Accurately measuring metric threads is crucial in ensuring the correct fit and function of mechanical components. Whether you’re working on automotive repairs, manufacturing equipment, or custom fabrication, understanding how to measure these threads with precision can prevent costly errors and enhance the reliability of your assemblies. This process involves using specialized tools such as thread gauges, calipers, and micrometers to determine key dimensions like the thread’s outside diameter, pitch, and pitch diameter. By mastering these techniques, you can confidently handle metric threads in any application, ensuring that every part fits perfectly and performs as expected.
What is a Metric Thread?
Metric threads are widely used in various industries due to their standardized design, making them easy to identify and measure. These threads are designated by the letter M, followed by two key dimensions: the nominal major diameter and the pitch, both measured in millimeters. For example, M10 x 1.0 signifies a thread with a 10mm major diameter and a 1.0mm pitch. The pitch refers to the distance between two corresponding points on adjacent threads.
When you mention only the diameter, like M10, you specify that the thread follows the coarse thread series with a standard pitch of 1.5mm for a 10mm diameter. The omission of the pitch value assumes the use of the coarse thread standard, which is most common for general applications. This standardization allows for consistency across different applications and industries, ensuring that parts and fasteners fit together correctly.
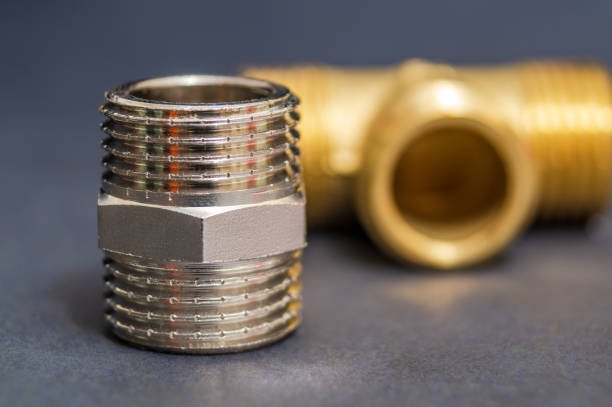
Why Accurate Metric Thread Measurement Matters
Accurately measuring metric threads is essential to ensure the correct fit and function of mechanical components. Incorrect measurements can lead to issues such as mismatched parts, potential leaks, or mechanical failures, especially in critical applications like automotive or aerospace engineering. Understanding how to measure and interpret these threads can prevent costly errors and ensure the reliability of assembled parts.
Tools Required for Measuring Metric Threads
Before you begin measuring metric threads, it’s essential to have the right tools at your disposal. These tools precisely measure and help you accurately identify the correct thread size and pitch.
- Thread Pitch Gauge: This tool measures the distance between threads, known as the pitch. It includes several blades with different pitches that you match to the thread.
- Calipers: A versatile measuring tool used to measure the outside diameter of a thread. Many prefer digital calipers for their ease of use and precise readings.
- Thread Micrometer: A more specialized tool used for measuring the pitch diameter of threads, which is crucial for ensuring a proper fit between threaded components.
Measuring Metric Threads: Step-by-Step Guide
Identify If the Thread is Parallel or Tapered
Before taking any measurements, it’s important to determine whether the thread is parallel or tapered. This can be done by visually inspecting the thread or using a caliper to measure the diameter at different points along the thread. In parallel threads, the diameter remains constant, while in tapered threads, the diameter decreases along the length.
Measure the Outside Diameter
The first physical measurement you should take is the outside diameter (O.D.) of the thread. This measurement provides the nominal size of the thread and is the first step in identifying the correct thread callout.
- Using Calipers:
- Place the calipers around the external threads (for male threads) or inside the internal threads (for female threads) and adjust until they are snug.
- Take the reading from the caliper. For example, a caliper reading of 12.03mm indicates a 12mm thread.
- Remember that this measurement only tells you the diameter and not the pitch, which is crucial for full thread identification.
- Understanding the Measurement:
- If the measured diameter matches a standard size, such as 10mm or 12mm, you have identified the major diameter. However, without knowing the pitch, the thread size remains incomplete.
Determine the Thread Pitch
After identifying the outside diameter, the next step is to determine the thread pitch. The pitch is the distance between the threads and is usually measured in millimeters.
- Using a Thread Pitch Gauge:
- Select a pitch gauge blade that you think matches the thread’s pitch.
- Fit the gauge against the thread, checking if it aligns perfectly without gaps or overlaps.
- The correct gauge will match the thread profile exactly, giving you the pitch measurement, such as 1.0mm, 1.5mm, or 2.0mm.
