Hydraulic systems play a critical role in powering equipment across industries—from agriculture and construction to manufacturing and logistics. Central to these systems are hydraulic hoses and couplers, which must be connected and disconnected with precision. Doing this properly ensures safety, minimizes downtime, and protects costly machinery from damage. In this guide, you’ll learn everything you need to know about safely connecting and disconnecting hydraulic hoses and couplers, step by step.
Understanding Hydraulic Hoses and Couplers
What Are Hydraulic Hoses?
Hydraulic hoses are high-pressure tubes made from reinforced rubber or thermoplastic material. These hoses are designed to carry hydraulic fluid to various parts of a hydraulic system, enabling force transmission, actuation, and movement. They are built to withstand harsh environments, extreme pressure, and constant motion.
What Are Hydraulic Couplers?
Hydraulic couplers—also known as quick couplers or quick disconnects—are devices used to connect and disconnect hydraulic lines quickly and easily. They come in male and female fittings that snap or twist together to ensure a secure, leak-free connection. Couplers facilitate maintenance, reduce downtime, and allow for quick equipment swaps.
Common Applications
Hydraulic hoses and couplers are used in numerous sectors:
- Agriculture: Tractors, harvesters, and tillage equipment
- Construction: Excavators, loaders, backhoes, and bulldozers
- Manufacturing: Presses, conveyor systems, and assembly lines
- Transport: Hydraulic brakes and lifting equipment
Importance of Proper Connection and Disconnection
Safety First
Improper handling of hydraulic connections can be extremely dangerous. High-pressure fluid can escape unexpectedly, leading to serious injuries such as injection wounds or burns. Always follow standardized safety procedures to minimize risk to personnel and equipment.
Efficiency and System Integrity
When hydraulic couplers are not properly attached, fluid leaks and pressure loss can occur. This affects the overall efficiency of the system and may lead to reduced performance or complete failure. Proper coupling ensures consistent fluid flow, reduces wear, and keeps the system sealed against contaminants.
Extending Equipment Life
Misaligned or worn-out connections lead to vibration, increased friction, and eventual damage. Consistently checking and properly handling hydraulic hoses and couplers helps extend the lifespan of both the hoses and the machinery they power.
Tools and Safety Gear You’ll Need
Before beginning any work involving hydraulic connections, gather the appropriate tools and personal protective equipment (PPE):
- Protective gloves: To prevent injury from high-pressure fluid or sharp edges
- Safety goggles: Protects your eyes from fluid spray or debris
- Clean, lint-free cloths: For wiping dirt, oil, and hydraulic fluid off connectors
- Spill containment tray: To manage any fluid that leaks during disconnection
- Hydraulic fitting tools: Such as spanner wrenches or torque wrenches for tightening or loosening couplers
- Dust caps and plugs: To cover open ends and prevent contamination during downtime
Having the right gear not only keeps you safe but also ensures the procedure goes smoothly and the equipment stays in top condition.
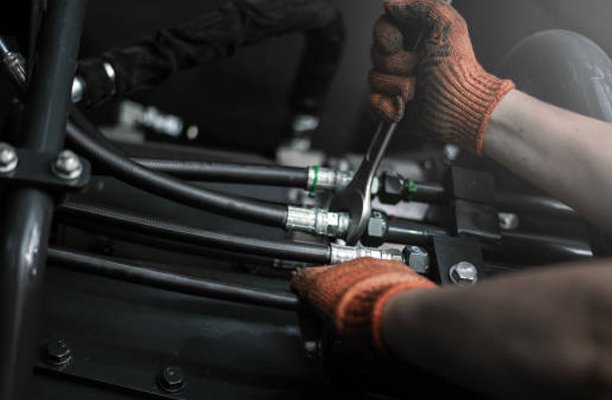
Step-by-Step Guide: Connecting Hydraulic Hoses
Step 1: Depressurize the System
Before touching any hydraulic components, ensure the system is completely turned off and depressurized. Failing to do so can result in high-pressure fluid spray, which poses a serious injury risk. Follow the equipment manufacturer’s guidelines for safely relieving hydraulic pressure—usually by moving the control levers or using a pressure release valve.
Step 2: Clean the Hose Ends and Couplers
Use a lint-free cloth to clean both the male and female coupler ends. Dirt, debris, or old hydraulic fluid can contaminate the system or cause a poor seal. Always ensure the fittings are free of rust, paint, or hardened residue.
Step 3: Inspect for Wear or Damage
Before connecting, carefully inspect the hoses and couplers for visible damage such as cracks, dents, worn-out O-rings, or corrosion. Replace any damaged components immediately to avoid leaks or system failure.
Step 4: Align and Attach the Couplers
Position the male and female coupler ends so they are aligned correctly. Depending on the coupler type (push-to-connect or threaded), either push firmly until you hear a click or twist until snug. Do not over-tighten, as this can damage threads or seals.
Step 5: Verify the Connection
Once connected, gently tug on the hose to ensure it is locked into place. Re-pressurize the system and monitor for any signs of leakage or abnormal operation such as hissing sounds or jerky movements.
