Introduction
Ball valves are widely used in residential plumbing, commercial HVAC systems, and high-pressure industrial applications. Their popularity stems from their straightforward design, reliability, and fast quarter-turn operation. However, one critical challenge for users and technicians alike is determining whether a ball valve is in the open or closed position—especially when safety and operational efficiency are on the line.
This comprehensive guide is designed to eliminate any confusion by explaining how to instantly identify a ball valve’s open position. We’ll break down the mechanics, visual and tactile indicators, and even explore how modern innovations are making valve position identification easier than ever before.
What is a Ball Valve?
Definition and Operational Concept
A ball valve is a shut-off valve that uses a hollow, perforated, and pivoting ball to control flow through it. When the ball’s hole is aligned with the flow, the valve is open. When rotated 90 degrees by the valve handle, the hole is perpendicular to the flow path, stopping all fluid or gas movement.
Function and Purpose
Ball valves offer a reliable and robust method of flow control in systems that require quick shutoff or unrestricted flow. Due to their tight sealing capabilities and minimal pressure drop, they are suitable for:
- Domestic water and gas piping
- Oil and gas processing
- Chemical and pharmaceutical manufacturing
- HVAC applications and compressed air systems
Anatomy of a Ball Valve
Core Components
To understand how to detect whether a ball valve is open, it’s essential to understand its internal and external components:
- Valve Body: The casing that houses all internal components and connects to the piping system.
- Rotary Ball: A spherical ball with a bore (hole) that rotates to control flow.
- Stem: A shaft that connects the ball to the handle and allows for manual or automated rotation.
- Handle or Lever: Used to manually rotate the ball; its alignment usually indicates the valve’s position.
- Seats and Seals: Ensure tight shutoff and prevent leaks around the ball and stem.
Flow Control Mechanism
Ball valves typically require only a 90-degree turn from open to closed. The bore inside the ball allows flow when aligned with the pipeline and completely blocks it when turned perpendicularly. This makes ball valves especially useful for applications where quick shutoff is necessary.
How to Identify the Open Position
Handle Alignment: The Most Reliable Indicator
The quickest and most universally accepted way to determine whether a ball valve is in the open position is by observing the orientation of the handle relative to the pipeline:
- Open Position: The handle is parallel to the pipe. This alignment indicates that the bore inside the ball is aligned with the flow path, allowing unrestricted fluid or gas movement.
- Closed Position: The handle is perpendicular to the pipe. This means the bore is crosswise to the flow path, effectively blocking it.
Most ball valves are designed so that the position of the handle provides a direct visual cue of the ball’s orientation, minimizing guesswork.
Quarter-Turn Operation and Visual Confirmation
Ball valves are known for their quarter-turn (90-degree) operation. A simple 90-degree twist changes the valve from fully open to fully closed. If you are unsure of the orientation, try this simple method:
- Note the current handle position.
- Turn the handle 90 degrees and observe the change.
- Return it to the initial position to restore the original state.
In well-maintained systems, this can quickly confirm whether you were starting from an open or closed state.
Visual and Tactile Indicators
Built-In Position Markings
Many ball valves, especially those used in industrial and commercial settings, come equipped with visual indicators such as:
- Engraved Arrows: Showing flow direction and alignment.
- Color-Coded Handles: Green often denotes “open,” while red signifies “closed.”
- Position Tabs or Flags: Mounted on top of the handle to display valve status from a distance.
Transparent and Color-Coated Bodies
Some specialty valves, especially those used in water treatment or lab settings, are made with transparent housings or visible ball components. This allows you to actually see whether the bore is aligned with the flow path.
Tactile Feedback from Handle Movement
If visual indicators are unclear or missing, and it’s safe to do so, tactile feedback can be invaluable:
- Freely Rotating Handle: Usually indicates no pressure on the ball, suggesting an open state.
- Resistance During Turn: Often felt when moving from open to closed due to compression of internal seals.
- Hard Stop: Signifies the valve has reached its operational limit—either fully open or fully closed.
Differences Between Open and Closed Position
Flow Characteristics
The core functional difference between the open and closed positions of a ball valve lies in how the internal bore allows or restricts movement of media:
- Open Position: Media flows directly through the bore with little resistance. This is ideal for operations requiring maximum flow rate and minimal pressure drop.
- Closed Position: The ball’s solid side faces the flow, completely obstructing passage. This ensures a tight shutoff, useful in isolating sections of the system.
