Introduction
Hydraulic hose crimping is a critical process that ensures the strength, safety, and longevity of hydraulic systems. Proper crimping guarantees that hoses can handle extreme pressures without leaking or bursting, protecting both equipment and operators. Among the vital aspects of this process, understanding and managing the crimping volume is key to achieving precision and optimal performance. In this guide, we dive deep into hydraulic hose crimping volume, covering essential insights, industry best practices, and common pitfalls to avoid.
What is Hydraulic Hose Crimping?
Hydraulic hose crimping is the process of securing a hose fitting to the end of a hydraulic hose by deforming the fitting around the hose. This mechanical joining method ensures a leak-proof and robust connection capable of withstanding high internal pressures. Unlike clamping or welding, crimping is a standardized, repeatable procedure that maintains the structural integrity of the hose. Precision in crimping affects not just the mechanical bond but also the flow dynamics and system efficiency, making it a foundational skill in hydraulic maintenance and assembly.
The Concept of Crimping Volume Explained
Crimping volume refers to the total space occupied by the crimped section of a hose assembly. It is influenced by the degree of compression applied during crimping, the dimensions of the fitting, and the hose material properties. Correct crimping volume ensures a secure connection without causing undue stress or damage to the hose fibers. If the crimping volume is too large or too small, it can compromise the assembly’s durability, leading to leakage, failure under pressure, or hose blow-off. Understanding and controlling crimping volume is therefore essential for achieving consistent, reliable hydraulic connections.
Factors Influencing Crimping Volume
Several factors play a role in determining the correct hydraulic hose crimping volume. First, the material and thickness of the hose significantly affect how much compression is needed for a secure fit. Different hoses—ranging from thermoplastic to steel-reinforced—respond differently to pressure. Second, the calibration and maintenance of the crimping machine are vital; even a slight misalignment can result in incorrect crimping volume. Lastly, environmental factors such as temperature and humidity can influence the flexibility and behavior of hose materials, making it crucial to account for working conditions during crimping operations.
Types of Hydraulic Hoses and Crimping Needs
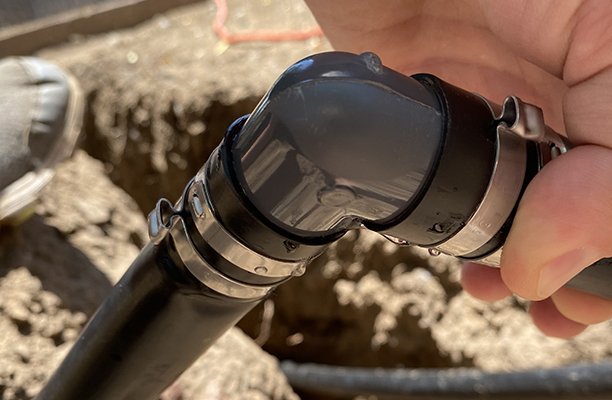
Hydraulic hoses come in various types, each requiring specific crimping techniques and volumes to ensure reliable performance:
- Low Pressure Hoses: Used for suction and return lines, these hoses require moderate crimping to maintain flexibility without leakage.
- Medium Pressure Hoses: Common in industrial and agricultural applications, they demand precise crimping to handle intermittent pressure spikes.
- High Pressure Hoses: Typically found in heavy machinery and construction equipment, these hoses require tight, accurate crimping to endure constant high-pressure environments.
Choosing the right crimping method for each hose type is critical to ensuring long-term system stability and safety.
Measuring Hydraulic Hose Crimping Volume
Measuring the crimping volume is crucial for quality assurance and system safety. Technicians use precision calipers, micrometers, and specialized crimping gauges to verify crimp dimensions post-assembly. Adherence to industry standards, such as SAE (Society of Automotive Engineers) specifications, ensures consistent, reliable measurements. It is best practice to document each crimp’s measurements, especially in critical applications, to provide traceability and confirm that the crimp meets the design and performance requirements. Accurate measurement reduces the risk of field failures and prolongs the lifespan of hydraulic assemblies.
The Role of Crimp Diameter in Volume Calculation
Crimp diameter is a critical metric directly related to the crimping volume. It refers to the final outer diameter of the hose and fitting assembly after crimping. A properly calibrated crimp diameter ensures the correct internal compression, which in turn determines the crimp volume. If the crimp diameter is too small, it can lead to hose damage or fitting distortion. If it’s too large, it may result in a loose connection and leakage. Most manufacturers provide crimp specifications, including target diameters, which technicians must adhere to for consistent and safe hose assemblies. Regular verification using precision measurement tools helps maintain the ideal balance between diameter and crimp volume.
Common Mistakes in Hydraulic Hose Crimping
Even experienced technicians can make errors that compromise hydraulic hose assemblies. Over-crimping, which compresses the hose beyond recommended limits, can cause structural damage, leading to early failures. Under-crimping, on the other hand, results in an insecure connection that risks leakage or blow-off under pressure. Using the wrong die size, skipping machine calibration, or ignoring manufacturer specifications are frequent mistakes. Additionally, failing to inspect hoses and fittings for defects before crimping can introduce hidden weaknesses. Awareness and adherence to best practices can significantly reduce these errors, ensuring safer and longer-lasting hydraulic systems.
Best Practices for Achieving Optimal Crimp Volume
Achieving optimal crimp volume requires a disciplined approach to preparation and execution. Begin with a thorough pre-inspection of the hose and fittings, checking for compatibility and any signs of wear or damage. Calibrate the crimping machine according to the manufacturer’s specifications before starting any job. Select the correct die size and pressure settings based on the hose type and size. It’s essential to perform a test crimp and measure the diameter to confirm settings before proceeding with production. Regular maintenance of crimping equipment and adherence to detailed documentation practices further enhance the reliability and repeatability of the crimping process.