Step-by-Step Guide: Disconnecting Hydraulic Hoses
Step 1: Shut Down and Depressurize the System
Just like during connection, make sure the equipment is fully powered down and the hydraulic pressure is relieved. This is a non-negotiable safety step. Check for pressure using the equipment’s gauges and use manual release methods if needed.
Step 2: Clean the Area Around the Coupler
Before disconnecting, wipe away any debris or fluid from around the coupler. This prevents dirt from entering the hydraulic system during disconnection and minimizes environmental contamination.
Step 3: Unlock the Coupler
Release the coupling mechanism according to the coupler type. For quick-release couplers, you may need to pull back the collar or rotate a locking sleeve. Do not force the connection—if it’s hard to remove, residual pressure may still be present.
Step 4: Cap and Seal the Ends
Immediately place dust caps and plugs on both the hose end and equipment port. This step is essential to prevent dirt, moisture, and air from contaminating the hydraulic fluid. Label and store hoses properly if they are to be reused later.
Common Mistakes to Avoid
Skipping the Depressurization Process
One of the most dangerous mistakes is attempting to connect or disconnect hydraulic hoses without fully relieving the system pressure. This can lead to hydraulic fluid injection injuries or component failure.
Forcing Misaligned Couplers
Forcing a connection between mismatched or misaligned couplers can damage threads, seals, and internal valves. Always align components carefully and use the correct type of coupler for the application.
Ignoring Wear and Tear
Using visibly worn or cracked hoses can lead to sudden bursts or leaks. Regular inspections should never be skipped, and damaged components should be replaced immediately.
Neglecting Dust Caps
After disconnecting hoses, failing to cover the ends can introduce dirt and moisture into the system, leading to contamination and internal wear. Always use proper sealing caps after disconnection.
Maintenance Tips for Longevity
Schedule Regular Inspections
Hydraulic hoses and couplers should be visually inspected on a regular basis—ideally every 3 months or before each heavy-use cycle. Look for wear patterns, abrasions, leaks, and corrosion. Pay special attention to O-rings, as these are common points of failure.
Replace Parts Proactively
Don’t wait until a hose bursts or a coupler fails to take action. Replace components at the first sign of fatigue or malfunction. Using parts beyond their service life invites unpredictable failures and costly downtime.
Store Hoses Correctly
When not in use, hydraulic hoses should be coiled loosely and stored in a dry, cool, and dust-free environment. Avoid exposure to direct sunlight, ozone, or chemicals that may degrade rubber or synthetic materials. Use storage racks or bins to prevent pinching or crushing.
Use the Right Hydraulic Fluid
Incorrect or contaminated hydraulic fluid can degrade hoses and couplers from within. Always use fluid recommended by the equipment manufacturer, and check for compatibility with seals and fittings. Replace fluid according to service schedules, and use high-quality filters to keep it clean.
Environmental & Workplace Safety Considerations
Prevent Hydraulic Spills
Hydraulic fluid is not only harmful to equipment—it’s also a potential environmental pollutant. When disconnecting hoses, always use a spill containment tray or absorbent mats. Wipe off residual oil and clean the area after completing the procedure.
Train Staff on Hydraulic Safety
Every operator, technician, and maintenance crew member should be trained on hydraulic safety procedures. Training should cover proper PPE use, how to relieve system pressure, how to identify coupling types, and how to respond to leaks or system failures.
Use Visual Labels and Hose Tags
Color-coded or numbered labels help personnel quickly identify hose functions, directions of flow, and safe coupling locations. This not only enhances safety but also minimizes human error during maintenance and reassembly.
Industry Standards & Compliance
Follow OSHA Guidelines
In the United States, OSHA (Occupational Safety and Health Administration) outlines clear rules for handling high-pressure hydraulic systems. These guidelines emphasize PPE, equipment guarding, pressure relief methods, and emergency shutdown protocols.
ISO Standards for Hydraulic Systems
The International Organization for Standardization (ISO) has developed standards such as ISO 4413, which covers safety requirements and best practices for hydraulic fluid power systems. Compliance ensures systems are designed, maintained, and operated in a safe and efficient manner.
Use Manufacturer-Approved Parts
Always use hoses, fittings, and couplers approved or recommended by the equipment manufacturer. Mismatched parts may not withstand the pressure levels or chemical exposure, which can void warranties and increase the risk of failure.
Troubleshooting Connection Issues
Issue: Couplers Won’t Connect
This often happens due to residual pressure trapped in the lines. Even after shutting off the machine, small pockets of hydraulic pressure may remain. Use the machine’s pressure relief valve or manually cycle the hydraulic control lever to release pressure before attempting to reconnect.
Issue: Leaking Connections
If you notice hydraulic fluid seeping from the coupling point, the issue could stem from a damaged O-ring, cracked threads, or improper alignment. Remove the connection, clean both ends thoroughly, and inspect the sealing surfaces. Replace damaged seals or couplers before reattempting.