Auditory and Pressure-Based Cues
While not always reliable, experienced technicians may use the following cues as supplementary indicators:
- Sound: A faint whoosh or hum of moving fluid usually confirms an open valve. Silence may suggest it’s closed.
- Pressure Gauges: A drop in downstream pressure usually indicates an open valve. Constant upstream pressure without change suggests closure.
Safety and Diagnostic Implications
Misidentifying the position can lead to serious issues including backflow, overpressure, or unintentional release of hazardous substances. That’s why it’s crucial to use a combination of visual, tactile, and system-based indicators when determining valve status.
Types of Ball Valve Handles and Indicators
Standard Lever Handle
The most common and intuitive type of handle used in ball valves is the lever handle. It offers clear and immediate feedback about the valve’s status:
- Parallel to the pipeline: Valve is open
- Perpendicular to the pipeline: Valve is closed
Standard lever handles are ideal for quick visual checks and are prevalent in residential, light commercial, and utility installations.
T-Handle and Round Handle Designs
Where space is limited or aesthetics are a factor—such as in tight mechanical rooms or decorative installations—T-handles or round handwheels may be used. These require a bit more familiarity since their alignment is less intuitive than lever handles. Users must check the stem orientation or built-in indicators to confirm position.
Locking Handles and Tamper-Resistant Designs
Industrial and high-security environments often require locking handles to prevent unauthorized operation. These typically feature:
- Padlock holes for lockout/tagout procedures
- Spring-loaded mechanisms that automatically return to a default position
- Shielded handles to prevent accidental actuation
When working with these types of valves, always refer to site-specific safety protocols and consult valve schematics where available.
Mechanical and Electronic Position Indicators
High-end valves used in process automation systems often incorporate indicators such as:
- Mechanical flags that rotate with the valve stem
- LED status lights showing open/closed condition
- Digital readouts for remote monitoring and integration into SCADA systems
Common Mistakes and Misinterpretations
Assuming Visual Cues Are Always Accurate
One of the most common user errors is assuming that the handle always represents the ball’s internal orientation. While this is true for most standard designs, certain conditions can lead to misinterpretation:
- Loose or detached handles may rotate independently of the ball
- Worn or corroded stem mechanisms can cause a lag between handle movement and ball rotation
- Retrofit or modified valves may not follow standard alignment conventions
Over-reliance on Partial Turns
Operators sometimes believe the valve is “open enough” or “closed enough” based on partial handle movement. This can lead to:
- Increased turbulence and pressure drop
- Wear on internal components not designed for throttling
- Leaks or pressure imbalances in sensitive systems
Neglecting Manufacturer Markings
Many valves are marked with stamped arrows or alphanumeric codes to indicate flow direction, pressure limits, and handle alignment references. These are frequently ignored or go unread due to paint, grime, or lack of training. A best practice is to clean and inspect all markings before operation.
Safety Considerations
Always Depressurize the System Before Inspection
Attempting to turn or inspect a valve under pressure can lead to serious injury or system damage. Before interacting with a ball valve:
- Shut off upstream pressure where possible
- Vent trapped pressure in the line
- Use drain ports or bypass valves to ensure a safe condition
Personal Protective Equipment (PPE)
Depending on the type of media being controlled, appropriate PPE is essential:
- Gloves to protect from heat, chemicals, or sharp edges
- Goggles or face shields to guard against fluid sprays
- Coveralls or flame-resistant gear in industrial or chemical applications
Follow Manufacturer and Site Protocols
Each ball valve model may have unique maintenance, operation, or positioning requirements. Always consult the manufacturer’s datasheet and comply with internal site safety policies, especially when working in regulated environments like chemical plants, food processing lines, or cleanrooms.
Maintenance Tips for Ball Valves
Regular Visual Inspection
Routine inspections are the first line of defense against valve failure. Check the following during scheduled maintenance:
- Handle Integrity: Ensure the handle is securely attached and operates without play.
- Body and Seals: Inspect for corrosion, leaks, or wear around the stem and body seals.
- Position Markings: Confirm that all visual indicators are legible and correctly aligned.
Lubrication and Internal Cleaning
Ball valves in high-debris or corrosive environments benefit greatly from regular lubrication. Use manufacturer-approved lubricants compatible with system media. For valves exposed to sediment or buildup:
- Flush the valve periodically using system-compatible solvents
- Remove debris that may obstruct the ball or seating surfaces
Be cautious not to over-lubricate, especially in potable water systems or sensitive applications.
