Hydraulic quick couplings play a critical role in modern fluid power systems. Their ability to rapidly connect and disconnect fluid lines without leakage or contamination has made them indispensable in industries ranging from agriculture and construction to manufacturing and aerospace. Selecting the right hydraulic quick coupling, however, requires a solid understanding of system demands, safety considerations, and compatibility factors.
This comprehensive guide is divided into structured sections to help engineers, maintenance teams, and procurement professionals make informed coupling decisions.
1. Introduction to Hydraulic Quick Couplings
Hydraulic quick couplings, often called quick disconnects or quick release couplings, are fittings designed to easily and quickly connect or disconnect hydraulic lines without tools. They ensure tight, secure sealing, and minimal fluid loss when lines are opened. These components are engineered to reduce downtime during equipment servicing or changeover and to help prevent environmental contamination by limiting fluid spills.
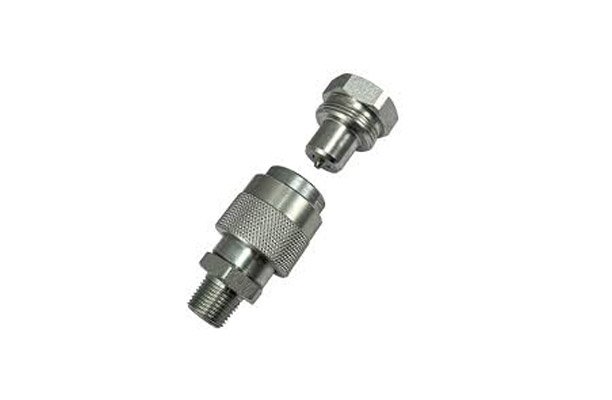
The core components typically include:
- Plug (male half): Inserts into the socket.
- Socket (female half): Contains internal valves and sealing surfaces.
- Valve mechanisms: Allow automatic shut-off to minimize fluid loss.
- Locking mechanism: Ensures a secure fit, with some designs including push-pull or threaded locking options.
There are various types of couplings, each designed for different hydraulic system demands and connection styles.
2. Functional Importance and Application Contexts
The use of hydraulic quick couplers varies widely across sectors, and their selection often hinges on operational context. The most common application environments include:
- Agriculture: Implements like harvesters, plows, and sprayers rely on flat-face couplings to prevent contamination from dust and soil.
- Construction: Excavators, backhoes, and skid steers require rugged couplings capable of withstanding pressure spikes and mechanical stress.
- Industrial Manufacturing: Assembly lines and hydraulic presses may need high-cycling couplings that offer minimal wear.
- Mining and Oil & Gas: Require corrosion-resistant and high-pressure-rated couplings, often made of stainless steel or coated brass.
- Forestry and Marine Equipment: Often operate in wet, muddy, or saline environments, where sealing and corrosion resistance are critical.
Using the wrong type of coupling can lead to pressure drops, system inefficiencies, and increased maintenance costs. Proper selection helps ensure safety, fluid integrity, and system uptime.
3. Types of Hydraulic Quick Couplings
Choosing the right type of quick coupling involves understanding the structural and performance differences between designs. Common types include:
a. Ball-Type Couplers
These are among the most widely used general-purpose hydraulic couplings. The mechanism uses spring-loaded balls to secure the plug inside the socket.
Advantages:
- Simple and quick to connect
- Cost-effective
- Available in a variety of sizes and materials
Limitations:
- More prone to leakage during connection/disconnection
- Not ideal for contaminated environments
b. Flat-Face Couplers (ISO 16028)
These couplers feature flat mating surfaces that reduce air inclusion and fluid loss. They’re commonly used in environments requiring cleanliness, such as food processing, construction, and mobile equipment.
Advantages:
- Minimal fluid loss and air entry
- Easy to clean
- Reduced contamination risk
Limitations:
- Typically more expensive
- Slightly bulkier than ball couplers
c. Threaded Screw-to-Connect Couplers
These are designed for high-pressure applications and provide strong resistance to vibrations and hydraulic shock.
Advantages:
- Secure under high pressure
- Can connect/disconnect under residual pressure
- Extremely reliable sealing
Limitations:
- Slower to connect/disconnect
- Thread wear can occur in aggressive environments
4. Key Performance Criteria for Selection
Selecting a hydraulic quick coupling isn’t just about matching thread sizes; rather, the decision should be based on a comprehensive understanding of your system’s operational parameters. Therefore, to make an informed choice, consider the following key performance criteria:
a. Working Pressure
Each coupling has a maximum rated working pressure; consequently, it must meet or exceed the operating pressure of your hydraulic system. Otherwise, exceeding this pressure can lead to failure, leaks, or even catastrophic damage.
