Introduction
Hydraulic hose fittings play a crucial role in maintaining secure, leak-free connections in hydraulic systems. These fittings are essential components used to join hydraulic hoses to various machinery or equipment, ensuring that fluids flow effectively under pressure. Proper installation is key to system reliability, as improperly attached fittings can lead to serious issues such as leaks, pressure loss, or even system failure.
In this guide, we will walk you through the different types of hydraulic hose fittings, tools required for attachment, and the steps to ensure a secure and safe connection. Whether you’re new to hydraulics or looking to improve your technique, this comprehensive guide will cover everything you need to know to attach hydraulic hose fittings properly.
Tools and Materials You Will Need
To attach hydraulic hose fittings correctly, it’s essential to have the right tools and materials on hand. Using quality components ensures that your installation is both secure and safe, minimizing the chances of leaks or damage to the hydraulic system. Here’s a list of the tools and materials you’ll need:
Essential Tools
- Hydraulic hose cutter: A clean, precise cut is crucial to prevent damaging the hose or fittings.
- Crimping tool: For crimped hose fittings, a crimping tool is necessary to secure the fitting onto the hose.
- Torque wrench: Ensures that the fittings are tightened to the manufacturer’s specified torque settings.
- Thread sealant: If you’re working with threaded fittings, thread sealant helps prevent leaks.
- Measuring tape: To ensure the correct hose length is cut.
Choosing the Right Hydraulic Hose and Fittings
It’s important to select the right hydraulic hose and fitting combination for your system. The hose’s pressure rating, temperature tolerance, and material compatibility must match the requirements of the hydraulic fluid and working conditions. Likewise, the fittings should correspond to the hose type (e.g., crimped, threaded) and the machine’s specifications. Always check the manufacturer’s guidelines for compatibility.
Why Quality Tools Matter
Using high-quality tools and materials ensures a long-lasting, safe hydraulic system. Cheap or worn-out tools may lead to improper installation, resulting in leaks, system inefficiency, or even dangerous failures. Invest in reliable tools, and your hydraulic system will perform optimally over time.
Types of Hydraulic Hose Fittings
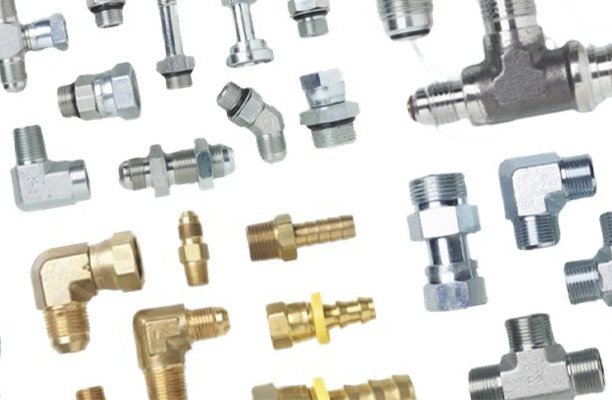
Hydraulic hose fittings come in various types, each designed for different applications. Understanding the type of fitting required for your hydraulic system is essential for achieving a proper seal and ensuring the safety and efficiency of the system.
1. Crimped Fittings
Crimped fittings are commonly used in hydraulic systems and are attached by using a crimping tool to securely fasten the fitting to the hose. The crimping process ensures a tight, leak-free connection that is resistant to vibrations and pressure fluctuations.
2. Threaded Fittings
Threaded fittings, which are also known as screw-on fittings, are used where the hose is threaded onto the fitting using a wrench. This type of fitting is typically used for high-pressure systems and provides a reliable seal when properly tightened. Ensure that the threads are properly aligned and lubricated before installation to avoid damage.
3. Push-on Fittings
Push-on fittings are one of the simplest types to install. They require no special tools, as they can be attached by simply pushing the fitting onto the hose. This method is used for low-pressure systems and is popular in automotive or industrial machinery where ease of installation is a priority.
