Check valves are essential components in various systems where fluid flow needs to be controlled and maintained in one direction only. By automatically preventing backflow, check valves ensure that fluids and gases flow safely and efficiently without reversing direction, which could cause damage or system malfunction. Whether in water treatment, oil pipelines, or HVAC systems, the presence of a reliable check valve is crucial to the smooth operation of industrial systems.
In this guide, we will explore the fundamentals of check valves, how they function, the different types available, their applications, and why they are important in maintaining system integrity and efficiency.
How Check Valves Work
Check valves operate by utilizing the pressure of the fluid to open and close a valve mechanism. The main function of a check valve is to prevent backflow, ensuring that fluid flows in only one direction. When the pressure in the line exceeds the preset pressure of the valve, it opens, allowing fluid to pass through. When the pressure decreases, the valve automatically closes, blocking any reverse flow.
The operation of a check valve depends on the type of valve and the internal mechanism. Common types include swing, ball, and lift check valves, each with different designs and modes of action. However, the core purpose remains the same: to prevent the fluid from flowing backward into the system, which could cause contamination, damage to equipment, or reduce efficiency.
The Basic Mechanism
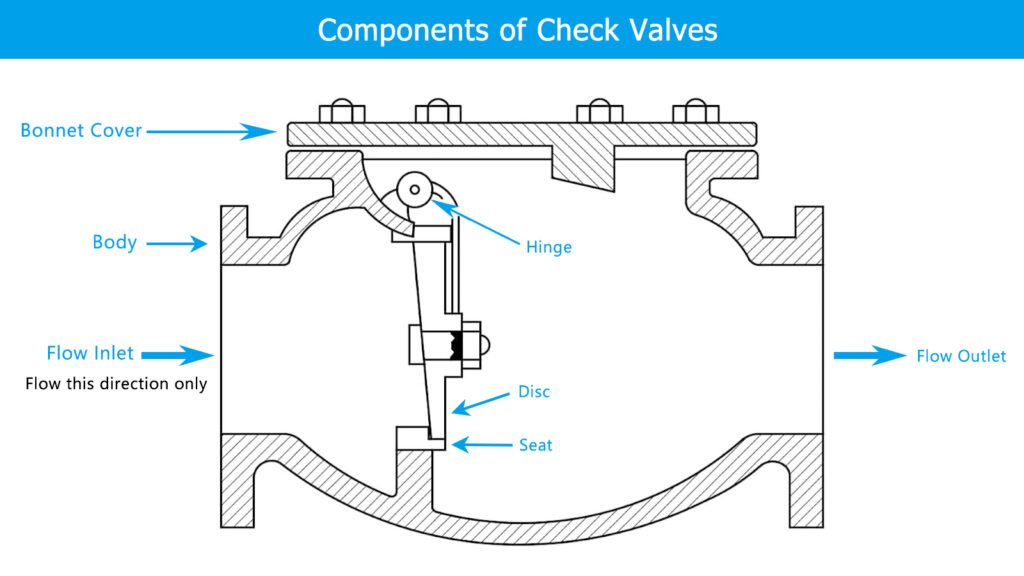
Check valves are designed to be as simple as possible, with a one-way mechanism that operates automatically. They typically consist of a body, a seat, and a disc or ball that controls the flow. When fluid moves in the intended direction, the pressure forces the disc or ball away from the valve seat, allowing the fluid to pass. When flow reverses, the disc or ball is pushed back against the seat, closing the valve and preventing backflow.
Understanding Flow Direction and Functionality
In a check valve, the flow direction is critical. Most check valves are installed with a marked direction of flow, as the valve will only function correctly when the flow direction aligns with this marking. If installed backward, the valve will not close properly, leading to potential damage to the system and reduced operational efficiency. Therefore, proper installation is key to ensuring the valve performs its intended role effectively.
Types of Check Valves
There are several types of check valves, each suited to different applications and operational needs. Below are some of the most common types:
Swing Check Valve
A swing check valve has a hinged disc that swings open and closed based on fluid pressure. It is widely used in low-flow applications and systems where backpressure is not a concern. Swing check valves are simple in design and are often used in pipelines that carry water or low-viscosity fluids.
Ball Check Valve
The ball check valve uses a ball that moves to open and close the valve. It is effective for use in systems with high-pressure conditions, such as oil or gas pipelines. The ball seals against the seat to prevent backflow, making it a reliable choice in industries requiring high performance.
Lift Check Valve
Lift check valves operate similarly to swing check valves, but instead of swinging, the valve’s disc lifts off the seat. These valves are typically used in higher-pressure and vertical applications, such as in water treatment plants and steam systems, where compact designs are needed.
Piston Check Valve
Piston check valves use a piston that moves in response to fluid pressure to open or close the valve. These valves are suitable for high-pressure applications, such as in large industrial systems, and provide a more precise and reliable sealing mechanism than other types of check valves.
