. They are flexible and come in various pressure ratings, making them suitable for general-purpose hydraulic systems.
What Are Hydraulic Fittings?
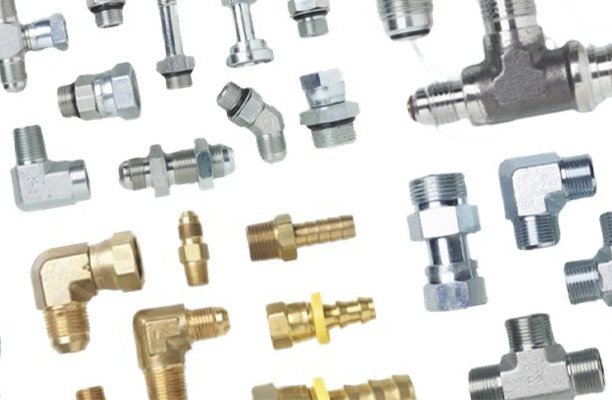
Hydraulic fittings connect hydraulic hoses to other parts of a hydraulic system, such as pumps, cylinders, valves, and tanks. These fittings provide a leak-proof seal and handle high-pressure fluids safely and efficiently. Customers select fittings based on the system’s specific requirements, choosing from various shapes, sizes, and materials.
Common types of hydraulic fittings include elbows, tees, nipples, couplings, and adapters. These fittings allow you to change the direction of fluid flow, connect multiple lines, or attach hoses to various components.
Key Features of Hydraulic Fittings:
- Leak Prevention: They ensure a tight seal, preventing fluid leakage.
- Variety of Configurations: Available in many shapes to accommodate different system needs.
- Corrosion Resistance: Many are made from stainless steel or other corrosion-resistant materials.
- Ease of Installation: Can be easily installed or replaced as needed.
Types of Hydraulic Fittings
As mentioned earlier, hydraulic fittings are the connectors that keep the system intact. But with so many different configurations, it can be tricky to know which fitting to choose. Below are some of the most common types of hydraulic fittings:
- JIC (Joint Industrial Council)
JIC fittings, commonly used in the United States, feature a 37-degree flare. They are designed for high-pressure applications and provide reliable, leak-proof connections. - NPT (National Pipe Thread)
NPT fittings have a tapered thread that creates a tight seal when connected. - BSP (British Standard Pipe)
BSP fittings are the equivalent of NPT fittings in the UK and other parts of the world. They feature both parallel and tapered threads and are commonly used in hydraulic systems outside North America. - ORFS (O-Ring Face Seal)
ORFS fittings use an O-ring to create a seal on the face of the fitting, making them ideal for preventing leaks in high-pressure hydraulic systems. These fittings are primarily used in low-pressure applications but are versatile enough for various industries. - Push-On Fittings
These fittings are designed to push onto the hose without requiring tools, as the name suggests. They’re simple to use and commonly found in applications that don’t require high-pressure ratings.
Why Are Hydraulic Hoses and Fittings So Important?
You can think of hydraulic hoses and fittings as the lifeblood of hydraulic systems. They are the components that make everything work, ensuring that the system operates efficiently and safely. Without them, fluid power would be impossible to achieve. Here’s a deeper look at why they’re indispensable:
- Power Transmission
Hydraulic systems rely on high-pressure fluids to transmit power. Hoses and fittings create the pathway that allows fluid to flow through the system, effectively transmitting force to perform a variety of tasks, from lifting heavy objects to powering machines. - Safety and Leak Prevention
Hydraulic systems operate under high pressure, which can pose serious safety risks if hoses or fittings fail. A broken hose or loose fitting can result in fluid leaks that might damage machinery, cause hazardous spills, or even lead to accidents. This makes leak-proof, durable hoses and fittings essential to safe operation. - Cost Efficiency
Choosing the right hoses and fittings—and maintaining them—helps avoid costly repairs or replacements. A well-maintained system can run for years, reducing the risk of unexpected downtime and ensuring that your machinery operates at optimal efficiency. - Performance Optimization
Well-matched hoses and fittings ensure that fluid flow remains uninterrupted, which directly impacts the efficiency and performance of the system. Systems that rely on hydraulic power often handle demanding tasks, and any compromise in fluid flow or pressure can affect productivity and system longevity.
