What is a Butterfly Valve?
A butterfly valve is a type of flow control device commonly used to regulate or isolate the flow of fluids in various applications. Known for their unique disc-shaped closure mechanism, butterfly valves are lightweight, compact, and cost-effective. These valves are ideal for a wide range of applications in industries such as water treatment, oil and gas, chemical processing, and HVAC systems. Their streamlined design and efficient performance make butterfly valves a popular choice in applications requiring rapid shutoff and minimal leakage.
How Butterfly Valves Work in Fluid Control Systems
Butterfly valves operate by rotating a disc within the valve body to allow, restrict, or block fluid flow. The disc, connected to a rod or stem, pivots to create an adjustable opening for the fluid. When the disc is parallel to the fluid flow, the valve is fully open, allowing fluid to pass freely. When the disc is rotated perpendicular to the flow, it creates a seal to stop the flow entirely. This simple, quarter-turn design allows butterfly valves to be opened or closed quickly, enhancing efficiency in applications where precise flow control is necessary.
Key Components of a Butterfly Valve
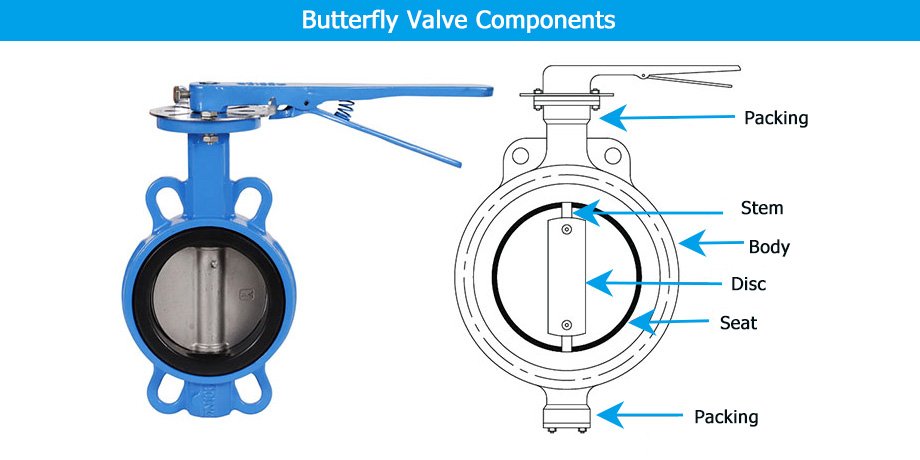
The Valve Body and Its Function
The body of a butterfly valve houses the valve’s internal components and serves as the main structure. It is designed to fit between pipe flanges and maintain a tight seal to prevent fluid leaks. The valve body is typically made from materials like stainless steel, cast iron, or other metals to ensure durability and withstand various pressure and temperature conditions.
The Disc: Control Element in Fluid Flow
The disc is the most critical part of the butterfly valve, as it directly regulates fluid flow. When positioned parallel to the flow, the disc allows for maximum fluid passage. When turned perpendicular, it blocks flow completely. Different disc designs and materials are available to optimize performance for specific applications, including slurries, chemicals, and corrosive fluids.
The Stem and Actuator Mechanism
The stem connects the actuator to the valve disc, allowing for rotation and movement. Depending on the type of butterfly valve, the stem may be a one-piece or two-piece design, and it may be manually or automatically controlled. Actuators, which are mechanical devices that turn the stem, provide the necessary force for opening and closing the valve, with options for electric, pneumatic, or hydraulic actuation based on application needs.
Seat and Seal: Ensuring Leak-Free Performance
The seat and seal components provide a tight fit between the valve body and the disc, preventing leaks when the valve is in the closed position. Typically, seats are made from soft materials like rubber or elastomers for flexibility, though metal-seated options are also available for higher-pressure applications. A quality seal is essential for maintaining operational efficiency and extending the life of the butterfly valve.
Types of Butterfly Valves
Concentric Butterfly Valves
Concentric butterfly valves, also known as resilient-seated butterfly valves, are the most common type. In these valves, the stem passes through the center of the disc, and the disc sits within a rubber-lined seat. This design is ideal for low-pressure applications, as the flexible seat provides a secure, leak-proof seal around the disc.
