Introduction to O-Ring Failures in Hydraulics
Hydraulic systems play a pivotal role in industrial, automotive, and aerospace applications, where power transmission and control depend on high-pressure fluid dynamics. A small component, the O-ring, is critical in maintaining leak-proof seals within these systems. However, O-ring failures are one of the most common causes of hydraulic malfunctions, often leading to performance loss, system downtime, and costly repairs. By understanding the causes and prevention techniques associated with O-ring leakage, operators and engineers can dramatically improve equipment reliability and operational efficiency.
Understanding the Role of O-Rings in Hydraulic Systems
O-rings are torus-shaped elastomeric seals used to prevent the escape of fluid or gas in pressurized systems. Positioned in grooves between metal components, O-rings compress when installed, creating a tight seal that withstands hydraulic pressure. They are ubiquitous across hydraulic cylinders, valves, pumps, and connectors due to their simplicity, cost-effectiveness, and high sealing efficiency.
Common materials used in O-ring manufacturing include:
- Nitrile (Buna-N): Cost-effective and widely used in petroleum-based fluids.
- Viton (FKM): Excellent chemical and temperature resistance.
- EPDM: Suitable for water, steam, and certain chemicals.
- Silicone: Great flexibility and thermal resistance for static applications.
Each material offers distinct advantages, depending on the system’s temperature, pressure, and fluid compatibility.
Most Common Causes of O-Ring Failures
Understanding why O-rings fail is key to preventing leaks. Here are the most frequent causes:
- Improper Installation: Twisting, tearing, or pinching during installation can compromise the seal.
- Material Incompatibility: Using the wrong O-ring compound for the hydraulic fluid or temperature can lead to swelling, cracking, or degradation.
- Excessive Temperature and Pressure: Operating outside the material’s limits causes hardening, extrusion, or permanent deformation.
- Chemical Degradation: Aggressive fluids can break down elastomer bonds, leading to cracking and loss of elasticity.
- Abrasion and Mechanical Damage: Repeated dynamic movement or contamination in the system can wear out O-rings prematurely.
Preventive steps begin with identifying these root causes and tailoring selection and maintenance accordingly.
Signs and Symptoms of O-Ring Failure
Detecting O-ring failure early can help prevent extensive damage to hydraulic systems. Here are some key indicators:
- Visible Leaks: The most obvious sign, often seen as fluid escaping from joints or fittings.
- System Pressure Drops: A loss in hydraulic pressure can signal internal leakage due to a compromised seal.
- Unusual Noises or Vibrations: These may indicate cavitation or pressure instability caused by faulty sealing.
- Increased Maintenance Frequency: Repeated need for top-ups or cleaning can point to slow leaks or seal erosion.
Technicians should be trained to identify these warning signs during regular system checks and inspections.
Consequences of Ignoring O-Ring Leaks
Failing to address O-ring issues can have far-reaching consequences beyond simple maintenance. Key risks include:
- Equipment Downtime: Leaks can lead to a shutdown of operations, resulting in lost productivity and missed deadlines.
- Contamination and Environmental Hazards: Hydraulic fluid leaks can contaminate the environment or compromise product purity in sensitive industries.
- Escalating Repair Costs: Small leaks often evolve into major breakdowns, necessitating costly component replacements and labor.
- Safety Hazards: Slippery floors, fire risks from flammable fluids, and unexpected equipment movements are all potential safety threats.
Proactive attention to small leaks can prevent catastrophic failure and ensure system longevity.
Best Practices for Preventing O-Ring Leaks
Implementing the following best practices can significantly reduce the chances of O-ring failure and leakage:
- Proper O-Ring Selection and Sizing: Ensure compatibility with the system’s operating temperature, pressure, and fluid type.
- Use Compatible Lubricants and Fluids: Select lubricants that do not degrade or swell the elastomer material.
- Regular System Inspection and Maintenance: Periodic checks for signs of wear, chemical attack, or loss of elasticity help detect issues early.
- Correct Installation Techniques: Use specialized tools to avoid twisting, tearing, or misalignment during installation.
These preventive actions, though simple, contribute to enhanced system reliability and reduced long-term costs.
