Introduction
Hydraulic hoses are essential components in a wide range of industrial, agricultural, and mobile equipment systems. They play a critical role in transmitting pressurized hydraulic fluid to actuators, valves, and other components, allowing machinery to function effectively. However, like any mechanical part, hydraulic hoses are subject to wear and degradation over time, making it crucial to understand what impacts hydraulic hose lifespan and how to manage it effectively.
Understanding the factors that affect their lifespan is crucial for maintaining safety, reducing downtime, and minimizing operational costs. This guide explores the key elements that influence the durability of hydraulic hoses and how you can maximize their service life through smart practices and preventive maintenance.
Understanding Hydraulic Hoses
What Are Hydraulic Hoses?
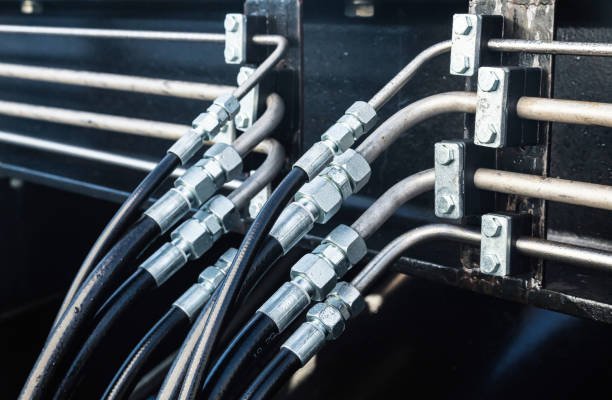
Hydraulic hoses are flexible, high-pressure tubes designed to carry hydraulic fluid between components in a hydraulic system. Typically made from synthetic rubber, thermoplastics, or reinforced materials, these hoses are engineered to withstand substantial pressure and environmental conditions.
Common Applications
Hydraulic hoses are found in a variety of settings including construction machinery, agricultural equipment, industrial presses, aviation systems, and marine vessels. Their flexibility and pressure-handling capabilities make them suitable for both mobile and static applications.
Key Components and Materials
Most hydraulic hoses consist of three main layers: an inner tube that carries the fluid, a reinforcement layer made of braided or spiral-wound wire for strength, and an outer cover that protects against abrasion, weather, and chemicals. The choice of materials affects the hose’s pressure rating, temperature tolerance, and compatibility with various hydraulic fluids.
Average Lifespan of Hydraulic Hoses
Manufacturer Guidelines
Manufacturers typically recommend replacing hydraulic hoses every 1 to 2 years in high-stress environments, and every 3 to 5 years in more controlled settings. These timelines are based on standard usage assumptions and ideal conditions.
Real-World Expectations
In practice, many hydraulic hoses operate well beyond their recommended lifespan — or fail prematurely — depending on how they’re used and maintained. Factors like over-pressurization, improper installation, and exposure to harsh environments can significantly shorten hose life.
Factors That Affect Actual Lifespan
Several variables impact how long a hose will last, including pressure fluctuations, temperature extremes, exposure to contaminants, and the quality of both the hose and the fittings. Understanding and controlling these variables is key to optimizing performance and safety.
Operating Pressure and Temperature
How Pressure Affects Hose Wear
Hydraulic hoses are rated for specific working pressures, and consistently operating near or above these limits can accelerate wear and lead to early failure. Excessive pressure increases the stress on the internal reinforcement layers, weakening the hose structure over time. Pressure surges or spikes are especially harmful, as they can exceed the hose’s burst pressure and cause sudden ruptures.
Temperature Ranges and Their Influence
Extreme temperatures—both high and low—can degrade the materials in hydraulic hoses. High temperatures can soften or harden the rubber, leading to cracks and leaks. Conversely, cold environments can make hoses brittle and inflexible. It’s important to choose hoses rated for the full range of temperatures expected in your operating environment.
The Role of Pressure Spikes
Transient pressure spikes, even if brief, exert intense stress on the hose interior. These spikes often go unnoticed without monitoring tools but can drastically reduce a hose’s service life. Using pressure relief valves and surge protectors can help mitigate their impact and extend hose longevity.
Environmental Conditions
Exposure to UV Light
Prolonged exposure to sunlight and UV radiation can deteriorate the outer cover of hydraulic hoses, especially those made from rubber. UV damage causes cracking, stiffness, and eventually leakage, especially in outdoor or mobile machinery. Protective coverings or routing hoses away from direct sunlight can help.
Effects of Moisture and Corrosion
Water ingress and humidity contribute to internal and external corrosion, particularly if the fittings or reinforcement layers are metal. Corrosion weakens structural integrity and can lead to joint failures. Selecting corrosion-resistant materials and sealing connectors can prevent moisture intrusion.