Seal and Seat Replacement
Over time, internal seats and seals can degrade due to pressure, chemical exposure, or repeated cycling. Signs it’s time to replace them include:
- Leaks when the valve is fully closed
- Resistance or grinding when turning the handle
- Difficulty achieving full open or closed positions
Many modern ball valves feature replaceable cartridges, making maintenance more efficient and less costly over time.
Ball Valve Open Position in Industrial Settings
Process Control and Safety Protocols
In industrial applications, ball valve position is more than an operational concern—it’s a critical safety factor. An incorrectly positioned valve can cause:
- Equipment damage from overpressure
- Product loss or contamination
- Serious injury in pressurized or toxic systems
For this reason, facilities often implement visual status boards, digital position indicators, or even automated valve interlocks to verify valve state in real-time.
Integration with SCADA and PLC Systems
Supervisory Control and Data Acquisition (SCADA) and Programmable Logic Controllers (PLCs) allow operators to monitor and control valves remotely. Smart valves outfitted with:
- Proximity sensors can confirm the open or closed position electronically
- Feedback loops can automate corrective actions in response to system data
- Historical logs can track valve performance and failure trends
This level of control not only boosts efficiency but also helps detect early signs of mechanical failure.
Environmental Compliance and Reporting
In industries like pharmaceuticals, oil & gas, and food production, regulatory bodies require detailed records of valve positions during critical operations. Digital tracking and automated logging tools ensure compliance with:
- EPA emissions standards
- OSHA safety protocols
- FDA clean manufacturing requirements
Ball Valve vs. Other Valve Types
Gate Valves
Gate valves operate by lifting a gate out of the fluid path. While they offer full-flow capabilities when fully open, they are not as quick or intuitive to operate as ball valves.
- Speed: Requires multiple turns to open/close
- Maintenance: More susceptible to seat wear and buildup
- Position Indication: No clear external cue for open/closed status
In contrast, a ball valve’s quarter-turn handle provides immediate visual feedback and faster operation.
Globe Valves
Globe valves are designed for throttling rather than on/off control. Their internal structure provides better flow regulation but also introduces higher pressure drops.
- Precision: Excellent for modulating flow
- Complexity: More moving parts and maintenance overhead
- Speed: Slower to operate than ball valves
For applications needing simple shutoff with minimal flow resistance, ball valves are typically superior.
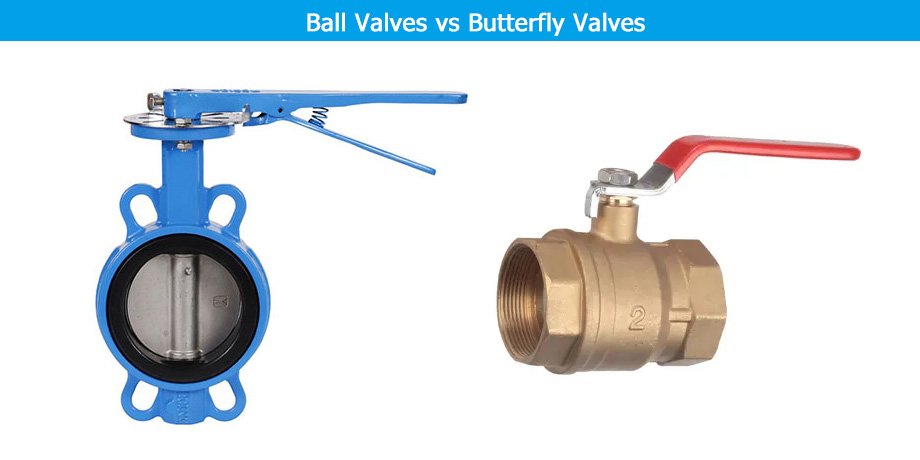
Butterfly Valves
Butterfly valves use a rotating disc to regulate flow. While useful in large-diameter pipes, they do not offer the same level of sealing as ball valves.
- Size Advantage: Compact and lightweight for large systems
- Seal Integrity: Less reliable in high-pressure environments
- Position Visibility: Often includes an indicator but may not be as intuitive as lever alignment
Ball valves remain the go-to choice when tight shutoff and fast operation are priorities.
