Introduction
Hydraulic systems are the backbone of numerous industries, from manufacturing and construction to aerospace and agriculture. These systems rely on hydraulic fittings to connect pipes, tubes, and hoses, ensuring seamless fluid transfer under high pressure. However, without proper coatings, these fittings are prone to corrosion, wear, and premature failure.
Choosing the right hydraulic fitting coating is crucial for durability, cost-efficiency, and system performance. Among the most popular options are zinc coatings, stainless steel, and nickel plating—each with its own strengths and weaknesses. In this article, we’ll compare these three coating types to help you determine the best fit for your application.
Understanding Hydraulic Fitting Coatings
Hydraulic fitting coatings serve multiple functions beyond just aesthetics. They enhance corrosion resistance, improve wear protection, and extend the overall lifespan of the fittings. Without a protective layer, metal fittings exposed to moisture, chemicals, and extreme conditions can deteriorate quickly, leading to leaks, equipment damage, and costly downtime.
Factors to consider when selecting a hydraulic fitting coating include:
- Corrosion Resistance: Protection against rust, oxidation, and chemical exposure.
- Mechanical Strength: The ability to withstand pressure, vibration, and impact.
- Cost and Longevity: Balancing affordability with long-term performance.
- Environmental Compliance: Adherence to regulations like RoHS and REACH.
Each coating type offers a unique balance of these factors, making it essential to understand their specific properties before making a decision.
Zinc-Coated Hydraulic Fittings
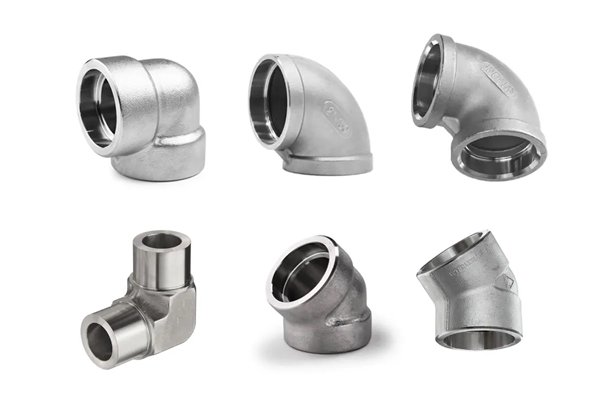
Zinc coatings are among the most widely used protective finishes for hydraulic fittings due to their affordability and moderate corrosion resistance. There are two primary types of zinc coatings:
- Electroplated Zinc: A thin layer of zinc is applied through an electrochemical process, providing basic corrosion protection. This is common in industrial and automotive applications.
- Zinc-Nickel Alloy: A more advanced version, zinc-nickel coatings offer superior durability and corrosion resistance, outperforming standard zinc plating.
Advantages of Zinc Coatings
Cost-Effective: One of the most affordable options for hydraulic fittings.
Moderate Corrosion Protection: Suitable for mild to moderate environments.
✔ Lightweight: Adds minimal weight to the fitting, maintaining system efficiency.
Disadvantages of Zinc Coatings
✖ Limited Durability: Zinc coatings wear down faster than stainless steel or nickel plating.
✖ Not Ideal for Harsh Environments: Struggles in extreme chemical exposure or marine settings.
Best Use Cases for Zinc-Coated Fittings
- Agriculture and Automotive: Suitable for systems exposed to mild weather conditions.
- General Industrial Use: A cost-effective option for moderate corrosion resistance.
Stainless Steel Hydraulic Fittings
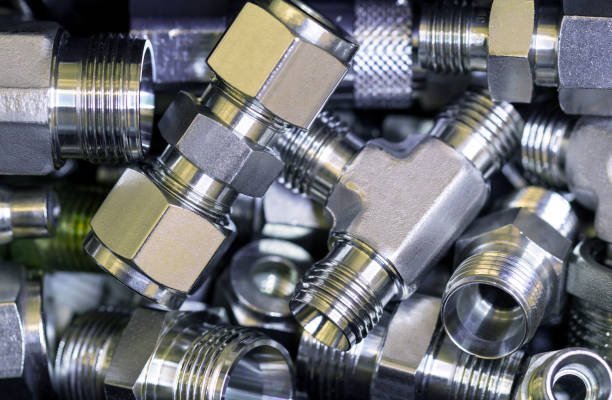
Stainless steel is widely regarded as one of the best materials for hydraulic fittings due to its exceptional corrosion resistance, strength, and longevity. Unlike zinc-coated fittings, stainless steel does not rely on an additional layer for protection—its natural composition provides inherent resistance to rust and oxidation.
Grades of Stainless Steel Used in Hydraulic Fittings
- 304 Stainless Steel: Provides good corrosion resistance and is commonly used in industrial applications.