4. Flanged Fittings
Flanged fittings are used for large-diameter hydraulic systems. They consist of a flange that attaches to a corresponding flange on the system, secured by bolts. Flanged fittings are ideal for high-flow applications and are often used in large industrial machinery or heavy equipment.
How to Select the Right Fitting Type
Choosing the right fitting type depends on your specific application. Factors such as pressure, temperature, and vibration levels, as well as the size and material of the hose, all influence the choice of fitting. Always consult the equipment manual and ensure that the fitting type is appropriate for your system’s requirements.
Step-by-Step Process to Attach Hydraulic Hose Fittings
Attaching hydraulic hose fittings may seem like a simple task, but proper installation is crucial to ensure the safety and longevity of your hydraulic system. Below is a step-by-step guide that explains how to securely attach hydraulic hose fittings for a leak-free connection.
Step 1: Prepare the Hose
Before attaching the fittings, the hydraulic hose must be properly prepared. A clean and precise cut ensures a perfect fit, preventing any issues during the fitting attachment process.
- Measure and cut the hose: Use a hydraulic hose cutter to ensure a clean and straight cut. Make sure you measure the hose accurately based on the required length.
- Clean the hose ends: Use a cloth to wipe off any debris, dust, or dirt from the ends of the hose. This will prevent contamination during fitting attachment and ensure a secure connection.
Step 2: Choose the Right Fitting
Selecting the appropriate hydraulic fitting for your system is essential for creating a reliable and leak-free connection. Refer to the manufacturer’s specifications to match the fitting type to the hose. Whether you’re using crimped, threaded, or push-on fittings, make sure the size and material are compatible with the system’s requirements.
Step 3: Attach the Fitting
Once the hose is prepped and the right fitting is selected, it’s time to attach the fitting. The installation method varies depending on the type of fitting:
- Crimping: Place the fitting over the hose and use a crimping tool to compress the fitting onto the hose. Ensure that the crimp is secure and uniform, without any gaps.
- Threading: For threaded fittings, simply screw the fitting onto the hose, ensuring the threads are properly aligned. Use a wrench to tighten the fitting to the recommended torque.
- Push-on: Push the fitting onto the hose until it clicks into place. Make sure the fitting is fully seated on the hose for a secure connection.
Step 4: Tighten and Test the Connection
After attaching the fitting, tighten it according to the manufacturer’s recommended torque specifications. Over-tightening can damage the hose or fitting, while under-tightening may cause leaks. Once the fitting is secured, it’s important to test the connection:
- Check for leaks: Apply pressure to the system and inspect the connection for any signs of leakage. A properly attached fitting should hold the pressure without any fluid escaping.
- Perform a pressure test: If the system allows, conduct a pressure test to ensure the connection is stable and the fitting is securely attached.
Best Practices for Hydraulic Hose Installation
Proper installation is not only about attaching the fitting, but also ensuring the entire hydraulic hose system is designed for longevity and performance. Below are some best practices for installing hydraulic hoses:
Proper Hose Routing and Securing
The way a hydraulic hose is routed and secured can significantly affect its performance. Ensure the hose is not subjected to unnecessary bending, twisting, or kinking, as this can lead to premature failure. When routing hoses, follow these guidelines:
- Keep hoses away from sharp edges or components that could cause abrasion.
- Use clamps or brackets to secure the hoses and prevent them from moving or rubbing against other surfaces.
- Avoid routing hoses near hot surfaces or in areas exposed to excessive heat, as this can cause hose degradation.
Avoiding Common Installation Mistakes
Several mistakes can compromise the installation of hydraulic hoses, leading to inefficiencies or even dangerous failures. Some common installation errors to avoid include:
- Incorrect hose length: If the hose is too long or too short, it may cause tension or inadequate reach to the connection points.
- Wrong fitting type: Always use the correct fitting type for your system to avoid leaks or system damage.
