Introduction
Aluminum fittings are popular in automotive, aerospace, construction, and electronics for their light weight, durability, and corrosion resistance. However, raw aluminum may not always provide the required strength, aesthetic appeal, or protection for specific applications. This is where aluminum fitting surface treatments come into play. These treatments improve the material’s properties, enhance its longevity, and offer custom finishes.
This blog will explore the different types of aluminum fitting surface treatments, including anodizing, powder coating, electroplating, and more. Each method serves a unique purpose, from corrosion protection to enhancing appearance and performance. Let’s dive into the essential surface treatment types and how they can benefit aluminum fittings.
Why Surface Treatment for Aluminum Fittings is Essential
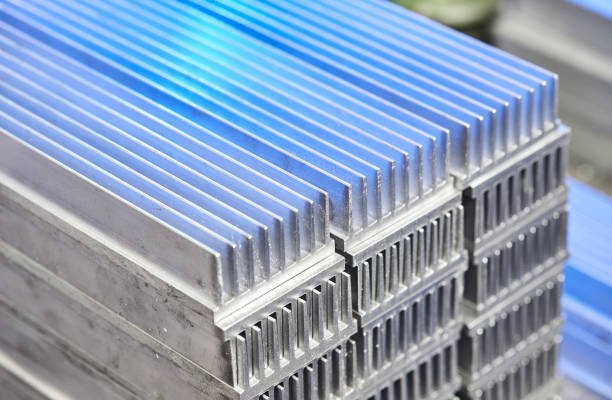
Surface treatments are vital for aluminum fittings as they enhance the material’s natural properties. Aluminum fittings are popular in automotive, aerospace, construction, and electronics for their light weight, durability, and corrosion resistance. By applying various surface treatments, manufacturers can significantly improve the longevity and functionality of aluminum fittings.
- Protection Against Corrosion: Aluminum naturally forms a protective oxide layer, but it can be vulnerable to corrosion in harsh environments. Surface treatments like anodizing and chromate conversion coatings enhance this protection.
- Improvement of Mechanical Properties: Aluminum fittings can be subject to wear, abrasion, and mechanical stress. Treatments like anodizing and electroplating can strengthen the material’s resistance to these factors.
- Aesthetic Enhancement: Surface treatments can create matte, glossy, or textured finishes, boosting the visual appeal of aluminum fittings for decorative use.
- Industry-Specific Applications: Aluminum fittings often need to meet specific industry standards for performance and appearance. Surface treatments can ensure they are suited for high-traffic, high-stress, or high-corrosion environments.
Types of Aluminum Fitting Surface Treatments
Now that we know the importance of surface treatments, let’s explore the most common methods for aluminum fittings:
Anodizing
Anodizing is one of the most popular and effective surface treatments for aluminum. This electrochemical process creates a thick oxide layer on the aluminum’s surface, which significantly increases its corrosion resistance and wear durability. Anodizing also allows for the addition of colors, giving aluminum fittings a unique and attractive appearance.
Benefits of Anodizing:
- Durability: The anodized layer is highly durable, offering resistance to corrosion, scratching, and fading. It’s ideal for products exposed to harsh weather conditions.
- Environmental Benefits: Anodizing is a non-toxic, environmentally friendly process, as it does not release harmful chemicals or pollutants.
- Improved Aesthetic Appeal: Anodized aluminum can be dyed in various colors, providing excellent opportunities for customization.
- Minimal Maintenance: Once anodized, aluminum surfaces require minimal maintenance to keep their appearance and function intact.
Anodizing is commonly used in the automotive, aerospace, and architectural industries where both durability and aesthetic appeal are essential.
Powder Coating
Powder coating is another widely used aluminum fitting surface treatment that provides both protective and decorative benefits. The process involves applying a dry powder to the aluminum surface, which is then cured under heat to form a solid, durable coating. Unlike traditional liquid paints, powder coating is more resistant to chipping, scratching, fading, and wearing.
Advantages of Powder Coating:
- Durability: Powder-coated aluminum fittings are highly resistant to abrasion and corrosion. This treatment is ideal for items that will be exposed to the elements.
- Eco-friendly: Powder coating contains no solvents, making it a more environmentally friendly option than liquid paint, which often emits harmful chemicals.
- Variety of Finishes: Powder coating can be done in a wide range of colors and finishes, including matte, glossy, and textured.
- Cost-Effectiveness: Although the initial setup for powder coating may be more expensive, the long-term benefits, including fewer maintenance needs, make it a cost-effective choice.
The automotive industry, architecture, and furniture commonly use powder coating for aluminum fittings in outdoor applications.