- 316 Stainless Steel: Contains molybdenum, making it highly resistant to chlorides and marine environments.
Advantages of Stainless Steel Fittings
Superior Corrosion Resistance: Ideal for harsh environments, including marine and chemical industries.
High Durability: Can withstand extreme temperatures and high-pressure systems.
Longevity: Offers the longest lifespan compared to zinc and nickel-plated fittings.
Disadvantages of Stainless Steel Fittings
✖ Higher Cost: More expensive than zinc and nickel-plated alternatives.
✖ Potential Galling Issues: Under high pressure, stainless steel threads may seize without proper lubrication.
Best Use Cases for Stainless Steel Fittings
- Marine Applications: Resistant to saltwater corrosion.
- Medical and Food Industries: Meets hygiene and safety standards.
- High-Pressure Hydraulic Systems: Suitable for demanding industrial operations.
Nickel-Plated Hydraulic Fittings
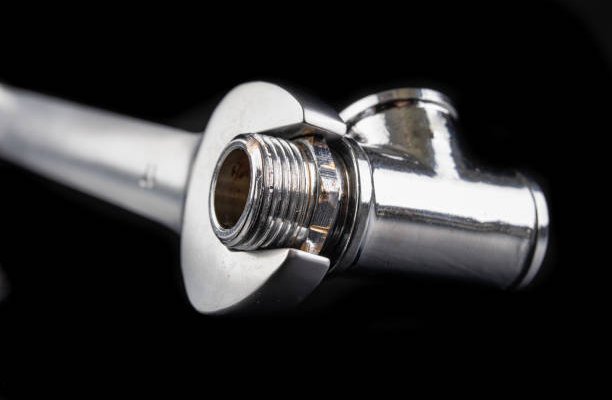
Nickel plating is a versatile coating that enhances both corrosion resistance and mechanical strength. Available in electroless and electroplated forms, nickel coatings provide a robust protective barrier against oxidation, wear, and chemical exposure.
Types of Nickel Plating
- Electroless Nickel Plating (ENP): Offers uniform coverage, even on complex fitting shapes, and provides excellent wear resistance.
- Electroplated Nickel: Uses an electric current to deposit nickel, creating a harder but less uniform coating.
Advantages of Nickel-Plated Fittings
Strong Adhesion: Forms a durable bond with the base metal, reducing flaking or peeling.
High Wear Resistance: Excellent for applications with high mechanical stress.
Good Corrosion Protection: Better than zinc but not as strong as stainless steel.
Disadvantages of Nickel-Plated Fittings
✖ Higher Cost Than Zinc: More expensive due to the complex plating process.
✖ Not as Corrosion-Resistant as Stainless Steel: Still susceptible to degradation over time.
Best Use Cases for Nickel-Plated Fittings
- Aerospace and Industrial Machinery: Requires enhanced wear and chemical resistance.
- High-Pressure Hydraulic Systems: Can withstand frequent pressure changes.
Corrosion Resistance Comparison
Since corrosion resistance is a key factor in choosing a hydraulic fitting coating, testing methods like salt spray testing (ASTM B117) are used to evaluate longevity in harsh environments.
Coating Type | Salt Spray Test Duration (Hours) | Best Resistance To |
---|---|---|
Zinc Plating | 96 – 240 | General industrial use |
Zinc-Nickel Alloy | 500 – 1,000 | Moderate corrosion exposure |
Nickel Plating | 500 – 1,200 | Wear resistance & chemicals |
304 Stainless Steel | 1,000 – 2,000 | Moderate corrosion & rust |
316 Stainless Steel | 2,000+ | Marine & extreme environments |
Key Takeaways from Corrosion Testing
- Zinc coatings provide the least corrosion resistance but are affordable for general applications.
- Nickel plating offers a strong balance between wear resistance and corrosion protection.
- Stainless steel provides the best long-term corrosion resistance, especially in marine and chemical environments.
Cost Comparison and ROI
When selecting a hydraulic fitting coating, cost is a major factor—but upfront expenses don’t always reflect the long-term investment. A more expensive coating may reduce maintenance costs and extend the life of your hydraulic system.
Price Analysis of Hydraulic Fitting Coatings
Coating Type | Initial Cost | Maintenance Cost | Lifespan | Overall ROI |
---|---|---|---|---|
Zinc Plating | Low | Moderate | Short | Cost-effective for short-term applications |
Nickel Plating | Medium | Low | Medium-Long | Good balance of cost and durability |
304 Stainless Steel | High | Very Low | Long | High ROI in corrosion-prone environments |
316 Stainless Steel | Very High | Very Low | Very Long | Best for extreme conditions |
Which Coating Offers the Best ROI?