Choosing the Right O-Ring Material for Your Application
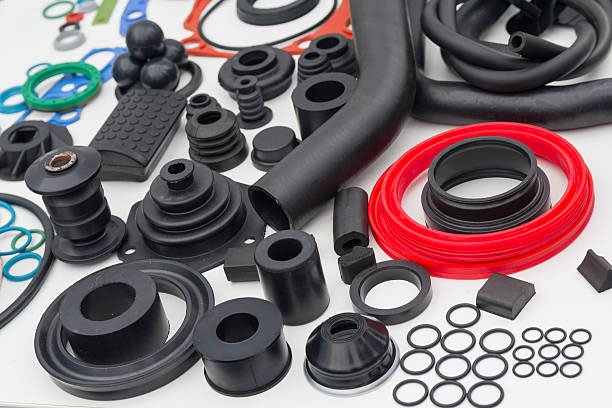
Selecting the correct O-ring material is crucial to ensuring optimal performance and longevity. Each elastomer behaves differently under various operating conditions. Here’s a quick overview of commonly used O-ring materials and their applications:
- Nitrile (Buna-N): Ideal for general-purpose hydraulic fluids and mineral oils. Not suitable for ozone or sunlight exposure.
- Viton (FKM): Excellent for high-temperature and chemically aggressive environments, including fuels and synthetic oils.
- EPDM: Best suited for brake fluids, steam, and water-based systems. Poor compatibility with petroleum oils.
- Silicone: Great for static applications in extreme temperatures but not recommended for dynamic sealing under pressure.
- PTFE (Teflon): High resistance to chemicals and temperature, often used as a backup or in static seals.
Choosing the right material involves assessing pressure, temperature, fluid compatibility, and system dynamics. Always consult manufacturer specifications and industry standards during the selection process.
Installation Tips to Avoid O-Ring Damage
Improper installation remains one of the most preventable causes of O-ring failure. Use these expert tips to ensure damage-free installation:
- Maintain Cleanliness: Keep the sealing surface and O-ring free from dust, dirt, or sharp burrs.
- Apply the Correct Lubricant: Use only compatible lubricants to ease installation and prevent frictional damage.
- Avoid Twisting or Overstretching: Use slow, even pressure to place the O-ring without deformation.
- Use Appropriate Installation Tools: Rely on non-metallic picks, cones, and guides to prevent cuts or nicks during placement.
- Check for Proper Alignment: Ensure the groove and mating parts are correctly aligned before system activation.
Careful attention during installation can significantly extend the service life of the O-ring and reduce maintenance downtime.
Importance of Regular Hydraulic System Maintenance
Preventive maintenance is the cornerstone of a leak-free hydraulic system. Rather than waiting for failures, a well-designed maintenance strategy includes:
- Scheduled Inspections: Conduct routine checks of O-rings, hoses, fittings, and fluid quality.
- Predictive Maintenance Using IoT: Sensors and smart diagnostics help detect early signs of degradation or pressure anomalies.
- Proactive Component Replacement: Replace O-rings and seals based on lifecycle predictions, not just upon failure.
- Fluid Analysis: Regular testing of hydraulic fluid for contamination, viscosity, and compatibility.
Staying ahead of issues not only reduces emergency repairs but also ensures consistent performance and equipment longevity.
Role of OEM Guidelines and Industry Standards
Adhering to OEM (Original Equipment Manufacturer) guidelines and recognized industry standards is essential for ensuring hydraulic system integrity and safety. These standards help engineers and technicians maintain consistency, quality, and compatibility in system design and maintenance.
Key considerations include:
- OEM Specifications: Manufacturers often provide detailed charts for O-ring materials, sizes, and installation methods tailored to their equipment.
- ISO Standards: For instance, ISO 3601 defines global standards for O-ring dimensions, tolerances, and material properties.
- SAE Standards: SAE J200 and other guidelines provide standard classifications and performance ratings for elastomers used in hydraulic systems.
Following these standards ensures that components meet performance expectations, are compatible with system requirements, and reduce the likelihood of failure due to mismatched parts or substandard materials.
How to Diagnose O-Ring Leaks Effectively
Efficient diagnosis of O-ring leaks is critical for timely maintenance and repair. Below are proven methods used by professionals to pinpoint seal failures:
- Pressure Testing: By pressurizing the hydraulic system and monitoring pressure drops, technicians can isolate leaking sections.