- Using Calipers (For Advanced Measurement):
- For more precision, especially if you don’t have a pitch gauge, you can use calipers to measure the distance between peaks or valleys of adjacent threads, though this method requires a steady hand and careful alignment.
Measure the Pitch Diameter
The pitch diameter is a critical dimension that defines the effective size of the thread, ensuring that male and female threads fit together correctly.
- Using a Thread Micrometer:
- Place the thread micrometer so that its anvils touch the threads at the correct points.
- Slowly tighten the micrometer until you feel slight resistance, then read the measurement.
- This measurement helps in verifying the class of fit for the thread, which is vital for applications requiring precise tolerances.
Find the Closest Match on a Thread Chart
Once you have both the outside diameter and the pitch, you can use these measurements to find the closest match on a thread chart. Thread charts list standard thread sizes and their corresponding pitch diameters.
- Combining Measurements:
- For example, if you measured an outside diameter of 12mm and a pitch of 1.5mm, you would look for a M12 x 1.5 entry on the chart.
- These charts are essential references for ensuring that your measurements match standard thread sizes.
Thread Callout | Thread Pitch (mm) | Male Thread O.D (mm) | Male Thread O.D (inches) | Female Thread I.D (mm) | Female Thread I.D (inches) |
---|---|---|---|---|---|
M8 X 1.0 | 1 | 8 | 0.315 | 6.9 | 0.272 |
M10 X 1.0 | 1 | 10 | 0.394 | 8.9 | 0.35 |
M10 X 1.5 | 1.5 | 10 | 0.394 | 8.4 | 0.331 |
M12 X 1.0 | 1 | 12 | 0.472 | 10.9 | 0.429 |
M12 X 1.5 | 1.5 | 12 | 0.472 | 10.4 | 0.409 |
M14 X 1.5 | 1.5 | 14 | 0.551 | 12.4 | 0.488 |
M16 X 1.5 | 1.5 | 16 | 0.63 | 14.4 | 0.567 |
M18 X 1.5 | 1.5 | 18 | 0.709 | 16.4 | 0.646 |
M20 X 1.5 | 1.5 | 20 | 0.787 | 18.4 | 0.724 |
M22 X 1.5 | 1.5 | 22 | 0.866 | 20.4 | 0.803 |
M24 X 1.5 | 1.5 | 24 | 0.945 | 22.4 | 0.882 |
M26 X 1.5 | 1.5 | 26 | 1.024 | 24.4 | 0.961 |
M27 X 2.0 | 2 | 27 | 1.063 | 24.8 | 0.976 |
M30 X 2.0 | 2 | 30 | 1.181 | 27.8 | 1.094 |
M33 X 2.0 | 2 | 33 | 1.299 | 30.8 | 1.213 |
M36 X 2.0 | 2 | 36 | 1.417 | 33.8 | 1.331 |
M42 X 2.0 | 2 | 42 | 1.654 | 39.8 | 1.567 |
M45 X 2.0 | 2 | 45 | 1.772 | 42.8 | 1.685 |
M48 X 2.0 | 2 | 48 | 1.89 | 45.8 | 1.803 |
M52 X 2.0 | 2 | 52 | 2.047 | 49.8 | 1.961 |
M60 X 2.0 | 2 | 60 | 2.362 | 57.8 | 2.276 |
Advanced Considerations in Metric Thread Measurement
In some cases, simply measuring the outside diameter and pitch might not be enough, especially for specialized applications. Here’s what you should consider:
- Check for Seals or Angled Sealing Surfaces:
If the thread has a sealing surface or an angle, this might indicate a specific type of fitting. Use this information along with your thread measurements to identify the exact fitting type. - Consider Thread Tolerances:
Metric threads have specific tolerance classes that define how tightly or loosely the threads will fit. Understanding these tolerances is crucial for applications where the fit is critical, such as in hydraulic systems or high-pressure applications.
Troubleshooting Common Issues in Metric Thread Measurement
Despite having the right tools and following the correct procedures, you may encounter some challenges when measuring metric threads. Here’s how to address common issues:
Worn or Damaged Threads
- Problem: Worn or damaged threads can produce inaccurate measurements because they no longer retain their original dimensions.
- Solution: Clean the threads thoroughly to remove debris or corrosion. If possible, use a thread file to restore the thread profile before measuring. For severely damaged threads, consider using a thread chaser to re-cut the threads.
