Introduction to Aluminum Fitting Surface Treatment
Aluminum fittings are prized for their lightweight structure, corrosion resistance, and adaptability across industries. However, untreated aluminum can be vulnerable to wear, oxidation, and environmental damage. Surface treatments are crucial to enhance these fittings’ performance, longevity, and appearance. Technological advancements have created diverse ways to enhance the protection and appearance of aluminum, making it stronger and more versatile.
Why Surface Treatment Matters for Aluminum Fittings
Applying the right surface treatment to aluminum fittings significantly boosts their durability and functional performance. It prevents early degradation, enhances mechanical strength, and offers aesthetic flexibility for different applications. Moreover, surface treatments provide a vital shield against corrosion, especially in harsh environments like marine, aerospace, and industrial sectors. Without proper treatment, aluminum fittings are at risk of pitting, oxidation, and structural failures, compromising both safety and visual quality.
Common Types of Surface Treatments for Aluminum Fittings
A variety of surface treatments are available to meet the specific needs of aluminum fittings, including:
- Mechanical Finishing: Techniques such as polishing, grinding, and sandblasting that physically alter the surface to remove imperfections and refine appearance.
- Chemical Treatments: Processes like acid etching and chromate conversion that chemically modify the surface for improved adhesion and corrosion resistance.
- Electrochemical Processes: Advanced methods like anodizing and electroplating that enhance surface strength and create visually appealing finishes.
Choosing the appropriate treatment method depends on the end-use requirements, desired aesthetics, and environmental exposure of the aluminum fittings.
Mechanical Surface Treatments Explained
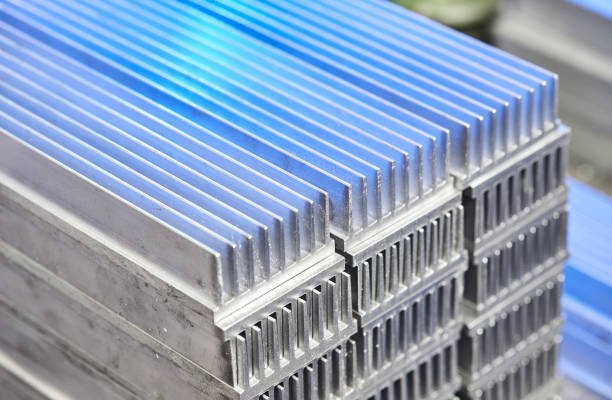
Mechanical surface treatments physically alter aluminum to improve its finish, fix imperfections, or prepare it for further processing. These techniques are essential for enhancing the metal’s durability and aesthetic appeal. The most common mechanical processes include:
- Polishing and Buffing: Polishing removes fine scratches for a smooth finish, while buffing boosts gloss and uniformity, making aluminum fittings more attractive and resistant to contaminants.
- Sandblasting and Shot Peening: High-pressure blasting techniques clean and roughen the aluminum surface. Sandblasting creates a uniform matte finish, while shot peening adds compressive stresses to boost surface strength and fatigue life.
- Grinding and Deburring: These methods remove sharp edges and defects, creating a safer, smoother product ready for further treatment or use.
Chemical Surface Treatments for Aluminum Fittings
Chemical treatments modify the aluminum surface at a molecular level, preparing it for coating or improving its inherent properties. These processes are crucial for enhancing corrosion resistance and promoting better adhesion of paints or other finishes:
- Acid Etching: By immersing aluminum in acid to remove contaminants and oxides, creating a clean, uniform, slightly textured surface for coating.
- Alkaline Cleaning: Alkaline cleaning removes oils, grease, and residues, leaving aluminum perfectly prepared for treatments like anodizing or painting.
- Chromate Conversion Coating: forms a corrosion-resistant layer and improves paint and powder coating adhesion. People often choose it for parts that require excellent conductivity and protection.
Electrochemical Surface Treatments
Electrochemical surface treatments use electrical currents to enhance the aluminum’s surface characteristics, offering outstanding durability, corrosion resistance, and aesthetic options:
- Anodizing Aluminum Fittings: Anodizing thickens aluminum’s oxide layer, boosting corrosion resistance and enabling decorative dye finishes. It also adds hardness and wear resistance to the surface.