Impact of Dust, Dirt, and Debris
Contaminants such as dirt and abrasive particles can cause surface wear and penetration, especially in rugged work environments like construction sites. Over time, this leads to abrasions that compromise the outer layer and eventually the reinforcement layer, increasing the risk of failure. Hose sleeves and guards can provide effective protection in such scenarios.
Fluid Compatibility
Choosing the Right Hydraulic Fluid
Each hydraulic hose is designed for specific fluid types. Using incompatible fluids can degrade the inner tube, causing it to swell, crack, or separate from the reinforcement layers. Always match the fluid type with the hose manufacturer’s specifications.
Effects of Using Incompatible Fluids
Incompatibility often leads to chemical reactions that weaken the hose structure. For example, using petroleum-based fluids in hoses designed for phosphate esters can result in swelling and delamination. This not only shortens the lifespan but also increases the risk of sudden failure.
Contaminant Buildup and Blockages
Hydraulic systems are susceptible to internal contamination from degraded fluid, particulates, or microbial growth. These contaminants can block the hose or cause internal abrasion, which reduces efficiency and leads to internal damage. Regular fluid analysis and filtration are crucial for avoiding such issues.
Hose Routing and Installation
Importance of Proper Routing
Incorrect routing is one of the leading causes of premature hose failure. Sharp bends, twists, and kinks create stress points that can weaken hose structure and reduce flow efficiency. Proper routing minimizes mechanical strain and ensures smooth fluid transmission throughout the system.
Common Installation Mistakes
Some frequent errors include over-tightening fittings, using the wrong bend radius, and failing to account for movement or vibration. These mistakes can cause excessive wear at connection points and increase the risk of leaks or bursts. Following manufacturer guidelines and using routing clamps can help avoid these pitfalls.
Vibration and Abrasion Risks
In systems where movement or vibration is common, hydraulic hoses are vulnerable to constant rubbing and chafing. This abrasion slowly erodes the hose exterior, exposing reinforcement layers and compromising safety. Protective wraps, sleeves, and vibration isolators can significantly reduce abrasion damage.
Maintenance Practices
Regular Inspection Schedules
Routine visual inspections are essential to detect early signs of wear such as cracks, bulges, or fluid seepage. Scheduled checks help catch problems before they escalate into failures, especially in high-pressure or mission-critical systems.
Leak Checks and Monitoring
Even small leaks can signal underlying issues and should never be ignored. Monitoring for pressure drops, fluid loss, or visible drips helps maintain operational integrity. Installing sensors and pressure gauges provides real-time monitoring for proactive maintenance.
Importance of Preventive Maintenance
Preventive maintenance extends the life of hydraulic hoses and reduces downtime. This includes cleaning, replacing aged hoses before failure, ensuring proper torque on fittings, and regularly updating fluid. A proactive approach minimizes emergency repairs and system disruptions.
Quality of Components
OEM vs Aftermarket Hoses
While aftermarket hoses may offer cost savings, they often lack the material consistency and performance standards of Original Equipment Manufacturer (OEM) hoses. OEM components are rigorously tested and better integrated with specific machinery requirements.
Impact of Fittings and Couplings
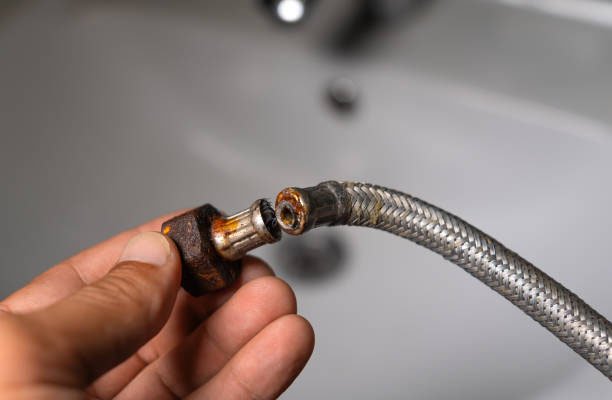
Low-quality or mismatched fittings can compromise seal integrity and increase wear at connection points. Precision-engineered couplings ensure a secure fit, reduce leak potential, and preserve hose lifespan. Compatibility and proper torque specifications are critical for safe operation.
The Role of Hose Certifications
Certified hoses (e.g., SAE, ISO-compliant) meet industry benchmarks for pressure, temperature, and fluid compatibility. Using certified components ensures that your system meets regulatory and performance standards, reducing liability and enhancing safety.
Frequency and Type of Use
High-Cycle vs Low-Cycle Applications
The number of cycles a hydraulic system undergoes directly impacts hose wear. High-cycle applications—where the hose flexes or operates continuously—tend to wear out faster than low-cycle systems. Choosing hoses rated for high-cycle durability helps mitigate early failure in these environments.
