Hydraulic systems are the lifeblood of many industries, including manufacturing, aerospace, construction, and marine operations. These systems rely on the precise movement of pressurized fluids to power machinery, control mechanisms, and perform heavy-duty tasks efficiently. However, within this fluid-driven sophistication lies a hidden challenge—vibrations.
Hydraulic system vibrations, though often underestimated, can quietly erode system integrity, compromise performance, and pose serious safety threats. From fluctuating fluid flows to mechanical imbalances, the causes are varied but the consequences can be severe. This article delves deep into the hidden dangers of hydraulic vibrations, exploring their causes, impact, and prevention strategies to help you maintain a safer, more efficient operation.
Why Vibrations in Hydraulic Systems Are a Serious Concern
While minor vibrations may seem inconsequential at first glance, they can lead to serious complications if left unaddressed. These vibrations typically originate from irregularities within the system and tend to amplify over time, affecting both performance and durability.
- Mechanical Integrity Risks: Continuous vibrations can weaken structural components, including hoses, fittings, and support frames. Over time, this wear and tear may result in cracks, leaks, or even catastrophic failures.
- Operational Inefficiencies: Vibrations reduce the precision and responsiveness of hydraulic actuators and control valves, leading to sluggish performance and increased energy consumption.
- Safety Hazards: In high-pressure environments, unexpected component failures due to vibrations can endanger personnel and damage nearby equipment.
Understanding and mitigating these dangers is essential for maintaining system health and ensuring safe, efficient operations.
Primary Causes of Hydraulic Vibrations
Identifying the root causes of hydraulic vibrations is the first step toward mitigation. Below are some of the most common culprits:
- Cavitation and Aeration: These phenomena occur when air or vapor bubbles form in the hydraulic fluid and collapse violently, causing noise, vibration, and damage to components.
- Fluid Turbulence and Flow Velocity Issues: High-speed fluid movement, especially through narrow passages or sharp bends, creates turbulence that leads to pulsations and vibrations.
- Misalignment and Mechanical Imbalances: Incorrect alignment of pumps, motors, or actuators causes irregular motion and vibration throughout the system.
- Pump and Motor Anomalies: Worn or unbalanced rotating elements inside pumps and motors are frequent sources of cyclic vibrations and resonance.
By addressing these factors early, it’s possible to reduce vibration levels and extend the lifespan of the entire hydraulic system.
The Impact of Vibrations on Hydraulic Components
Hydraulic vibrations don’t just affect performance—they cause physical damage to key system components. These damages can occur incrementally, making them hard to detect until a failure occurs.
- Damage to Hoses and Seals: Constant vibration creates friction and strain on flexible components. Over time, this results in cracks, leaks, or complete hose failure, often with little warning.
- Accelerated Wear of Pumps and Valves: Vibrations introduce unpredictable loads on precision components like valves and pumps, accelerating internal wear and reducing their functional lifespan.
- Structural Fatigue in Metal Components: Continuous mechanical stress from vibrations weakens metals, causing microfractures and eventual breakage, especially in welded or bolted joints.
Routine inspection and vibration control measures are essential to avoid these common, costly failures.
Effects on System Performance and Efficiency
Unchecked vibrations drastically reduce the efficiency of hydraulic systems, affecting both energy consumption and output quality. The consequences can ripple across production lines and service operations.
- Energy Loss and Heat Generation: Vibrations increase internal friction and create resistance, leading to unnecessary power consumption and excessive heat buildup.
- Decreased Accuracy and Responsiveness: Vibrations interfere with the fluid’s ability to transmit power smoothly, reducing the system’s precision—critical in automated or CNC-controlled environments.
- Increased Maintenance and Downtime: A system struggling with persistent vibrations is more prone to breakdowns, resulting in higher maintenance costs and extended downtimes.
These issues not only inflate operating costs but also compromise product quality and output timelines.
Safety Implications of Ignored Vibrations
Vibrations in hydraulic systems are not just a maintenance issue—they’re a serious safety risk. Ignoring them can lead to hazardous situations for operators and nearby personnel.
- Risk of Hydraulic Fluid Leaks and Fires: Leaking fluid under pressure can spray out violently, potentially igniting if it contacts hot surfaces or electrical components.
- Potential for Equipment Failure During Operation: Vibrations can cause unexpected shutdowns or malfunctions during critical operations, posing dangers in sectors like aerospace, marine, and construction.
- Endangerment of Operator Safety: A sudden failure of pressurized systems can cause physical injury from burst components or machine misbehavior.
Safety protocols must include regular vibration monitoring to ensure workplace safety and regulatory compliance.
How to Detect Hydraulic Vibrations Early
Early detection of vibrations can prevent severe damage and enhance the reliability of your hydraulic systems. Here’s how to catch issues before they escalate:
- Use of Vibration Analysis Tools and Sensors: Advanced monitoring tools can detect abnormal vibration frequencies and amplitude in real time, offering a critical early warning system.
- Periodic System Inspections and Diagnostics: Scheduled checks by technicians can identify signs of wear, misalignment, or other root causes of vibration before they cause failure.
- Listening for Audible Cues and Physical Feedback: Operators should be trained to notice new sounds, heat, or movement that signal unusual vibration levels.
Integrating detection systems into routine maintenance schedules improves safety and equipment lifespan.
Best Practices for Preventing Vibrations
Prevention is more cost-effective than repair. The following best practices help reduce or eliminate harmful vibrations in hydraulic systems:
- Proper System Design and Component Selection: Design with fluid dynamics in mind, ensuring optimal flow paths, correct sizing of components, and stable mounting structures.
- Regular Maintenance and Condition Monitoring: Timely servicing of pumps, valves, and actuators helps prevent buildup of conditions that cause vibration.