Double-Eccentric (High-Performance) Butterfly Valves
Double-eccentric or high-performance butterfly valves feature an offset stem, which reduces friction between the disc and seat. This design allows for greater durability and resistance to wear, making it suitable for higher pressure and temperature applications. Often used in industrial processes, high-performance butterfly valves offer improved sealing and longer service life compared to concentric designs.
Triple-Eccentric (Triple-Offset) Butterfly Valves
Triple-eccentric butterfly valves, also known as triple-offset valves, are designed for maximum efficiency in demanding applications. The three offsets in the design minimize contact between the disc and seat, reducing wear and enhancing the valve’s sealing capability. These valves are well-suited for critical applications requiring zero leakage, such as in oil and gas and chemical industries.
Wafer vs. Lug-Style Butterfly Valves
Butterfly valves come in wafer and lug-style configurations, which determine how the valve is mounted in the piping system. Wafer-style valves fit between two flanges and are held in place by the surrounding bolts. Lug-style valves have threaded inserts, allowing for easier maintenance and isolation of sections of piping without interrupting the entire system. Each style has its own advantages depending on installation and maintenance needs.
Common Applications of Butterfly Valves
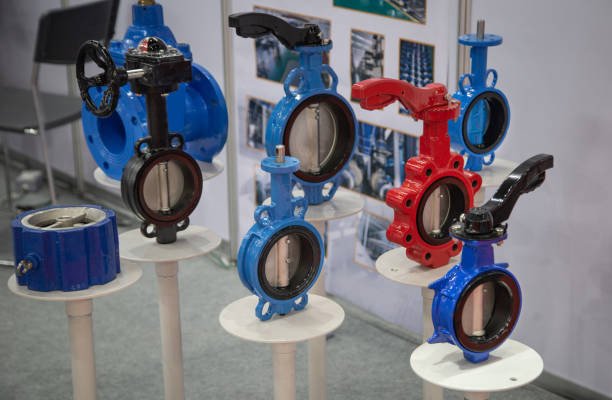
Industrial Applications in Water and Wastewater Treatment
Butterfly valves are widely used in water and wastewater treatment facilities for their ability to handle large volumes of fluid efficiently. They regulate water flow through treatment processes and manage the controlled release of wastewater. Their quick shut-off capability and cost-effectiveness make them a popular choice in municipal and industrial water systems.
Butterfly Valves in the Oil and Gas Industry
In the oil and gas sector, butterfly valves are utilized for isolating and regulating flow in pipelines. Their lightweight design and ability to operate in high-pressure and high-temperature environments make them suitable for a variety of applications, from oil extraction to refinery processes. Triple-offset butterfly valves, in particular, are used in critical applications due to their superior sealing capabilities.
Use in Chemical Processing and Power Generation
Butterfly valves are common in chemical plants where they control the flow of fluids, including corrosive chemicals, acids, and slurries. The choice of materials for the valve body, disc, and seat is crucial in these environments to ensure resistance to corrosion and chemical degradation. Power plants also rely on butterfly valves for efficient and reliable flow control in cooling systems, steam regulation, and other operations.
HVAC Systems and Building Management
In HVAC systems, butterfly valves are essential for controlling air and water flow in heating and cooling applications. They help regulate temperature and improve energy efficiency in buildings. Butterfly valves are also used in fire protection systems to manage water flow and maintain safety standards in building management systems.
Advantages of Using Butterfly Valves
Cost-Effectiveness Compared to Other Valve Types
Butterfly valves are generally more affordable than other valve types, such as ball or globe valves. Their simple design requires fewer materials and manufacturing processes, which helps lower costs. This cost-effectiveness, combined with reliable performance, makes them a popular choice across various industries.
Lightweight and Compact Design
Unlike many other valves, butterfly valves have a lightweight and compact construction, making them easier to install and handle. This design is particularly advantageous in large-scale operations where reducing the weight and space of equipment is crucial. Their compact size also allows for installation in tighter spaces.
Easy Installation and Minimal Maintenance
Butterfly valves are straightforward to install, often requiring fewer bolts and support structures. Additionally, their simple design results in minimal maintenance requirements. With proper routine checks, these valves can function effectively for long periods without the need for extensive upkeep, making them a low-maintenance solution.