- Low-pressure systems: Less than 2,000 PSI
- Medium-pressure systems: 2,000–4,000 PSI
- High-pressure systems: 4,000–10,000+ PSI
Ensure that the coupling’s burst pressure is also appropriate for safety margins.
b. Flow Rate
Flow capacity is usually rated in gallons per minute (GPM) or liters per minute (LPM). A coupling with insufficient internal diameter can restrict flow, causing pressure drops and heat buildup.
- Select a size that matches your system’s flow without becoming a bottleneck.
- Review manufacturer flow charts to match performance at given pressures.
c. Connection and Disconnection Requirements
Some systems require couplings to be connected or disconnected under pressure—known as residual or trapped pressure.
- Standard couplers cannot be connected under pressure.
- Specialized designs, such as flat-face or decompression couplers, allow connection with trapped pressure in one or both sides.
Verify your system’s typical connection state and select couplings accordingly.
5. Material Selection and Corrosion Resistance
Hydraulic quick couplings are made from a variety of materials, each offering unique properties for different environments and fluid types.
a. Carbon Steel
- Most common and cost-effective
- Suitable for general industrial and mobile applications
- Requires plating (e.g., zinc) for corrosion protection
b. Stainless Steel
- Ideal for corrosive or marine environments
- Suitable for food processing, pharmaceuticals, and offshore drilling
- Higher cost but superior longevity
c. Brass
- Corrosion-resistant and compatible with water-based fluids
- Common in lower-pressure applications and lab environments
d. Composite/Polymer
- Lightweight and corrosion-resistant
- Limited to specific niche uses, such as agricultural spraying or coolant systems
Coating Options
Zinc-nickel and other advanced coatings can significantly enhance the corrosion resistance of steel couplings in aggressive environments.
6. Seal Material Compatibility
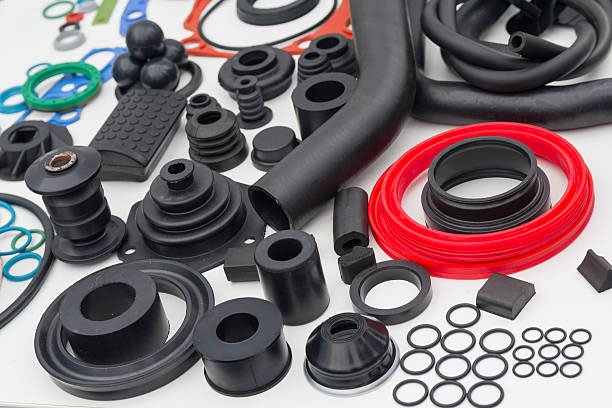
The sealing element inside a hydraulic coupling plays a critical role in maintaining fluid integrity and preventing leaks. However, choosing the wrong seal for your hydraulic fluid or temperature conditions can result in premature failure.
Common Seal Materials:
- Nitrile (Buna-N)
- General-purpose material
- Excellent for petroleum-based fluids
- Temperature range: -40°C to 120°C
- Viton (FKM)
- High-temperature and chemical-resistant
- Used with aggressive fluids like synthetic oils and biodiesel
- Temperature range: -20°C to 200°C
- EPDM
- Suitable for phosphate ester and glycol-based fluids
- Not compatible with petroleum oils
- Used in fire-resistant and environmentally sensitive systems
- PTFE (Teflon)
- Chemically inert and highly temperature-resistant
- Used in static seals or non-dynamic applications
Always cross-reference the seal material with the hydraulic fluid type, ambient conditions, and system operating temperatures before finalizing your selection.
7. Environmental and Operational Considerations
Hydraulic couplings are often used in demanding environments; therefore, exposure to external elements can significantly impact their performance. As a result, understanding your operating conditions is essential to selecting the appropriate coupling type and material.
a. Contaminated Environments (Dust, Mud, Debris)
- Choose flat-face couplers for their ease of cleaning and minimal exposure of internal components.
- Use protective dust caps and plugs to prevent ingress of contaminants when disconnected.
b. Corrosive Environments (Saltwater, Chemicals)
- Opt for stainless steel or nickel-plated carbon steel to resist corrosion.
- Verify compatibility with both the fluid and the external exposure.
c. High-Vibration Applications
- Use screw-to-connect couplers to prevent unintentional disconnection under stress.
- Locking sleeves or safety locking pins may be necessary for secure installation.
d. Extreme Temperatures
- Ensure seal and body materials are rated for your expected temperature ranges.
- Low-temperature applications may require low-durometer seals for flexibility, while high-temperature applications demand thermal-resistant elastomers like Viton.