- Fluid Quality Control and Contamination Prevention: Clean, properly viscous hydraulic fluid reduces turbulence, cavitation, and inconsistent pressure that contribute to vibration.
Consistent application of these practices minimizes the risk of vibration and supports long-term system reliability.
Role of Hydraulic Fluid in System Stability
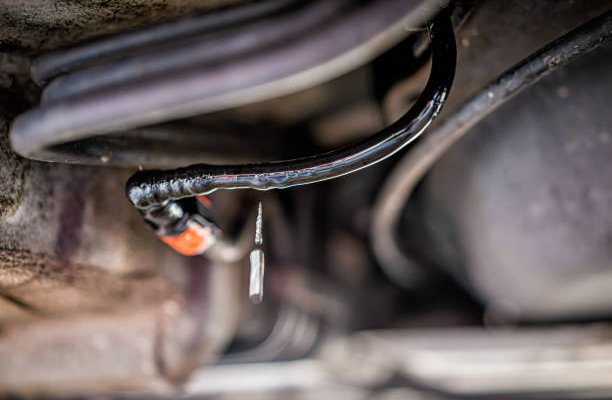
The condition and type of hydraulic fluid play a critical role in maintaining system stability and minimizing vibrations. Neglecting fluid quality can trigger cascading failures.
- Importance of Correct Viscosity and Cleanliness: The fluid’s viscosity must match system requirements. Too thick or too thin, and it can cause pressure spikes or erratic flow behavior that contributes to vibration.
- How Fluid Degradation Contributes to Vibration: Contaminants, thermal breakdown, and moisture reduce fluid performance and can lead to cavitation, foaming, and irregular pressure—all key sources of vibration.
Regular fluid analysis and filtration ensure smooth operation and minimize vibration-related risks.
Innovations in Vibration Mitigation Technologies
Technological advancements are transforming how industries tackle hydraulic vibrations. These innovations enhance system monitoring and durability.
- Use of Dampers and Vibration Isolators: Mechanical solutions like tuned mass dampers and rubber mounts help absorb excess motion, protecting sensitive components.
- Smart Systems and Real-Time Monitoring Solutions: IoT-enabled sensors allow operators to monitor system health 24/7 and receive instant alerts for abnormal vibration levels.
- Predictive Maintenance Powered by AI and IoT: Machine learning models can analyze vibration data patterns over time, forecasting failures before they happen and allowing preemptive action.
These technologies not only reduce downtime but also boost confidence in high-performance applications.
Industry Standards and Guidelines
Adhering to industry standards ensures that vibration control is not an afterthought but a design and maintenance priority.
- ISO Standards Related to Hydraulic System Health: ISO 10816 and ISO 7919 define acceptable vibration levels for rotating machinery, offering benchmarks for performance and safety.
- OEM Recommendations and Compliance Checks: Equipment manufacturers often provide specific guidelines for acceptable vibration limits and recommended maintenance protocols.
Following these standards not only improves safety and longevity but also supports regulatory compliance and warranty protection.
Training and Awareness for Operators and Engineers
One of the most effective defenses against hydraulic system vibration issues is a well-informed team. Training and awareness help ensure early detection and proper response.
- Importance of Training in Identifying Early Signs: Operators should be educated on how to recognize the subtle indicators of vibration, such as unusual noise, heat, or performance dips.
- Developing a Vibration-Conscious Culture in Operations: Embedding vibration awareness into safety protocols and daily routines fosters proactive maintenance and risk mitigation.
By investing in training, companies reduce system failures and improve operational efficiency.
When to Seek Professional Help
Not all vibration issues can be solved in-house. Recognizing when to call in experts can prevent minor issues from escalating into system-wide failures.
- Signs That Indicate Expert Intervention Is Needed: Persistent vibrations despite maintenance, recurring component failures, or unclear vibration sources are all red flags.
- Choosing the Right Hydraulic Service Provider: Look for providers with proven experience, modern diagnostic tools, and alignment with industry standards like ISO and OEM protocols.
Timely professional support can save substantial costs and prevent hazardous outcomes.
Conclusion
Hydraulic system vibrations are more than a nuisance—they’re a silent threat to safety, performance, and longevity. From damaging essential components to risking catastrophic failure, the dangers are very real and often underestimated.
By understanding the causes, identifying early warning signs, and implementing proactive strategies—including fluid quality control, advanced monitoring technologies, and regular maintenance—you can effectively combat vibration issues. Combined with operator training and adherence to industry standards, these measures create a resilient hydraulic environment with optimized performance and reduced risk.
In today’s fast-paced, high-stakes industrial landscape, addressing hydraulic vibrations isn’t optional—it’s essential.
FAQs
1. What are the early signs of hydraulic system vibration?
Early signs include unusual noises (such as whining or knocking), erratic system movements, increased heat, and visible shaking of components. Monitoring these symptoms can help detect problems before they escalate.
2. Can hydraulic fluid quality affect system vibration?
Yes. Poor fluid quality—such as incorrect viscosity, contamination, or degradation—can lead to cavitation, foaming, and pressure instability, all of which contribute to harmful vibrations in the system.
3. How often should vibration monitoring be conducted in hydraulic systems?
Vibration monitoring should be part of regular preventive maintenance. High-performance or mission-critical systems may require real-time monitoring, while others benefit from monthly or quarterly diagnostics.
4. Are there industry standards for acceptable hydraulic vibration levels?
Yes, ISO standards such as ISO 10816 provide guidelines for acceptable vibration levels in rotating machinery. OEMs may also offer specific recommendations tailored to their equipment.
5. What tools are used to measure hydraulic system vibrations?
Common tools include accelerometers, vibration analyzers, and IoT-enabled sensors. These devices measure frequency and amplitude to detect anomalies and help pinpoint vibration sources.