Introduction to Hydraulic Adapters
Hydraulic adapters are specialized fittings used to connect hoses, pipes, and tubes within hydraulic systems. They allow components with different sizes, thread types, or fitting standards to work together, ensuring a secure, leak-proof connection. Without adapters, many hydraulic systems would lack the flexibility to link components effectively.
In short: they are the essential “bridges” that keep hydraulic machinery operating smoothly across varying pressures and configurations.
Types of Hydraulic Adapters
There are several common types of hydraulic adapters, each serving a specific design purpose:
- Straight Adapters:
These are simple, straight-line connectors for joining two components directly. - Elbow Adapters (45° or 90° angles):
Used when you need to redirect the hydraulic flow in tight spaces without bending hoses unnaturally. - Tee Adapters:
These create a T-shaped junction, allowing hydraulic fluid to split off into two directions. - Cross Adapters:
Form a cross-shape, connecting four components — ideal for more complex hydraulic setups.
Each type helps adapt fluid flow paths based on system layout and space constraints.
Common Materials Used in Hydraulic Adapters
Choosing the right material is vital because it affects durability, safety, and compatibility:
- Stainless Steel:
Best for corrosive environments like marine or chemical applications due to high corrosion resistance. - Carbon Steel:
Very strong and cost-effective. Ideal for general industrial applications where corrosion is less of an issue. - Brass:
Offers good corrosion resistance and is easy to machine. Often used in low- to medium-pressure systems. - Plastic and Composites:
Lightweight and corrosion-resistant; used in special cases where metal isn’t ideal (e.g., chemical handling).
Thread Types and Standards
Hydraulic adapters must match thread types and standards precisely to ensure leak-free, secure connections. Common thread standards include:
- NPT (National Pipe Tapered):
Common in North America, these threads taper to form a seal when tightened. They often require thread sealant or tape. - BSP (British Standard Pipe):
Used widely in Europe and Asia, BSP threads come in parallel (BSPP) and tapered (BSPT) forms. They require proper seals like bonded washers for BSPP. - JIC (Joint Industry Council):
Features a 37° flare fitting. These threads are very reliable for high-pressure applications and easy to assemble and disassemble. - SAE (Society of Automotive Engineers):
SAE threads use straight thread O-ring bosses (ORB) that seal with an O-ring, providing excellent leak prevention under high pressures.
Understanding thread compatibility is critical to avoid misfitting parts and system failures.
How Hydraulic Adapters Work
Hydraulic adapters work by joining different components in a system where direct connections aren’t possible. They bridge differences in size, thread type, angle, or flow direction between hoses, tubes, and fittings. A correctly chosen adapter prevents leaks, maintains pressure integrity, and ensures the overall reliability of the system. In high-pressure applications, their role becomes even more critical, preventing blowouts or accidents.
Key Applications of Hydraulic Adapters
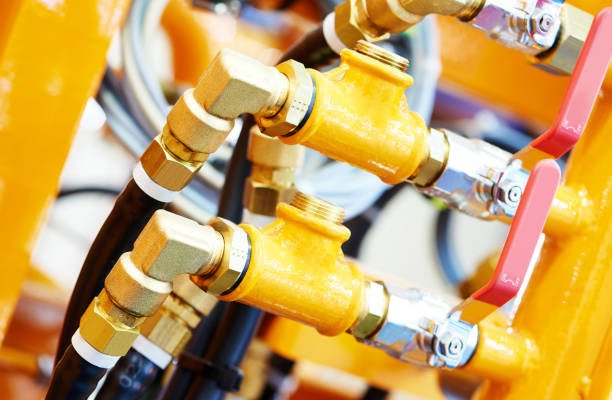
Hydraulic adapters are used across many industries to keep machinery and systems operating efficiently:
- Construction Machinery:
Excavators, loaders, and cranes use adapters to route hydraulic fluid efficiently through multiple cylinders and attachments. - Agricultural Equipment:
Tractors, harvesters, and sprayers rely on adapters for connecting hydraulic lines for steering, lifting, and operating implements. - Industrial Manufacturing:
Hydraulic presses, robotic arms, and assembly machinery use adapters to manage complex hydraulic circuits. - Automotive and Aerospace:
Vehicles and aircraft use compact hydraulic systems requiring adapters to connect components within tight spaces with absolute reliability.