Efficient Flow Control for Various Applications
Butterfly valves provide excellent flow control capabilities, allowing operators to adjust fluid flow quickly and accurately. Their ability to function well across a range of pressures and temperatures enhances their versatility, making them suitable for everything from low-pressure HVAC systems to high-pressure industrial pipelines.
Disadvantages and Limitations of Butterfly Valves
Potential for Leakage and Solutions
While butterfly valves offer efficient flow control, they can be prone to leakage if not properly maintained or if the seals and seats degrade over time. Choosing high-quality seals and seats and conducting regular maintenance can reduce leakage issues. For critical applications, triple-offset butterfly valves are recommended for their enhanced sealing capabilities.
Pressure Handling Capabilities Compared to Other Valves
Butterfly valves may not handle extremely high pressures as well as other valve types, such as globe or gate valves. For low- to medium-pressure applications, they perform well, but they may not be suitable for high-pressure systems unless using high-performance or triple-offset designs specifically built for those conditions.
Factors to Consider in Valve Selection
When selecting a butterfly valve, it’s important to consider factors such as the type of fluid, temperature, pressure conditions, and flow control requirements. While butterfly valves are highly versatile, certain applications may demand alternative valve types. Evaluating these factors ensures the chosen valve will meet performance and durability expectations for the specific application.
Key Differences Between Butterfly Valves and Other Valve Types
Butterfly Valves vs. Ball Valves
Both butterfly and ball valves are used to control fluid flow, but they operate differently. While butterfly valves use a rotating disc to open and close, ball valves use a spherical ball with a hole through its center. Ball valves typically offer a tighter seal and can handle higher pressures, whereas butterfly valves are lighter and more compact, making them ideal for applications requiring space efficiency.
Gate Valves vs. Butterfly Valves
Gate valves control fluid flow by raising or lowering a gate, which provides a straightforward shut-off mechanism. They are often used in applications where the valve will remain either fully open or closed. Butterfly valves, on the other hand, are better suited for applications that require frequent adjustment, as they allow for faster opening and closing with minimal effort.
Globe Valves and Their Comparison with Butterfly Valves
Globe valves are typically used for regulating flow and pressure in systems that require precise control. They offer superior throttling capabilities but tend to be larger and more expensive than butterfly valves. Butterfly valves are preferred in applications where cost, size, and fast actuation are primary considerations, though globe valves may be better suited for high-precision flow control.
Materials Used in Butterfly Valve Manufacturing
Stainless Steel and Corrosion Resistance
Stainless steel is a common choice for butterfly valves due to its durability and resistance to corrosion. It’s especially suitable for applications where the valve will be exposed to corrosive fluids or harsh environmental conditions. Stainless steel valves are often used in chemical processing, food and beverage, and marine industries.
Carbon Steel for High-Pressure Applications
Carbon steel is another popular material for butterfly valves, particularly in high-pressure applications. It is known for its strength and toughness, making it ideal for handling higher pressures and temperatures. Carbon steel valves are widely used in oil and gas, power generation, and industrial applications.
Polymer-Coated and Elastomer Options
Polymer coatings and elastomer seats are used in butterfly valves to enhance sealing and resist wear in applications involving abrasive or chemically aggressive fluids. Elastomer materials like EPDM, NBR, and Viton® offer flexibility and provide a tight seal around the valve disc, making them a suitable choice for water treatment and wastewater management.
Choosing the Right Butterfly Valve for Your Needs
Assessing Application Requirements
Choosing the correct butterfly valve starts with understanding the specific requirements of your application, including the type of fluid, pressure, temperature, and flow control needs. These factors will determine the appropriate valve type, material, and size to ensure reliable performance and longevity.
Flow Control and Pressure Conditions
Different butterfly valves are designed to handle various pressure levels and flow control requirements. For low- to moderate-pressure applications, a concentric butterfly valve may be sufficient. In high-pressure environments, consider using high-performance or triple-offset butterfly valves, which offer enhanced sealing and durability.
