1. Introduction
Hydraulic systems play a critical role in many industrial and mechanical processes, leveraging fluid pressure to power machinery. Central to these systems is the hydraulic adapter, an essential component that ensures smooth and secure connections between hydraulic hoses, pipes, and other system parts. These adapters are designed to manage the complex flow of liquids and gases under pressure, enabling efficient operation and preventing leaks or malfunctions.
In this blog, we will dive deep into what hydraulic adapters are, how they function, their different types, materials, and common applications. Whether you are an engineer, technician, or enthusiast, understanding hydraulic adapters will help you better appreciate their vital role in hydraulic systems.
2. Understanding Hydraulic Adapters
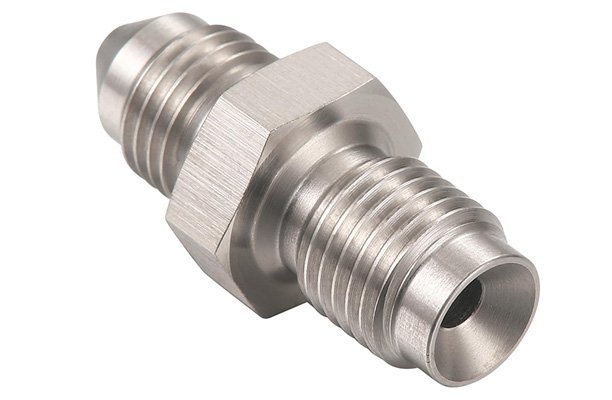
A hydraulic adapter is a mechanical fitting used to connect various hydraulic components within a system, such as hoses, pipes, and valves. It ensures that different parts of a hydraulic circuit are securely linked, enabling the transfer of fluid under pressure from one component to another. Without adapters, there would be no reliable way to create these connections, leading to inefficiencies and potential failures in fluid transfer.
Hydraulic adapters come in a variety of designs; therefore, they can be used for straight connections, angled connections, or even branching connections. Furthermore, they are essential for maintaining the integrity of hydraulic circuits by preventing leaks and withstanding the high pressures commonly found in industrial applications.
3. How Hydraulic Adapters Work
Hydraulic adapters function by creating a secure connection between two hydraulic components. Consequently, they ensure that a hose or pipe firmly attaches to a port, valve, or pump, enabling a continuous flow of hydraulic fluid. Moreover, they are designed to handle high-pressure fluids, making them both durable and resistant to wear and tear.
The primary role of a hydraulic adapter is to prevent leakage, which could lead to system failure or safety hazards. Adapters achieve this by using compression seals, O-rings, or other sealing mechanisms that ensure tight connections. The design of the adapter also ensures that it can handle the specific pressure and temperature ranges of the hydraulic system it is part of.
Moreover, hydraulic adapters help in reducing the risk of contamination by keeping the hydraulic fluid contained and sealed. Hydraulic adapters are especially crucial when different parts of the system aren’t compatible, such as when different thread types or pipe sizes are involved. In these cases, adapters allow for a proper match, ensuring seamless functionality of the entire hydraulic circuit.
4. Types of Hydraulic Adapters
Hydraulic adapters come in various shapes and configurations to accommodate the unique needs of different hydraulic systems. As a result, they offer versatility in connecting components. Some of the most common types include:
Straight Adapters: These adapters are the most common and simplest form. They connect two components with matching thread types directly. Use them when the alignment between parts is straight and does not require any angular adjustments.
Elbow Adapters: These adapters create a 90-degree angle between two connected parts. They guide fluid flow around obstacles in tight spaces.
Tee Adapters: These adapters split the flow of hydraulic fluid into three directions. They are common in applications where fluid needs to be directed to multiple components.
Cross Adapters: Like tee adapters, cross adapters split fluid into four directions. They offer more flexibility in complex hydraulic circuits.
Bulkhead Adapters: They pass hydraulic fluid through a wall or barrier. They provide a secure, leak-free connection when hoses or pipes need to pass through structural elements like a tank or casing.