8. Sizing and Flow Capacity Considerations
Proper sizing ensures hydraulic efficiency and avoids unnecessary restrictions in flow. Sizing is based not just on thread size, but on the internal diameter (ID) of the coupling and its pressure/flow performance curves.
a. Common Coupling Sizes and Typical Flow Ranges
Coupling Size | Internal Diameter | Flow Range (GPM) | Typical Applications |
---|---|---|---|
1/4″ | 0.25″ | 1 – 3 GPM | Test points, diagnostics |
3/8″ | 0.375″ | 3 – 6 GPM | Skid steers, small implements |
1/2″ | 0.50″ | 6 – 12 GPM | Loaders, agricultural equipment |
3/4″ | 0.75″ | 12 – 20 GPM | Excavators, industrial equipment |
1″ | 1.00″ | 20 – 50 GPM | Heavy construction machinery |
b. Undersizing Consequences
- Flow restriction increases pressure drop and reduces actuator speed.
- Heat generation rises, decreasing hydraulic fluid life.
- Increased energy consumption from the pump.
c. Oversizing Considerations
- Higher cost
- Bulkier installation
- More weight and potential for misfit in compact equipment
Always reference OEM performance charts or manufacturer recommendations when determining coupling size for your application.
9. Connection Interface Standards
Hydraulic quick couplings are governed by various international standards; consequently, these standards ensure interchangeability and performance consistency across different manufacturers.
a. ISO Standards
- ISO 7241-A / ISO 7241-B: General-purpose couplers; common in agriculture and industry.
- ISO 5675: Agricultural-specific couplers; designed for implements and tractors.
- ISO 16028: Flat-face couplers; widely used in construction and mobile equipment.
- ISO 15171-1: Screw-to-connect couplers; for high-pressure and impulse systems.
b. Thread Standards
Couplings come with different thread types depending on region and application:
- NPT (National Pipe Taper): U.S. standard, uses a tapered thread for sealing.
- BSP (British Standard Pipe): Used in Europe, available in parallel (BSPP) or tapered (BSPT).
- SAE ORB (O-Ring Boss): Provides reliable sealing in high-pressure hydraulic systems.
- Metric Threads: Common in machinery manufactured in Asia or Europe.
Ensuring the coupling’s thread matches your port fittings is vital to prevent leaks, cross-threading, or failure under pressure.
10. Safety Features and Best Practices
Safety is paramount when dealing with hydraulic systems under pressure. Couplings should not only be durable but should also help minimize the risk of accidental disconnection, fluid spray, or equipment damage.
a. Locking Mechanisms
Couplings may include features such as:
- Ball-lock sleeves: Require manual retraction for disconnection.
- Threaded collars: Prevent accidental release in high-vibration or high-shock environments.
- Push-pull locking systems: Found on flat-face couplers, suitable for quick changeover with integrated safety.
b. Pressure Relief Features
Some quick couplings are designed to allow connection or disconnection under residual pressure, typically using:
- Pressure relief valves
- Decompression slots
- Push-to-connect under pressure systems
These reduce the risk of fluid spray or seal damage when disconnecting a line that hasn’t been fully depressurized.
c. Color Coding and Identification
To prevent incorrect connection between circuits:
- Use color-coded dust caps or sleeves.
- Apply tags or laser markings to indicate pressure rating, flow direction, or fluid compatibility.
d. Routine Inspection Protocols
- Visually inspect for signs of wear, pitting, cracking, or rust.
- Check for damaged O-rings or seals.
- Replace worn or mismatched halves immediately.
11. Maintenance and Troubleshooting
Proper maintenance of hydraulic quick couplings extends the life of your system and helps avoid failures in the field. Establishing a proactive maintenance plan is vital.
a. Preventive Maintenance Tips
- Clean before connection: Prevent dirt from entering the system.
- Lubricate seals: Use recommended compatible lubricants.
- Replace damaged dust caps: Uncapped couplers can quickly become contaminated.
- Flush couplings before long-term storage.
b. Common Coupling Issues
Issue | Possible Cause | Solution |
---|---|---|
Dripping/Leaking | Worn or damaged seal | Replace O-ring or seal set |
Hard to Connect | Pressure trapped in one or both sides | Use decompression coupling or bleed-off valves |
Coupling Disconnects Easily | Locking sleeve not engaged properly | Inspect sleeve, replace if worn |
Overheating | Undersized coupler or flow restriction | Reassess sizing; match with system flow demand |
c. Storage Practices
- Store unused couplers in sealed, dry containers.
- Avoid leaving couplers exposed on outdoor equipment when not in use.
- Plug or cap both male and female ends after disconnection.
12. Industry-Specific Recommendations
Different industries demand specific performance and compliance standards when it comes to hydraulic couplings. Tailoring selection to your sector improves efficiency, safety, and regulatory alignment.
a. Agriculture
- ISO 5675 couplers are commonly used.
