Introduction
In the realm of industrial operations, hydraulic systems play an indispensable role by powering a wide variety of machines—from heavy construction equipment to precision-based manufacturing tools. However, hydraulic oil leaks remain a persistent challenge, often resulting in environmental concerns, safety risks, costly repairs, and extended equipment downtime. While common sources of leaks such as worn seals or deteriorated hoses are typically addressed in routine maintenance schedules, a deeper layer of hidden causes often goes unnoticed until significant damage occurs.
This article uncovers the often-overlooked reasons behind hydraulic oil leaks in industrial systems, helping maintenance professionals, plant managers, and engineers adopt a more proactive and informed approach to hydraulic system health. From thermal dynamics to fluid compatibility issues, we delve into the technical intricacies that can spell trouble when left unchecked.
Understanding Hydraulic Oil Systems
What Are Hydraulic Systems?
A hydraulic system is a technology that utilizes fluid under pressure to transmit force and energy. These systems convert mechanical energy into hydraulic energy, which is then used to perform tasks such as lifting, pushing, rotating, or moving heavy loads with precision and ease. The core strength of hydraulic systems lies in their ability to provide consistent force and control over a wide range of motion.
Key Components of Hydraulic Systems
To better understand how leaks can originate, it’s essential to familiarize yourself with the primary components involved:
- Pumps: Generate the flow of hydraulic fluid.
- Valves: Regulate flow direction, pressure, and rate.
- Cylinders & Motors: Convert hydraulic energy back into mechanical energy.
- Reservoirs: Store hydraulic fluid.
- Hoses & Tubing: Transport fluid throughout the system.
- Filters: Remove contaminants to maintain fluid integrity.
The Role of Hydraulic Oil
Hydraulic oil is the lifeblood of the system. It serves multiple functions beyond simply transmitting power. These include:
- Lubrication: Reduces friction and wear between moving parts.
- Heat Transfer: Helps dissipate heat generated during system operation.
- Contamination Control: Captures debris and carries it to the filter.
- Sealing: Forms a film between components to prevent internal leaks.
Common Causes of Hydraulic Oil Leaks
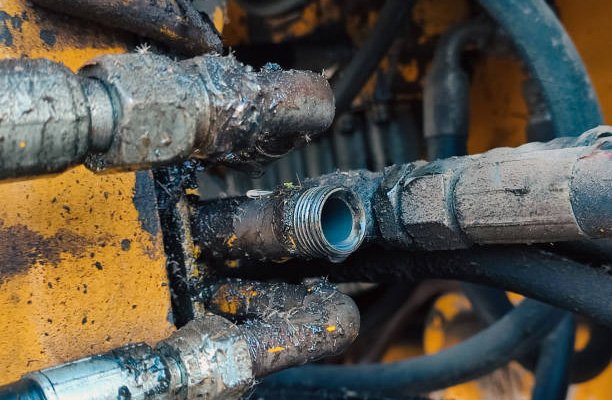
Surface-Level Culprits
Most hydraulic leaks are visible and stem from predictable wear and tear. Some of the most frequent causes include:
- Worn Seals and O-rings: These components degrade over time due to exposure to pressure, heat, and contaminants.
- Cracked or Aged Hoses: Rubber hoses can become brittle and crack under prolonged exposure to hydraulic pressure and environmental factors.
- Loose or Damaged Fittings: Vibrations and improper torque application can cause fittings to loosen, allowing oil to escape.
The Limitations of Reactive Maintenance
While these common issues are typically addressed through routine inspections and part replacements, a reactive approach often misses the more insidious, hidden causes. This results in recurring leaks, escalating maintenance costs, and systemic inefficiencies.
Hidden Causes of Hydraulic Oil Leaks
1. Micro-Fissures in Welds and Joints
Hairline cracks in metal components—especially at weld seams and mechanical joints—are often invisible to the naked eye. These micro-fissures can be caused by material fatigue, thermal stress, or substandard welding techniques. Although they may not leak under low pressure, sustained or high-pressure operation can force oil through these tiny openings, leading to slow, hard-to-detect leaks that compound over time.