Issue: Difficulty Disconnecting
Hydraulic couplers can become difficult to remove if the locking mechanism is jammed or if pressure has built up unexpectedly. Always depressurize before attempting disconnection. If stuck, use appropriate tools rather than forcing the parts apart by hand.
Issue: Unusual Noises or System Jerking
These symptoms typically indicate air trapped in the system or poor fluid flow due to a partially engaged or blocked coupler. Recheck the connection, fully engage the coupler, and inspect the fluid level and condition.
Choosing the Right Couplers for the Job
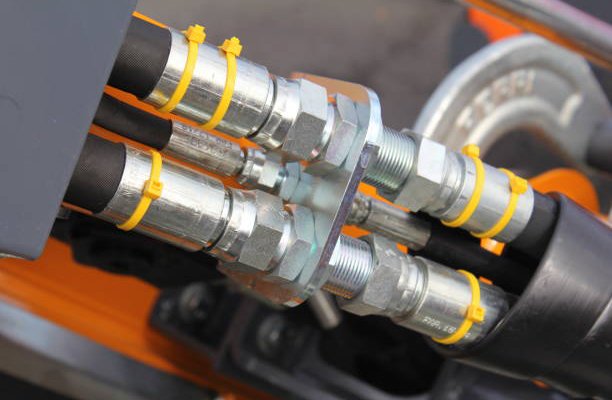
Know Your Coupler Types
Hydraulic couplers come in a variety of types, including:
- Flat Face Couplers: Minimize fluid loss and air inclusion, ideal for high-dirt environments
- Ball-Type Couplers: Common and cost-effective, suitable for general applications
- Push-to-Connect Couplers: Quick connection with a locking mechanism, perfect for frequent tool changes
Check Pressure and Flow Ratings
Always match the coupler to your hydraulic system’s specifications. Check the maximum working pressure (psi) and flow rate (GPM) to ensure compatibility. Using an underrated coupler can lead to dangerous failures under load.
Material Considerations
Different couplers are made from materials such as brass, stainless steel, or hardened steel. Choose based on the environment—e.g., stainless steel for corrosive or marine applications, or hardened steel for heavy-duty construction use.
Fluid and Seal Compatibility
Hydraulic fluid type plays a role in coupler selection. Make sure seals and internal components are compatible with the fluid’s chemical makeup—especially when using fire-resistant or biodegradable fluids.
When to Replace Hydraulic Hoses and Couplers
Signs of Hose Wear
Look for abrasions, blisters, cracks, and exposed reinforcement layers. Also check for stiffness or brittleness in the hose material, which often indicates aging or degradation.
Coupler Damage or Deformation
Any bent, dented, or warped couplers should be replaced immediately. Deformations can prevent proper sealing, leading to leaks or connection failure under pressure.
Frequent Leaks or Drips
Repetitive small leaks at the coupling point are a clear sign that the seal integrity has been compromised. While temporary fixes might work in the short term, replacement is the only reliable long-term solution.
Connection Feels Loose or Unstable
If a coupler doesn’t lock securely or the connection feels wobbly, it’s likely the locking mechanism has worn out. Loose fittings are dangerous and should not be ignored.
Conclusion
Mastering the proper techniques for connecting and disconnecting hydraulic hoses and couplers is essential for maintaining system integrity, ensuring operator safety, and extending the life of your hydraulic equipment. From understanding different coupler types to troubleshooting common connection issues, every step counts when working with high-pressure systems.
By consistently following best practices—such as depressurizing systems before maintenance, using the right PPE, and regularly inspecting for wear—you can avoid costly mistakes, prevent workplace injuries, and keep your operations running smoothly.
Whether you’re a seasoned mechanic or a first-time equipment operator, treating hydraulic components with care and respect is a non-negotiable standard in any industry reliant on fluid power systems.
FAQs
Q1: Can I connect or disconnect hydraulic couplers while the machine is running?
A: No. You should never attempt to connect or disconnect hydraulic hoses or couplers while the equipment is operating. Always shut down and depressurize the system first to prevent injury and equipment damage.
Q2: How do I know which type of hydraulic coupler to use?
A: The right coupler depends on your equipment’s pressure rating, hydraulic fluid type, environment, and how frequently connections need to be made. Flat-face couplers are ideal for clean environments, while ball-type and threaded couplers are better suited for general or heavy-duty use.
Q3: How often should hydraulic hoses and couplers be replaced?
A: Inspect components regularly—every 3 to 6 months for high-use equipment. Replace hoses or couplers immediately if you see cracks, leaks, worn threads, or if the connection no longer locks securely.
Q4: What happens if dirt enters the hydraulic system?
A: Contamination is a leading cause of hydraulic system failure. Dirt and debris can block valves, wear down seals, and reduce fluid quality—leading to loss of efficiency, breakdowns, and costly repairs.
Q5: Is it safe to reuse old O-rings or seals when reconnecting hoses?
A: No. Reusing O-rings is not recommended, as they may have compressed, deformed, or degraded. Always install new seals during maintenance to ensure a secure, leak-free fit.