- Tractors and implements may need push-pull designs for on-the-fly connection.
- Flat-face designs are gaining traction due to better contamination control.
b. Construction and Earthmoving
- ISO 16028 flat-face couplers are preferred for skid steers, excavators, and loaders.
- Look for couplers that can connect under pressure due to hydraulic locking.
- Anti-vibration locking is critical in heavy-duty mobile applications.
c. Oil & Gas
- Require stainless steel or corrosion-resistant coatings.
- High-pressure screw-type couplers rated for 10,000+ PSI are common.
- Couplers must comply with safety standards such as API or ATEX.
d. Industrial Manufacturing
- High-frequency coupling/decoupling requires long-life valves and seals.
- Inline check valves and integrated leak testing ports can improve reliability.
- Compatibility with robotic tool changers and automation systems may be necessary.
13. Interchangeability and Cross-Reference Compatibility
In many maintenance and OEM scenarios, quick couplings need to be replaced with alternatives from different manufacturers. This makes interchangeability a key consideration when selecting couplers.
a. Interchange Standards
Certain ISO standards ensure couplers from different brands can be substituted:
- ISO 7241-A/B: Common for general-purpose use; most manufacturers produce A/B series interchangeably.
- ISO 16028: Flat-face couplers across brands are designed to be interchangeable.
- Manufacturer-specific series: Some couplings (especially screw-to-connect) are proprietary and not interchangeable—always check cross-reference charts.
b. Cross-Reference Tips
- Use manufacturer cross-reference guides to find equivalents.
- Match not only external dimensions, but also internal components like seal materials and flow specs.
- Beware of slight dimensional mismatches, even among “interchangeable” couplers—they can cause leaks or fitment issues under high pressure.
If interchangeability is a priority in your application (e.g., rental fleets or globally serviced machines), choose couplers built to ISO interchange standards.
14. Purchasing Considerations
Making a coupling decision extends beyond performance specs—it must also align with budget, supply chain, and long-term serviceability.
a. Total Cost of Ownership (TCO)
While cheaper couplers may appear attractive, they can cost more in the long run due to:
- Frequent replacements
- Downtime from poor sealing
- Safety issues from unintended disconnects
Investing in higher-grade couplers reduces TCO over the product lifecycle.
b. Supply Chain and Availability
- Choose brands with global distribution networks for faster replacements.
- Ensure standard sizing and threads for off-the-shelf compatibility.
- Partner with suppliers offering custom kitting or labeling for faster serviceability.
c. Brand Reputation and Warranty
- Favor manufacturers known for strict adherence to standards and quality assurance.
- Review warranty terms and failure rate data when available.
- Ask for certificates of compliance for mission-critical systems.
Conclusion
Hydraulic quick couplings are essential components that directly impact the performance, safety, and uptime of fluid power systems. A poor coupling choice can lead to downtime, contamination, and even equipment failure. A well-selected coupling, on the other hand, ensures:
- Fast and secure connection/disconnection
- Minimal fluid loss or contamination
- System compatibility across pressure, flow, and environmental factors
- Long-term durability with reduced maintenance costs
To choose the right hydraulic quick coupling:
- Understand your system’s pressure, flow, and temperature requirements.
- Select the correct type (flat-face, ball, screw-to-connect) for your application.
- Match seal material with fluid type and environmental conditions.
- Use ISO-standard couplers when interchangeability matters.
- Invest in reliable, reputable brands that offer product support and warranty.
FAQs
1. What is the main purpose of a hydraulic quick coupling?
Hydraulic quick couplings allow fast, tool-free connection and disconnection of hydraulic lines, minimizing fluid loss and system contamination.
2. Can I connect a quick coupler under pressure?
Only certain couplings are designed for connection under residual pressure. Flat-face and screw-to-connect types often offer this capability—always check the manufacturer’s specifications.
3. How do I know which size quick coupling to use?
Size selection depends on the required flow rate (GPM) and system pressure. Undersized couplings restrict flow and generate heat, while oversized ones may be unnecessarily bulky or expensive.
4. What is the difference between flat-face and ball-type couplers?
Flat-face couplers are designed to prevent fluid loss and contamination, making them ideal for dirty environments. Ball-type couplers are more common and generally easier to connect, but can leak more during disconnection.
5. How often should hydraulic couplers be replaced?
There’s no fixed timeline—replace them when you notice leaks, difficulty connecting, worn seals, or physical damage. Regular inspection helps avoid unexpected failures.
6. Are all hydraulic quick couplings interchangeable?
No. Only couplers that comply with the same ISO standard (e.g., ISO 16028) are interchangeable across brands. Always check compatibility before substituting.