5. Materials
The material of a hydraulic adapter is a key factor in determining its durability, pressure resistance, and compatibility with specific hydraulic fluids. Some of the most common materials used include:
Steel: Manufacturers use steel the most for hydraulic adapters due to its strength, durability, and ability to withstand high pressures. It suits a wide range of industrial applications and handles aggressive fluids well.
Brass: Brass hydraulic adapters resist corrosion and perform excellently in both high- and low-pressure systems. They are common in applications where corrosion resistance is crucial, such as in marine environments.
Stainless Steel: Stainless steel adapters resist corrosion; therefore, they are ideal for high-performance, high-temperature, and high-pressure environments. As a result, manufacturers commonly use these adapters in industries such as food processing, pharmaceuticals, and chemicals.
4o
Aluminum: Manufacturers use aluminum adapters because they are lighter, making them ideal for industries where weight is a concern. However, they are generally unsuitable for extremely high-pressure applications.
Plastic: Plastic hydraulic adapters are less common but are used in low-pressure systems or specialized applications, such as certain medical equipment or testing systems.
6. Thread Types in Hydraulic Adapters
The proper selection of thread type is essential for ensuring a secure and leak-free connection in hydraulic systems. Since different industries and regions follow distinct thread standards, it is important to choose the right one for compatibility. Among the most commonly used thread types in hydraulic adapters are:
NPT (National Pipe Thread): NPT is a common threading standard in the United States. It provides a tapered thread that ensures a tight seal when mated with another NPT thread. These adapters work in low- to medium-pressure systems.
BSPP (British Standard Pipe Parallel): BSPP is a parallel thread standard used predominantly in the UK and Europe. It creates a seal using a flat face or O-ring, rather than the thread itself.
BSPT (British Standard Pipe Taper): Similar to NPT, BSPT threads are tapered and work in systems requiring a pressure-tight seal.
JIC (Joint Industry Council): JIC adapters feature a 37-degree flare design and work in applications that require high-pressure resistance. They are common in the automotive and aerospace industries.
ORFS (O-Ring Face Seal): ORFS adapters use an O-ring to provide an extremely reliable seal and prevent leakage. They are highly effective in high-pressure applications and commonly used in heavy-duty machinery.
7. Benefits of Using Hydraulic Adapters
Hydraulic adapters offer numerous benefits that contribute to the efficiency and longevity of hydraulic systems. Some of the key advantages include:
- Leak Prevention: Hydraulic adapters create a tight seal between components, preventing the leakage of fluid, which could cause system inefficiency or safety hazards.
- Pressure Resistance: Designed to withstand high fluid pressures, hydraulic adapters ensure that the system maintains its pressure integrity, even under extreme conditions.
- Corrosion Resistance: Depending on the material, hydraulic adapters can be highly resistant to corrosion, which is crucial in environments exposed to harsh chemicals or weather conditions.
- Versatility: Hydraulic adapters are highly versatile and can connect a wide range of hydraulic components with different sizes, shapes, and thread types, making them indispensable in various industries.
8. Common Applications
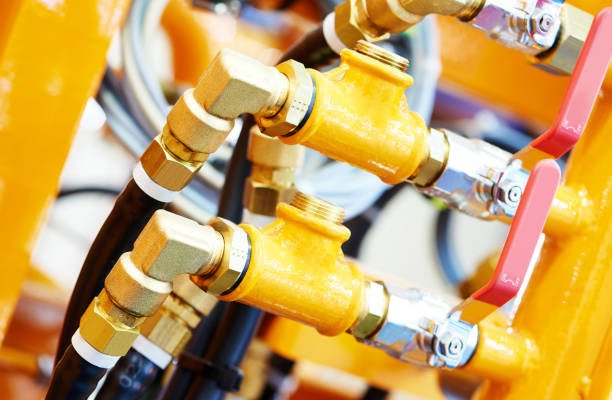
- Automotive Industry: Hydraulic adapters are crucial in automotive applications, especially in brake systems, power steering, and heavy-duty truck systems.
- Construction Machinery: Construction machines like excavators, bulldozers, and cranes rely on hydraulic systems that use adapters for fluid connections.