Diaphragm Check Valve
Diaphragm check valves use a flexible diaphragm to regulate flow. These valves are used in systems where hygiene and cleanliness are critical, such as in pharmaceutical or food processing industries. The diaphragm’s flexibility ensures tight sealing, making it ideal for preventing contamination in sensitive environments.
Dual Plate Check Valve
Dual plate check valves have two hinged plates that open and close based on fluid flow. This type is compact and is used in high-flow applications, such as in large pipelines. Dual plate check valves are designed to reduce the pressure drop and maintain system efficiency, making them ideal for larger industrial systems.
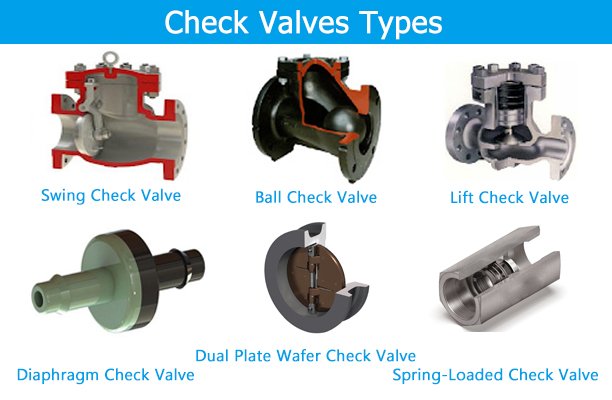
Choosing the Right Check Valve for Your Needs
Choosing the correct check valve for your application is crucial to ensure system reliability and efficiency. Several factors influence the selection process, including:
Factors to Consider: Pressure, Temperature, and Flow Rate
The pressure, temperature, and flow rate of your system are key factors when selecting a check valve. You should match the valve to the pressure requirements of the system, as well as the temperature ranges it will experience. Choosing the wrong valve for your system’s specifications can result in premature wear, leakage, or failure to perform as intended.
Material Selection for Check Valves
Check valves are available in a wide range of materials, including brass, stainless steel, plastic, and cast iron. The material should be chosen based on the type of fluid being handled, the pressure and temperature conditions, and the potential for corrosion or wear. For example, stainless steel valves are commonly used in high-pressure and corrosive environments, while plastic valves may be suitable for less demanding applications.
Common Applications by Industry
Check valves are found in numerous industries, each requiring specific types of valves for optimal performance:
- Water Treatment: Used to prevent backflow in pipelines and filtration systems.
- Oil & Gas: Essential in pipelines and drilling operations to protect equipment.
- Food & Beverage: Prevent contamination in sensitive systems, such as dairy or brewing systems.
- HVAC: Used in heating, ventilation, and air conditioning systems to maintain consistent flow and prevent reverse flow.
Applications of Check Valves
Check valves play a critical role in various systems where maintaining unidirectional flow is vital for safety, efficiency, and system longevity. Some of the most common applications of check valves include:
Water and Wastewater Systems
In water treatment plants and wastewater systems, check valves prevent backflow, which could lead to contamination of clean water supplies. These valves are commonly installed in pumps, pipelines, and filtration systems to protect both infrastructure and public health.
Oil and Gas Industry
Check valves are crucial in the oil and gas industry to prevent backflow from occurring in drilling operations and pipelines. They help ensure that pressurized oil or gas flows in the intended direction, reducing the risk of accidents and equipment damage.
Pharmaceutical and Food Processing
In the pharmaceutical and food processing industries, check valves ensure hygiene and prevent contamination. They help maintain sterile conditions in pipelines carrying ingredients or final products, preventing reverse flow that could introduce contaminants.
HVAC Systems
In HVAC systems, check valves prevent the backflow of fluids in the heating or cooling process, maintaining system efficiency and avoiding damage to sensitive components like compressors or pumps.
Marine and Offshore Engineering
Marine vessels and offshore platforms rely on check valves to protect critical systems, such as water cooling pumps, ballast systems, and fire suppression systems. These valves ensure that water and fluids flow in the correct direction, avoiding catastrophic failures in harsh environments.
Benefits of Using Check Valves
Check valves offer numerous benefits that help to maintain system integrity and operational efficiency. Below are the main advantages of using check valves in various systems:
Preventing Backflow
The primary function of a check valve is to prevent backflow. By ensuring that fluid only moves in one direction, check valves protect systems from potential contamination, damage, or reverse pressure. In industries like water treatment and oil refining, backflow prevention is critical for maintaining safe and clean processes.
Protecting Pumps and Equipment
Check valves act as a safeguard for pumps and other sensitive equipment. If backflow occurs, it can damage pumps, motors, or other machinery, leading to expensive repairs and downtime. By preventing backflow, check valves ensure that pumps run efficiently and last longer, which saves money on maintenance costs in the long term.
Enhancing System Efficiency
By ensuring that fluids flow in the intended direction without interference, check valves enhance the overall efficiency of a system. They help maintain consistent pressure, reduce turbulence, and prevent system breakdowns, all of which contribute to smoother operations and less energy consumption.