Troubleshooting Hydraulic Hose and Fitting Problems
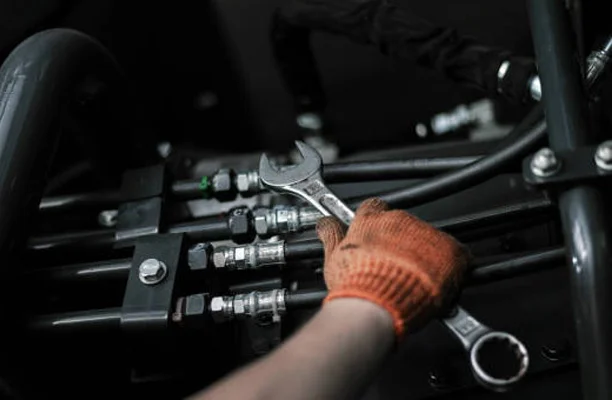
Even the most well-maintained hydraulic system can face problems from time to time. The good news is that you can diagnose and resolve many hydraulic hose and fitting issues with some troubleshooting knowledge. Let’s explore common problems and how to address them to keep your system running smoothly.
1. Leaking Fluid
Problem:
A fluid leak is one of the most common issues in hydraulic systems. Leaks can occur at the hose or fitting connections and can range from small drips to full-blown spills. This not only wastes hydraulic fluid but can also lead to system pressure loss, decreased efficiency, and even environmental hazards.
Possible Causes:
- Loose fittings: Over time, fittings can loosen due to vibration or changes in pressure, leading to leaks.
- Damaged hoses: Cracks, abrasions, or punctures in the hose can cause fluid to leak out.
- Worn-out seals: O-rings or seals in the fittings might degrade or get damaged, preventing a proper seal and causing leakage.
Solution:
- Tighten fittings: If you notice a leak, check all connections and tighten the fittings using the appropriate tools. Make sure they are torqued to the manufacturer’s specifications.
- Replace damaged hoses: Inspect the hose for visible damage like cracks, cuts, or bulges. If you find any, replace the hose to avoid further issues.
- Replace seals: If the seals or O-rings are worn, replace them immediately to restore a tight seal.
2. Hose Kinking or Cracking
Problem:
A kinked or cracked hose restricts fluid flow, making the system work harder and potentially causing complete failure if not addressed. Kinks occur when the hose bends too sharply, while cracks develop over time due to excessive wear, high pressure, or exposure to harsh environments.
Possible Causes:
- Improper installation: If the hose is routed too sharply or exposed to excessive bending, it can kink.
- Aging hoses: Over time, hoses naturally degrade due to constant pressure and exposure to environmental factors.
- Excessive pressure: If the hydraulic system is over-pressurized, the hose can crack or burst.
Solution:
- Inspect routing: Ensure the hose is installed with a proper bend radius and isn’t subjected to sharp angles that could cause kinks.
- Replace damaged hoses: Cracked hoses can’t be repaired effectively, so they should be replaced as soon as possible.
- Check system pressure: Monitor the system pressure to ensure it is within the recommended range. Overpressurization can lead to hose failure, so adjusting the pressure relief valve may be necessary.
3. Loss of Pressure or Power
Problem:
A drop in system pressure or reduced performance can indicate an issue with the hydraulic hose or fittings. When pressure drops, it means the hydraulic system isn’t operating at full capacity, which can lead to inefficient machinery operation, reduced lifting capabilities, or even complete system failure.
Possible Causes:
- Internal hose damage: If the internal lining of the hose is damaged, it could create restrictions or blockages, reducing pressure.
- Clogged or blocked fittings: Dirt, debris, or even aging seals can cause fittings to clog, preventing proper fluid flow.
- Leaks: Even small leaks can cause a noticeable loss of pressure, especially in high-pressure systems.
Solution:
- Inspect hoses for blockages: Inspect the inside of hoses for signs of damage or blockage. If a hose is clogged, replace it.
- Check fittings for debris: Ensure that fittings are clean and free of debris. If you find any contamination, clean or replace the fittings.
- Perform pressure checks: Test the pressure levels in the system to ensure they match the manufacturer’s recommended settings. If the pressure is low, check for leaks, and verify that the hydraulic pump is working efficiently.
4. Excessive Vibration or Noise
Problem:
Excessive vibration or noise in a hydraulic system can be a sign that something is wrong with the hose or fittings. These issues can often lead to increased wear and tear, damaging components and causing premature failure.