Understanding Crimp Specifications
Crimp specifications are detailed guidelines provided by hose and fitting manufacturers to ensure proper crimping. They include information such as crimp diameter, crimping force, and die selection for each hose and fitting combination. Understanding these specifications is critical because even slight deviations can jeopardize the safety and performance of the hydraulic system. Specifications are usually found in crimp charts, either in printed manuals or digital databases, and must be followed meticulously. Cross-referencing hose type, fitting type, and desired pressure rating helps technicians achieve consistent, reliable crimping results every time.
Hydraulic Crimping Machines: Key Features to Consider
Choosing the right hydraulic crimping machine is essential for achieving optimal crimping volume. Key features to look for include adjustable pressure settings, which allow for precise control based on the hose type and size. Die versatility and ease of die changing enhance flexibility and efficiency, especially in shops handling diverse hose types. Automatic stop functions and built-in measuring tools add layers of accuracy and safety. In high-volume operations, machines with digital controls and programmable settings can drastically reduce setup time and errors, ensuring each crimp meets the exact specifications required.
Innovations in Crimping Technology
Recent innovations in crimping technology have significantly improved accuracy, efficiency, and safety. Automated crimping systems can now store multiple crimp profiles and self-adjust to specific hose and fitting types, reducing manual errors. Digital calibration tools provide real-time feedback, ensuring crimp diameters remain within tight tolerances. Some advanced systems even integrate with IoT platforms, allowing remote monitoring, predictive maintenance alerts, and detailed performance analytics. These innovations are transforming hydraulic hose assembly into a smarter, more connected process, setting new benchmarks for reliability and quality assurance in the industry.
Safety Considerations During Crimping
Safety is paramount during hydraulic hose crimping operations. Technicians must always wear appropriate Personal Protective Equipment (PPE), including safety glasses, gloves, and protective footwear, to minimize the risk of injury. Proper machine setup is critical; unsecured hoses or incorrect die placements can result in dangerous blowouts or equipment damage. Operators should follow lockout/tagout procedures when performing maintenance on crimping machines. Additionally, it’s important to maintain a clean work environment free of oil spills, debris, or any material that could cause slips or equipment malfunctions. Prioritizing safety not only protects workers but also ensures the quality and reliability of the finished hose assemblies.
Troubleshooting Crimping Volume Problems
When hydraulic hose assemblies fail, crimping volume is often a contributing factor. Common symptoms include visible hose deformation, fitting blow-off, leaks at the connection, or premature wear near the crimped area. To troubleshoot, technicians should first verify crimp diameters against specifications using precision tools. Reviewing machine calibration logs and examining the condition of the dies can also reveal root causes. If inconsistencies are found, re-calibration and replacement of worn components are necessary. A systematic, step-by-step approach to troubleshooting ensures that crimping issues are identified and corrected promptly, restoring system reliability and safety.
Environmental Impact of Hydraulic Hose Crimping
Hydraulic hose crimping, while vital to many industries, has an environmental footprint that must be considered. Waste generated from incorrectly crimped hoses, discarded fittings, and excess hydraulic fluid can accumulate quickly. Companies are now adopting waste reduction strategies such as recycling old hoses, using biodegradable hydraulic fluids, and implementing more accurate crimping technologies to minimize material waste. Eco-friendly crimping solutions, including energy-efficient machines and smart monitoring systems, help reduce emissions and promote sustainability throughout the hose assembly lifecycle.
Future Trends in Hydraulic Hose Crimping
The future of hydraulic hose crimping is marked by smart technology integration and increased automation. Smart crimping machines equipped with IoT sensors are making predictive maintenance possible, allowing technicians to address machine issues before they cause downtime. Artificial Intelligence (AI) algorithms are being developed to optimize crimping settings dynamically based on real-time environmental and material data. Furthermore, digital crimp certification is becoming standard, enabling full traceability and quality assurance for critical hydraulic systems. These trends promise greater precision, efficiency, and sustainability across the hydraulic hose industry.
Conclusion
Understanding and mastering hydraulic hose crimping volume is essential for ensuring the safety, reliability, and efficiency of hydraulic systems. From selecting the right equipment and adhering to precise specifications to embracing modern innovations and maintaining a focus on safety, every step matters. As industries continue to demand higher performance and greater accountability, attention to crimping volume will remain a cornerstone of quality hydraulic assembly practices. By investing in proper techniques, continuous learning, and cutting-edge technologies, businesses can achieve lasting success and operational excellence in their hydraulic operations.
FAQs
1. What happens if the crimping volume is too high?
If the crimping volume is too high, it can excessively compress the hose material, causing internal damage to the hose structure. This may lead to premature failure, leaks, or even sudden hose bursts under pressure, posing serious safety risks.
2. How often should crimping machines be recalibrated?
Crimping machines should typically be recalibrated every six months or after every 10,000 crimps, whichever comes first. However, high-usage environments or critical applications may require more frequent calibration checks to ensure accuracy and safety.
3. Are there universal standards for hydraulic crimping volume?
While there are general industry standards such as SAE and ISO guidelines, most crimping volume specifications are specific to the hose and fitting manufacturers. Always refer to the manufacturer’s crimp charts and instructions for exact specifications.
4. Can crimping volume affect hydraulic flow rate?
Yes, improper crimping volume can impact the internal hose dimensions and alter fluid dynamics. Over-crimping can restrict flow, leading to pressure drops and reduced system efficiency, while under-crimping can cause leakage and flow instability.
5. What are the signs of a poorly crimped hydraulic hose?
Signs of a poorly crimped hydraulic hose include visible hose deformation, fluid leaks at the fitting connection, unusual bulging near the crimp area, fitting slippage, and early hose deterioration under normal operating pressures.