Static vs Dynamic Operations
Static hoses remain relatively still during operation, while dynamic hoses move, twist, or bend. Dynamic applications expose hoses to greater mechanical stress and require materials with higher flexibility and fatigue resistance to ensure long-term performance.
Duty Cycles and Load Demands
Hoses operating under heavy or continuous loads face elevated pressure and thermal stress, accelerating fatigue. Understanding your system’s duty cycle and selecting hoses accordingly—such as reinforced or spiral-wound designs—helps handle demanding operational conditions.
Signs of Hose Degradation
External Wear and Cracking
Visible damage like cracks, cuts, and abrasions on the hose’s outer cover are early indicators of degradation. These signs suggest the protective layer is compromised and the inner structure is at risk, warranting immediate inspection or replacement.
Bulging, Leaks, and Stiffness
Bulges indicate internal damage or impending failure due to excessive pressure or material fatigue. Leaks, especially near fittings, suggest seal deterioration or hose wall breakdown. If the hose becomes rigid or unusually stiff, it may no longer be safe for use and should be replaced promptly.
When to Replace a Hose
Hydraulic hoses should be replaced at the first sign of significant wear, aging, or incompatibility issues. Relying on manufacturer service life estimates and conducting regular condition-based assessments ensures safe and efficient system operation.
Best Practices to Extend Lifespan
Smart Design and Layout
Designing a hydraulic system with optimal hose lengths, bend radii, and protection from abrasion or high-heat areas significantly enhances hose longevity. Routing hoses to minimize movement and stress also contributes to longer service life.
Environmental Shielding
Use of sleeves, wraps, and guards protects hoses from UV exposure, heat, and physical damage. Shielding solutions are especially vital in outdoor or mobile equipment where environmental conditions are harsher and less predictable.
Regular Testing and Monitoring Tools
Advanced diagnostic tools such as pressure sensors, temperature gauges, and flow meters help monitor hose health in real-time. Predictive maintenance systems that analyze usage data can alert operators before failures occur, reducing downtime and repair costs.
Industry Standards and Compliance
SAE and ISO Standards
Hydraulic hoses are governed by standards such as those from the Society of Automotive Engineers (SAE) and the International Organization for Standardization (ISO). These standards define performance benchmarks for pressure, temperature, and dimensional tolerances, ensuring consistent quality and safety.
Importance of Compliance for Safety
Using hoses and components that meet recognized industry standards is essential for maintaining workplace safety and equipment integrity. Non-compliant hoses may not perform as expected under pressure, leading to failures that can result in equipment damage or personal injury.
Regulatory Requirements in Different Sectors
Various industries—such as mining, construction, oil & gas, and aerospace—have sector-specific compliance requirements. Ensuring that your hoses meet relevant regulations not only ensures safety but also avoids costly fines or operational shutdowns due to non-compliance.
Case Studies and Real-World Examples
Common Failure Scenarios
In one instance, a mining operation experienced recurring hose failures due to incorrect routing and abrasion from machinery vibration. After redesigning the layout and adding abrasion sleeves, hose life tripled, significantly reducing downtime and repair costs.
Extended Lifespan Success Stories
A construction company implemented smart hose monitoring and preventive maintenance schedules. This proactive approach extended the average hose lifespan from 18 months to over 36 months, while also improving operational uptime by 27%.
Conclusion
The lifespan of hydraulic hoses is influenced by a complex mix of factors including pressure, temperature, environmental exposure, fluid compatibility, and maintenance practices. By understanding these variables and implementing best practices—such as proper routing, scheduled inspections, and using high-quality components—businesses can greatly extend the life of their hoses and avoid costly failures.
Investing in innovations like smart hoses and predictive maintenance systems further enhances safety and efficiency. Ultimately, proactive hose management not only protects equipment and personnel but also contributes to smoother, more cost-effective operations.
FAQs
1. How often should hydraulic hoses be replaced?
While manufacturers may recommend replacement every 1 to 5 years, actual replacement should be based on visual inspection, usage conditions, and wear indicators. High-pressure or high-cycle systems may require more frequent replacements.
2. What is the most common cause of hydraulic hose failure?
The leading causes include improper installation, abrasion, pressure spikes, and exposure to incompatible fluids. Many failures are preventable with proper routing and regular maintenance.
3. Can weather significantly reduce hose lifespan?
Yes. UV rays, extreme temperatures, and moisture can all degrade hose materials. Using environmental shielding and choosing weather-resistant hoses can mitigate this risk.
4. How do I know if a hydraulic hose is failing?
Signs include external cracks, bulges, leaks, or a stiffened hose body. Sudden drops in pressure or system efficiency may also indicate internal hose issues.
5. Are smart hydraulic hoses worth the investment?
For critical operations, smart hoses provide real-time data and failure predictions that can prevent downtime and accidents. While initial costs are higher, the long-term savings and safety benefits often justify the investment.