1. Introduction
Swage fittings are critical components used in various industries, including aerospace, marine, and construction. These fittings provide strong and reliable connections between cables, pipes, or hoses, ensuring durability and high performance in demanding applications.
Whether used in hydraulic systems, rigging applications, or industrial setups, swage fittings offer numerous advantages, such as resistance to corrosion, enhanced load-bearing capacity, and ease of installation. In this guide, we’ll explore everything you need to know about swage fittings, their types, uses, and installation best practices.
2. Understanding Swage Fittings
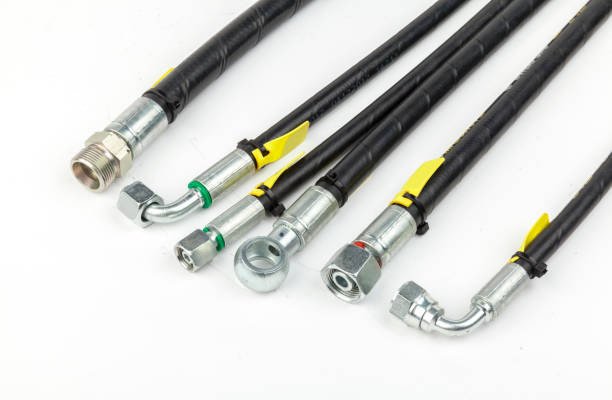
A swage fitting is a mechanical connector used to secure a cable or hose by compressing or deforming the fitting around the material, thereby creating a permanent and secure joint. Additionally, these fittings are commonly made from stainless steel, aluminum, brass, or other high-strength materials to withstand extreme conditions.
Unlike traditional fittings that rely on welding or threading, swage fittings use a swaging process, which involves mechanically crimping or compressing the fitting onto the cable or pipe. This method ensures a tight and leak-proof seal, making them ideal for high-pressure applications.
Key Features of Swage Fittings
- Durability: Designed to withstand high pressure and stress.
- Corrosion Resistance: Ideal for marine and industrial applications.
- Ease of Installation: Quick and secure swaging process.
- Versatility: Used in aerospace, construction, and automotive industries.
3. Types of Swage Fittings
Swage fittings come in various types, each designed for specific applications. Therefore, choosing the right type ensures optimal performance and safety.
Permanent Swage Fittings
These fittings are designed for long-term use and require specialized swaging tools for installation. Once swaged, they cannot be removed or adjusted; therefore, they provide a highly secure connection.
Reusable Swage Fittings
Unlike permanent fittings, reusable swage fittings can be removed and reinstalled. They are ideal for applications where flexibility and maintenance are required.
Threaded Swage Fittings
These fittings combine swaging with threading, which allows for easy attachment to threaded components. As a result, they are commonly used in industrial piping systems.
Hydraulic Swage Fittings
These fittings ensure leak-proof performance in demanding environments such as aerospace and heavy machinery, making them ideal for high-pressure hydraulic systems.
4. Applications of Swage Fittings
Swage fittings are widely used across multiple industries due to their strength, durability, and ability to form secure connections. Below are some of the most common applications:
Aerospace and Aviation
The aerospace industry relies on swage fittings for aircraft control systems, hydraulic lines, and structural cable assemblies. Because of their high strength and lightweight materials, they are ideal for aerospace applications.
Marine and Shipbuilding
In the marine industry, swage fittings play a crucial role in rigging, mooring, and securing components. Stainless steel swage fittings are particularly popular due to their resistance to corrosion caused by saltwater exposure.
Automotive Industry
Swage fittings are used in automotive brake lines, fuel systems, and power steering hoses. Due to their ability to withstand high pressure, they are an excellent choice for critical automotive components.
Industrial and Construction Projects
Heavy machinery, cranes, and suspension systems in construction rely on swage fittings to ensure stability and secure connections. These fittings are commonly used in tension cable structures, such as bridges and stadium roofs.
Military and Defense Applications
Swage fittings are used in military vehicles, aircraft, and equipment where reliable and high-strength connections are necessary. Moreover, their durability makes them well-suited for extreme environments.
5. How Swage Fittings Work
The swaging process involves compressing or crimping a fitting onto a cable, hose, or pipe to create a strong, leak-proof connection. As a result, this method ensures the integrity of the assembly, even under high pressure and load conditions.
The Swaging Process Explained
1. Material Preparation: The cable or hose is cut to the required length.
2. Insertion: The swage fitting is placed over the cable or hose.
3. Compression: Using a swaging tool or machine, pressure is applied to deform the fitting around the material.
4. Final Inspection: The connection is tested for strength and leakage.
Crimping vs. Swaging: Key Differences
- Crimping: Uses a pre-manufactured sleeve that is squeezed onto the cable.
- Swaging: Mechanically deforms the fitting onto the cable for a permanent bond.
Factors Affecting Installation and Durability
- Material Quality: Using high-grade stainless steel or aluminum improves longevity.
- Swaging Pressure: Proper pressure ensures a secure fit.