Choosing the Right Valve Material
The choice of valve material is critical to avoid corrosion, wear, and premature failure. Stainless steel is ideal for corrosive environments, while carbon steel is better suited for high-pressure applications. For chemical handling, consider a valve with a polymer-coated or elastomer seat to ensure compatibility with the fluid being managed.
How to Install a Butterfly Valve
Step-by-Step Guide to Valve Installation
Proper installation of a butterfly valve is crucial for ensuring its optimal performance and longevity. Start by positioning the valve between the flanges, ensuring the disc is in a slightly open position to prevent damage during installation. Align the bolt holes with the flanges, and tighten bolts evenly in a cross-pattern to ensure a tight seal. Avoid over-tightening, as it could damage the valve seat.
Common Mistakes to Avoid During Installation
Avoid common installation errors like misalignment, which can cause the valve to leak or operate improperly. Another mistake to avoid is over-tightening the bolts, which can warp the seat or disc. Always check the manufacturer’s instructions for specific torque recommendations to prevent damage.
Maintenance Tips for Butterfly Valves
Routine Inspection Checklist
Routine inspection is key to ensuring the reliability and longevity of butterfly valves. Regularly check for signs of wear on the disc, seat, and seals, and ensure that the valve operates smoothly. Look for corrosion, especially in harsh environments, and monitor any buildup that could hinder the valve’s function.
Common Issues and Troubleshooting
Common issues with butterfly valves include leaks, difficulty turning the disc, and wear on the seat. Leaks can often be addressed by tightening the bolts or replacing worn seals. If the disc is hard to turn, check for debris or buildup around the disc and stem, and clean as needed. Regular lubrication can also help maintain smooth operation.
Extending the Valve’s Lifespan with Proper Care
To extend the life of a butterfly valve, establish a regular maintenance schedule that includes lubrication, cleaning, and periodic inspection. Replace worn parts promptly to prevent further damage. For valves used in high-corrosion or high-temperature environments, consider protective coatings and regular performance monitoring.
Emerging Trends and Innovations in Butterfly Valve Technology
Automation in Butterfly Valves for Remote Control
Automation is increasingly being integrated into butterfly valves, allowing for remote control and monitoring in industrial settings. Actuators equipped with smart technology enable operators to adjust flow control remotely, monitor valve performance, and receive alerts for maintenance, enhancing both safety and efficiency.
Self-Cleaning Features and Longer Lifespans
Some butterfly valves now feature self-cleaning mechanisms that reduce the accumulation of debris around the disc and stem, helping to extend the valve’s operational life. These innovations are particularly beneficial in applications with high particle loads, like wastewater treatment, where sediment buildup can interfere with functionality.
Improved Material Design for Corrosion Resistance
Advances in materials science have led to new coatings and composite materials that enhance corrosion resistance. Polymer coatings and advanced alloys help butterfly valves withstand harsher conditions, such as high temperatures and corrosive chemicals, thereby extending valve life and improving reliability.
FAQs
How Long Do Butterfly Valves Last?
With proper maintenance and suitable materials for the application, butterfly valves can last up to 15-20 years or more. However, lifespan varies depending on the valve’s environment, pressure, temperature, and frequency of use.
Can Butterfly Valves Be Used for Slurries and Sludge?
Yes, butterfly valves can handle slurries and sludge, particularly in wastewater treatment and industrial applications. However, using a valve with suitable materials and a robust seal is important to withstand abrasive particles and prevent leaks.
What Makes Butterfly Valves More Efficient Than Other Valves?
Butterfly valves are known for their compact size, lightweight construction, and quick quarter-turn operation. These features make them efficient for fast shut-off and flow control, especially in applications where space and cost efficiency are essential.
Are Butterfly Valves Suitable for High-Pressure Applications?
High-performance and triple-offset butterfly valves are designed for moderate to high-pressure applications, but traditional concentric butterfly valves may not be suitable for extreme pressures. Always check pressure ratings and specifications for the best performance in high-pressure settings.
What Maintenance is Required for Butterfly Valves?
Regular maintenance includes routine inspections for wear, cleaning around the disc and stem, lubrication of moving parts, and checking for leaks. Replacing worn seals and seats promptly can also extend the valve’s lifespan and ensure reliable performance.