- Electropolishing: Electropolishing smooths and brightens aluminum by removing surface material, creating a clean, glossy, and ultra-smooth finish.
- Electroplating: Involves depositing a thin layer of another metal, such as nickel or chrome, onto the aluminum surface. This enhances the appearance, wear resistance, and corrosion protection, extending the component’s functional life.
Anodizing: A Deep Dive
Anodizing is one of the most popular and effective electrochemical treatments for aluminum fittings. It enhances the natural oxide layer, providing superior corrosion resistance, durability, and aesthetic appeal. There are three primary types of anodizing:
- Type I – Chromic Acid Anodizing: A thinner, more flexible anodic layer, ideal for aerospace applications where slight weight increases must be avoided.
- Type II – Sulfuric Acid Anodizing: The most common method, producing a moderate thickness layer suitable for decorative finishes and enhanced wear resistance.
- Type III – Hardcoat Anodizing: Creates a much thicker and harder oxide layer, offering exceptional abrasion resistance for heavy-duty industrial uses.
Industries such as aerospace, automotive, architecture, and consumer electronics widely rely on anodized aluminum fittings for their durability, aesthetic flexibility, and protective benefits.
Powder Coating for Aluminum Fittings
In powder coating, workers spray electrostatically charged powder particles onto the aluminum surface and cure them under heat. It creates a tough, durable, and attractive finish:
- Process Overview: Workers pre-treat the aluminum fittings, coat them with powder, and bake them to form a solid, uniform layer that resists chipping, scratching, and fading.
- Color and Finish Options: Powder coating offers a vast range of colors, textures, and gloss levels, from matte to high gloss, making it ideal for branding and design consistency.
- Advantages: Powder coatings are environmentally friendly, VOC-free, and provide superior weather, chemical, and UV resistance compared to traditional liquid paints.
Painting and Liquid Coating Options
Although powder coating has become increasingly popular, traditional painting remains a viable surface treatment for aluminum fittings, especially for projects requiring specific textures or colors not achievable through powder:
- Choosing the Right Paint: Epoxy, polyurethane, and acrylic paints are commonly used for aluminum, each offering different levels of chemical, weather, and abrasion resistance.
- Application Methods: Spraying, brushing, and dipping are typical methods for applying liquid paints, each with its benefits depending on the project’s size and complexity.
- Pros and Cons: While painting allows for greater flexibility in custom finishes and repairs, it generally offers less durability than powder coating and may require more frequent maintenance.
Surface Treatment Selection Criteria
Selecting the right surface treatment for aluminum fittings depends on several critical factors. Making the right choice ensures the component meets both performance and aesthetic expectations:
- End-Use Environment Considerations: Exposure to harsh weather, chemicals, or marine conditions demands high-corrosion-resistant treatments like anodizing or powder coating.
- Mechanical Performance Requirements: Applications requiring enhanced wear resistance or hardness may benefit from hardcoat anodizing or specific electroplating methods.
- Aesthetic and Branding Needs: Architectural and consumer products often prioritize custom colors, gloss levels, and textures achievable through powder coating or painting.
Quality Control and Testing After Surface Treatment
Ensuring the effectiveness of aluminum surface treatments involves rigorous quality control and testing protocols. These measures verify that the surface treatment meets industry standards and specific project requirements:
- Coating Thickness Measurements: Tools like eddy current or magnetic induction gauges assess whether the anodic layer or coating thickness falls within specified tolerances.
- Adhesion Tests: Methods like cross-hatch tests or pull-off tests are employed to evaluate the bonding strength of applied coatings.
- Corrosion Resistance Evaluation: Salt spray testing and cyclic corrosion testing simulate harsh environments to determine the longevity and effectiveness of protective treatments.
