Control valves are the unsung heroes of industrial processes, ensuring precise regulation of flow, pressure, and temperature. But what enables these valves to operate so effectively? The answer lies in actuators—devices that drive the motion of the valve. Whether you’re optimizing a new system or upgrading an existing one, selecting the right actuator is key to performance and reliability. In this detailed guide, we’ll explore the various types of actuators, their applications, and the critical factors to consider when choosing one for your system.
What Are Actuators for Control Valves?
Actuators are mechanical devices that convert energy—whether pneumatic, electric, hydraulic, or manual—into motion, which then operates a control valve. Their primary role is to automate the process, providing accuracy and consistency in systems where manual operation would be inefficient or impractical.
Key Functions of Actuators:
- Open and close the valve fully.
- Position the valve at precise increments for accurate flow control.
- Respond to control signals (e.g., 4–20 mA signals in electric actuators).
- Provide feedback to control systems (in advanced or smart actuators).
Types of Actuators for Control Valves
Each actuator type has its strengths and is suited for specific applications. Let’s take a deep dive into the most commonly used actuators.
1. Pneumatic Actuators
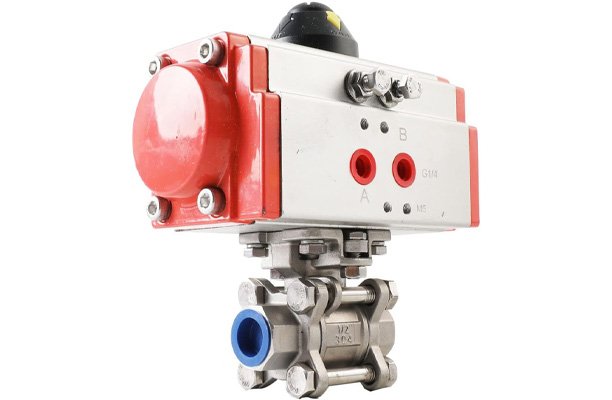
Pneumatic actuators are powered by compressed air and are the most widely used in industrial applications due to their simplicity, cost-efficiency, and durability.
How They Work:
- Compressed air enters a chamber, exerting pressure on a piston or diaphragm.
- This pressure generates motion, which either opens, closes, or adjusts the valve.
Subtypes:
- Spring-Return Pneumatic Actuators:
- Uses air pressure to move the valve in one direction and a spring to return it to its original position when the air supply is cut off.
- Common in fail-safe operations (e.g., emergency shutdown systems).
- Double-Acting Pneumatic Actuators:
- Requires air pressure for both opening and closing motions, offering precise control over valve movement.
- Ideal for applications where fail-safe positioning isn’t necessary.
Advantages:
- Cost-effective and low maintenance.
- Fast response times.
- Safe for hazardous environments (no risk of ignition).
- Simple design makes them reliable.
Limitations:
- Requires a continuous supply of compressed air.
- Less precise compared to electric actuators.
Best Applications:
- Oil and gas pipelines.
- Water treatment facilities.
- Chemical processing plants.
2. Electric Actuators
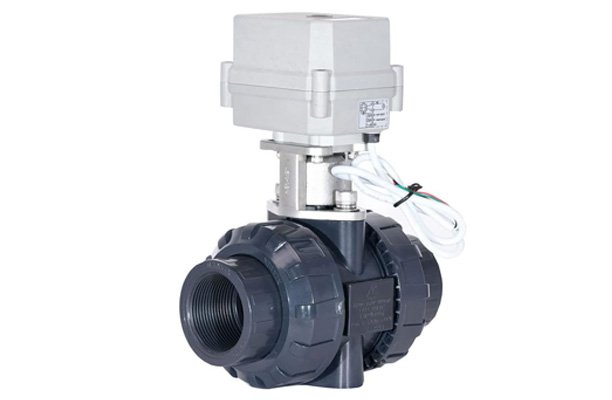
Electric actuators rely on an electric motor to drive the valve’s motion. These actuators are often chosen for applications requiring high precision and integration with advanced control systems.
How They Work:
- An electric motor generates rotary or linear motion.
- This motion is transmitted through a gearbox or mechanism to move the valve.
Advantages:
- High Precision: Allows for fine-tuned control, making them suitable for throttling applications.
- Ease of Integration: Can easily interface with programmable logic controllers (PLCs), distributed control systems (DCS), and SCADA.
- Eco-Friendly: No emissions or need for air compressors.
- Quiet Operation: Suitable for noise-sensitive environments.
Limitations:
- Slower response time compared to pneumatic actuators.
- More expensive upfront.
- Not ideal for hazardous environments (risk of electrical sparks).
Best Applications:
- Power generation facilities.
- HVAC systems in buildings.
- Food and beverage manufacturing.
3. Hydraulic Actuators
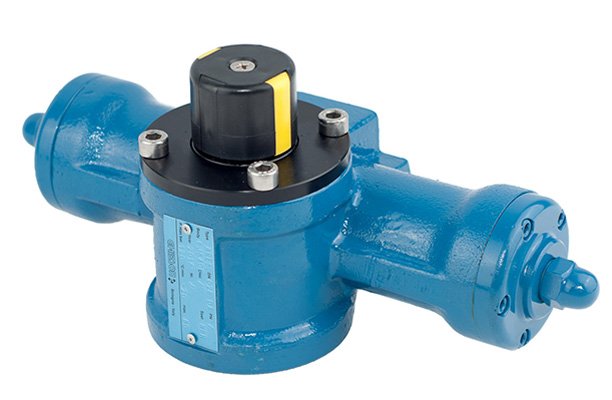
Hydraulic actuators use pressurized fluid to generate motion and are known for delivering high torque and force. They’re built for heavy-duty applications where other actuators might fall short.