Electroplating
Electroplating applies a metal coating to the aluminum surface through an electric current. This method improves the appearance, corrosion resistance, and hardness of aluminum fittings. Nickel, chrome, and gold are the most common electroplated metals, each offering unique benefits for different applications.
Benefits of Electroplating:
- Enhanced Corrosion Resistance: Electroplated layers, such as chrome or nickel, provide additional corrosion resistance, making them ideal for use in marine or chemical environments.
- Improved Aesthetic Finish: Electroplating can give aluminum fittings a shiny, mirror-like finish, which is highly desirable in decorative applications.
- Increased Hardness: The electroplated layer can significantly increase the hardness of the aluminum surface, providing enhanced resistance to wear and tear.
- Precision and Customization: Electroplating provides precise control over coating thickness and uniformity, making it ideal for detailed designs and intricate finishes.
The automotive, electronics, and decorative industries often use electroplating, where appearance and functionality are paramount.
Chromate Conversion Coating
Chromate conversion coating is a chemical process that creates a protective layer on the aluminum surface. This treatment not only improves the material’s corrosion resistance but also provides a good base for painting and bonding. Unlike anodizing, which thickens the aluminum oxide layer, chromate conversion forms a thin but effective protective film.
Advantages of Chromate Conversion Coating:
- Excellent Corrosion Protection: Chromate conversion coatings offer significant corrosion resistance, especially in environments exposed to saltwater or other harsh chemicals.
- Improved Adhesion: This coating improves the adhesion of subsequent coatings, such as paints or powder coatings, which can be vital for aesthetic applications.
- Versatility: Chromate conversion is versatile and can be applied to aluminum fittings of all sizes and configurations, from small parts to large structural components.
- Fast and Economical: Compared to other surface treatments, chromate conversion is a relatively quick and cost-effective process.
Aerospace, military, and automotive industries use chromate conversion coatings, where corrosion resistance is critical, and aluminum fittings are exposed to extreme conditions.
Brushed and Polished Aluminum
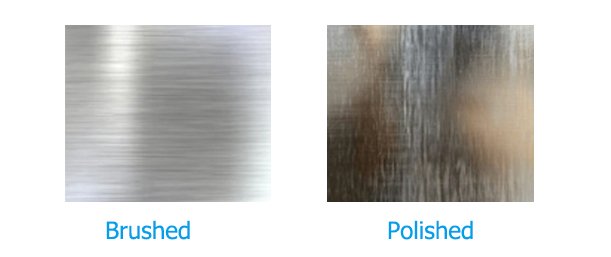
Brushed and polished aluminum are treatments that focus on the appearance of the material. The brushing process involves using abrasives to create a textured surface with fine lines, while polishing gives the aluminum a smooth, shiny, reflective finish. These treatments not only enhance the aesthetics of aluminum fittings but can also provide minor improvements in corrosion resistance.
Benefits of Brushed and Polished Aluminum:
- Aesthetic Appeal: Brushed aluminum offers a modern, industrial look with a matte finish, while polished aluminum provides a sleek, shiny surface.
- Resistance to Smudges and Fingerprints: The brushed finish helps to hide fingerprints and smudges, making it ideal for high-traffic areas or products that will be handled frequently.
- Increased Durability: While not as protective as anodizing, polished and brushed finishes can help to reduce the risk of scratches and surface damage.
- Easy to Maintain: Both brushed and polished aluminum surfaces are relatively easy to clean and maintain, requiring only basic cleaning agents and a soft cloth.
Laser Etching and Engraving
Laser etching and engraving use a laser beam to create precise patterns, markings, or designs on aluminum surfaces. These methods are ideal for adding logos, serial numbers, or intricate designs with high accuracy. Unlike traditional methods, laser etching and engraving use no chemicals or consumables, making them more environmentally friendly.
Advantages of Laser Etching and Engraving:
- High Precision: Laser technology allows for extremely fine details and patterns, ensuring a high level of accuracy that is not possible with traditional methods.
- Permanent Markings: The markings created by laser etching are permanent and resistant to wear, making them ideal for applications requiring durability.
- Customization: Laser etching allows for detailed customization, such as personalized engraving or logo marking, making it a popular choice for promotional items or products requiring identification.
- Non-contact Process: Since laser etching is a non-contact process, it eliminates the risk of surface damage caused by physical contact, ensuring the integrity of the aluminum fittings.
Electronics, jewelry, and consumer goods widely use laser etching and engraving, where precision and customization are key.