Maintaining Fluid Quality
In many industries, such as pharmaceuticals and food processing, check valves help maintain the quality and purity of fluids. By preventing the reverse flow of contaminated liquids, check valves ensure that the integrity of the fluid is preserved throughout the system, which is especially important in sensitive production environments.
Common Issues and Troubleshooting in Check Valves
While check valves are durable and reliable, they are not immune to problems. Here are some common issues encountered with check valves, along with troubleshooting tips:
Common Problems in Check Valves
- Valve Leakage: Over time, seals or discs may wear out, causing leakage. This can be due to corrosion, debris buildup, or poor installation.
- Sticking or Jamming: Dirt, debris, or excessive wear can cause the valve to stick or jam, preventing it from closing properly.
- Inadequate Closure: In some cases, the valve may not close completely due to improper installation or damage, which can lead to backflow.
How to Identify Faulty Check Valves
If you suspect your check valve is malfunctioning, there are several signs to look out for:
- Backflow: If the valve is not closing properly, backflow may occur, leading to contamination or system failure.
- Noise: A noisy valve could indicate that it’s not sealing properly, which may cause vibrations and inefficient operation.
- Leaks: Visual leaks around the valve may signal that seals are worn out or there is a crack in the valve body.
Repairing vs. Replacing Check Valves
When a check valve starts to fail, you have two options: repair or replace. The decision depends on the extent of the damage and the type of valve. Minor issues like debris buildup or worn seals may be repaired, while more significant damage, such as cracks or structural failure, often necessitates replacement. In some cases, replacing the valve might be more cost-effective than attempting a repair, especially if the valve is old or has experienced significant wear.
Best Practices for Maintenance of Check Valves
Maintaining check valves is crucial to ensure long-term performance and avoid unexpected system failures. Below are some best practices for check valve maintenance:
Regular Inspections
Inspect your check valves regularly for signs of wear and tear, leaks, or misalignment. Timely inspections can help identify potential issues before they cause serious damage. Routine checks should be part of your regular maintenance schedule to ensure that all components are functioning properly.
Cleaning and Lubrication Tips
In some applications, check valves may accumulate dirt, debris, or scale, which can impair their function. Cleaning the valve periodically can help ensure smooth operation. For valves with moving parts, proper lubrication can also prevent excessive wear and reduce the risk of sticking or jamming.
When to Replace Check Valves
While regular maintenance can extend the lifespan of a check valve, there will come a time when replacement is necessary. If the valve exhibits signs of severe wear, such as cracks in the body, an inability to close properly, or persistent leakage, it is time to replace the valve to avoid system failure.
Choosing the Right Check Valve for Your System
Selecting the right check valve for your system involves considering various factors such as flow direction, pressure, and the type of fluid being handled. Here are some key points to keep in mind when choosing a check valve:
1. Fluid Characteristics
Consider the properties of the fluid being transported. For example, if the fluid is corrosive, you’ll need a check valve made of materials resistant to corrosion, such as stainless steel or plastic. Additionally, fluids with high particulate content may require a valve with a larger opening to prevent clogging.
2. Pressure and Temperature
The valve you choose must be rated to withstand the pressure and temperature conditions of your system. Ensure the check valve can handle the maximum pressure and temperature expected in the system without failing.
3. Valve Size and Flow Rate
Choose a check valve that matches the size of the pipe and the flow rate of the fluid. A valve that is too small will cause excessive pressure loss, while a valve that is too large will reduce the system’s efficiency.
4. Ease of Maintenance
Consider the ease of maintenance and whether the check valve can be easily cleaned or replaced if needed. Valves with accessible components are easier to maintain, reducing downtime and maintenance costs.
Conclusion:
Check valves are essential components in fluid systems, offering critical protection against backflow, system damage, and inefficiencies. By understanding the different types of check valves and selecting the right one for your system, you can ensure smooth, uninterrupted operation. Regular maintenance is key to maximizing the lifespan of these valves and minimizing the risk of failures. Whether you’re working in water treatment, oil and gas, or industrial manufacturing, investing in the right check valve for your system is crucial for long-term reliability and efficiency.
FAQs
What is the main function of a check valve?
The main function of a check valve is to allow fluid to flow in one direction only, preventing backflow that could damage equipment or contaminate systems.
How do I know if my check valve is malfunctioning?
Common signs of a malfunctioning check valve include backflow, noisy operation, leaks, or failure to close properly.
Can a check valve be repaired?
Yes, depending on the damage, a check valve can often be repaired by replacing seals, cleaning debris, or replacing minor parts.
What industries use check valves?
Check valves are used in industries such as water treatment, oil and gas, pharmaceuticals, food processing, and HVAC systems.
How do I choose the right check valve for my system?
Consider factors such as fluid characteristics, pressure, temperature, valve size, and flow rate when selecting a check valve for your system.