Difficulty Aligning the Pitch Gauge
- Problem: Especially with fine threads, it can be challenging to align the pitch gauge perfectly with the threads, leading to misreadings.
- Solution: Ensure that you are working in a well-lit environment. Use a magnifying glass to see the threads clearly and ensure the gauge is seated correctly whenever possible. Take your time to verify the fit of the gauge multiple times.
Inconsistent Measurements
- Problem: You might get slightly different measurements each time you use the calipers or micrometer.
- Solution: Ensure that your tools are properly calibrated before use. When using calipers, apply consistent pressure and measure at several points around the thread to account for any out-of-round conditions.
Identifying Non-Standard Threads
- Problem: Some components may have non-standard or custom threads that don’t match any entries in standard thread charts.
- Solution: Double-check your measurements to confirm accuracy. If you’re certain the measurements are correct, consult with the manufacturer’s documentation or contact a technical support specialist who might have information on non-standard threads.
Applications of Metric Threads in Different Industries
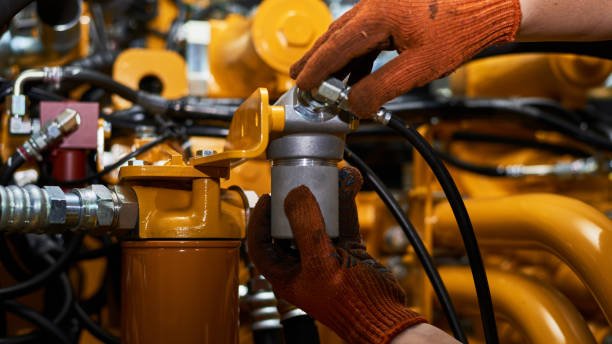
Metric threads are widely used across various industries, each with specific requirements and standards. Understanding the application context can help ensure that you measure and select the correct threads for your needs.
Automotive Industry
- Automotive components, such as bolts, nuts, and studs, commonly use metric threads. Accurate measurement is critical for maintaining vehicle safety and performance. Common sizes include M6, M8, and M10, often with fine threads for precise fitment in engine components.
Manufacturing and Machinery
- In manufacturing, machinery, and industrial applications, metric threads are standard for assembling equipment and components. Thread tolerance and class of fit are particularly important in these settings to prevent issues like vibration loosening or thread stripping.
Aerospace
- The aerospace industry demands extremely precise thread measurements, often with tight tolerances and high-strength materials. Various aircraft parts use metric threads, and measuring them requires high precision to meet stringent safety standards.
Conclusion
Accurately measuring metric threads is essential for ensuring the proper fit and function of mechanical components. By using the right tools, such as thread pitch gauges, calipers, and thread micrometers, and following a systematic approach, you can effectively identify and measure metric threads. Whether for automotive, manufacturing, or aerospace applications, understanding and applying correct thread measurement techniques will help prevent costly errors and ensure that your assemblies are both safe and reliable.
With these insights, you’re now equipped to handle metric thread measurements with confidence, ensuring precision in your projects and professional tasks.
FAQs
Q1: What does the “M” in metric threads stand for?
The “M” in metric threads stands for “metric,” indicating that the thread dimensions (diameter and pitch) are measured in millimeters. For example, M8 x 1.25 means a metric thread with an 8mm diameter and a 1.25mm pitch.
Q2: Can metric threads be measured with imperial tools?
While it is possible to measure metric threads with imperial tools, it is not recommended due to potential inaccuracies. It is best to use metric tools designed for the purpose, such as metric calipers and thread gauges, to ensure precise measurements.
Q3: How can I tell if a thread is coarse or fine?
Metric threads are coarse if only the diameter is specified (e.g., M10), with a standard pitch assigned based on the diameter. Fine threads will have a specific pitch value indicated (e.g., M10 x 1.0), meaning the pitch is smaller than the standard coarse pitch.
Q4: What is a thread’s pitch diameter?
The pitch diameter of a thread is the diameter of an imaginary cylinder that passes through the threads where the width of the thread equals the width of the space between the threads. It is critical for ensuring the fit between internal and external threads.
Q5: Are thread pitch gauges universal?
Thread pitch gauges are not universal; they are specific to the type of thread being measured. Ensure that you use a metric thread pitch gauge for metric threads, as using an incorrect gauge can result in inaccurate measurements.
Q6: Why do my measurements not match standard sizes?
If your measurements do not match standard sizes, recheck them to ensure accuracy. It could also be that the threads are non-standard or custom. Consulting with a technical expert or using a more detailed thread chart might help resolve the discrepancy.