How They Work:
- Pressurized hydraulic fluid is directed into a cylinder.
- The pressure moves a piston, creating linear or rotary motion to operate the valve.
Advantages:
- Capable of handling high-pressure systems.
- Suitable for large, heavy valves that require significant force to operate.
- Reliable in extreme conditions, including subsea or high-temperature environments.
Limitations:
- Requires a hydraulic power unit, which adds complexity and cost.
- Maintenance can be challenging due to potential fluid leaks.
Best Applications:
- Offshore oil rigs.
- Mining operations.
- High-pressure pipelines in the energy sector.
4. Manual Actuators
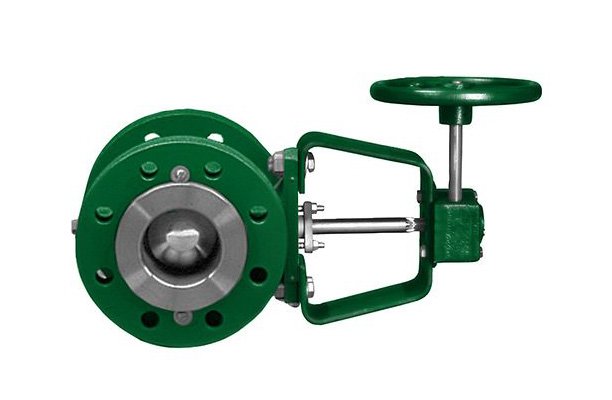
Though less advanced, manual actuators still play a vital role in small-scale and emergency applications. These actuators use handwheels, levers, or gear mechanisms to operate valves.
Advantages:
- Simple and cost-effective.
- No external power source needed.
- Easy to install and maintain.
Limitations:
- Requires manual intervention, making them impractical for automated processes.
- Not suitable for remote or inaccessible locations.
Best Applications:
- Small-scale industrial systems.
- Backup or emergency shut-off valves.
- Test and maintenance scenarios.
5. Smart Actuators
Smart actuators combine traditional actuator functionality with advanced sensors, diagnostics, and control capabilities. They’re a product of Industry 4.0, allowing real-time monitoring and remote operation.
How They Work:
- Equipped with sensors and digital controls that communicate with IoT platforms or SCADA systems.
- Provides continuous feedback on valve position, system health, and performance.
Advantages:
- Remote Operation: Perfect for hard-to-reach locations.
- Predictive Maintenance: Alerts operators of potential issues before failure occurs.
- Integration with IoT: Enhances system efficiency and reliability.
Limitations:
- High initial cost.
- Requires skilled personnel for setup and maintenance.
Best Applications:
- Smart factories and industrial automation.
- Power plants with advanced process control systems.
- Energy management systems for renewable sources.
Factors to Consider When Selecting an Actuator
1. Valve Type and Size
- Larger valves may require hydraulic or high-torque electric actuators.
- For quick-opening valves like ball valves, pneumatic actuators are often a good fit.
2. Process Conditions
- Temperature: Ensure the actuator can handle extreme heat or cold.
- Pressure: High-pressure systems often need hydraulic actuators for sufficient force.
3. Power Availability
- No compressed air? Go with electric or hydraulic actuators.
- For remote locations, manual or battery-powered electric actuators might be ideal.
4. Environmental Factors
- Corrosive environments may require actuators with special coatings or materials.
- Explosion-proof electric actuators are essential for hazardous areas.
5. Control System Integration
- Modern facilities benefit from actuators that integrate seamlessly with PLCs, DCS, and SCADA systems for real-time monitoring and control.
6. Cost and Maintenance
- Pneumatic actuators are budget-friendly but need a reliable air supply.
- Smart actuators may have a higher upfront cost but can reduce long-term operational expenses through advanced diagnostics.
Conclusion
Actuators for control valves play a vital role in industrial automation and process control. The choice between pneumatic, electric, hydraulic, manual, or smart actuators depends on your application, operating environment, and budget. Remember to evaluate torque requirements, power availability, and system integration when making your decision.
FAQs
1. Which actuator is best for high-speed applications?
Pneumatic actuators are best for high-speed applications due to their rapid response times.
2. Can smart actuators save money in the long run?
Yes! While they’re more expensive upfront, their advanced diagnostics and predictive maintenance features minimize downtime and repair costs.
3. Are hydraulic actuators noisy?
Not typically. Hydraulic actuators operate quietly, especially compared to pneumatic systems, making them suitable for noise-sensitive environments.
4. Do electric actuators require frequent maintenance?
Not usually. Electric actuators have fewer moving parts compared to hydraulic or pneumatic actuators, so they require less maintenance over time.
5. How do I know the torque needed for my valve?
Check the valve type, size, and system pressure. Most manufacturers provide torque charts—choose an actuator with slightly more torque than required for safe operation.
6. What’s the difference between fail-open and fail-close actuators?
- Fail-Open: Opens the valve during power loss for continuous flow.
- Fail-Close: Shuts the valve during power loss to stop flow.
Choose based on your system’s safety needs.