2. Thermal Expansion and Contraction
Industrial environments often experience significant temperature fluctuations. Components like pipes, valves, and fittings expand when heated and contract as they cool. Over time, these repeated cycles can compromise seals and fittings, loosening connections or distorting metal surfaces, which gradually leads to fluid leakage. This is especially common in systems that operate continuously in outdoor or unregulated conditions.
3. Vibration-Induced Loosening
Heavy machinery typically generates strong vibrations, which, if unchecked, can have a detrimental effect on hydraulic systems. These vibrations can cause threaded connections, bolts, and fittings to slowly back out or become misaligned. Even slight movements can weaken the integrity of seals and allow hydraulic oil to seep out during operation.
4. Incompatible Fluid Additives
Using hydraulic oils that contain incompatible additives or are not approved by the equipment manufacturer can degrade elastomeric materials in seals and hoses. Some additives might react with specific metals or materials within the system, leading to chemical breakdown and eventual leakage. Always consult the OEM specifications before switching or mixing fluid types.
5. Over-Pressurization Events
Unexpected pressure spikes—whether due to faulty valves, sudden load changes, or operator error—can damage hoses, blow out seals, or crack fittings. These over-pressure conditions may not immediately cause a noticeable leak but can weaken components, making them prone to future failures. Installing pressure relief valves and monitoring systems can help detect and mitigate such risks.
6. Incorrect Installation Practices
Poor installation techniques—such as improper torqueing, cross-threading, or misalignment—can result in immediate or latent leakage problems. Technicians may overlook small gaps or over-tighten fittings, leading to cracked housings or distorted seals. Proper training and adherence to installation protocols are crucial in preventing these issues.
7. Poor Reservoir Breather Maintenance
Reservoir breathers are essential for allowing air exchange in hydraulic tanks. When these breathers become clogged or contaminated, they can create a vacuum inside the tank or allow dirt and moisture to enter the system. Both scenarios can lead to increased wear on internal components and premature seal failure, culminating in oil leaks.
8. Faulty O-Ring Design or Placement
Even minor deviations in O-ring sizing, material, or placement can cause significant leakage problems. Engineers must consider pressure ratings, chemical compatibility, and temperature conditions when choosing O-rings. Additionally, incorrect groove dimensions or surface finishes can prevent the O-ring from sealing properly.
9. External Contamination
Fine dust, dirt, or chemical particulates introduced from the environment can wear down seals and surfaces, especially in open or unprotected systems. These contaminants may also lead to abrasion within cylinders and valves, slowly creating internal pathways for leaks to develop. Using protective bellows, covers, and filtration can minimize exposure.
10. Fluid Foaming and Air Entrapment
Entrained air bubbles can cause the hydraulic fluid to foam, reducing its lubricating properties and promoting cavitation. Over time, this leads to the pitting of metal surfaces and deterioration of seals, eventually resulting in internal and external leaks. Regular fluid analysis and proper reservoir design can help prevent this condition.
Diagnosing Hidden Hydraulic Leaks
Advanced Leak Detection Methods
- UV Dye Testing: Special fluorescent dyes mixed with the hydraulic oil can help trace the source of leaks under UV light.
- Pressure Decay Testing: Monitors pressure drops in sealed sections of the system to identify leak points.
- Acoustic Emission Sensors: Detect high-frequency signals emitted by escaping fluids, even from microscopic holes.
- Thermal Imaging: Infrared cameras identify abnormal heat signatures, which often correlate with leak sources or friction points.
Visual and Manual Inspections
While advanced technology is helpful, skilled technicians can also use their senses to identify early leak indicators. Look for:
- Oil film on seemingly clean surfaces
- Discolored dust accumulation (sticky spots)
- Inconsistent fluid levels in the reservoir
- Noise changes (e.g., whining, knocking)
Data Logging and Trend Analysis
Using computerized maintenance management systems (CMMS) and IoT sensors, maintenance teams can collect performance data and detect anomalies that suggest leaks. Over time, trend analysis allows teams to predict leak-prone components before failure occurs.