Troubleshooting Guide
Valve Won’t Turn
This could result from corrosion, sediment buildup, or a seized stem. Steps to resolve:
- Apply penetrating lubricant to the stem
- Gently work the handle back and forth—avoid using excess force
- If stuck, disassemble and inspect for internal rust or mineral buildup
Valve Leaks When Closed
This is often a sign that internal seats or seals have worn out. To address:
- Disassemble the valve and inspect the seating surfaces
- Replace O-rings and seats as needed (many models offer seal kits)
- Check for cracks or corrosion in the ball itself
Handle Spins Freely with No Flow Control
This usually indicates a disconnected or broken stem. The internal connection between the handle and ball may be compromised. Corrective steps:
- Disassemble to verify if the stem is stripped or broken
- Replace the stem or the entire valve assembly depending on damage extent
- Avoid future issues by using valves rated for the correct pressure and torque
Environmental Factors Affecting Valve Position
Freezing Temperatures
Exposure to freezing conditions can cause water inside the valve to expand, potentially seizing the mechanism or cracking internal parts. Preventive measures include:
- Insulating exposed valves
- Using heat tape or electric pipe heaters in cold climates
- Draining unused exterior lines during winter months
Corrosion and Chemical Exposure
Valves used in chemically aggressive or moist environments are prone to external and internal corrosion. Effects include:
- Degradation of handle and stem
- Loss of sealing integrity
- Stiff or frozen operation
Mitigation includes choosing corrosion-resistant materials like stainless steel or brass and conducting periodic anti-corrosion treatments.
Debris and Particulate Contamination
In unfiltered systems or older piping networks, debris can accumulate around the ball or within the seats. This can lead to:
- Partial closure despite full handle rotation
- Valve leaking even when fully shut
- Increased wear on the bore and seats
Installing upstream filters or screens and flushing the system regularly are good practices to minimize particulate issues.
Innovations in Valve Position Technology
Smart Ball Valves
Modern smart valves are revolutionizing how valve position is monitored and controlled. These advanced devices integrate sensors and communication modules to offer precise, real-time valve status. Key features include:
- Remote monitoring via mobile apps or control panels
- Automated actuation based on system data
- Self-diagnostics and failure alerts
Smart ball valves are particularly useful in critical systems where constant oversight is needed—like in pharmaceutical cleanrooms or petrochemical operations.
Integrated Position Sensors
Position sensors are embedded in the valve stem or housing and provide binary or analog output that reflects the valve’s orientation. These can be connected to:
- SCADA systems for live process tracking
- Building automation systems for HVAC control
- Data loggers for performance audits
This innovation is vital for compliance with safety and quality assurance regulations, especially in industries governed by ISO or FDA standards.
IoT and Cloud Integration
Internet of Things (IoT) platforms allow ball valves to be part of a broader smart infrastructure. Benefits include:
- Predictive maintenance alerts when wear thresholds are detected
- Cloud-based analytics to optimize system performance
- Multi-location control from centralized dashboards
Cloud integration ensures that even remote or unmanned installations maintain optimal valve functionality with minimal human intervention.
Conclusion
Understanding and identifying the open position of a ball valve is a foundational skill for anyone working with piping systems—whether in home plumbing, commercial buildings, or complex industrial operations. The key lies in visual cues like handle alignment, enhanced by tactile feedback and verified through modern technologies like sensors and smart controls.
From basic maintenance tips to troubleshooting failures and leveraging cutting-edge innovations, this guide equips you with a full-spectrum understanding of how to manage and verify ball valve operation effectively. When properly maintained and monitored, ball valves offer unmatched reliability, making them indispensable across industries.
FAQs
Q1: Can a ball valve be used to regulate flow instead of just open/close?
While it is technically possible to partially open a ball valve for flow regulation, it’s not recommended. The internal seats are not designed for throttling and may wear out prematurely or cause flow turbulence.
Q2: What should I do if my valve handle doesn’t align perfectly with the pipe?
This could indicate wear in the stem or misalignment during installation. Inspect internally to confirm whether the ball is in the correct position, and replace components if necessary.
Q3: How do I know if my ball valve is failing internally?
Symptoms of internal failure include leaks when closed, stiff handle movement, or inconsistent flow. Inspection may reveal worn seals, sediment buildup, or ball surface damage.
Q4: Are there specific codes or standards that govern ball valve installation?
Yes. Standards like ASME B16.34, API 608, and ISO 5211 define testing, pressure ratings, and installation best practices for various types of ball valves.
Q5: Can I replace just the handle of a ball valve if it’s damaged?
In many cases, yes—especially for threaded or bolt-on handles. However, ensure the replacement handle matches the valve model and torque rating to avoid operational errors.