- For budget-conscious applications, zinc-plated fittings are the most affordable but require frequent replacements.
- Nickel-plated fittings provide a balance of cost, durability, and corrosion resistance.
- Stainless steel fittings offer the longest lifespan and lowest maintenance, making them the best long-term investment.
Mechanical Strength and Wear Resistance
Aside from corrosion resistance, mechanical durability plays a crucial role in hydraulic fitting performance. The ability to withstand high pressures, friction, and physical impact varies between coatings.
Comparing Strength and Wear Resistance
Coating Type | Hardness (Rockwell Scale) | Abrasion Resistance | Impact Resistance |
---|---|---|---|
Zinc Plating | Soft (HRB 50-60) | Low | Moderate |
Nickel Plating | Medium (HRC 40-50) | High | High |
304 Stainless Steel | Medium (HRB 70-80) | Medium | High |
316 Stainless Steel | Medium-High (HRB 80-90) | Very High | Very High |
Key Takeaways
- Nickel plating offers excellent wear resistance, making it ideal for high-friction applications.
- Stainless steel is highly impact-resistant, suitable for extreme pressures and rough handling.
- Zinc coatings wear down more quickly, making them less ideal for heavy-duty use.
Environmental and Regulatory Considerations
As industries move towards sustainability, eco-friendly and compliant materials are becoming essential. Regulations like RoHS (Restriction of Hazardous Substances) and REACH (Registration, Evaluation, Authorization, and Restriction of Chemicals) restrict harmful substances in industrial components.
Environmental Impact of Coatings
Coating Type | Eco-Friendliness | Regulatory Compliance |
---|---|---|
Zinc Plating | Moderate (Toxic byproducts from plating process) | May require RoHS compliance checks |
Nickel Plating | Low-Moderate (Nickel is a heavy metal with potential health risks) | Subject to REACH regulations |
304 Stainless Steel | High (Recyclable and non-toxic) | Fully RoHS compliant |
316 Stainless Steel | Very High (Corrosion-resistant, long lifespan, 100% recyclable) | Fully RoHS and REACH compliant |
Best Choice for Eco-Friendly Applications
- Stainless steel is the most sustainable option, as it is fully recyclable and requires no hazardous coatings.
- Nickel plating and zinc coatings have a higher environmental impact due to potential heavy metal contamination.
Application-Based Recommendations
Choosing the right hydraulic fitting coating depends on your industry, environmental conditions, and budget. Below are tailored recommendations for different applications:
Best Coating for Industrial Use
Nickel-plated fittings
- Offers a balance of corrosion resistance, durability, and affordability.
- Ideal for manufacturing plants, hydraulic power systems, and heavy machinery.
Best Coating for Marine and Chemical Applications
316 stainless steel fittings
- Superior corrosion resistance, even in saltwater and acidic environments.
- Used in offshore oil rigs, shipbuilding, and chemical processing plants.
Best Coating for High-Pressure Hydraulic Systems
Nickel-plated or stainless steel fittings
- Nickel plating provides excellent wear resistance and high-pressure durability.
- Stainless steel prevents galling under extreme hydraulic pressure.
Best Budget-Friendly Coating for Mild Environments
Zinc-plated fittings
- Ideal for agriculture, automotive, and general industrial use where corrosion is moderate.
Conclusion
The right hydraulic fitting coating can significantly impact the efficiency, longevity, and cost-effectiveness of a hydraulic system.
- Zinc coatings are affordable but best suited for low to moderate exposure environments.
- Nickel plating offers a balance between wear resistance, corrosion protection, and cost.
- Stainless steel is the best long-term investment, especially for marine, chemical, and extreme pressure applications.
When selecting a hydraulic fitting coating, consider your system’s environment, expected lifespan, and maintenance costs. The right choice will maximize system performance while minimizing downtime and replacements.
FAQs
1. Which hydraulic fitting coating lasts the longest in harsh environments?
316 stainless steel offers the best corrosion resistance and durability, making it ideal for extreme conditions like marine and chemical industries.
2. Can I mix different coated fittings in a hydraulic system?
While possible, it’s generally not recommended due to the risk of galvanic corrosion when different metals interact.
3. What’s the best coating for extreme temperatures?
Stainless steel performs best under extreme hot or cold conditions, as it maintains structural integrity without degrading.
4. Are there any coatings better than these three?
Other advanced coatings, like ceramic or polymer coatings, are emerging in specialized applications but are not yet widely adopted for hydraulic fittings.
5. How do I maintain hydraulic fittings for a longer lifespan?
- Regularly inspect for corrosion or wear.
- Use proper lubrication to prevent galling in stainless steel fittings.
- Flush hydraulic systems to prevent contamination buildup.