Prevention Strategies
Invest in High-Quality Components
Premium hydraulic components—especially seals, hoses, and fittings—are manufactured to tighter tolerances and with better materials, providing superior longevity and performance. Although they may have a higher upfront cost, they reduce the frequency of breakdowns and oil leaks in the long term.
Maintain Optimal Operating Conditions
Operating your system within recommended parameters for pressure, temperature, and cleanliness is essential. Install filtration systems, temperature monitors, and pressure relief valves to ensure consistency. Monitor for signs of fluid degradation or contamination, and change oil as specified by manufacturers.
Regular and Proactive Maintenance
Implement a preventive maintenance schedule that includes system audits, fluid sampling, and part inspections. Catching wear and tear early minimizes the chances of leaks spreading or escalating into serious system damage.
Train Technicians on Leak Detection
Well-trained staff are an organization’s first line of defense. Offer continuous training to technicians on the latest tools, inspection methods, and OEM service protocols for identifying hidden and developing leaks. Empowering your team ensures faster identification and resolution of issues.
Establish a Leak Tracking and Reporting System
Track every detected leak in a centralized system, noting location, severity, root cause, and resolution. This historical data helps identify patterns and chronic problem areas, enabling data-driven improvements to the hydraulic system design or maintenance approach.
Consequences of Ignoring Hidden Leaks
Unplanned Downtime and Production Loss
Hidden hydraulic oil leaks can gradually deplete fluid levels, leading to decreased system efficiency or complete shutdown. If not detected in time, the machinery may suffer from performance lag or stop working altogether, causing unexpected production halts. This downtime can result in missed deadlines, dissatisfied customers, and a sharp increase in operational costs.
Environmental and Safety Hazards
Leaking hydraulic fluid can pose serious safety hazards, including slip-and-fall risks for workers and potential fire hazards in high-temperature environments. Moreover, hydraulic oil spills can lead to soil and water contamination, potentially violating environmental regulations and attracting fines or lawsuits. Containment and cleanup efforts often require expensive third-party intervention.
Accelerated Component Wear and System Failure
Low hydraulic oil levels and contaminated fluid accelerate internal wear on pumps, cylinders, and valves. Components that run without adequate lubrication or experience cavitation due to air bubbles can quickly degrade. These failures are not only costly to repair but may also require full system overhauls if left unresolved.
Escalating Operational Costs
From frequent top-offs of hydraulic fluid to increased part replacements and labor expenses, hidden leaks create a ripple effect on operational budgets. Over time, the cumulative impact of these seemingly minor leaks can represent a significant portion of a facility’s maintenance expenditures.
Conclusion
Hydraulic oil leaks are more than just a nuisance—they are a silent threat to industrial efficiency, safety, and sustainability. While many organizations address obvious signs of leakage, the hidden causes often go undetected until severe damage has occurred. By understanding these underlying contributors—such as thermal cycling, micro-fissures, and incompatible fluids—companies can implement more robust inspection and prevention protocols.
A proactive approach that includes advanced diagnostic tools, technician training, and system monitoring not only reduces the likelihood of leaks but also extends equipment life and improves overall plant performance. Don’t wait for leaks to surface—invest in uncovering them before they compromise your operations.
FAQs
1. What is the most overlooked cause of hydraulic oil leaks?
Micro-fissures in welds and thermal expansion/contraction effects are commonly overlooked yet significant contributors to slow hydraulic leaks.
2. Can fluid foaming actually cause internal system damage?
Yes. Foaming introduces air into the fluid, causing cavitation and poor lubrication. Over time, this leads to wear, overheating, and internal leakage points.
3. How often should I inspect a hydraulic system?
As a rule of thumb, hydraulic systems should be visually inspected at least once per month, and undergo a full diagnostic review quarterly—especially in high-duty environments.
4. What are the most effective tools for detecting hidden leaks?
UV dye testing, thermal imaging, and acoustic emission sensors are among the most accurate tools for locating hard-to-find leaks.
5. Can tracking software really help in leak prevention?
Absolutely. CMMS (Computerized Maintenance Management Systems) allow teams to log, monitor, and analyze recurring leak issues, helping to identify trends and proactively mitigate future risks.