American standard fittings are versatile connectors used in various pipelines, systems, and equipment. However, over time, these fittings may experience failure due to factors such as leaks, rust, or loosening. In this article, we’ll explore the causes of American standard fittings failure and discuss methods to extend their lifespan, helping to clarify some common concerns.
I. Common Types of American Standard Fittings
There are several types of American Standard fittings commonly used across various industries. Understanding these types can help in selecting the right fitting for specific applications:
1. NPT (National Pipe Thread) Fittings
These are commonly used for connecting pipes and fittings in low-pressure applications. They are available in various materials, including brass, stainless steel, and plastic.
2. JIC (Joint Industry Council) Fittings
These fittings have a 37-degree flare seating surface and are widely used in high-pressure hydraulic systems. They provide a reliable seal and are resistant to vibration.
3. SAE (Society of Automotive Engineers) Fittings
These fittings are often used in automotive and industrial hydraulic applications. They come in various forms, including straight, elbow, and tee shapes, to accommodate different connection requirements.
4. ORB (O-Ring Boss) Fittings
These fittings use an O-ring to create a seal and are designed for leak-free connections in hydraulic systems. They are commonly used in applications where high pressure is a concern.
5. Compression Fittings
These fittings are used for connecting tubes and pipes and are ideal for applications requiring a leak-proof seal. They are widely used in plumbing, gas lines, and chemical processing.
II. The Importance of High-Quality Fittings
High-quality fittings are crucial for the safe and efficient operation of any system that relies on fluid or gas transfer. These components ensure tight connections, prevent leaks, and withstand high pressures and temperatures. Using inferior fittings can lead to system failures, costly repairs, and even safety hazards. Therefore, investing in high-quality American Standard fittings not only enhances system reliability but also ensures long-term performance and reduces maintenance costs.
III. Causes of American Standard Fittings Failure
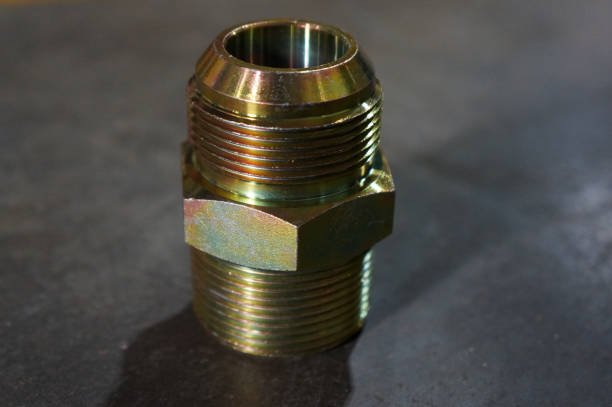
1. Improper Design and Selection
- Design Oversights: Designers can often trace fitting failures back to flaws where they did not adequately consider specific operating conditions, such as pressure, temperature, and chemical exposure. If you do not match the fitting’s material or size correctly to its application, premature failure is likely.
- Incorrect Material Selection: Choosing the wrong material for the environment can lead to corrosion, embrittlement, or degradation of the fitting. For example, using carbon steel fittings in corrosive environments without proper protection will lead to rust and eventual failure.
2. Manufacturing Defects
- Poor Workmanship: Manufacturing defects like cracks, voids, or improper thread cutting can weaken the fitting, making it prone to failure under stress. Inconsistent production quality can also lead to variations in fitting performance.
- Surface Finish Issues: A poor surface finish on sealing surfaces can cause improper sealing, leading to leaks and potential fitting failure over time. This is especially critical in high-pressure hydraulic systems.
3. Installation Errors
- Over-Tightening or Under-Tightening: Incorrect torque application during installation can either strip threads or fail to create an adequate seal, leading to leaks. Both over-tightening and under-tightening are common causes of fitting failure.
- Misalignment: If you do not properly align fittings with connected pipes or hoses, they can experience undue stress, which leads to cracks or breaks over time. Hasty installation or lack of attention to detail often causes misalignment.
4. Environmental and Operational Stresses
- Extreme Temperatures: Exposing fittings to temperatures beyond their limits can cause them to expand or shrink, leading to leaks, cracks, or complete failure. For high-temperature use, choose fittings made from materials that can handle heat without breaking down.
- Pressure Surges: When hydraulic systems experience pressure spikes that exceed the fittings’ capacity, the fittings can burst or seals can break. It’s important to choose the right size and type of fittings for these situations.