- Industrial Equipment: Hydraulic systems are used in manufacturing equipment, hydraulic presses, and production lines. Adapters ensure the smooth operation of these machines by connecting various hydraulic components.
- Agriculture and Farming Equipment: Hydraulic systems in farming equipment such as tractors and harvesters depend on hydraulic adapters for fluid power in lifting and operating machinery.
- Aerospace Industry: In aerospace, hydraulic systems are critical for flight controls, landing gear, and actuation systems. High-quality adapters ensure secure, leak-proof connections in these high-pressure environments.
9. Choosing the Right Hydraulic Adapter
Selecting the correct hydraulic adapter is essential for ensuring that your hydraulic system operates effectively and without issue. When choosing an adapter, consider the following factors:
- Material: Choose a material that is compatible with the fluid in the system and can withstand the pressures and temperatures of the application.
- Pressure Rating: Make sure the adapter can handle the maximum pressure of the system. Over-specifying or under-specifying the pressure rating could lead to system failure.
- Compatibility: Ensure the adapter is compatible with the thread types and sizes used in your hydraulic components. Mismatched threads can lead to leaks or damaged connections.
10. Installation and Maintenance Tips
To ensure the longevity and performance of hydraulic adapters, proper installation and maintenance are essential:
- Proper Tightening: Adapters should be tightened according to the manufacturer’s specifications. Over-tightening can damage threads, while under-tightening may result in leaks.
- Avoid Over-Torquing: Excessive torque can lead to damaged seals and threads. Use a torque wrench to ensure proper tightening.
- Check for Leaks: After installation, check for leaks by pressurizing the system and inspecting all connections. Regularly inspect adapters for wear or corrosion.
11. Conclusion
Hydraulic adapters are vital components in any hydraulic system, ensuring smooth fluid transfer and reliable connections between various system parts. Whether you are dealing with high-pressure machinery, automotive applications, or aerospace technology, hydraulic adapters are key to preventing leaks, maintaining pressure, and ensuring the safety and efficiency of hydraulic operations.
By understanding the different types of hydraulic adapters, their materials, and their applications, you can make informed decisions when choosing the right adapters for your system. Remember that proper installation and maintenance are just as important in extending the lifespan and performance of your hydraulic system. Ultimately, hydraulic adapters help create a seamless connection between components, allowing industries worldwide to operate more efficiently and effectively.
12. FAQs
1. What is the difference between hydraulic adapters and hydraulic fittings?
Hydraulic systems use both adapters and fittings to connect components. Adapters modify the size, thread type, or angle of the connection, while fittings establish the actual connection between parts. In other words, adapters ensure compatibility between different components, while fittings create a secure and leak-proof connection.
2. Can hydraulic adapters be used in high-temperature environments?
Hydraulic adapters work in high-temperature environments, but their material plays a crucial role in withstanding extreme temperatures. For high-temperature applications, manufacturers prefer stainless steel or brass due to their durability and heat resistance.
3. How do I choose the right size hydraulic adapter for my system?
Choosing the right size hydraulic adapter depends on the size and thread type of the components you’re connecting. Be sure to measure the diameter and thread pitch of the hoses or pipes and select an adapter that matches these specifications. It is also important to consider the pressure and temperature ratings of both the adapter and the hydraulic components to ensure compatibility.
4. Are there any safety concerns with using hydraulic adapters?
Improperly installed or maintained hydraulic adapters pose safety risks. Incorrectly tightened adapters can cause leaks, leading to system failures or hazardous situations. Always apply the correct torque during installation and regularly inspect adapters for wear or damage.
5. How can I prevent leaks in hydraulic adapters?
Proper installation, correct sealing methods (such as O-rings or compression seals), and high-quality materials prevent leaks in hydraulic adapters. Regular inspections and maintenance of hydraulic adapters also help identify potential issues before they become critical.
6. Can hydraulic adapters be reused?
You can often reuse hydraulic adapters if they remain in good condition without wear, corrosion, or damage. However, always inspect them thoroughly before reuse to ensure a proper, leak-free connection. Replace damaged or worn adapters to maintain system integrity.