Possible Causes:
- Loose fittings: If fittings are not securely tightened, they can cause a rattling noise or vibrations as the fluid flows through the system.
- Air in the system: Air trapped in the hydraulic fluid can cause erratic flow, resulting in noise and vibration. This can occur due to poor sealing or an improperly bled system.
- Incompatible components: Using the wrong type or size of hoses and fittings for the system can lead to improper fluid flow and increased noise.
Solution:
- Tighten all fittings: Ensure that all connections are tightly secured to prevent vibrations and rattling.
- Check for air in the system: Bleed the system to remove trapped air and restore smooth operation. This is especially important after system maintenance or hose replacements.
- Verify hose compatibility: Double-check that all hoses and fittings match the system’s specifications and are capable of handling the required fluid flow and pressure.
5. Hose Wear Due to Abrasion
Problem:
Over time, abrasion can wear down the outer layer of the hose, weakening it and making it more susceptible to rupture or failure. Abrasion often occurs when the hose rubs against surfaces such as machinery, sharp edges, or other components.
Possible Causes:
- Improper routing: If the hose is rubbing against sharp edges or moving parts, it can quickly wear down.
- Environmental factors: Exposure to harsh weather, UV rays, and chemicals can also lead to increased wear on the hose material.
- Lack of protective coverings: Hoses that are not fitted with protective covers or sleeves are more vulnerable to abrasion.
Solution:
- Check routing and protect the hose: Ensure hoses are properly routed and do not rub against sharp edges or components. Install protective covers or sleeves to shield hoses from abrasion.
- Replace worn hoses: If the outer layer of the hose is significantly worn, it’s time to replace the hose. Continuing to use an abraded hose could lead to catastrophic failure.
6. Overheating of the Hydraulic System
Problem:
An overheated hydraulic system can cause oil to break down, leading to sludge build-up, reduced lubrication, and potential damage to hoses, seals, and fittings. Overheating can also cause system components to expand, which could result in leaks or ruptures.
Possible Causes:
- Excessive pressure: If the system is over-pressurized, it can generate excessive heat.
- Blocked filters: Dirty or clogged filters restrict the flow of fluid, leading to overheating as the pump works harder to circulate fluid.
- Insufficient fluid: Running a hydraulic system with low fluid levels can increase friction and cause the system to overheat.
Solution:
- Check system pressure: Ensure the system is operating within the specified pressure range. If it’s too high, adjust the pressure relief valve.
- Clean or replace filters: Regularly clean or replace the filters to ensure proper fluid circulation and prevent overheating.
- Maintain fluid levels: Regularly check fluid levels and top them up as necessary. Be sure to use the recommended type of fluid for your system.
Conclusion
Troubleshooting hydraulic hose and fitting problems may seem overwhelming at first, but with knowledge and careful inspection, you can quickly identify and resolve many issues. Regular maintenance, proper installation, and careful monitoring of the system’s pressure and performance can go a long way in preventing major problems down the road.
A preventative approach—addressing small issues before they grow into big problems—is always better than waiting for a system failure. By staying proactive and keeping a close eye on your hydraulic hoses and fittings, you can maximize the lifespan of your system and maintain its reliability.
FAQs
Q1: How often should I replace hydraulic hoses and fittings?
Regular inspections should be done every 6 months or more frequently in harsh environments. Replace them if you notice cracks, abrasions, or leaks.
Q2: Can I use any hydraulic hose with any system?
No, you must select hoses and fittings that are compatible with the pressure, temperature, and fluid type of your specific system.
Q3: What’s the difference between hydraulic and industrial hoses?
Hydraulic hoses handle high-pressure applications, while industrial hoses serve low-pressure applications, such as air or water systems.
Q4: How can I prevent hydraulic hoses from leaking?
To prevent leaks, regularly check the tightness of the fittings and inspect hoses for any signs of damage. Replacing worn seals and ensuring proper installation can also help avoid leaks.
Q5: Why does my hydraulic hose keep bursting?
Excessive pressure or wear and tear usually cause a burst hose. Ensure the system pressure stays within the manufacturer’s recommended limits, and regularly inspect hoses for cracks or weak spots.
Q6: How often should I replace hydraulic hoses?
Replace hydraulic hoses when they show visible signs of wear, such as cracks, bulges, or leaks. Conduct regular inspections every 6 months to identify when a replacement is needed before serious damage occurs.