Innovations in Aluminum Fitting Surface Treatments
The surface treatment industry continues to evolve with groundbreaking technologies that offer enhanced performance, sustainability, and new functionalities:
- Nanocoatings and Smart Coatings: Ultra-thin, self-healing, or multifunctional coatings provide enhanced protection while responding to environmental stimuli.
- Eco-Friendly Treatment Alternatives: New chromium-free conversion coatings and low-VOC processes are reducing the environmental impact without sacrificing performance.
- Future Trends: Digital printing on aluminum surfaces, advanced plasma treatments, and biomimetic coatings inspired by nature are setting the stage for the next generation of surface engineering.
Challenges in Aluminum Surface Treatments
Despite the numerous benefits of aluminum surface treatments, several challenges must be managed to achieve optimal results:
- Surface Contamination Issues: Oil, grease, and oxide layers on aluminum surfaces can interfere with treatment adhesion and performance. Thorough cleaning and preparation are critical to avoid defects.
- Treatment Compatibility with Alloy Types: Different aluminum alloys respond uniquely to treatments. For example, high-copper content alloys may anodize poorly, requiring customized surface preparation strategies.
- Environmental and Regulatory Constraints: Traditional treatments like chromate conversion face strict environmental regulations due to toxicity concerns, pushing the industry towards greener alternatives.
Maintenance of Treated Aluminum Fittings
Proper maintenance is essential to preserve the performance and appearance of treated aluminum fittings over time:
- Cleaning Best Practices: Use mild soaps, non-abrasive cloths, and fresh water for regular cleaning to prevent buildup of pollutants and contaminants.
- Recoating and Refurbishment Options: Fittings exposed to extreme conditions may require periodic recoating. Sanding, chemical stripping, or mild abrasive blasting can prepare surfaces for renewed treatment.
- Signs of Surface Degradation: Look for discoloration, blistering, or peeling coatings, which signal that maintenance or re-treatment is necessary to restore protective properties.
Aluminum Fittings in Different Industries
Surface-treated aluminum fittings are integral to various industries, offering customized solutions tailored to specific application needs:
- Aerospace Applications: Lightweight, high-strength anodized fittings are essential for aircraft structures, ensuring corrosion resistance without adding unnecessary weight.
- Marine and Offshore Uses: Powder-coated or anodized aluminum fittings withstand salty environments, resisting corrosion and extending operational life in harsh conditions.
- Architectural and Construction Sectors: Decorative finishes on aluminum fittings provide both functionality and aesthetic appeal for buildings, facades, and infrastructure projects.
Conclusion
Selecting the appropriate surface treatment for aluminum fittings is essential to maximize their performance, durability, and aesthetic value. By considering environmental exposure, mechanical demands, and visual requirements, businesses can ensure their fittings perform reliably over time. Advances in technology have made it easier than ever to tailor surface treatments to specific industry needs, offering a perfect balance between protection and design. Careful selection, rigorous quality control, and proper maintenance will help extend the life of aluminum fittings, saving costs and ensuring superior performance in even the harshest environments.
FAQs
1. What is the most durable surface treatment for aluminum fittings?
Hardcoat anodizing (Type III anodizing) is considered the most durable, offering exceptional wear resistance, corrosion protection, and hardness ideal for industrial and aerospace applications.
2. How often should powder-coated aluminum fittings be maintained?
Powder-coated fittings should be cleaned at least twice a year using mild detergents and fresh water. In harsher environments, quarterly cleaning is recommended to maintain the finish and protection.
3. Can treated aluminum fittings be welded?
Surface treatments like anodizing and powder coating must typically be removed from the weld area before welding to avoid contamination and achieve strong weld joints. Post-welding, re-treatment is usually necessary.
4. Are eco-friendly surface treatments as effective as traditional ones?
Yes, modern eco-friendly alternatives, such as chromium-free conversion coatings and low-VOC powder coatings, offer comparable protection and performance while reducing environmental impact.
5. What industries benefit most from surface-treated aluminum fittings?
Industries like aerospace, marine, construction, automotive, and electronics heavily rely on surface-treated aluminum fittings to ensure long-term reliability, aesthetic value, and resistance to harsh operating conditions.