- Environmental Conditions: Exposure to extreme temperatures and chemicals may affect performance.
6. Advantages of Using Swage Fittings
Swage fittings offer numerous benefits compared to other types of connectors. Here’s why they are a preferred choice in many industries:
Strength and Reliability
Swage fittings create a permanent connection that can withstand high loads and pressures; therefore, they are ideal for critical applications.
Corrosion Resistance
Many swage fittings are made from stainless steel or other corrosion-resistant materials; therefore, they are perfect for marine, chemical, and outdoor applications.
Cost-Effectiveness in Long-Term Use
Despite their initial cost, swage fittings provide long-term value due to their durability, reducing the need for frequent replacements.
Flexibility and Customization Options
Swage fittings come in various sizes and materials, allowing users to customize their connections based on specific project requirements. As a result, they offer flexibility and adaptability for a wide range of applications.
7. Choosing the Right Swage Fittings
Selecting the correct swage fitting is essential for ensuring safety, durability, and optimal performance. Therefore, here are key factors to consider:
Material Selection
- Stainless Steel: Ideal for marine, aerospace, and corrosive environments.
- Aluminum: Lightweight and commonly used in aviation and automotive industries.
- Brass: Used for plumbing and lower-pressure applications due to its resistance to corrosion.
Size and Compatibility
Ensure the fitting matches the cable, hose, or pipe diameter; otherwise, using an incorrectly sized fitting can lead to leaks, inefficiencies, or even failure under pressure.
Pressure Rating
Verify the maximum operating pressure of the swage fitting to ensure it meets the load requirements of your application. This is especially crucial for hydraulic and high-pressure systems.
Environmental Factors
Take into account temperature extremes, chemical exposure, and moisture levels. Additionally, some materials and coatings offer superior durability in harsh environments.
Supplier Reputation
Always choose reputable manufacturers that meet industry standards like ISO, ANSI, or MIL-SPEC certifications to ensure product reliability.
8. Installation & Maintenance of Swage Fittings
Proper installation and maintenance are crucial for long-lasting and leak-proof swage fittings.
Step-by-Step Installation Guide
- Measure & Cut: Use a precise cutter to ensure clean cable or hose edges.
- Insert the Fitting: Slide the swage fitting onto the material.
- Apply Swaging Pressure: Use a hydraulic or manual swaging tool to compress the fitting.
- Check the Connection: Inspect for a uniform and secure fit.
- Leak & Strength Test: Perform a pressure or pull test to verify the integrity of the swaged connection.
Common Installation Mistakes to Avoid
- Under or Over Swaging: Applying incorrect pressure can lead to weak or brittle connections.
- Using Mismatched Components: Ensure the fitting and material are compatible in size and material.
- Poor Cutting Techniques: Frayed cable ends can weaken the swaged joint.
Maintenance Best Practices
- Regularly inspect fittings for corrosion, cracks, or wear.
- Keep swage fittings clean and free from debris.
- Apply anti-corrosion coatings if used in harsh environments.
- Replace fittings if there are visible signs of damage or wear.
9. Swage Fittings vs. Traditional Fittings
Understanding the key differences between swage fittings and traditional fittings helps in making the right choice for specific applications.
Key Differences
Feature | Swage Fittings | Traditional Fittings |
---|---|---|
Installation Method | Requires swaging tools for permanent compression | Threaded, welded, or clamped |
Strength & Durability | High-strength, resistant to loosening | May loosen over time |
Leak Prevention | Leak-proof when installed correctly | Prone to leaks if not properly sealed |
Application | Common in aerospace, marine, and high-pressure systems | Used in plumbing, low-pressure, and non-permanent applications |
Cost Comparison
- Swage fittings: Higher upfront cost but long-term savings due to durability.
- Traditional fittings: Lower initial cost but may require frequent maintenance.
Best Use Cases
- Choose Swage Fittings: For aerospace, marine, and high-pressure applications.
- Choose Traditional Fittings: For temporary or low-pressure connections.
10. Safety Considerations & Industry Standards
Ensuring **proper safety measures and compliance with industry standards** is crucial when using swage fittings. Here are key safety guidelines:
Key Safety Precautions
- Proper Installation: Always follow the manufacturer’s installation guidelines to avoid fitting failure.
- Use the Right Tools: Ensure you use the correct swaging tools to apply proper compression force.
- Inspect Regularly: Conduct routine inspections to identify wear, corrosion, or damage.
- Do Not Overload: Ensure the swage fitting is used within its rated load capacity.
Industry Standards and Certifications
Swage fittings must meet specific industry standards to ensure safety and reliability:
- ANSI (American National Standards Institute): Sets standards for quality and safety.
- ISO (International Organization for Standardization): Global certification for manufacturing and material quality.
- SAE (Society of Automotive Engineers): Common for automotive and aerospace applications.
- MIL-SPEC (Military Specifications): Required for defense and military applications.