- Visual Inspection: Physical examination of seals and joints can reveal wear, cracks, flattening, or misalignment.
- Use of Dye or UV Tracers: Fluorescent dyes can be added to the hydraulic fluid to visually track leaks under UV light.
- Ultrasonic Leak Detectors: These devices pick up the high-frequency sound of escaping gas or fluid under pressure.
- Systematic Troubleshooting: Step-by-step isolation of components helps narrow down the problem without system-wide disassembly.
Regularly training personnel in diagnostic techniques and using the right tools reduces repair time and improves detection accuracy.
Cost-Benefit Analysis: Maintenance vs. Repairs
One of the most compelling reasons to prioritize O-ring health is the financial advantage of preventive maintenance over reactive repairs. Here’s a breakdown:
Preventive Maintenance | Reactive Repair |
---|---|
Lower long-term costs | High unplanned expenses |
Minimal downtime | Extended production loss |
Predictable budgeting | Emergency procurement costs |
Extended equipment lifespan | Potential for premature system failure |
Case studies show that companies implementing structured preventive maintenance programs reduce their repair costs by up to 40% and improve overall operational uptime. Investing in routine care is not just wise—it’s financially sound.
Innovations in O-Ring Technology
As hydraulic systems evolve, so too do the materials and technologies behind O-rings. Recent innovations have greatly improved their reliability and performance under extreme conditions. Key advancements include:
- Self-Lubricating O-Rings: These reduce friction in dynamic applications and extend the service life by minimizing wear.
- High-Performance Elastomers: New formulations resist extreme heat, cold, and aggressive chemicals better than traditional materials.
- Smart Materials: Some O-rings are being integrated with sensors or designed with color-change properties to indicate wear or failure.
- Nano-Engineered Surfaces: Enhanced surface coatings improve resilience against abrasion and fatigue in high-duty cycles.
These innovations offer promising solutions for industries where reliability is critical, such as aerospace, oil and gas, and high-performance manufacturing.
Training and Awareness for Technicians
The best technology is only as effective as the people who install and maintain it. That’s why training and technical awareness are crucial for hydraulic technicians and maintenance teams. Areas of focus should include:
- Proper Installation Techniques: Training ensures O-rings are installed correctly every time, avoiding preventable failures.
- Material Knowledge: Understanding the characteristics and limitations of each elastomer aids in selection and troubleshooting.
- Certification Programs: Certifications from bodies like the International Fluid Power Society (IFPS) validate technician expertise.
- Ongoing Education: Regular workshops and updated manuals help teams stay current with new technologies and standards.
Well-trained personnel not only improve system performance but also reduce operating costs and safety risks through better decision-making and execution.
Conclusion: Strengthening Hydraulic System Reliability
O-ring failures are a small issue with potentially massive consequences. However, with the right approach—starting from material selection and installation, through to routine inspections and adherence to OEM standards—leaks can be effectively minimized or eliminated altogether. By prioritizing preventive maintenance, investing in training, and embracing technological innovations, businesses can ensure the long-term efficiency and safety of their hydraulic systems.
Ultimately, preventing leaks isn’t just about sealing a component—it’s about safeguarding productivity, reducing environmental impact, and maintaining the integrity of your operations.
FAQs
1. What is the lifespan of a typical hydraulic O-ring?
O-ring lifespan varies depending on material, operating conditions, and maintenance, but typically ranges from 2 to 10 years in well-maintained systems.
2. Can I reuse O-rings after disassembly?
It is generally not recommended. Even if they appear intact, reused O-rings may have surface imperfections or have lost elasticity, leading to future leaks.
3. How do I know which O-ring material is best for my system?
Refer to manufacturer guidelines and industry compatibility charts that consider fluid type, pressure, temperature, and system dynamics.
4. Are colored O-rings better for identification?
Yes. Color-coded O-rings help differentiate materials quickly and reduce the risk of installing an incompatible seal in critical applications.
5. What should I do if my system frequently blows O-rings?
Frequent failures may indicate excessive pressure, improper material choice, or flawed installation practices. Perform a system audit and consult a sealing expert.