Imperial thread fittings are widely used in various industries due to their reliability and standardized measurements. However, many newcomers find the variety of thread diameters confusing when purchasing these fittings. In reality, selecting the right fitting isn’t difficult if you know the proper method. Today, let’s hear how to choose the right imperial thread fitting diameter from the fitting manufacturers.
Understanding the Impact of Diameter
First, it’s essential to understand that the diameter affects the strength and durability of the fitting. A diameter that’s too small increases the risk of fatigue fractures in the fitting, while a diameter that’s too large can cause the fitting to become loose. Therefore, selecting the appropriate thread diameter is crucial.
The thread diameter plays a significant role in determining the fitting’s overall performance. It’s not just about the size but also about how the diameter interacts with other components. For instance, in hydraulic systems, the fitting’s diameter can affect fluid flow rates and pressure levels, making it a critical factor in system efficiency and safety.
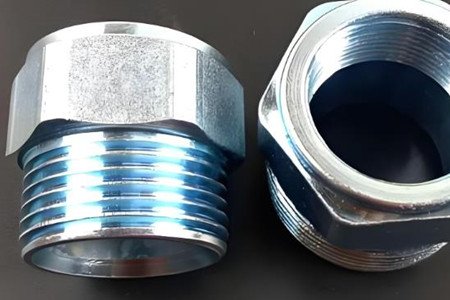
Manufacturer’s Insights on Choosing Imperial Thread Fitting Diameters
For most Imperial thread fittings, the thread pitch is a constant. Thus, with the same thread pitch, a larger thread diameter results in a greater fastening torque and more stable connection.
In other words, a larger diameter generates higher torque and contact stress. However, excessively large diameters can also impact performance, requiring a careful balance. Therefore, the diameter should be chosen based on actual needs.
When manufacturers design fittings, they consider the application environment and the specific requirements of the system. For example, in automotive applications, fittings must withstand high temperatures and pressures, necessitating robust designs with appropriate thread diameters. On the other hand, fittings used in residential plumbing might have different requirements, such as ease of installation and compatibility with existing systems.
Measuring Threads for Accurate Selection
Accurate measurement of thread diameter is crucial for ensuring a proper fit. Tools such as calipers and thread gauges are commonly used for this purpose.
- Calipers: Measure the outside diameter of the male thread or the inside diameter of the female thread.
- Thread Gauges: Used to determine the pitch of the thread, which is the distance between each thread.
High-Strength Environments
In high-strength environments, selecting a larger diameter can improve fastening strength and connection stability, allowing the fitting to withstand higher forces and weights. Larger diameters are often used in construction and heavy machinery, where the fittings must handle significant loads and resist loosening under vibration.
The choice of a larger diameter also provides additional safety margins, reducing the likelihood of failure in critical applications. For instance, in aerospace engineering, the reliability of fittings is paramount, and larger diameters can contribute to the overall integrity of the structure.
Small Machinery and Electronic Devices
Conversely, in small machinery and electronic devices, a compact design with a smaller diameter is preferable. In such cases, choosing a smaller diameter can reduce the net weight and volume of the connector, making it lighter.
In electronic devices, space is at a premium, and smaller fittings help maintain a sleek design without compromising functionality. These applications often require precision and minimal interference with other components, making the choice of diameter even more critical.
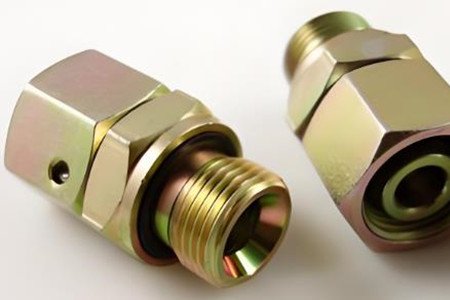
Material Considerations
The production material also significantly influences the thread diameter choice. For example, steel has high strength but is brittle, while aluminum and magnesium have lower strength. Surface treatments, such as coating stainless steel, can achieve higher hardness and strength values. Depending on the usage scenario, selecting different materials and diameters can result in optimal performance.
In corrosive environments, materials like stainless steel or specially coated alloys are preferred to enhance durability. The material’s compatibility with the operating environment ensures the longevity and reliability of the fittings.
Factors to Consider
When choosing the diameter of Imperial thread fittings, it’s important to consider the application environment, material, and testing standards in the industrial field. Specific requirements may vary across industries and fields.
For instance, in the food and beverage industry, fittings must comply with hygiene standards, which may influence the choice of materials and diameters. Similarly, in the medical field, fittings need to meet strict regulatory requirements, ensuring safety and performance under various conditions.
Conclusion
Selecting the correct diameter for Imperial thread fittings directly impacts the stability and reliability of the connection. The decision should not be based solely on price but should also take into account diameter size, usage conditions, production materials, quality, and service. After considering these factors comprehensively, you can choose a fitting that meets your needs. Fitting manufacturers can also provide professional technical support to help users select the right fitting.
Choosing the appropriate Imperial thread fitting diameter ensures stability, reliability, and safety. In the selection process, carefully consider all relevant factors to make an informed decision.
FAQs
What is the importance of thread diameter in imperial fittings?
Thread diameter affects the strength, durability, and overall performance of imperial fittings. It is crucial for ensuring a secure and stable connection.
How do manufacturers determine the appropriate thread diameter?
Manufacturers consider the application environment, system requirements, and specific industry standards when designing fittings with appropriate thread diameters.
What tools are used to measure thread diameter?
Common tools for measuring thread diameter include calipers for measuring outside and inside diameters and thread gauges for determining thread pitch.
Why are larger diameters used in high-strength environments?
Larger diameters provide increased fastening strength and stability, making them suitable for high-strength environments like construction and heavy machinery.
What considerations are there for small machinery and electronic devices?
In these applications, smaller diameters help maintain a compact design, reducing weight and volume while ensuring precision and minimal interference with other components.
How does material choice influence thread diameter selection?
The material’s properties, such as strength and compatibility with the operating environment, influence the selection of thread diameter to ensure optimal performance and durability.