- Improper torque: Failing to torque fittings correctly can cause leaks or stress on the hose, leading to failure.
Maintenance Tips for Longer Hose Life
To maximize the lifespan of hydraulic hoses, regular maintenance and inspection are essential. Here are some maintenance tips:
- Inspect hoses regularly for signs of wear, cracking, or leaks.
- Replace hoses or fittings that show any damage or wear.
- Clean and maintain hydraulic fittings to prevent the build-up of debris or contaminants.
Troubleshooting Common Issues with Hydraulic Hose Fittings
Even with proper installation, issues with hydraulic hose fittings can arise over time. Being able to identify and resolve common problems quickly is essential to keep your hydraulic system running smoothly.
Leaks and How to Prevent Them
Leaks are one of the most common problems with hydraulic hose fittings. Here’s how you can prevent leaks:
- Use proper sealing: For threaded fittings, always apply the right amount of thread sealant.
- Ensure correct torque: Both over-tightening and under-tightening can cause leaks, so follow torque specifications precisely.
- Inspect regularly: Regular inspection helps to identify potential leaks before they become a bigger issue.
Fitting Misalignment
Misalignment between the hose and fitting can cause improper sealing, leading to leaks or loss of pressure. To avoid misalignment:
- Make sure the fitting and hose are correctly aligned before tightening.
- If using crimped fittings, ensure the hose is inserted fully into the fitting.
Over-tightening or Under-tightening Issues
Improper tightening can compromise the integrity of the connection. Over-tightening can damage the hose or fitting, while under-tightening can lead to leaks. Always use a torque wrench to ensure that the fittings are tightened according to the manufacturer’s recommendations.
Conclusion
Attaching hydraulic hose fittings properly is critical for the safety and efficiency of your hydraulic system. By following the correct procedures, using the right tools and fittings, and adhering to best practices, you can ensure leak-free, reliable connections that last. Whether you’re a professional technician or a DIY enthusiast, mastering hydraulic hose fitting installation will save time, money, and prevent unnecessary breakdowns.
Remember, the key steps are:
- Preparing the hose and ensuring cleanliness.
- Choosing the correct type of fitting for your system.
- Following the proper installation and torqueing procedures.
- Regular inspection and maintenance to prolong the life of your hydraulic hoses.
By following these guidelines, you can confidently tackle any hydraulic hose fitting installation or maintenance project, ensuring your system performs at its best for years to come.
FAQs
1. How do I know if my hydraulic hose fitting is installed correctly?
The best way to ensure a correct installation is to check for leaks after the system has been pressurized. Additionally, the fitting should be tightly secured, with no signs of movement or misalignment. Always refer to the manufacturer’s specifications for torque values and fitting types.
2. Can I reuse hydraulic hose fittings?
In some cases, hydraulic hose fittings can be reused, but it’s important to inspect them for signs of wear or damage. If the fitting shows any cracks, rust, or signs of deterioration, it should be replaced to prevent leaks or system failure.
3. What should I do if I notice a hydraulic hose fitting leak?
If you notice a leak, immediately turn off the system and relieve the pressure. Inspect the fitting to identify the source of the leak. It could be due to incorrect installation, loose fittings, or worn-out seals. Tighten the fitting as needed, or replace it if necessary.
4. How often should I inspect my hydraulic hoses and fittings?
Hydraulic hoses and fittings should be inspected regularly, ideally once every few months or as recommended by the manufacturer. Frequent inspections help to catch early signs of wear, corrosion, or leaks before they cause major issues.
5. What are the risks of improper hydraulic hose fitting installation?
Improper installation of hydraulic hose fittings can result in leaks, loss of pressure, or even catastrophic system failure. This can lead to downtime, costly repairs, or hazardous situations, especially in high-pressure systems. Always ensure the fittings are installed according to the manufacturer’s guidelines to prevent these risks.