- Vibration and Shocks: Continuous shaking or sudden shocks can loosen fittings, wear down seals, and eventually cause them to fail. In such environments, use fittings designed to resist strong vibrations.
5. Material Aging and Degradation
- Corrosion: Over time, exposure to moisture, chemicals, and other corrosive agents can cause fittings to corrode. This weakens the structure of the fitting and increases the risk of failure. Stainless steel or coated fittings can help mitigate corrosion issues.
- Fatigue and Creep: Repeated cyclic loads can cause material fatigue, leading to microcracks that grow over time and eventually cause failure. Creep, which is the gradual deformation of the fitting under sustained stress, can also contribute to long-term failure, especially in high-temperature applications.
6. Lack of Regular Maintenance
- Neglect of Inspection and Servicing: Fittings require regular inspection to ensure they remain in good working condition. Neglecting routine maintenance can allow minor issues, such as small leaks or corrosion, to develop into major failures.
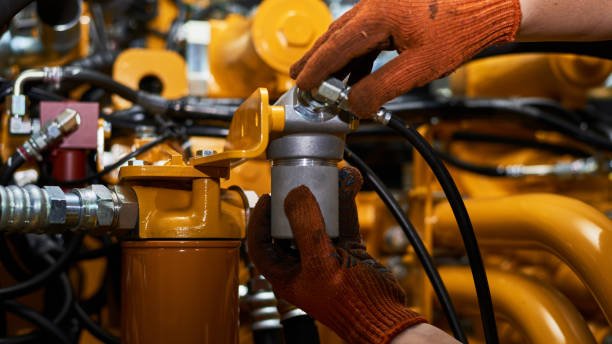
IV. Methods to Extend Fitting Lifespan
- Pay Attention to Design and Manufacturing: During the design and manufacturing process, carefully consider the environment and conditions to create a reliable plan.
- Use Proper Practices: Make sure to use American Standard fittings correctly. Avoid using too much force or tightening too much.
- Regular Maintenance: Regularly clean, tighten, and check the fittings to keep them in good condition.
- Choose the Right Materials: Select the right materials and sizes to ensure the fittings are strong and last longer.
- Follow Proper Installation Steps: Install the fittings following the recommended steps to ensure they are secure and avoid problems like loosening, slipping, or damage.
V. Comparing American Standard Fittings with Other Standards
When selecting fittings, it’s essential to understand how American Standard fittings compare to other common standards like DIN, ISO, and JIS. Many prefer American Standard fittings, such as NPT and JIC, for their robustness and wide availability in the North American market. In contrast, European markets commonly use DIN fittings because they offer precision and compatibility with specific equipment. ISO fittings, on the other hand, provide a global standard that ensures different regions and industries can easily work together. By understanding these differences, businesses can choose the fittings that best meet their needs, ensuring compatibility and performance.
VI. Conclusion
American Standard fittings play a crucial role in many applications. When these fittings fail, they can cause significant problems. Therefore, it is essential to focus on the design, material selection, usage, maintenance, and care of the fittings during actual usage. This approach can improve the performance, quality, and lifespan of the fittings, preventing premature failure.
VII. FAQs
Q1: What are the most common reasons for American standard fittings failure?
Common reasons include improper material selection, manufacturing defects, environmental factors, improper installation, and lack of maintenance.
Q2: How can I extend the lifespan of my plumbing fittings?
To extend the lifespan of plumbing fittings, choose high-quality materials, ensure proper installation, conduct regular maintenance, and protect fittings from harsh environmental conditions.
Q3: What role does water quality play in American standard fittings failure?
Poor water quality, such as hard or acidic water, can lead to scale buildup and corrosion, which weaken fittings and cause them to fail prematurely.
Q4: Can manufacturing defects in fittings be detected before installation?
You can detect some defects through inspections and testing, but others might only become apparent after the fitting is in use. This underscores the importance of choosing reputable manufacturers.
Q5: How do environmental factors affect the lifespan of plumbing fittings?
Environmental factors like temperature changes, humidity, and exposure to harsh chemicals can speed up the breakdown of materials, causing fittings to fail earlier than expected.
Q6: What are some future trends in plumbing fittings that could improve their lifespan?
Future trends include the development of more durable materials, smart technologies for monitoring system health, and a greater emphasis on sustainability in plumbing design.