Electroless Plating
Electroless plating is a process that deposits a metal coating onto aluminum fittings without the use of an electric current. Unlike electroplating, which requires an electrical charge, electroless plating relies on a chemical reaction to deposit a metal layer. The most common metals used in electroless plating for aluminum are nickel and copper. This treatment is highly effective in providing uniform coverage and increased corrosion resistance.
Advantages of Electroless Plating:
- Uniform Coating: Electroless plating provides a uniform metal layer over the entire surface of the aluminum fitting, regardless of its shape or size.
- Improved Wear Resistance: This process increases the wear resistance of the aluminum surface, making it more suitable for high-traffic or mechanical applications.
- Enhanced Corrosion Resistance: Electroless nickel plating, in particular, offers excellent corrosion protection, especially in harsh environments such as marine or chemical applications.
- No Need for Electrical Current: Since electroless plating doesn’t require electricity, it can be applied to non-conductive materials as well, making it versatile in different applications.
ndustries like automotive, aerospace, and electronics often use electroless plating where uniformity, durability, and corrosion protection are critical.
Hot-Dip Galvanizing
The process of hot-dip galvanizing coats aluminum fittings with a layer of zinc to enhance corrosion resistance. The process dips the aluminum part in molten zinc, forming a strong bond that provides excellent rust and corrosion protection. Though commonly used for steel, hot-dip galvanizing can also protect aluminum fittings in outdoor environments.
Benefits of Hot-Dip Galvanizing:
- Superior Corrosion Protection: The zinc coating forms a durable, protective barrier against corrosion, especially in harsh environments like marine or industrial settings.
- Long-Lasting Finish: The galvanized finish provides long-term protection and requires minimal maintenance.
- Cost-Effective: Hot-dip galvanizing is an affordable surface treatment option, especially for large batches of aluminum fittings.
- High Durability: The zinc coating is highly durable and resistant to physical damage, making it ideal for items subjected to rough handling.
Hot-dip galvanizing is widely used in construction, infrastructure, and agriculture, where aluminum fittings face harsh environmental conditions.
Conclusion
Aluminum fitting surface treatments are essential for enhancing the material’s durability, corrosion resistance, and aesthetic appeal. Each surface treatment—anodizing, powder coating, electroplating, and others—serves a specific purpose based on the application. These treatments improve mechanical properties, provide unique finishes, and ensure aluminum fittings withstand the test of time while maintaining performance.
Choosing the right surface treatment depends on the fitting’s environment, appearance, and functional needs. By understanding each treatment’s benefits, manufacturers can ensure aluminum fittings perform at their best over time.
FAQs
1. What is the best surface treatment for aluminum fittings used outdoors?
The best surface treatment for aluminum fittings used outdoors depends on the environmental conditions they will face. For maximum corrosion resistance, anodizing and powder coating are excellent options. Both treatments offer enhanced durability and protection against the elements, with powder coating providing more flexibility in color choices. Chromate conversion coating is also a good choice for applications requiring both corrosion resistance and the ability to apply additional coatings, such as paints.
2. Can aluminum fittings be both anodized and powder coated?
Yes, aluminum fittings can undergo both anodizing and powder coating processes. However, it is important to understand that anodizing creates a porous oxide layer on the aluminum surface, which can affect the adhesion of the powder coating. Typically, anodizing is done first to enhance corrosion resistance, followed by powder coating for additional durability and aesthetic appeal.
3. How does anodizing differ from electroplating?
Anodizing and electroplating are both surface treatments that provide aluminum with added protection, but they differ in their methods. Anodizing involves an electrochemical process that thickens the oxide layer on aluminum, providing corrosion resistance and a matte finish. Electroplating, on the other hand, involves applying a thin metal coating, such as nickel or chrome, to the surface of the aluminum, enhancing its appearance, wear resistance, and corrosion protection.
4. Is powder coating a good option for aluminum furniture?
Yes, powder coating is an excellent option for aluminum furniture, particularly for outdoor use. It provides a durable, long-lasting finish that resists scratches, fading, and corrosion, making it ideal for aluminum furniture exposed to the elements. The powder coating process also offers a wide range of colors and finishes, allowing for both functional and aesthetic customization.
5. How long does the anodizing process last on aluminum fittings?
The lifespan of anodized aluminum fittings largely depends on the thickness of the anodized layer and the environmental conditions. In general, anodized aluminum can last many years with proper care, with the finish maintaining its corrosion resistance and appearance. For aluminum exposed to harsh conditions, thicker anodized coatings can provide enhanced durability, potentially lasting 20 years or more before showing signs of wear.