Choosing the Right Hydraulic Adapter
Selecting the correct hydraulic adapter is essential for system performance and safety. Key factors to consider include:
- Pressure Rating: Ensure the adapter can handle the maximum system pressure without failure.
- Temperature Compatibility: Choose materials and seals that withstand the operating temperature range.
- Fluid Compatibility: Confirm the material is resistant to the type of hydraulic fluid being used.
- Size and Thread Matching: Always verify both the size and thread type to ensure a perfect fit without forcing connections.
Installation Best Practices
Proper installation ensures the longevity and safety of hydraulic adapters. Key best practices include:
- Torque Control: Follow manufacturer-recommended torque specifications to avoid overtightening or undertightening.
- Sealant Use: Apply thread sealant or Teflon tape only when appropriate, avoiding excess that could enter the system.
- Thread Alignment: Start threading connections carefully by hand to avoid cross-threading, which can weaken the joint and cause leaks.
Maintenance Tips for Longevity
Maintaining hydraulic adapters properly can greatly extend their service life. Important tips include:
- Regular Inspections: Check for cracks, corrosion, and leaks during routine system checks.
- Cleaning Threads: Keep threads clean from debris and old sealant to ensure proper seating.
- Timely Replacement: Replace adapters showing any signs of wear or damage to prevent system failure.
Advantages of Using High-Quality Hydraulic Adapters
Investing in high-quality hydraulic adapters offers numerous benefits for system efficiency and longevity:
- Improved System Efficiency: Precision manufacturing reduces energy loss and improves overall performance.
- Reduced Downtime: Durable adapters mean fewer failures and maintenance interventions, keeping operations running smoothly.
- Enhanced Safety: Reliable adapters minimize the risk of leaks, bursts, and other safety hazards in high-pressure systems.
Common Issues and Troubleshooting
Despite their reliability, hydraulic adapters can occasionally present issues. Common problems include:
- Leak Points: Often caused by improper installation, damaged threads, or worn seals. Inspect and reseal if necessary.
- Cross-Threading: Occurs when fittings are forced at incorrect angles. Always hand-thread connections first before tightening with tools.
- Material Fatigue: Over time, repeated pressure cycles can weaken materials. Replace any adapter showing visible signs of fatigue or deformation.
Environmental Considerations
As industries prioritize sustainability, hydraulic adapters are evolving to meet eco-friendly standards:
- Eco-Friendly Materials: Manufacturers are using recyclable metals and composites that reduce environmental footprint.
- Recycling Programs: Many companies now offer recycling options for used adapters, promoting circular economy practices.
- Waste Reduction: Enhanced durability and modular designs help minimize waste by reducing the frequency of replacements.
Conclusion
Understanding hydraulic adapter basics is crucial for designing and maintaining efficient fluid systems. Selecting the right type, material, and thread standard ensures reliability, safety, and optimal performance. By following proper installation and maintenance practices, you can extend the life of your hydraulic systems while embracing new innovations and sustainability trends. Investing in high-quality adapters today leads to fewer problems and better results tomorrow.
FAQs
How Do I Identify the Thread Type?
Use thread identification kits, measuring tools, or consult manufacturer specifications. Visual inspection alone is not reliable.
Can Different Materials Be Mixed?
It is possible but should be done cautiously. Mixing metals like brass and steel may cause galvanic corrosion if not properly managed.
Are Hydraulic Adapters Reusable?
In many cases, yes. However, if an adapter shows signs of thread damage, deformation, or seal wear, it should be replaced to maintain system integrity.