11. Common Issues & Troubleshooting
Swage fittings are highly reliable, but improper installation or material wear can lead to issues. Here’s how to troubleshoot common problems:
Leaks in the Fitting
Causes:
- Insufficient swaging pressure
- Incorrect fitting size
- Damaged hose or cable
Solution: Re-swage the fitting with the correct pressure or replace it if damage is visible.
Fitting Slippage
Causes:
- Improper compression
- Using a worn-out swaging tool
- Incorrect material selection
Solution: Reinstall the fitting with the correct tool and inspect the material for compatibility.
Corrosion or Material Degradation
Causes:
- Exposure to moisture and chemicals
- Using non-corrosion-resistant materials
Solution: Use **stainless steel fittings** for high-moisture environments and apply protective coatings when necessary.
12. Top Manufacturers & Brands of Swage Fittings
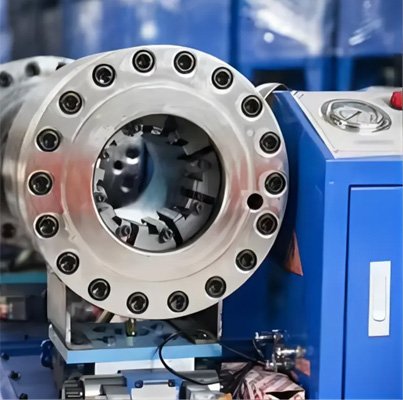
Choosing a reliable manufacturer ensures high-quality swage fittings for industrial applications. Therefore, below are some of the leading brands:
Leading Global Manufacturers
Best Brands for Different Industries
- Parker Hannifin: Specializes in hydraulic and industrial swage fittings.
- Swagelok: Known for high-pressure and precision-engineered fittings.
- Hydrasearch: Preferred for military and marine applications.
- Taske: Offers customizable swage fittings for industrial use.
- Aerospace: Eaton Aerospace, Boeing Approved Fittings
- Automotive: Aeroquip, Goodridge Performance Fittings
- Marine: Blue Wave Rigging, Sta-Lok
- Construction: Crosby, Green Pin
Price and Quality Comparison
- High-End (Premium Quality): Swagelok, Parker Hannifin
- Mid-Range (Balanced Performance & Cost): Eaton, Aeroquip
- Budget-Friendly (Cost-Effective Solutions): Generic industrial brands, imported fittings
13. Buying Guide: Where to Purchase Swage Fittings?
Whether you need swage fittings for industrial, automotive, or marine applications, choosing the right supplier is crucial. Below are the best places to buy swage fittings:
Online vs. Offline Stores
- Online Stores: Websites like Grainger, and Amazon Industrialoffer convenience and bulk purchase options.
- Offline Stores: Local hydraulic and industrial supply storesprovide expert recommendations and immediate availability.
How to Verify Quality Before Purchasing
- Check for industry certifications (ISO, ANSI, MIL-SPEC).
- Review **customer feedback and supplier reputation**.
- Ensure fittings are **made from corrosion-resistant materials** if used in harsh environments.
Bulk Buying Options for Businesses
- Many manufacturers offer bulk discounts for industrial buyers. like Taske.
- Custom fabrication services are available for large-scale projects.
Conclusion
Swage fittings are widely used across industries for secure and leak-proof connections. They play a key role in aerospace, automotive, and marine applications, ensuring durable assemblies.
Understanding the types, applications, and installation methods of swage fittings helps in selecting the right product. Moreover, factors like material, pressure rating, and environmental conditions significantly influence their lifespan and performance.
Advancements in technology continue to improve swage fittings, making them stronger, more efficient, and eco-friendly. Consequently, choosing high-quality, industry-certified fittings enhances safety and reliability in every application.
FAQs
1. Difference Between Swage Fittings and Crimp Fittings
Swage fittings use a mechanical deformation process to permanently compress the fitting onto a cable or hose, ensuring a strong, leak-proof connection. Crimp fittings, on the other hand, rely on pre-manufactured sleeves that are squeezed around the material, which may not be as durable as swaged connections.
2. Reusability of Swage Fittings
It depends on the type. Manufacturers design permanent swage fittings for one-time use, while they engineer reusable swage fittings for multiple removals and reinstallations. If a system requires frequent maintenance or adjustments, reusable fittings provide a better choice.
3. Tools Required for Swage Fittings Installation
Swage fittings require swaging tools such as:
- Manual or hydraulic swage presses
- Swaging dies matched to the fitting size
- Cutting tools for clean cable or hose preparation
Proper tools ensure secure and uniform swaging.
4. Suitability for High-Pressure Applications
Swage fittings are widely used in hydraulic, aerospace, and industrial applications where high-pressure resistance is required. Therefore, always check the pressure rating of the fitting to ensure compatibility with your system.
5. Preventing Corrosion in Swage Fittings
To prevent corrosion:
- Use stainless steel or coated materials for marine and outdoor applications.
- Apply anti-corrosion treatments if used in harsh environments.
- Conduct regular maintenance and inspections to detect early signs of wear.